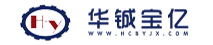
乳化含油废水是机械加工业和金属表面处理行业排放的一种较难处理的含油废水。因其中含有表面活性剂使油成为乳化液,油滴粒径极微小(一般小于10μm,大部分为0.1~2μm),在动力学上具有较强的稳定性,通常较难处理。乳化液中有机物含量很高,CODcr在通常为几万mg/L,其成分不仅仅是乳化油,还含有大量表面活性剂和其他添加剂。目前常使用的乳化油废水除油方法有多种(如隔油、离心、破乳、浮选、粗粒化、电解等),但这些方法都有其局限性,实际应用中通常是二三种方法联合使用,如盐析-气浮-吸附、破乳-混凝-气浮、隔油-微絮凝等。这些工艺在实际应用中均取得了较好的除油效果,一般出水中油的含量为几十mg/L,但CODcr仍较高(几百至几千mg/L),不能满足排放标准的要求。通常物化处理出水还需进行后续处理,后处理通常采用物理化学法(吸附、膜分离、纳滤等)和生物氧化法等手段。
上述工艺过程存在的主要问题是,单纯采用物理化学方法或者很难实现达标排放,或者因多级处理导致工艺复杂、流程长、成本过高、运行费过高、出水水质不稳定;特别是采用常规生物法时,需要对废水进行严格的预处理,且污泥负荷低、占地面积大,基建费用高。因此目前的乳化油废水处理技术虽得到广泛应用,但仍有很多不足之处,需要探索更为有效、简便、经济的处理工艺。
1 共降解膜生物反应器技术原理
共降解是指微生物利用一种容易降解的物质作为支持生长的营养基质,而同时降解另一种物质,但是后一种物质的降解并不支持微生物的生长,且往往都是难以降解的污染物质。前者通常称为第一基质,而后者称为第二基质或者共降解基质。
油类是一种烃类有机物,原理上可以利用微生物将其分解氧化成为CO2和水。但油类对微生物的生长有抑制作用,一般认为,流入到生物处理构筑物混合废水的含油浓度不能大于30mg/L,否则将影响活性污泥和生物膜的正常代谢过程。因而导致乳化油废水的生物处理负荷低、效率低,生物法常用于处理含量较低的溶解油,而不宜用于处理乳化油。研究发现,以葡萄糖、牛肉胨或者酵母提取物作为营养基质的微生物,能够共降解链烃类。因而采用葡萄糖等易氧化基质作为第一基质培养微生物,而将乳化油作为微生物的第二基质,利用共降解原理,驯化培养高效降解油类污染物的微生物群,可以大大提高生物处理负荷及效率,从而改变生物法不宜处理乳化油废水的传统认识。
乳化油废水的诸多处理方法中,物理、化学方法只能起到将污染物从水相转移至固相的作用,只有生物法利用微生物的氧化作用,才能将油彻底分解,从而最终消除了乳化油废水对环境的危害。因此,笔者在生物处理过程中,结合共降解原理和板式液中MBR开发出共降解MBR技术用于处理乳化油废水。上述工艺在北京北内集团和北京SMC工厂得到应用。工程实践表明,生物共降解与膜生物反应器的有机结合,可大大提高生物处理系统对进水中油的耐受浓度,反应器出水可以达到COD<100mg/L。
2 工程实例
2.1 工程概况
北内集团发动机生产车间不定期地排出少量含油废水,废水中含油主要为乳化油,根据来源和浓度可分为三类:高浓度废水为乳化液(CODcr约为70000mg/L,250m3/a)、中等浓度废水主要是各个车间的清洗液(CODcr1000~2000mg/L,600m3/a)、低浓度废水主要是各个车间的试车废水(CODcr100~500mgL,200m/a)。混合后的年平均进水CODcr仍接近2万mg/L。由于水量小(3.2m3/d)、不定期排放且浓度高,仅仅采用简单的物理化学方法除油难以实现达标排放,而采用传统的破乳-气浮-生物法,显然既不经济又难以稳定运行,最后选用隔油-破乳-共降解MBR-纳滤(NF)工艺,出水执行与《污水综合排放标准》(GB8978-1996)二级标准相当的标准,即CODcr150mg/L,BOD560mg/L,石油类10mg/L,SS200mg/L,色度80倍,pH6~9。
2.2 主要构筑物及设备参数
(1)破乳反应池。有效容积0.7m3,间歇操作,反应、静置1.5h。本工程的前期破乳试验中,选用了CaO、CaCl2、PAC、FeCl3进行测试,均取得了较好的破乳效果,虽然CaO破乳效果不是最佳,但该厂可以免费获得大量生石灰,是从经济上考虑,最终采用CaO为破乳剂,加药量为2.5g/L(8kg/d),产生浮渣约为0.28m3/d。
(2)MBR池。预处理后的各类乳化油废水经混合池混匀后,进入MBR,进水CODcr1400~2500mgL,油>500mg/L,仍属于高浓度含油废水,此进水水质显然不能为传统生物处理系统所接受。采用共降解理论,按1kgCODcr:(0.5~1)kg葡萄糖的比例,向混合池投加葡萄糖作为MBR内微生物代谢的营养基质,而乳化油废水作为第二基质被协同去除。同时适当投加磷酸氢二铵和碳酸氢铵,以补充微生物生长所需的N、P元素。MBR有效容积为5.25m3,容积负荷4.5kgCODcr/(m3·d),曝气量为25.5kgO2/d,DO2~5mg/L,膜组件1组(10片),膜分离面积8m2,MLSS10~15g/L,活性污泥为黄褐色。处理效果良好,出水CODcr<100mg/L,油<10mg/L。
(3)NF装置。流量为0.8m3/h,设计时对共降解-膜生物法的处理能力做了较为保守的估计,且由于乳化油废水的排水量和各种浓度废水的比例随生产需要变化较大,为确保系统出水始终达标,在生物处理后增设了一套NF装置。但在实际运行过程中,由于MBR出水完全能够实现达标排放,该装置一直未启动。
(4)污泥处理。该工程采用1台小型板框压滤机进行污泥脱水,污泥来源主要是破乳池的化学污泥和MBR反应池的剩余活性污泥,两种污泥产量均较小,且混合脱水后,泥饼稳定性好。
2.3 膜清洗与维护
本工程选用的板式膜具有较强的抗污能力,膜通量为0.4m3/(m2·d),运行6个月后膜阻力由0.03MPa升至0.06MPa,故采用0.5%~1%的NaClO和1%的柠檬酸进行在线清洗,2h后膜通量>0.4m3/(m2·d),但仍按设计膜通量0.4m3/(m2·d)运行。
3 运行效果
该工程于2005年11月投入使用,已稳定运行一年多,现场运行水质监测结果表明MBR出水即可实现达标排放。2006年1~6月MBR的运行数据表明:MBR平均进水CODcr1768mg/L,油589mg/L,pH7.5~8,SS约200mg/L;平均出水CODcr78.5mg/L,油3.9mg/L,pH6.5~7,SS未检出。且在一年多的运行中,膜分离性能良好,运行期间只进行2次的药液清洗(每半年1次),板式膜的交叉流自清洗功能得到了充分体现。
4 技术经济分析
该系统运行成本为药剂费8元/d,电费25元/d,运行费合计33元/d,折合为11元/m3。目前较为常用的废油减量化处理为焚烧法,其燃烧费用为1000~3000元/m3;超滤工艺处理费用为31.76元/m3,但经超滤浓缩处理后的废水仍需进一步处理。可见,该项技术的经济优势十分明显,同时通过微生物对油进行生物降解,使其无害化,具有焚烧法所不能比拟的环境效益。
5 结论
(1)共降解MBR技术是一项乳化油废水处理新工艺,微生物共降解理论与MBR的有机结合,突破了传统生物处理负荷低、效率低、受抑制等局限,将活性污泥进水油浓度的限制性要求由原来的30~50mg/L,扩大至500mg/L以上,极大地提高了生物法处理乳化油废水的能力,大大简化了工艺流程、减少了基建、运行费用。该技术对于水量小、浓度高、污染物具有特异性的其他废水同样适用。
(2)北内集团发动机生产车间乳化油废水处理工程实践中,采用隔油-破乳-共降解MBR工艺,MBR平均进水CODcr1768mg/L,油>500mg/L,经过微生物共降解和膜分离,出水为CODcr<100mg/L,油<10mg/L,达到《污水综合排放标准》(GB8978-1996)二级排放标准。