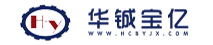
油田和石化公司的废水处理系统以及原油生产储运系统会产生大量污泥,包括隔油池和浮选池底泥、浮选池浮渣及剩余活性污泥等,统称“三泥”,目前我国每年产生的三泥总量总量达500余万t。笔者针对某石化公司污泥处理厂的工程实践,介绍了一套成熟可靠的污泥处理技术;污泥经过重力浓缩、离心脱水、超热蒸汽干化处理,含水率从97%~99%降至20%以下,可用于掺煤焚烧等综合利用,变废为宝。
1 工程概述
1.1 项目背景及现状
某石化公司现有污水处理站流程为隔油→浮选→AO生化处理,设计处理能力为600m3/h,三泥产量约为6.5万m3/a,约180m3/d,含水率为97%~99%。现有污泥处理工艺流程为污泥干化池→浓缩罐→压滤机,现有主要污泥处理设施为1座1800m3污泥干化池(12格),2座80m3污泥浓缩罐,1台污泥压滤机。
由于目前污水处理站长期超负荷运行,污泥池已积累大量油泥。存在的主要问题是污水站污油收集不当,污泥处理工艺设备老旧、处理能力不足,并缺少最终的无害化处理措施等。目前浓缩罐和压滤机基本处于停运状态,主要靠污泥池自然蒸发作用实现污泥减量化,效果较差,污泥排放压力越来越大。
1.2 工程概况
为解决以上污泥处理问题,需对现有污泥处理站进行改扩建,立项为某石化公司污泥综合处理及利用工程。该工程于2008年8月完成初步设计,于同年10月中旬完成施工图设计,预计明年6月投产。
1.3 处理流程
采用如下流程:污水处理站来三泥→重力浓缩罐→污泥提升泵→离心脱水机→螺旋输送机→蒸汽喷射超温干化装置→外运掺煤进燃煤锅炉焚烧。
1.4 设计规模
污泥浓缩罐的设计处理能力200m3/d,离心脱水机的设计处理能力为20m3/h,干化装置的设计规模为600kg/h。
1.5 自然地理及气象资料
该地区的极端最低和最高气温为-37.8℃和36.3℃,主导风向为西南风,冬季为西北风,年平均风速3.5m/s,最大风速18.7m/s。年平均相对湿度63%。年平均气压99.8kPa,年平均降水量441.4mm,年平均无霜期134~142天,年平均蒸发量1683.7mm。该地区土质为细砂、粉砂和中砂,标准地基强度为100kpa,最大冻土深度1.8m。
1.6 项目建设的意义
(1)国家和地方环保法律、法规要求必须要对含油污泥实行无害化处理。
(2)实现污泥无害化处理是中国石油集团公司建设环境友好型、资源节约型企业的需要,符合国家清洁生产及循环经济政策的要求。
(3)污泥综合利用工程建设是为了保证污水处理站的正常运行。
(4)实现含油污泥无害化、清洁化、资源化处理及综合利用具有良好的经济效益。按照国家发改委、环保总局等四部委发布2003年7月1日起施行的《排污费征收标准管理办法》,危险废物排污费征收标准为每次每吨1000元。该石化公司目前污泥实际产生量6.5万t/a,每年需支付的排污费就高达650多万元,改扩建项目建设后,仅节约排污费一项,4年就可以收回全部工程投资,经济效益显著。
2 主要构筑物及设备
2.1 污泥浓缩罐
2座,钢制锥底,尺寸Φ7.0×8.1m,有效容积200m3,设计停留时间为2d,污泥固体负荷为50kg/m2·d,设计进泥含水率97~99%,设计出泥含水率96~98%,体积可减少50%。为确保污泥浓缩罐正常运行,罐内设加热盘管,罐外保温。进泥口设在罐上部,罐内设有导流筒,出泥管线设在罐底。
2.2 离心脱水机
2台,处理规模20m3/h,污泥经自然沉降浓缩后,经污泥提升泵提升,进入离心脱水机进行脱水,脱水后泥饼含水率为75~80%。在进离心机前投加絮凝剂,在污泥提升泵吸泥口设置粉碎切割机。
2.3 超热蒸汽喷射干化装置
污泥的干化常采用焚烧技术、焦化处理、微波法、热解吸、热脱附法、调质脱水、高温处理、作为辅助燃料烧砖等。脱水后污泥焚烧技术的主要缺点是由于含水率在60%以上,含有轻质烃类,能耗和处理成本高、容易造成废气污染等,必须建造合适的尾气净化装置及热回收装置;由于运行成本过高,国内石化企业的焚烧装置多处于停产状态。焦化处理要求污泥的含油量必须达到50%以上,才能和焦化原料油按一定比例处理,该方法无法大规模推广,需进一步研究。微波法、热解吸、热脱附法等方法也仅限于研究阶段,没有工业应用实践。而脱水后污泥用作砖瓦厂烧砖也存在一定的安全隐患和环境风险。
本工程离心脱水后的泥饼加入进料斗后,在螺旋送料器作用下进入处理室,600℃的超高温蒸汽经特制的喷嘴高速喷出粉碎污泥,油分和水分同时被蒸发出来,被粉碎的细小颗粒连同蒸汽一起进入气旋室,在旋流作用下实现蒸汽与固体颗粒的分离,固体颗粒粉末状直接进入回收槽,可直接掺入热电厂煤粉中一起灼烧处理。蒸汽进入油水分离槽,经冷却后实现油水分离,原油可直接回收。
2007年5月该技术已经在新疆某石化公司应用并投产,目前运行正常。
2.4 循环冷却水系统
为实现高温含油污水的分离回收,需设计1套循环冷却水系统。设置了1台密闭式逆流玻璃钢冷却塔,Q=100m3/h,配套2台循环水泵,Q=100m3/h,H=20m,N=11kW,1用1备。为确保冷却塔在冬季的正常运行,要求冷却塔设有化冰管,并设有放空管。考虑防止滋生细菌和减缓腐蚀,冷却塔选择密闭式,并设有缓蚀、杀菌加药系统。
2.5 加药调质装置
1套,包括1套投加和储配药剂箱,2台加药泵(Q=2m3/h,H=60m,N=1.5kW)。根据试验结果和新疆某石化公司的应用经验,投加有机絮凝剂CPAM3,投加量为100~150mg/L;药剂投加点设在离心脱水机或浓缩罐进泥口。最佳反应温度选在40℃,最佳pH为7。工业应用中使用与离心机配套的加药装置就可以达到药剂与污泥混合的要求,无需再增加搅拌装置。
2.6 污泥池和干粉堆放场
污泥池1座,半地下钢筋混凝土结构,尺寸6m×6m×2.5m,地上高0.5m,有效容积80m3,进泥端顶部设有玻璃钢格栅板,用于拦截污泥中的较大污物;在出泥端设有集泥坑,池底设有0.01的坡度,坑内设有2台潜污泵。
干粉堆放场1座,地上式,有效容积40m3,用于堆放不能及时外运的干粉,堆放场设有防雨棚。
2.7 干粉掺煤进燃煤锅炉焚烧的综合利用
经超热蒸汽喷射处理后干粉中含油<1%,已不属于含油固体废物,不存在安全隐患,可直接掺入型煤进锅炉焚烧。进行焚烧的干化油泥必须满足以下条件:
①残渣中含水应<20%;
②残渣中含油不应超过5%,并且经碾压、撞击不结成饼状;
③脱除易挥发烃类;
④低含硫量。
蒸汽喷射处理后的干泥粉含水<20%,含油可控制在<1%,最低可降到0.08%,并且均为不易挥发的重组分,干泥呈细粉末状,可以满足上述要求。根据新疆某石化运行经验,产生的干粉热值在3600kcal/kg(1cal=4.1868J),相当于劣质煤,所以掺入干泥粉对煤的热值不会有太大的影响。
2.8 污泥恶臭治理技术
三泥处理系统恶臭源是浓泥池和污泥干化间,造成恶臭的主要组分为有机及无机硫化物、挥发性酚类等。浓泥池通气管接至脱臭塔,呼出气体经过脱臭塔床层催化剂吸附脱臭后放空。
干化处理间在干化装置进料斗设置密封盖,盖顶开孔,用软管将气体引至室外脱臭塔,脱臭后放空。脱臭塔考虑冷凝水的排除。
3 技术特点
(1)成熟技术与新技术相结合。离心脱水工艺技术成熟,改扩建后,采用高效的离心脱水机,并投加合适的脱水药剂,离心脱水后浓泥的含水率可降至75%左右。干化处理部分采用国际先进的含油污泥超热蒸汽处理技术,该技术为美国专利技术,已成功应用于壳牌石油公司和马来西亚石油公司的油泥处理,国内已成功应用于新疆某石化公司污泥处理工程,并积累了一些经验。该设备具有处理效果好、设备小巧、能耗低、回收油质纯净等优点。
(2)各工艺相对独立,方便运行管理。各处理工艺既连续,又可相对独立,各工艺及构筑物间设有跨越管线或进、出料口,保证污泥既可以全流程处理,由含水97%~99%左右的液态直接变为粉末状固态,又可只进行浓缩或离心脱水处理。同时,干化工艺段即可以承接经离心脱水后的浓泥,也可以承接外运来的含水95~97%的罐底泥。可以方便调整流程,便于运行管理。
(3)充分利用现有设施和有利条件,实现固体和液体废弃物的零排放。污泥综合处理工程建在原污泥站内,干化装置与离心脱水设施紧邻,便于浓缩污泥的运输。污泥站内现有电力、供水、消防及蒸汽管道等设施均可利用,浓泥脱水、干化处理过程中排出的含油污水排入现有回收水系统,输回废水处理站循环处理。
4 技术经济分析
本工程按含水率为98%的污泥计算,污泥设计规模为200m3/d,工程投资约为2600万元。
运行费用包括动力费、药剂费、水电费、蒸汽费、燃油费、工资福利费、折旧费、大修费、其它费用等。每吨湿泥动力消耗1(kW·h)/吨,电价按0.5元/kW·h计,则电费为0.5元/吨,按运行335d/a计,则动力费为3.5万元/a;处理单位污泥的药剂费5元/m3(药剂费1000元/d),药剂费为36.5万元/a;蒸汽耗量15t/d,蒸汽单价60元/t,蒸汽费33万元/a;清水消耗20m3/d,水价按2.17元m计,则水费为1.6万元/a;干化后污泥(含水率<20%)单位燃油消耗12L/t,干化后污泥量14.4t/d,燃油消耗为172.8L/d,单价5.3元/L,燃油费为33.5万元/a;设计定员10人,人均工资福利费30000元/a,则工资福利费30万元/a;直接工程费为2100万元,折旧费按其2.1%计为44万元/a;大修费按其1.5%计为31.5万元/a;其他费用按以上各费用之和的10%计为21.5万元/a。综上所述,运行费用为234.5万元/a,制水成本32.1元/吨湿泥。
5 结论
环保法规的日益严格和完善,含油污泥无害化、清洁化、资源化处理技术将成为污泥处理技术发展的必然趋势。国内外广泛研究的污泥无害化处理技术,主要有干燥焚烧、冷冻/解冻、生物降解、溶剂萃取、焦化处理、微波法、热解吸、热脱附法、调质脱水、高温处理技术等,但根据运行现状,采用离心脱水后进行超热蒸汽干化的高温处理技术,取得了较好的效果,具有一定的经济效益,社会和环境效益显著。