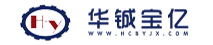
油类物质通过不同途径进入水中形成含油废水,由于其量大面广的特点使其成为一种危害严重的废水。其来源主要有:石油工业中的石油开采和油品的加工、提炼、储存及运输;运输工业中洗车、铁路机务段的洗油罐等排放的含油废水、机械制造加工过程中产生的轧钢水、润滑油液等以乳化油为主的废水;另外餐饮业、纺织业、食品加工业及其他制造业的废水中也含有大量的油。
含油废水在水体表面形成一层油膜,阻断了空气和水体间的气体交换,导致水体溶解氧下降,致使水体中浮游生物因缺氧而死亡;同时影响水生植物的光合作用,进而影响水体的自净功能,使水变臭,破坏水资源的利用价值。鱼、虾、贝类等长期在含油污水中生存将导致其肉内含有油味,不宜食用。油污染严重还会直接导致水生动物的死亡,因此必须对含油废水进行处理。
油类物质在水中的存在形式可分为浮油、分散油、乳化油和溶解油4大类。浮油的油珠粒径较大,大于100μm易于浮出水面,形成油膜和油层。分散油的油珠粒径一般为10~100μm,以微小的颗粒悬浮在水中,不稳定,静置一段时间后往往会形成浮油。乳化油是由于水中含有表面活性剂而形成的,油滴粒径极小,一般小于10μm。溶解油是一种以化学方式溶解在水中的油,其粒径可以达到几个纳米。
1 浮油和分散油废水的处理
1.1 隔油装置
常用的隔油装置有平流隔油池、斜板隔油池和小型隔油池等。其中平流隔油池的优点是构造简单,维护容易,使用较为方便;缺点是池体大,占地面积多。根据国内外的资料,这种隔油池可能去除的较小油滴粒径一般为100~150μm。某炼油厂废水处理站使用这种类型的隔油池,停留时间为90~120min,原废水中的含油质量浓度为400~1000mg/L,出水<150mg/L,除油率>70%。根据浅池理论而发展起来的斜板隔油池,大大缩短了停留时间,节约了占地面积。
1.2 气浮法
气浮技术是国内外处理含油废水当中使用较为广泛的一种技术。目前对气浮法的研究多集中在气浮装置的革新、改进以及气浮工艺的优化组合方面。如浮选池的结构由方形改成圆形以减少死角,采用溢流堰板排出浮渣而去掉机械刮泥设备等。此外还开发出一些新型的设备和工艺流程,如刘军利用涡流泵的特殊搅拌功能来改进工艺而形成高效气浮装置,将难以相溶的水和气体进行高效混合溶解并同时进行压送,不仅大大缩减了搅拌工艺环节,而且能替代工艺复杂且成本较高的空气压缩机、大型溶气罐等,实现了设备的小型化。经此工艺处理的废水含油质量浓度由80mg/L降至<10mg/L,完全能够达到排放标准。王振欧等将压缩空气溶气改为喷射器吸气溶气,提高了浮选过程的处理效果,增强了系统抗冲击负荷的能力。浮选出水中油质量浓度由40mg/L降至<20mg/L,COD由150mg/L降至<110mg/L,且出水水质稳定;流程中因省去了空压机,所以可降低能耗、减少噪声、降低废水治理成本,取得较好的环境和经济效益。肖坤琳等在实验研究的基础上,结合单级气浮技术和多级板式塔理论,开发出两级气浮塔处理含油废水的新工艺,实现了塔釜一次曝气,多级气浮分离。试验测定表明,当进水含油质量浓度为20~150mg/L时,二级气浮塔板处理效率较单极处理要高出20%,试验阶段处理水量为6~14L/h。
2 乳化油废水的处理
由于乳化油的油珠极小,其表面形成一层带有电荷的界膜,油珠外围形成双电层,使油珠相互排斥极难接近,在动力学上有一定的稳定性,较难处理。因此首先要破乳,破坏油珠的界膜,使油珠相互接近并聚集成大滴油珠从而浮出水面。乳化油破乳后还需进行后续处理。
2.1 絮凝法破乳
絮凝剂一般分为无机絮凝剂、复合絮凝剂以及有机絮凝剂。为了提高絮凝的效果,克服日益加剧的水污染问题,近年来有许多学者对絮凝剂进行了改进,也开发了许多新型絮凝剂,主要为无机高分子
絮凝剂和复合絮凝剂。杨永哲等在聚合氯化铝的制备过程中加入Fe3+,使Al3+和Fe3+发生聚合,从而得到改进型复合碱式氯化铝。动态试验表明,改进型复合碱式氯化铝的较佳碱化度是2.0,铝铁物质的量比为1:1,在此条件下,投加这种碱式氯化铝节省投药量20%左右,因而产生浮杂较少,运行费用较低,由此而成为一种有效的溶气气浮法的破乳剂。无机高分子絮凝剂主要是铝盐和铁盐的聚合体系,如聚氯化铝(PAC)、聚硫酸铁(PFS)、聚硅氯化铝(PASC)、聚硅硫酸铝(PASS)、聚硅硫酸铁(PFSS)等。PAC是常用的水处理剂,但其处理成本较高,而且沉降速度较慢。与PAC相比,PFS具有COD去除率高、成本低廉且沉降速度较快等优点。但处理后铁在水中有残留,易造成管线腐蚀。具有合适铝硅物质的量比的聚硅氯化铝主要通过电中和及吸附架桥起到混凝作用,不但较PAC具有更好的除浊、脱色、降藻、除油和去除COD的絮凝功效,而且降低了投药成本。PASS由于硅铝之间的作用,不但去浊率高、沉降速度快,在低温低浊条件下仍有较好的絮凝效果,而且处理后残余铝量可显著降低。PFSS在降低SS,增大矾花直径,提高沉降速度等方面均优于PAC和PFS。PASS和PFSS都是通过长链大分子卷扫聚集作用使形成的絮凝体沉降速度增大,同时可以显著降低残余铝和残余铁含量。综合比较二者处理效果相当,只是PFSS贮藏时间可达到PASS的3倍。
复合混凝剂由不同盐系结合而成。如含A的聚硅酸絮凝剂,是在聚硅酸的基础上,加入适当的Al3+而形成的一种复合型的无机阳离子高分子絮凝剂。适用pH 5~11,n(Al):n(SiO2)为0.25:1~0.5:1之间,具有良好的絮凝效果。SPTL-CS复合絮凝剂是以FeSO4、硫酸、铝盐为基本原料,在硫酸介质中以MnO2为催化剂经空气氧化而得到的一种高聚合度无机高分子絮凝剂,但使用这种絮凝剂需先去除浮油。XG977混凝剂是以聚合硫酸铝铁和钙盐为主的多聚物,其分子中具有多核羟基络合离子结构,在投加量相同条件下,XG977的处理效果明显优于PAC,且污泥体积小,其形成絮体的沉降性能优于PAC,综合处理费用比PAC低20%。
常用的有机絮凝剂是聚丙烯酰胺、ZB型阳离子有机絮凝剂等。现场试验表明,在除油率大致相同的情况下,ZB复合配方的投加量约为PAC的1/2~1/5,并且有废渣生成量少,废渣含水率低、含油量高的特点,它是PAC很好的替代品。
2.2 后续处理
乳化油破乳后,还需要进一步处理,才能达到排放标准,去除浮油和分散油的隔油池和气浮法也可以用于破乳后的后续处理。后续处理方法有吸附法、粗粒化法、膜分离法、 氧化法等。
2.2.1 吸附法
传统吸附分离技术很早就应用于含油废水的深度处理中。常见的吸附剂是活性炭,其对油的吸附容量为30~80mg/g,但活性炭成本较高,再生困难。开发高效、经济的吸油剂是目前研究的重点。曹乃珍等对膨胀石墨进行了吸附研究,通过膨胀石墨吸附材料对各种油类及各种存在形式的油的吸附试验,研究了其对水中各种状态油的吸附性能。结果表明膨胀石墨无论是对各种单纯油类、水面浮油以及乳化油还是对低含油废水都有极好的吸附能力,其吸附量远高于活性炭,并且由于其具有疏水性,在水中清除油污时不会因大量吸附水而浪费吸附剂。吴敦虎等运用多种方法对硼砂生产过程中的废料—硼泥的吸附除油性能进行研究,也取得了较好的效果。在处理大连某机车厂含乳化油废水时,其除油率达到98.0%,出水透光率为98.2%。关于粉煤灰在含油废水处理中的应用也有较多的报道,此除油剂对废水适应范围较广,较佳pH范围为4~11,较佳温度为5~50℃,较佳投加质量浓度为4.1g/L,其去除率达到90%左右。
2.2.2 粗粒化法
粗粒化法(亦叫聚结法)是使含油废水通过一种填有粗粒化材料的装置,使污水中的微细油珠聚结成大颗粒,从而使油水分离的方法,其技术关键是粗粒化材料。
许多研究者认为材质表面的亲油疏水性能是其性能好坏的关键,而且亲油性材料与油的接触角<70°为好。当含油质量浓度>100mg/L的废水通过这种材料时,微细油粒便吸附在其表面上,经过不断碰撞,油珠逐渐聚结扩大而形成油膜,然后在重力和水流推力的作用下,脱离材料表面而浮升于水面。其出水含油质量浓度一般>10mg/L,还需适当的深度处理。可通过污水在粗粒化前后油珠粒径的变化来判断此工艺的除油效果及工艺可行性。
粗粒化除油装置具有体积小、效率高、结构简单、不需加药、投资省等优点;缺点是填料容易堵塞,出水油含量较高,水中含有表面活性剂时处理效果受到影响,常需要再进行深度处理。
2.2.3 膜分离法
在含油废水治理中研究应用较多的是超滤法,它是治理含油废水的一种新技术,正从实验室逐渐走向应用。如陆晓千等试验用超滤法处理上海某厂乳化液废水,结果表明采用该方法可使废水含油质量浓度从100~1000mg/L降至<10mg/L。王冠平等试验采用超滤技术处理含油废水,处理水量为4.5mh。试验结果表明,COD的去除率达到80%~90%,油类物质的去除率>95%,浓缩倍数可达到71倍,且对出水水质影响不大。郭晓等采用超滤法对采油厂低渗油层的石油废水进行处理实验,在流量6m3/h、操作压力0.45MPa、产水率75%、反冲洗周期8h、所用膜为磺化聚枫膜的条件下,使含油质量浓度为80~120mg/L的废水经处理后出水达到了回注水标准。
膜分离技术具有操作简单、分离效果好、可回收油等优点,但膜污染严重、不易清洗、运行费用高。其发展趋势是将各种膜处理方法结合或是与其他方法相结合使用。如将超滤和微滤结合处理含油废水,膜分离法和电化学法相结合,也有将臭氧氧化作为超滤的前处理,从而延长超滤设备的使用寿命。
2.2.4 氧化法
在化学氧化法中,超临界水氧化技术是近年来迅速发展起来的废水 氧化技术。其原理是将水体中有机污染物在超临界水中氧化分解成为CO2、H2O等无害的小分子化合物。赵朝成等发现超临界水中的氧化反应能有效去除污水中的油分,在一定条件下反应时间和反应压力是COD去除率的主要影响因素。反应压力达到240~280MPa时,压力的影响不大;反应时间为2min时COD去除率达到75%~80%,但随着时间的推移去除率趋于100%。此项技术较大问题就是高压反应器存在比较严重的腐蚀问题,这也是超临界水氧化技术工业化需要解决的主要问题之一。
光催化氧化降解法是目前研究处理含油废水的另一项氧化技术,半导体催化氧化法具有很强的氧化功能。陈士夫等利用空心玻璃球负载TiO2清除水面漂浮的油层,去除率达到90%以上;通入空气或是H2O2还可以大大提高光催化的效果。方佑龄等用硅偶联剂将纳米TiO2偶联在空心微球上,制得漂浮于水上的TiO2光催化剂,进行水面油膜污染物的光催化分解研究,去除率达到90%以上。
3 溶解油废水处理
溶解油用一般的物理及化学方法都难以将其去除,目前用得较多的还是生化法,在除油的同时还能去除其他的污染物。油类是一种烃类物质,可利用微生物将其分解氧化成CO2、H2O。由于传统活性污泥法处理含油废水时,存在含油废水中有机物种类繁多、状态复杂、处理效果不好的情况,因此人们开展了含油废水优势菌种的研究,研究较多的菌种是动胶菌属、氮单胞菌属和假单胞菌属。
4 展望
含油废水处理技术的研究和应用得到迅速发展,利用工业废弃物或其改性后制成较好的除油剂,在工程实例中加以运用达到了较好的以废治废的目的。今后含油废水的发展趋势主要是采用物理化学法,目前正在快速发展的新方法有:
(1)磁吸附分离法。借助磁性物质作为载体,利用油珠的磁化效应,将磁性颗粒与含油废水相结合,使油吸附在磁性颗粒上,再通过分离装置,将磁性物质及其吸附的油留在磁场中,从而达到油水分离的目的。
(2)超声波法。超声波一般用来破乳,有研究表明超声波和破乳剂具有良好的协同作用。它可以提高破乳剂的效率,减少破乳剂的用量,特别是对那些用常规脱水方式难以奏效的原油乳状液破乳脱水具有较好的效果。超声波与破乳剂结合用于乳化原油脱水有着良好的发展前景,但是与其他方法相比,仍存在处理量小、费用高等问题。
(3)新型聚结法。聚结法就是将材料填充于粗粒化装置中,当废水通过时可以去除其中的分散油和部分乳化油。该技术的关键是聚结材料,常用的亲水性材料是在聚酰胺、聚乙烯醇、维尼纶等纤维内引入酸基和盐类,亲油性材料主要有蜡状球、聚烯系和聚苯乙烯系球体或发泡体等。该技术不需要添加任何化学药剂,具有投资省、运行费用低、占地面积小、出水水质高、可以实现油回收的特点,在含油废水处理中具有广阔的前景。