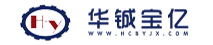
随着石油化工的快速发展,石油与环境之间的矛盾越来越突出。近几年,随着延长石油不断发展壮大,2015年油气产量已经达到了1400万t以上,加工原油1200万t以上,在石油开采和炼制过程中产生的各类含油污泥达15万t以上。这些污泥组成成分极其复杂,含有大量的老化油、蜡质、胶质和沥青质,其稳定性高,处理难度大,若不加以处理直接排放,不仅会对周围土壤和水体等造成严重污染,而且极大浪费了有限的石油资源。尤其是陕北地处黄土高原,气候干旱缺水,生态环境脆弱,含油污泥带来的环境污染问题更加严重。
近几年,随着国家环保政策的不断深化,国内各主要石油生产及石油化工企业、大专院校等研究部门均加强了含油污泥处理技术研究与应用。如邓皓等利用水泥窑系统的高温煅烧功能,将含油污泥中的无机矿物质和矿物油作为水泥生产的原料和燃料,同时还可将有害有机物彻底分解,实现了含油污泥的资源化利用和无害化处理。王志强等将含油污泥与煤按一定质量比混合制成煤球,燃烧性能得到明显改善,同时也达到了在链条炉中燃烧的要求,实现了含油污泥的资源化利用。赵瑞玉等将正已烷、混合环烷烃和醇醚混合物复配,制得一种高效、低毒和环境友好的萃取剂,通过水辅助萃取法较好的实现了含油污泥中原油的回收。含油污泥减量化、无害化和资源化处理成为污泥处理技术发展的必然趋势。
本文针对延长油田含油污泥处理现状,分析研究了延长油田含油污泥的特性,开展了“筛分流化-化学调质-机械分离”处理工艺技术的研究,并开展了现场应用试验。
1 延长油田含油污泥来源及性质
1.1 含油污泥来源
油泥产生于石油开发、运输、炼制的整个过程。
1.1.1 原油开采过程
该类油泥主要来源于地面采油污水处理系统产生的油泥和在钻井、作业、管线穿孔时产生的落地油泥,一般具有含油量高、粘度大、脱水难等特点。
1.1.2 油田集输过程
该类油泥主要是指油罐、沉降罐、接转站、洗井水回收罐、隔油池产生的油泥。此类油泥成分复杂,含有大量的老化原油、蜡质、沥青质等,以及污水处理过程中加入的絮凝剂、杀菌剂和缓蚀阻垢剂等。
1.1.3 炼化过程
该类油泥主要是指隔油池和原油罐的底泥,以及浮选池的浮渣等。
1.2 含油污泥组成及性质
由于含油污泥的来源不同,其组成和性质也各不相同。延长油田开采过程中产生的含油污泥其含油率较高,含水率较低,污泥的可压缩性能差、相对密度高、粘度大。
1.3 含油污泥中原油族组分
油泥中原油的族组分含量与环境友好性有着密切联系,因此分析检测了含油污泥分离出原油的族组分含量,其结果见表2。从中可以看出,油泥中原油的主要成分是饱和烃与芳香烃,而芳香烃具有较高的毒性,因此,长期堆放油泥会对周边的土壤和水体产生严重污染。
1.4 含油污泥中原油的元素
含油污泥分离出的原油可以进行资源再利用,原油中C、N、S含量是衡量产品质量的重要指标,含油污泥中原油的主要组成元素是C,占元素总量的82%~86%,N、S含量相对较低。
2 实验部分
2.1 材料与仪器
油泥分离剂(自研);阳离子聚丙烯酰胺(分子量1200万);四氯化碳,光谱纯;石油醚,分析纯。
JLBG-129红外分光测油仪;TDL-40B型离心机;HH-S8数显恒温水浴锅;JJ-1精密增力电动搅拌器。
2.2 分析方法
本研究以含油量为主要分析评价指标,含油量参照国家环境保护标准《水质石油类和动植物油类的测定红外分光光度法》(HJ637-2012)进行测定。
3 含油污泥处理工艺流程
本工艺系统主要由油泥预处理系统、油泥分离系统、污泥脱水系统和油水分离系统组成。
3.1 油泥预处理系统
由于含油污泥具有来源广、成分复杂的特点,因此含油污泥在进入调质设备之前,必须辅以预处理将少量的固体杂质从油泥中去除,保证其处理效率。另外,在该工序中,通过蒸汽加热,可将油泥升温至60℃左右,并将油泥硫化成可流动状态。收集来的油泥一般具有较高的含水率和含油率,通过沉降除油处理,可以将上层的浮油提前收集,有助于减少后续处理负荷,提升处理效果。
3.2 油泥分离系统
实现油泥分离的关键之一是使吸附油解吸或破乳,为促使原油从泥砂表面分离,需对油泥进行调质处理,为原油从泥砂表面脱附创造更好的条件。含油污泥分离系统用来接收从预处理装置处理后的液态含油污泥,其顶部设有搅拌器,可对在罐入口处加药后的油泥进行搅拌匀化,进一步增强油和泥的脱附,有利于后续的离心处理;罐内还设有加热盘管,用于将油泥加热到60℃左右,从而增强油和泥的分离效果。经调质后的油泥,在罐内沉降一定时间后,罐体上部的浮油会从溢流口流出,直接进入油水分离系统进行分离,罐底沉降分离的污泥输送至污泥脱水系统进行离心分离。
3.3 污泥脱水系统
含油污泥经过调质分离后,使污泥的脱水和沉降性能得到了显著改善。处于乳化状态的原油在破乳剂的作用下,突破了油粒间的乳化膜,相互凝聚为较大的油粒,但难以直接与水、泥脱离,因而需要进入脱水系统进行油、水、固三相分离。该部分为油泥处理的核心部分。
3.4 油水分离系统
油水分离系统主要依靠油水的重力作用进行分离,并利用分离罐内的隔板将沉降后上层原油溢流到回收区外输;下层分离出的污水进入污水回收区,用作回掺水循环利用。
4 工艺运行参数优化
为了确保现场处理工艺最终的处理结果,首先在室内进行药剂用量的优选和设备运行参数的优化试验,用于指导现场生产装置的稳定运行。
4.1 药剂用量对剩余含油量的影响
油泥分离剂可投加在调质罐内,用以破坏油水界面,降低油水界面张力,使界面膜的黏度下降,利于油水破乳达到油水分离的目的。实验针对来源相同而含油率不同的含油污泥,在60℃温度下,考察药剂用量对剩余含油量的影响。
由考察结果可知,当油泥含油率一定时,随着分离剂用量的增加,污泥的清洗效果越好;初始的含油率越高,所需要的分离剂用量越多,当分离剂用量达到一定量后,药剂的破乳效果基本稳定。这是因为油泥分离剂可吸附到油-水界面,破坏原有的油-水界面保护层,此时油水界面张力随着药剂浓度的增加而迅速下降,从而使油粒相互靠近并聚结变大,最终实现油水分离;但当分离剂浓度过高时,油-水界面的吸附趋于饱和,分离剂会在油-水相聚集形成胶束,反而使界面张力上升,分离效果变差,剩余含油量略有增大。因此,污泥含油率为5%~30%时,最佳的药剂用量为10~20g/kg,现场可根据实际情况适当调整加药量。
4.2 含油污泥调质温度对剩余含油量的影响
为了提高含油污泥的调质效果,需要对调质罐中油泥继续进行加热。实验针对来源相同而含油率不同的含油污泥,在分离剂用量为10g/kg条件下,考察调质温度对剩余含油量的影响。
由考察结果可知,调质温度越高,调质效果越好,这主要是因为原油的黏度随着温度的升高而降低,流动性也随之增大,油水密度差变大,脱出的原油以小油粒形式不断上浮;同时,在较高温度时,原油在泥砂表面的润湿角较小,原油更易从泥砂表面剥离。但当温度过高(>65℃)时,处理药剂活性降低,且能耗也较高,同时原油中的低碳有机物也易挥发,污染环境。因此,从处理效果、经济和环境方面考虑,选用60℃为最佳处理温度。
4.3 离心机转速对剩余含油量的影响
实验选择同一调质罐内调质好的含油污泥,调整离心机转速,让污泥在不同的转速下进行离心处理,对离心分离出的泥样进行含油量检测。
由监测结果可知,当离心机转速低于3000r/min时,离心分离后的污泥中的含油量较高,当离心机转速高于3000r/min时,分离效果变好;之后继续增加离心机的转速,离心分离后的污泥中剩余含油量继续下降,但变化不大。考虑到随着转速的升高,离心机的轴瓦温度也随之升高,因此从安全和分离效果考虑,离心机的最佳转速设定在3000~3200r/min。
4.4 絮凝剂用量对剩余含油量的影响
絮凝剂投加在两相离心机前,便于固液分离。实验选用带正电和分子量高的阳离子聚丙烯酰胺作为絮凝剂,该絮凝剂可与体系中带负电的微粒发生电荷中和、吸附以及架桥作用,从而使微粒脱稳、絮凝,实现固液分离。在其他参数不变的情况下,加入不同量的阳离子聚丙烯酰胺,以剩余含油量为考察标准,优化阳离子聚丙烯酰胺的投加量。
由考察结果可知,当被处理的污泥含固率增加时,要保证离心分出的污泥效果,即含油量较低,絮凝剂的投加量也应随之增加;而当投加量到2.5g/kg以上时,处理效果变化不明显,甚至变差。因此,污泥含固率为1%~5%时,最佳的絮凝剂用量为1.5~2.5g/kg,现场可根据实际情况适当调整加药量。
5 现场应用
在对相关工艺参数优化的基础上,开展了现场应用试验。整个油泥处理设备主要由预处理系统、油泥分离系统、油水分离系统、污泥脱水系统、蒸汽加热系统及加药系统等组成。具有如下特点:①适用范围广,抗冲击能力强,可用于油气田各类含油污泥的处理;②处理能力10000t/a,每天可24h连续运转;③自动化程度高,设备运行、加药系统均可实现手动/自动操作,全程在线监测;④设备运行稳定,处理后污泥连续稳定达标。
设备调试运行6个月,对其运行结果进行测试跟踪。由测试结果可知,处理后污泥的剩余含油量低于20g/kg,含水率低于70%,达到了国内外含油污泥处理标准要求。
6 结论
针对延长油田含油污泥,分析研究了油泥的组成及性质,开展了含油污泥处理工艺技术的应用研究,并室内探索了最佳工艺运行参数,当油泥分离剂用量为10~20g/kg,调质温度为60℃,离心机转速为3000~3200r/min,絮凝剂用量为1.5~2.5g/kg时,含油污泥经筛分流化-化学调质-机械分离工艺处理后,污泥的剩余含油量可小于20g/kg;在此基础上,进行了现场应用试验,处理后污泥含油量小于20g/kg,含水率低于70%,达到了国内外含油污泥处理标准要求,该研究较好地解决了含油污泥污染问题,为国内含油污泥治理提供了技术借鉴。