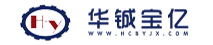
含油废水是一种量大而且面广的污染源,其排放量居各类工业废水之首。含油废水的来源很广,其中主要有石油工业的炼油厂含油废水、铁路机务段的洗油罐含油废水、轧钢废水和金属清洗液、拆船厂的油货轮含油废水、油轮压舱水、洗舱水、机械切削加工的乳化油废水、以及餐饮业、食品加工业、洗车业排放的含油废水等。
随着人们生活水平的提高,对环境的要求日益提高,含油废水的处理越来越受重视,成为现代社会待解决的重要课题之一。
一般情况下,含油废水的含油量为几10到几1000mg/L,有的甚至高达数10000mg/L。根据其存在方式的不同,废水中的油类可分为浮油、分散油、乳化油和溶解油4种:
(1)浮油以连续相漂浮于水面,形成油膜或油层。这种油的油滴粒径较大,一般大于100μm,它的去除相对较为容易。含油废水主要含有浮油,占总含油量的70%~80%。
(2)分散油以微小油滴悬浮于水中,不稳定,静置一定时间后往往变成浮油,其油滴粒径为10~100um。
(3)乳化油水中往往含有表面活性剂,使油成为稳定的乳化液。油滴粒径极微小,一般小于10μm,大部分为0.1~2um。
(4)溶解油粒径很小,有的可小到几nm,是溶于水中的油微粒,油粒间难以合并,难以分离。
油类对环境的污染主要表现在对生态系统及自然环境的严重影响。流到水体中的浮油形成油膜后会阻碍大气复氧,断绝水体氧的来源。而水中的乳化油和溶解油,由于需氧微生物的作用,在分解过程中消耗水中溶解氧,生成二氧化碳和水,使水体形成缺氧状态,水体中二氧化碳浓度增高,水体pH值降低。如果pH值降低到正常范围以下,将导致鱼类和水生生物不能生存。含油废水流人土壤,由于土层对油污的吸附和过滤作用,也会在土壤中形成油膜,使空气难以透入,阻碍土壤微生物的增殖,破坏土层团粒结构。含油废水排入城市排水管道,对排水设备和城市污水处理厂都会造成影响,流人到生物处理构筑物的混和废水的含油浓度通常不能大于30~50mg/L,否则将影响活性污泥和生物膜的正常代谢过程。
1 含油废水常用处理方法
1.1 重力分离法
重力分离法是一种利用油水密度差进行分离的方法。此法可用于除粒径60μm以上的油粒和废水中的大部分固体颗粒。采用重力分离法常用的设备是隔油池。它是利用油比水轻的特性,将油分离于水面并撇除。隔油池主要用于去除浮油或破乳后的乳化油。隔油池的形式较多,主要有平流式隔油池、平行板式隔油池、波纹斜板隔油池和压力差自动撇油装置等。该方法适用于浮油、分散油,且效果稳定运行费用低,但设备占地面积大。
平流式隔油池完全靠重力作用进行油水分离,能去除浮油和大粒径的分散油,池型简单,操作方便,除油效率稳定,但占地面积大,受水流不均匀性影响,处理效果不好。斜板式隔油池根据浅池沉降原理从而应用于工程实际,沿水流方向安装斜板,增加有效分离面积,提高整流效果,增强了隔油效果。波纹斜板式隔油池由于提高了单位池容分离面积,占地面积小,停留时间不超过30min,且单位处理能力池容只相当于平流式隔油池的1/4~1/2。
David和Rochford报道了科威特北部油田废水处理工艺,主要采用平流式隔油池和波纹斜板隔油池油水分离器,含油废水经隔油、气浮法处理后可用于回注。近来,针对重力除油技术占地面积大、基建投资高、停留时间长等缺点,研制开发高效除油技术及油水分离器成为热点。Carriere和Berger对油滴聚结技术进行了研究,表明该技术可以提高脱油效率,加快油水分离过程。所谓聚结又称粗粒化,是指含油废水通过一个装有填充物(聚结材料)的装置,在废水流经填充物时,油珠粒径由小变大的过程。美国Quontek公司开发研制了聚结板油水分离器,除油效果良好。此外,还有多层倾斜双波纹板峰谷对置型油水分离装置、日本NCP系三菱油污水净化装置等。
1.2 气浮法
气浮法是国内外正在深入研究与不断推广的一种水处理技术。该法是在水中通人空气或其他气体产生微细气泡,使水中的一些细小悬浮油珠及固体颗粒附着在气泡上,随气泡一起上浮到水面形成浮渣(含油泡沫层),然后使用适当的撇油器将油撇去。该法主要用于处理隔油池处理后残留于水中粒径为10~60μm的分散油、乳化油及细小的悬浮固体物,出水的含油质量浓度可降至20~30mg/L。
根据产生气泡的方式不同,气浮法又分为加压气浮、鼓气气浮、电解气浮等,其中应用较多的是加压溶气气浮法。还有混凝沉淀-气浮法,即在气浮过程中投加适当的混凝剂,使气浮的效果更加有效,但是该法浮渣量大且含有大量气泡。另外还有吸附气浮法,即在气浮池里投加粉末活性炭,吸附废水中的油和溶解性污染物,废炭以及废水中的其他悬浮物附着在气泡上并与气泡一起上浮到池顶由除渣机除去。张登庆等把电气浮技术应用在油田采出水处理中,研究表明电气浮工艺用于油田采出水除油及杀菌是可行的。阳极用于除油,阴极用于杀菌,除油率为80%~90%,电耗约为0.1kWh/m3。雷乐成针对油田稠油污水水温高、溶气效果差、含油和悬浮物浓度高、油水密度接近等特点,在充分吸收各种气浮技术的基础上, 将气液多相泵应用于高温含油污水的气浮处理。通过在相同进水条件下的工程现场实际运行数据对比,多相泵气浮具有气浮效率高、微气泡直径小、操作维护简单、工程造价和运行费用低等诸多优点。试验结果表明,应用气液多相泵处理高水温超稠油污水,油和悬浮物去除率均高于95%。Rajinder用浮选柱回收乳状液中的油,效果良好。试验结果表明,对给定的送液量,随送液油浓度增加,油品回收率下降,但产品中油浓度增加;随气体流量增加,油回收率增加;随表面活性剂的增加,油回收率下降。
1.3 电化学法
常用的电化学法是电絮凝法。电絮凝法是电浮选和电沉淀的综合过程,其特点是使用可溶性阳极如金属铝或铁作牺牲电极,通过化学反应,既产生气浮分离所需要的气泡,也产生使悬浮物絮凝的絮凝剂。电絮凝过程的两个主要反应为吸附电荷中和反应和去除聚结物反应。电絮凝法具有处理效果好、占地面积小、操作简单、浮渣量相对较少等优点,但同时也存在阳极金属消耗量大、需要大量盐类作辅助药剂、耗电量高、运行费用较高等缺点。王车礼等采用电絮凝法处理油田废水,考察了电流强度、PAC投加量、电极板间距和pH值对废水脱油率的影响。正交实验结果表明,在选定条件下进行电絮凝实验,电解反应4min,废水脱油率达到84.3%。王蓉沙等应用电絮凝浮选法对油田3类主要污水进行处理研究结果表明,电絮凝法适宜油田污水处理,具有明显的去油作用和降低污水的COD、SS作用,处理后污水能达到 污水排放标准。韩洪军采用微电池滤床法处理含油废水,将焦炭-铁屑粒料浸没在含油废水中,构成完整的微电池回路。在其表面有电流流动,从而促进金属的电化学腐蚀,使大量的金属离子进入废水成为凝聚剂,使油珠很快完成电泳沉积和聚结,油去除率达70%~80%。陈水平研究了用铁屑内电解法处理船舶机舱含油废水。实验结果表明,油污水的SS、油分和COD去除率分别超过95%、90%和80%,处理后的污水油分浓度低于15mg/L,符合有关国际公约的标准,出水水质优于油水分离器。Qgutveren等采用电凝法处理含油废水,取得良好效果。S.Rubach等采用电絮凝处理北海油田采出水。研究发现,当电导率由60ms/m提高到480060ms/m(相当于含盐量从1g/L上升至80g/L)时,耗电量相应由9kWh/m3降到1.5kWh/m3,而出水油浓度在10~15mg/L间变化,去除率均在98%以上。油的去除效率几乎不受其他因素的影响。
1.4 吸附法
常见的吸附剂是活性炭,它不仅对油有很好的吸附性能,而且能同时有效地吸附废水中的其他有机物,对油的吸附容量一般为30~80mg/g,且成本高,再生困难,故一般只用于含油废水的深度处理。吸附法的研究进展多体现在高效、经济的吸油剂开发与应用方面,文献介绍了一种由质量分数为5%~80%具有吸油性能的无机填充剂(如镁或铁的盐类、氧化物等)与20%~95%的交联聚合物(如聚乙烯、聚苯乙烯等)组成的吸油剂。这种吸油剂对油的吸附容量可达0.3/g~0.69/g,但一般需要接触时间很长,如废水的油质量浓度为120mg/L时,需处理50h才能降至0.8mg/L。刘汉利采用改性粉煤灰处理炼油厂高、低浓度含油废水,使之达到排放标准,获得了满意的效果。磁分离法是吸附除油方面的研究成果,通过投入经过磁化的磁种吸附污染物,然后磁分离而使水质净化。有研究利用磁铁矿良好的吸油特性,探讨了该法处理含动植物油废水的原理和工艺条件,结果表明,当废水含油质量浓度为112~1855mg/L,COD为2800~8020mg/L时,用磁分离法处理可使油和COD去除率分别达到85%和75%以上。若能解决该法成本问题,将具有广阔的应用前景。
1.5 絮凝法
絮凝法是处理含油废水的一种常用方法,在废水处理中占有十分重要的地位。这种方法通过加入合适的絮凝剂而在污水中形成高分子絮状物,经过中和、吸附、架桥等作用将水中污染物质去除。常用絮凝剂种类多为高价阳离子铝盐。近年来新型絮凝剂的开发与应用主要着眼于无机高分子凝聚剂和复合絮凝剂。陶丽英等考察了自制的兼具破乳和絮凝功能的化学药剂——净水灵处理采油废水的效果,在较佳实验条件下,COD及油的去除率分别达到了85%、95%以上且药剂费用低,并在现场得以应用取得满意的效果。周珊针对含油废水的特性,采用絮凝法对含油废水进行了初步处理,试验结果表明:含油废水中加入100mg/L聚合AlCl3絮凝处理后,油去除率可达86.4%,COD去除率可达42.2%,可成为生物处理法的预处理工艺。
1.6 生物化学法
生化处理法是利用微生物的生物化学作用,对废水中石油烃类进行降解,主要是在加氧酶的催化作用下,将分子氧结合到基质中,先形成含氧中间体,然后再转化成其他物质。常用的生物法有活性污泥法、生物滤池法、生物膜法、接触氧化法、曝气塔、深井曝气、纯氧曝气以及循序间歇式生物处理等。李哲等采用SRB方法来处理某油田废水。研究结果表明,用SRB法处理油田采出水在技术上是可行的。杜卫东等利用厌氧酸化-接触氧化的方法对某油田废水进行试验研究。试验结果表明,采用“厌氧-好氧”工艺处理采油废水是可行的。对COD浓度较高(400mg/L左右)的采油废水,通过厌氧与好氧串联
运行处理,COD去除率78%,油去除率为76%~87%,处理后水质指标全部达到CB8978-1996《污水综合排放标准》要求。竺建荣等采用厌氧-好氧交替工艺处理适当稀释或原浓度的油田废水,若先经过厌氧UABS反应器处理后的废水,再经厌氧-好氧交替工艺进行处理,在停留时间为8~12h的条件下,其COD浓度能够从350mg/L降到160~240mg/L,COD去除率31%~48.5%。对于COD浓度为160~180mg/L的废水,采用好氧接触氧化法作为好氧2级处理,其出水COD去除率在50%~60%,出水COD浓度一般接近80mg/L左右,可满足 排放标准。目前,生物化学法除油趋向于针对含油废水进行分离筛选优势菌种的研究。研究较多的菌种有动胶菌属、氮单胞菌属和假单胞菌属等,其中动胶菌的处理效果较好。谢思琴等利用自行分离筛选的动胶菌D2菌株,以生物接触氧化法对含机械润滑油的废水进行处理。在实验室条件下,控制人流流量,除油效果十分显著。当废水含油浓度为424~1432mg/L时,经过试验运转,出水油浓度已降至0~20mg/L,除油率达97%以上,水质基本达到 2级排放标准。此外,伪氧化技术在含油废水处理中的应用也日益广泛。电化学、光电化学法由于能耗和处理费用较高,目前尚处于试验阶段。当前,膜分离、氧化技术、生物深度处理技术已成为处理含油废水的研
究热点。
2 结论与展望
传统的含油废水处理方法虽然较多,但各种方法都有其局限性,受废水成分、油分存在的形式、回收利用的深度以及排放方式等多因素的影响。如果只使用单一的处理方法,难以达到满意的效果。随着人们对环保的重视及我国对污染治理力度的加大,目前的方法已经不能满足当前人们要求,采用新的处理方法势在必行。今后含油废水处理技术的发展趋势通常是采用几种方法结合在一起,形成多级处理的工艺,从而实现良好的除油效果,使出水水质达到废水排放标准。同时加强除油机理的研究,为提高含油废水处理效率及降低处理成本提供理论基础。