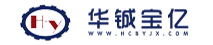
目前,卧螺离心机在石油石化企业污水处理厂污泥处理单元中应用越来越广泛,它具有分离效果好,工作效率高,使用管理维护方便等优点。本文根据生产中的大量试验结果,分析了影响离心机处理污泥效果的主要因素,总结了使离心机稳定运行的管理方法。
一、卧螺离心机结构特点及工作原理
卧螺离心机主要由高速旋转的转鼓,与转鼓转向相同转速略低的螺旋和差速器等部件组成。当污泥通过中心供料管进入离心机转鼓腔后,高速旋转的转鼓产生强大的离心力,密度大的固体沉降到转鼓壁上。轻相的澄清液流向液相排出口,经由可调节液池深度的可调堰板排出离心机转筒。沉积在转筒壁上的固体由螺旋输送器传送到转筒体的锥体端,从排料口排入固体集料箱。
二、影响卧螺离心机处理污泥效果的因素
影响卧螺离心机脱水效果的因素很多,并且各个因素又互相影响,寻找到污泥、设备和絮凝剂三者之间的运行组合参数十分关键。经过生产中大量的实验和不断调试,找出影响卧螺离心机脱水效果的主要因素及控制参数范围。
1.转速
根据离心机的工作原理,转速越高,离心力越大,有助于提高泥饼含固率,滤饼越干,滤后液越清,但并不是说转速越高越好,对于易沉降的介质,转速越高轴功率越大,容易引起机械或固料来不及推出,造成物料堵塞。因此要根据离心机的功率与进料、脱水效果等因素来选择合适的转速。试验结果表明,在石油石化企业,离心机的转速控制在2000-3000转/分,能取得良好的处理效果。
2.差转速
差转速是转鼓与螺旋转速之差,直接影响排渣能力,泥饼干度和滤液质量,是离心机运行中重要的可调节参数之一。提高差转速,有利于提高排渣能力,但沉渣脱水时间会缩短,脱水后泥饼含水率大,同时过大差转速会使螺旋对澄清区液池的扰动加大,滤液质量相对差一些。降低差转速,会加大沉渣厚度,沉渣脱水时间增长,脱水后泥饼含水率降低,同时螺旋对澄清区物料的扰动小,滤液质量也相对好些,但会增大螺旋推料的负荷,应防止排渣量减小造成离心机内沉渣不能及时排除而引起的堵料现象。因此,应根据物料性质、处理量大小,处理要求及离心机结构参数来确定差转速大小。在石油石化企业,离心机的差转速一般控制在1-5转/分。
3.絮凝剂
3.1絮凝剂的选择
为改善污泥脱水性能,进行机械脱水前一般应均匀加入适量的有机高分子絮凝剂。在石油石化企业,根据污水污泥性质和特点,选择的是聚丙烯酰胺(PAM),使污泥固相和液相分离后更易于脱水。
3.2聚丙烯酰胺的浓度
絮凝剂配置浓度过低可导致药液有效成分供应不足,则难以形成相应干度的泥饼,影响上清液质量;而絮凝剂浓度太大,絮凝剂高分子链上的活性基团则会由于相互屏蔽、包裹而使有效成分难以充分发挥功效,从而造成药剂的浪费,综上考虑及实验分析,聚丙烯酰胺的配置浓度设定为2‰。
3.3聚丙烯酰胺的投加
车间将絮凝剂投加位置设定在离心机的进料口处,与污泥同时进入转鼓腔内,瞬间絮凝并通过离心机作用使泥水快速分离,如果污泥中提前加入絮凝剂,在进入转鼓腔之前絮凝,形成大的絮团,絮团进入离心机后,将被打碎,使泥水不易分离,分离效果变差。另外絮凝剂的投加量一定要有准确的可调的手段。投加量小起不到作用,絮凝效果差;而投加量大一方面造成浪费,另一方面加药量超过一定的限度会形成反胶体,使得介质无法分离。选用螺杆泵和流量计来控制絮凝剂的均匀投加,用量一般为5-8Kg/TDS。
三、结语
实践证明,应用离心机处理污水污泥,不但处理能力大,效果好,而且自动化程度高。通过实际操作总结得出各参数的合适控制范围:离心机转速控制在2000-3200转/分,差转速控制在1-5转/分,聚丙烯酰胺浓度控制在2‰-2.5‰,处理后泥饼含水率在70%-80%。