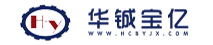
1 现状及问题
某采油厂一联合站投产于1987年,污水处理系统分为水驱污水处理站和聚驱污水处理站。水、聚驱污水处理站工艺均为横向流除油器除油,一、二次滤罐过滤工艺。其中聚驱系统于2000年正式投产,2001年起水质开始恶化。从2001年开始,对聚驱系统采用了多种方式进行治理,在一定程度上改善了水质处理效果,但没有从根本上解决水质处理难度大的问题。
2 原因分析
污水不达标及脱水器运行不稳定的原因主要有两个:一是水驱污水处理站处理液见聚后,含聚的污水处理难度加大,油、水、悬浮固体之间分离难度加大;二是联合站为密闭系统,在采出液和含油污水处理设施中,大量富集着含有黑色硫化物固体颗粒的污油,增大了含油污水处理难度。同时,这部分污油回收到原油脱水系统处理时又经常造成电脱水器运行不平稳。
综合分析认为,富含硫化物的老化油或回收油处理难度大是影响污水处理效果的主要原因之一。
3 解决方案
改造思路:将站内原油处理系统及污水处理系统回收的原油单独处理,使处理后的回收油达到或基本达到外输原油指标要求(含水0.5%),与正常处理的合格原油汇合后外输。结合联合站地面设施建设和原油处理生产情况,经过优选,确定改造方案为:利用现有电脱水器,新建加热炉,完善工艺,对老化油单独加热脱水处理。
为降低新建装置的处理负荷,并保证污油处理的平稳运行,对回收油工艺进行改造:一是将已建的500m3收油罐作为前端回收油储罐,1000m3、2000m3和3000m3沉降罐收油直接进500m3收油罐,然后泵输至新建加热炉加热;二是利用现有1000m3沉降罐,将1000m3沉降罐作为处理聚驱污水回收池回收水、横向流收油混合液的沉降罐使用,沉降后的水回收到2000m3沉降罐,油回收到500m3收油罐;三是为保证回收油处理系统的连续平稳运行,并且减少后端加热装置的建设规模,更换回收油泵;四是配套建设加药装置;五是利用3#电脱水器进行热化学脱水场所,处理后的老化油或回收油与净化油汇合后外输。
改造后运行方式为:500m3收油罐收油进新建加热炉加热(60~80℃),并与添加的正向、反向两种破乳剂充分混合,加热升温后的油进3#电脱水器,电脱水器内(不送电)经热化学作用进行油水分离,处理后的净化油(含水1%左右)与正常生产原油混合后外输(含水小于0.3%),脱水器出油、放水工艺不变。经计算,采用该种运行方式,其余2台脱水器正常生产时,电脱水负荷率为30.3%。
4 新工艺特点
一是对老化油进行集中、连续处理,避免回收油时对系统的冲击,保证生产运行的稳定性。
二是老化油回收及处理单成系统,老化油可及时处理,确保老化油中硫化物等杂质不能够在站内沉降罐、回收水池等容器内逐渐聚集,从而保证了原油处理系统放水指标合格、稳定,避免水质恶化。
三是聚驱回收水池内污水可以通过1000m3沉降罐进行一次沉降,避免回收水对聚驱污水处理系统的影响。
四是充分利用已建设备剩余能力,减少一次性建设投资。利用已建3#电脱水器剩余能力,减少一次性改造投资107×104元。
5 结语
(1)联合站采用新工艺后可以提高污油回收率,每年增加回收污油163.5t,增效28.13×104元。
(2)节约原油重复处理费用,包括节约电费、燃气费、药剂费,合计3.84×104元。
(3)减少污水处理系统负荷,减少反冲洗次数、水量、回收水量,累计节约用电36.5×104kW·h,节约运行费用18.78×104元。
(4)改造后,电脱水器运行平稳,可减轻后续处理工艺的负荷;污水处理系统运行平稳,保证了污水水质,延长滤料使用寿命;由于回收油量、反冲洗次数、水量等减少,降低了管理难度及工人的劳动强度;避免了不合格水质对油层的污染,潜在效益巨大;新工艺对其它联合站的回收油或老化油处理工艺有良好的借鉴作用,整体效益潜力巨大。