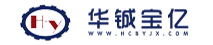
含油污泥是石油企业开发过程中产生的重要污染之一,也是制约油田环境质量持续提高的一大难题。孤东油田的含油污泥主要来源于以下场所:接转站、联合站的油罐、沉降罐、污水罐、隔油池的底泥,作业、管线穿孔而产生的落地原油及含油污泥。含油污泥的组成主要是原油、泥和水,给环境造成危害的主要是原油。
油泥(砂)既是原油生产过程中产生的废物,也是可贵的二次资源。对这些含油污泥,特别对高含油污泥进行有组织的收集,并开发研究出一种经济实用的方法对含油污泥进行无害化处理和污油回收,那么不仅会回收大量的能源,产生一定的经济效益,而且会减轻污染,产生巨大的环境效益和社会效益。
1 含油污泥(砂)现状
孤东油田属于疏松砂岩油藏,原油采掘携砂十分严重,日前砂液比已高达5.928:10000(休积比),日产液量高达13.5万m³,因此联合站每年春秋两季都要进行大罐清砂。同时山于出砂严重,导致油水井维护修井频繁,年作业工作量高达3500井次,每年人罐产生的油泥(砂)大约3.56万m³,其中4座联合站大罐清出油泥每年约2.91万m³,修井作业和管线穿孔等落地油产生的油泥每年约6500m³。前孤东油各联合站产生的油泥(砂)清罐后仅是采取简单的露天堆放、填埋处置方式,作业施工和管线穿孔产生的油泥也仅采取就地填理。这些简单的处置方式并未真正消除或减少其污染危害程度,完全不能满足环保的要求,同时还会对土壤、水体和大气造成二次环境污染,特别到雨季,雨水冲淋和渗出的污油到处漂溢,进一步加剧环境污染。
另外孤东油田又属于人工围海造陆形成的大型滩涂油口,临海靠河,其中所管辖的红柳油田、新滩油田又地处 级黄河三角洲自然保护区内。特殊的地理环境、特殊的环境要求和特殊的生产条件及工艺,更加突出了对油泥进行无害化处理的重要性。目前含油污泥的常用处理技术主要有:生物降解法、含油污泥固化法、焚烧法、溶剂萃取法、离心分离等方法。
2 含油污泥(砂)处理技术
2.1 含油污泥的组成特点
孤东油田的含油污泥主要来自联合站清出的汕泥和作业现场落地油产生的油泥,污泥外观呈黑色,粘稠,其中联合站的油泥乳化严重,其组成主要为原油、水、泥砂等。
2.2 实验
为了较好地从含油污泥中回收原油,根据孤东油田油泥(砂)的粒径较大的特点,和对几种油泥处理方法的对比,拟选用离心分离法对油泥进行实验。
2.2.1 实验样品
实验样品分别为联合站一次罐和二次罐清出的油泥混合样(1号样)、联合站好油罐清出的油泥(2号样)、落地油产生的油泥(3号样)。
2.2.2 药剂的选型
将油泥进行加水、加温稀释后,取同等量放在同型号的锥型瓶中,分别加不同药剂,进行等时间搅拌后静置,进行药剂定性选型,初步选出两类比较理想的药剂,编号分别为HS-1和HS-2。
2.2.3 实验条件
根据孤东原油的粘度、密度、凝固点等性能,初步确定实验条件,实验温度选45~55℃,采用电加热提升温度。
2.2.4 实验设备
离心机采用LW400×1200型卧式沉降离心机,该机每小时处理量油泥量为3m³。
2.2.5 实验流程
实验油泥样→搅拌液化→加温匀化→加药→离心分离→实验分析。
2.2.6 实验分析
主要针对固相(经离心分离后的污泥)中的含油量、含水率和液相(分离出的油水混合液)中的含固率。
转速在2500~3000r/min,转速差在7~9较为理想,其中药剂HS-1的除油效果较为理想,药剂HS-2的除油效果比HS-1稍差,但脱水效果较IS-1理想。
温度越高、油泥匀化越好,油、泥分离效果就越好。
油泥氧化时间越长、油乳化越严重,油泥分离越难,效果越差。
3 可行性分析
日处理规模为固态含油污泥60m³,该处理工艺设备投资规模大约在250万元,设计整体采用可移动式的撬装结构。
3.1 运行成本测算
运行成本主要为油泥(砂)收集运输费、电费、气费、药剂费和人工成本,其液化所需的水采用污水(循环使用,以降低能耗)。具体测算方式:
以每小时处理油泥6m³,日处理60m³(日连续运行12h),油泥被液化成300m进行测算:
①燃气费:1500m³×1.0元/m³=1500元(温度升高40℃,需耗热1.2×10kcal,需耗气450m³)。
②耗电费:96kWh×12h×0.45元/kWh=518.4元。
③耗水费:5m³×2.7元/m³-13.5元(油泥液化采用污水,并循环使用,药剂配比采用清水)。
④耗药剂:0.5kg/m×60m³×20元/kg-600元。
⑤油泥收集运输费:25元/m³×60m³-1500元(以油泥收集运输距离10公里测算)。
⑥人工费:50元/人·日×20人=1000元。
以上6项费用共计5131.9元,则每立方米油泥处理费用为:5131.9元÷60m³=85.53元/m³。
考虑到不可预见费等项,则油泥处理成本约为100元/m³。
3.2 原油回收效益
以日处理固态油泥60m³(含水率55%),其含油量平均值为20%(下样含油),原油回收率为75%,吨油价格按1000元进行测算:60m³×1.5t/m³×45%×20%×75%×1000元/t-6075元。
按油泥处理成本100元/m测算,通过计算得出:当油泥含油量(干样)大于20%时,对其进行处理才会有经济效益。
根据孤东采油厂年产油泥分类统计情况,年产油3.56万m³,含油污泥含油量平均高于盈亏临界值的油泥量大约为15900m³,其中好油罐5600m³,二次罐3800m³,落地油产生的油泥6500m³,年可回收原油4250.14t。按吨原油1000元,折合人民币425.014万元。扣除处理费用356万元,年产效益69.014万元。如仅对二次罐、号油罐和落地油产生的油泥进行处理,则其效益测算为166.83万元。
需要说明的是,效益测算中,未考虑设备折旧费和设备维护费,是因为未达标的汕泥每年需相应的缴纳排污费用,同时也需资金对油泥进行填埋等治理,二者费用是可以相互抵消的。
4 结论及建议
4.1 结论
(1)用离心分离技术是可以达到分离含油污泥中的油、泥的目的,并连续处理,技术工艺是可行的,油回收率可以达到80%以上。
(2)该技术对处理落地油产生的油泥效果显著:对细颗粒、乳化严重的油泥处理,需调整药剂,处理后的污泥是可以达到排放标准的(英国标准BS5750,淋浸法测试游离油不大于5%)。
(3)温度、药剂是实现含油污泥分离的关键因素。药剂的效果受油泥的性能影响很大,油乳化越严重,处理效果越差,温度越高,处理效果越好。
(4)含油污泥处理的含油量受油泥收集方式的影响,当含油量达到一定值时,会产生一定的经济效益,同时其所产生的环境效益和社会效益尤为明显。
4.2 建议
(1)对落地油产生的油泥采用适当的方式进行收集,有利于提高含油污泥的含油量。
(2)对联合站油泥的处理,建议采取大罐清砂和油泥处理同步进行的方式,使用泥浆泵,通过管线将油泥直接输入油泥处理系统,避免产生二次污染的产生,既有利于油泥的处理效果和提高原油回收率,又可以大大减少油泥的收集运输费用,减低油泥处理成本。
(3)对一次罐等容易处理的油泥,在不影响处理效果的同时,调整运行参数(如降低运行温度和用药剂量等),是可以降低处理费用,提高油泥处理项目的整体经济效益的。