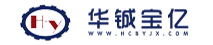
目前,油田产生的含油污泥主要来自两个方面:一是在集输、处理过程中沉积在各类容器、油水储罐和回收水池等地面设施中,定期产生的含油污泥,这类设施一般包括:污水沉降罐、除油罐、油罐、电脱水器、回收水池、气浮和过滤反洗等。二是由于油井作业、集输油管道腐蚀穿孔等产生的落地污泥。
目前,油田污泥产生后基本上采取直接掩埋或就地固化的处理方式,由于含油污泥已被列入《国家危险废物目录》中的含油废物类,且污泥中往往含油重金属等有害物质,如果不进行无害化处理,不仅造成石油资源的浪费,同时也会对环境产生放射性污染。其中第一类污泥约占总量的85%以上,这里主要研究采出水处理站(水区)处理过程中产生的污泥。
一、含油污泥特征及处置标准
采出水处理站具有采出水处理和注水功能,并管辖2条调水线,主要负责含油污水的净化处理、调水以及注水任务,采出水设计处理能力5500m³/d,目前处理量3500m³/d。该站采出水处理工艺为气浮+流砂装置,并配套负压排泥、浮筒收油、电解盐杀菌等辅助工艺。油区来水先进入4具700m³沉降罐进行沉降,沉降后进入2具700m³调节罐,经提升泵,进入气浮流砂过滤装置进行处理,合格污水进入3具500m³注水罐;再经喂水泵、注水泵、配水间、到单井,再由单井进入地层。
油田含油污泥来源广泛,组分也非常复杂,一般含有大量老化油、蜡质、沥青质、胶体、固体悬浮液、细菌、盐类等,还包括生产过程中投加的各种药剂。在实验室条件下,将该站气浮、过滤反洗和沉降、调节罐内产生的含油污泥用石油醚进行清洗后,经干燥、称重等过程,测试含油量、含水率和固含量。测试分析显示,3种污泥每天产泥量大概为375m³,污泥含油在1%~15%,含水率在93%~98%,含固体悬浮物在1%~10%,其特点是含油、含固体悬浮物高且很不稳定,杂质多,处理难度大。
经有机溶剂萃取后,用放射性射线分析仪对以上这几种污泥来源中重金属含量进行测定,可以看出该站污泥中六种重金属(Zn、Cu、Ni、Pb、Cd、Cr)含量均小于《农用污泥中污染物控制标准》(GB 4284-1984)中相应重金属排放含量控制的限度,故在后续处理过程中无需考虑重金属无害化处理。
取该站对应区块的普通原油与该采出水处理站污泥样品中分离出的原油进行对比,按照GB/T 2538-1998《原油实验法》、SY/T 5119《岩石中可溶有机物及原油族组分分析》中的测试方法对原油物性进行测定。结果证明,污泥分离出的原油只是在含蜡量和胶质沥青含量上有所增多,造成密度、黏度和原油凝固点有所上升,但与原油品性质差异不大,应该对污泥进行资源化处理,回收其中的油组分。
在《国家废弃物》名录中,虽然将含油污泥定为危险固体废物,但并没有处理后定量的指标,现在含油污泥的处理多依照GB 4284-1984,要求土壤中含油量小于或等于3000mg/Kg(即3‰);黑龙江省地标DB 23-2010《油田含油污泥综合利用污染控制指标》将处理标准分为两种,其中农用污泥与GB 4284-1984的要求一致,另外用于垫井场和通井路的污泥要求含油量小于或等于20000mg/Kg(即2%)。
二、主体工艺
采用热洗+微生物+叠螺脱水处理技术,整个处理工艺分为三个部分:预处理系统、生化处理系统和污泥脱水系统。
1.油泥分离剂室内试验
含油污泥的热洗药剂种类很多,一般要求热洗药剂满足两个条件,一是在搅拌状态下可降低油水界面张力,增加乳化效果;二是在静置状态下,加速油水分离。挨次选用十六烷基三甲基氯化铵、盐酸、聚丙二醇溶于水中,恒温反应1~2h后加入过硫酸盐溶液,在恒温微波2~3h,得到油泥分离剂,通过搅拌等机械作用,使生物油泥分离剂与污泥充分混合均匀,加速油、水、泥三相分离。
①剂泥比对污泥分离效果测定。取污泥100g,分别按照1:1,2:1,3:1,4:1,5:1,6:1,7:1,8:1的剂泥比加入配置好的油泥分离剂,在实验温度40℃,搅拌速率300r/min,搅拌时间30min后,再用石油醚清洗污泥,测定污泥中原油回收率及固含量。结果显示,原油回收率先随着油泥分离剂计量的增加而上升,而后逐渐下降,污泥中固含量先减少后增加,主要是由于随着药剂剂量增加,药剂中的水含量越多,在搅拌的作用下会与污泥中的油形成水包油的状态,加速乳化,反而不利于油、泥、水的三相分离。在剂泥比3:1的情况下,原油回收率可达93%,固含量为3.6%,因此合适的剂泥比为3:1。
②不同实验温度下污泥分离效果测定。不同的实验温度对油、泥、水三相之间的界面结合力和界面强度影响很大。较搅拌速率和搅拌时间相比,对污泥的分离效果影响更大,在剂泥比3:1,搅拌速率300r/min、搅拌时间30min的情况下,选择实验温度30、35、40、45、50、55、60、65℃进行测定。结果显示,随着温度的升高,原油回收率逐步上升,而后趋于平稳,固含量逐步下降,在55℃以上又逐渐增加,主要是由于温度的上升,有助于药剂和污泥之间的结合。同时,可加速破坏分子之间的氢键作用,但温度上升到一定程度后,污泥的流动性反而加强,固相和液相的分离更加困难。结果还显示,由于后期需用微生物进行生物处理,微生物菌种的温度不宜过高,否则会影响菌种的培养和生长,因此选择搅拌温度为45℃。
③不同搅拌速率、不同搅拌时间下的污泥分离效果测定。在剂泥比3:1、搅拌温度45℃、搅拌时间30min的条件下,选择300、400、500、600、700、800r/min这几种搅拌速率进行原油收率和固含量测定。结果显示,搅拌速率在600r/min时,原油回收率极高,可达90%,固含量极低为2.2%,随着搅拌速率的上升,原油回收率有所下降,固含量有所提高,主要是因为搅拌速率过高会加速固相和液相的乳化程度,因此搅拌速率在600r/min左右即可。
在剂泥比3:1、搅拌温度45℃、搅拌速度600r/min的条件下,选择30、40、50、60、70、80、90min这几种搅拌时间进行分离效果测定。结果显示,随着搅拌时间的增加,固含量先是大幅降低,在70min后趋于平稳,原油回收率先上升,之后在60min也趋于平稳,因此合适的搅拌时间为60~70min。
针对上述室内试验,将剂泥比设置为3:1,搅拌温度45℃,搅拌速度600r/min,搅拌时间60~70min。
2.热洗处理系统
将气浮刮渣、沉降罐和调节罐底部污泥排至收集池,如遇污泥流动性不好,可与回掺水混合,并通过蒸汽加热,使污泥流态化,然后用泵打入预处理装置,在预处理装置中投加高效生物油泥分离剂进行热洗。分离的油上浮至表面,通过收油机收至回收油罐,由于过滤器反洗产生的污泥含水率较高,一般不单独处理,而是与下层水和污泥混合后进入生物处理系统。处理后可将原先含油15%左右的污泥处理至含油小于或等于3%。
3.生物处理系统
设置生物处理系统,经预处理系统处理后的污泥与过滤反洗水混合进入污泥生物处理系统,在生物反应系统中投加“倍加清”专性微生物菌种,经过曝气生物反应后,专性微生物把泥、水中油、有机类污染物进行生物降解,保持在30℃、150r/min的条件下培养,经过好氧处理30天,污泥、水含油率达到此阶段的设计要求,处理后的污泥中油含量小于或等于3000mg/Kg,满足了GB 4284的含油量要求。水进入回收水罐回掺至前级处理系统或泵至污水处理系统,污泥进入后级污泥脱水系统。
4.污泥脱水处理系统
经前级生物系统处理后排放的污泥含油量已很低,但含水率仍然在95%,如果直接拉运,体积庞大且费用昂贵,需要进行脱水处理,减少污泥体积。
叠螺式污泥脱水系统主要由叠螺机和加药装置组成。叠螺机主体是由固定环和游动环相互层叠,螺旋推力轴贯穿其中组成,分为浓缩区和脱水区,固定环和游动环之间的滤缝以及螺旋轴螺距,由浓缩区至脱水区逐渐变小,加药装置由计量槽、絮凝混合槽和加药泵组成。
运行过程中污泥通过外力提升被输送至叠螺污泥脱水系统的计量槽内,加药泵根据污泥流量,按设定加药量向混合槽内投加絮凝剂,通过搅拌使污泥与药剂在絮凝混合槽内充分作用,形成矾花的污泥自流进入叠螺主体,液相在浓缩区通过游动环和固定环之间的滤缝排出,固相物质截留在腔体内部;螺旋推力轴在电动机的带动下,推动轴圆周外的多重游动环上下运动,使浓缩区截留的固相物质,被螺旋轴推至污泥脱水区,利用螺旋轴矩的不断收缩,增强内压,使滤饼含固量不断提高,在螺旋推力轴连续运转推动下,液相连续分离流出,污泥不断受挤压脱水排出,从而达到污泥浓缩脱水的目的。
浓缩处理后的污泥加入助凝剂后进入叠螺污泥脱水机脱水,使泥水分离,脱水后的水收集后进入回收水罐,经叠螺机脱水后污泥含水率在75%~80%,处理前污泥含水率为93%~98%,取97%,脱水后含水率按80%计算,体积可降低6.666倍,大大降低了外运体积,且含油率为2%已达到了资源化的标准。
三、效果评价和效益分析
分别取连续8天不同时间段的污泥进行取样检测,经油区沉降后污泥来样含油量相对稳定,平均在11366mg/Kg左右,泥中含油波动不是很大,经生物+叠螺机脱水处理技术处理后,泥中含油平均为958mg/Kg,平均去除率达到91.55%,满足GB 4284中含油量小于或等于3000mg/Kg的要求,达到了资源化利用的条件。
四、结论
1.经过一系列的室内试验,对油泥分离剂进行了工艺参数优化,将剂泥比设置为3:1,搅拌温度45℃,搅拌速率600r/min,搅拌时间60~70min。
2.经热洗+微生物+叠螺脱水技术处理后的污泥达到了减量化、无害化、资源化的处理要求,满足了国家和当地环保要求。
3.下一步要继续针对钻井、油水井作业、管道泄漏等的废液、废渣实施不落地回收,并进行集中处理。
4.含油污泥处理技术多种多样,单一技术往往很难达到预期效果,下一步要考虑多种技术的耦合,对污泥进行分级、分阶段处理,形成不同种类污泥处理的标准化工艺。