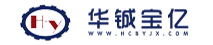
一、工艺流程
煤在高温炼焦炉中产生焦炭、煤焦油、氨水、苯、煤气等产物,焦炭经冷却后直接炼钢,而煤焦油、氨水、苯、煤气等物质经除冷器降温后进入水汽分离器,将煤焦油、氨水、煤气分离。由于煤气的主要成分是硫化氢,煤气进预冷塔降温至25~30℃后进入再生塔,加催化剂、曝气,产生泡沫硫,使用离心机泵将泡沫硫打进卧螺离心机进行固液分离,分离后的清液排入再生塔循环使用,分离后的硫膏经加热釜生产出成品硫膏。
二、离心机配置、工作原理、技术特性
1.1 LW520×2080离心机配置
1.1.1 组成
LW520×2080离心机是专门针对硫泡沫固液分离研发生产的卧式螺旋卸料沉降离心机,离心机主要由主电机、副电机、转鼓部件、螺旋部件、轴承座部件、机座部件、行星齿轮差速器等部分组成。其主要技术参数如下:
转鼓内直径:520mm。
设计转速:3000r/min。
分离因素:2620。
工作转速:1800r/min。
主电机功率:55kW。
副电机功率:18.5kW。
1.1.2 工作原理
离心机的工作原理为利用离心力的作用,使具有不同比重的物体分开。含悬浮硫的硫泡沫经由进料泵,经进料管进入离心机转鼓内部,在高速旋转所产生的离心力的作用下,因固液二相存在比重差,而实现分层,比重较大的固体颗粒沉积在转鼓内壁上被螺旋输送器不断推出转鼓出渣口,而分离后的清液则经液层调节板开口溢流出转鼓,螺旋与转鼓之间的转速差是通过差速器来实现的,转速差的大小通过副电机进行调节,因此实现了离心机硫泡沫的连续分离。
1.2 技术特性
1.2.1 采用大长径比技术
大长径比可增加物料的沉降区域,延长物料在离心机内的停留时间,使固形物去除率提高。
1.2.2 独特的涡流式出料部位设计
螺旋卸料器的出料部位采用涡流式结构,符合液体力学的“双S”结构设计原理,可加速物料快速进入转鼓,缩短物料与液池接触距离,减少进料对已形成的分离固相的扰动,提高处理能力,避免螺旋内的堵塞和进料管抱死现象。在物料出口处堆焊碳化钨硬质合金,增加了螺旋体的使用寿命。
1.2.3 独特的泡沫破碎装置
由于大量泡沫的存在,直接影响了固体的回收率,针对这一特性,离心机配备了泡沫破碎装置——漂浮物捕捉器。泡沫气泡破碎后,附着在气泡表面的固体颗粒发生了沉降,固体颗粒被螺旋体从渣相推出,从而提高了液相的回收率。
1.2.4 关键部件采用高性能不锈钢材料
针对泡沫硫物料颗粒较细小、硫酸粒子含量较高等特性,为保证离心机运行稳定性和使用寿命,转鼓部件采用高强度、耐腐蚀性更好的SAF2205,而螺旋部件采用316L材料。
1.2.5 先进的双电机双变频共直流母线和恒扭矩控制技术
离心机的主副电机各采用一台高性能矢量变频器控制,副电机在差速作用下始终处于发电机状态,由于采用变频器共直流母线技术,副变频器能很好地将副电机产生的电能通过转化供主电机使用,从而达到节能降耗目的。通过双电机双变频控制技术,可实现对离心机差速的无级可调,具有反应速度快,扭矩检测准确,扭矩控制稳定,故障率低等优点。
三、影响离心机分离效果的因素
1.1 转速对离心机分离效果的影响
理论上,转速越高,物料受到离心力越大,固体颗粒沉降速度越快,分离效果就越好。但对于硫泡沫物料,因其物料中所含灰份为70%左右,过高的转速会加快螺旋叶片对分离物料的扰动,从而影响到渣、液二相的分离效果。经过测试,较佳的转速在1800r/min为宜。
1.2 液层深度对分离效果的影响
提高液层深度会降低液相中的含固率,增加固相中的含水率;降低液层深度则反之。对液层深度的调整需要从离心机分离后的渣相含水率与清液含固率综合考虑。经过测试,液层深度控制在159mm档位,硫膏的含水率与清液的含渣率在较佳状态。
1.3 转鼓与螺旋转速差对分离效果的影响
转鼓与螺旋转速差也就是差转速度,差转速决定了螺旋推料器的排料速度,在转速恒定的情况下,差转速增大,清液在被排出离心机之前经过的路径将增加,可以降低液相的含固率,但由于螺旋排料速度会加快而减少了固相部分在离心机内的停留时间,从而影响到分离出的硫膏的干度。经过测试,差转速控制在14~16r/min,硫膏的含水率与清液的含渣率在较佳状态。
1.4 处理量对分离效果的影响
处理量的调整是一个综合过程,要根据处理效果和主机负荷来决定;经现场分离调试,LW520×2080离心机的处理量在25m³/h时,渣相含水率与液相含固率都处于较佳的分离状态。
四、优势对比
与板框压滤机相比较,卧螺离心机具有以下优势:
①板框压滤机占地面积大,安装调试复杂,维修费用较高;而卧螺离心机占地面积小,安装调试简单,现场维护方便。
②板框压滤机为间歇性工作,需要定期排渣和清洁滤布,工作效率低;而卧螺离心机在工作时的进料、分离、卸料等工序是在密闭的环境中连续自动进行,工作效率高,现场环境好。
③板框压滤机压滤出的硫膏含水率在45%左右,液相含固率0.5%~0.8%;而卧螺离心机分离出的硫膏含水率≤40%,由于采用了特殊结构的漂浮物捕捉器,分离出的液相含固率≤0.02%。
五、结语
通过在河北迁安中化煤化工、唐山达峰焦化等几家国内煤化工企业的分离实践证明,无论从分离效果、处理量、液相纯净度,还是运营成本、离心机稳定性、可靠性,卧螺离心机都是一种较为理想的选择。