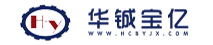
淀粉糖是以淀粉为原料通过水解获得的甜味剂,可部分替代蔗糖用于食品加工。近年来,我国淀粉糖行业发展迅速,2013年产能和产量达到历史峰值约800万吨,之后由于玉米价格、蔗糖价格等诸多因素影响,2016年全国淀粉糖总产量686万吨。目前我国淀粉糖生产主要以双酶法工艺为主,传统工艺中,淀粉乳经过液化工序后,淀粉分子被α淀粉酶作用分解成多糖,DE值12~18左右,而淀粉中所含的蛋白质等杂质会发生絮凝,液化液在糖化工序中根据添加酶品种不同得到不同组分和DE值的糖化液,而蛋白质等杂质会发生分层,一部分会漂浮在糖化罐顶部,一部分会沉淀在糖化罐底部,糖化结束后的糖液传统工艺一般采用真空转鼓或者板框压滤机来去除淀粉中带来的1%~1.5%的蛋白质、脂肪等杂质。由于真空转鼓和板框压滤机都需要经过预涂硅藻土或珍珠岩等助滤剂才能进行糖液过滤,所以过滤下来蛋白质和脂肪等杂质与助滤剂混合,其利用价值大大降低。
卧螺离心机作为一种新型分离设备,主要部件由转鼓、螺旋推进器和差速系统等构成,分离过程为:物料在转鼓内壁以设计速度高速旋转,沿着转鼓壳体形成一个同心液层,成为液环层。物料内所含的固体在离心力作用下沉积到转鼓上,再通过螺旋的运转将干物料推至转鼓锥端,上清液则从转鼓大端排出,实现固液分离。分离过程中不需要添加任何助滤剂,确保分离出的重相无外来添加的杂质。卧螺离心机具有处理能力大、连续化作业和自动化程度高等优点,已经在制药、污泥脱水、化工等行业成功应用。卧螺离心机在淀粉糖生产中比较少见,仅有少数报道在柠檬酸清液发酵生产中采用。
本研究对卧螺离心机在玉米淀粉糖生产过程中蛋白质分离的工艺参数和运行效果进行分析,为卧螺离心机用于淀粉糖和蛋白质分离提供参考。
一、仪器和方法
1.1 仪器和设备
STNX944S卧螺离心机,AL104电子天平,DHG-9240A电热鼓风干燥箱,DTL-5台式离心机。
1.2 试验方法
1.2.1 工艺流程
双酶法生产淀粉糖工艺中,采用卧螺离心机替代板框过滤机或者真空转鼓过滤机,分别对液化液和糖化液进行蛋白质分离,以分析不同工艺方案蛋白质的分离效果。
1.2.2 操作要点
经过液化工段之后的液化液温度为95~98℃,工艺中设置有两级换热器,一级换热器液化液与后续工段的糖浆进行料料换热,换热后温度约为75~80℃,二级换热器液化液与冷却水换热,换热后温度为糖化要求的60℃,糖化过程维持温度不变。
为试验卧螺离心机用于液化和糖化后分离固形物的效果,工艺中通过管道和阀门的切换可以将卧螺离心机分别应用于液化后和糖化后分离固形物。由于卧螺离心机工作温度为100℃,出于保护卧螺离心机的目的,卧螺离心机处理一级换热后的液化液。
1.2.3 测定方法
悬浮液固形物含量=M1/M2×100%,式中M1为固形物质量,g;M2为液化液或糖化液质量,g。
含水率=(M1-M2)/M1×100%,式中,M1为烘干前固体质量,g;M2为烘干后固体质量,g。
固相回收率=(C1-C2)/C1×100%,式中,C1为分离前悬浮液固形物浓度,%;C2为分离后悬浮液固形物浓度,%。
二、结果与分析
2.1 卧螺离心机用于分离液化液和糖化液效果对比
卧螺离心机分离液化液和糖化液,糖化液经卧螺离心机分离出的固相水分明显高于液化液分离出的固相,运行过程中糖化液分离出的固相呈糊状,在螺旋输送机中黏着在螺旋和外壁上,烘干困难。而液化液分离出的固相呈块状,容易烘干。原因是物料的黏度影响了固形物的分离,物料的黏度是阻碍其中的固体颗粒沉降速度的重要因素之一,物料温度越高,液相黏度越低,越有利于分离。黏度过高,将使离心分离变得十分困难,用离心机处理这种物料时分离效果可能极差,因为此时的物料不具备很好的自然沉降性能。糖化液温度为60℃,而液化液经过一级换热后温度为75~80℃,液化液黏度低于糖化液黏度,造成糖化液固相分离困难。因此,卧螺离心机适合于分离一级换热降温后的液化液。
2.2 不同进料量对卧螺离心机分离效果的影响
以液化液为原料,通过调节卧螺离心机进料量,随着进料流量增加,固相回收率逐渐降低,主要原因是料液进入卧螺离心机后,固相颗粒在离心力作用下沿径向沉降,直径大的颗粒沉降速度快,直径小的颗粒沉降速度慢,随着进料量增加,流速增加,造成直径小的颗粒在卧螺离心机中停留时间少于沉降所需时间,进而造成卧螺离心机转鼓内的固相层厚度增加,固相和液相分界线向转鼓中心移动,液相截面积减少,分界线附近还未完成沉降,比较松散的颗粒容易被液相冲刷带走,降低固相回收率。进料流量在13~14m³/h时,固相回收率变化不大,流量大于14m³/h之后,随着进料流量逐步增加,固相回收率逐步降低,因此,对于STNX944S卧螺离心机而言,进料流量控制在14m³/h左右运行效果较佳。
2.3 不同差速度对卧螺离心机分离效果的影响
通过调节差速器参数设置,随着差速度增加,固相含水率不断增加,而固相回收率先增加后趋于平缓。差速度是指卧螺离心机运行过程中转鼓和螺旋的旋转速度差,差速度较低时,螺旋推出固相的速度降低,固相在转鼓中受离心力作用时间较长,所以固相含水率较低,但是由于停留时间长,造成沉降下来的固相又渗透到液相中,造成固相回收率降低。差速度较高时,螺旋推出固相的速度提高,固相在转鼓中受离心力作用时间短,所以固相含水率较高,但由于停留时间短,沉降下来的固相渗透到液相中的几率降低,因此,固相回收率较高。差速度为10r/min时,蛋白质分离效果较好。
2.4 卧螺离心机与板框过滤糖液固形物的对比
板框过滤机过滤糖液为间歇操作过程,每个周期包括预涂、进料、压榨、卸料和清洗滤布等多个步骤,预涂的硅藻土或者珍珠岩与糖液中固形物混合在一起,固相无法回收利用。卸料和清洗滤布全部由人工完成,劳动强度大且卫生条件较差,并且板框过滤机过滤出的糖液固形物含水率约为40%~50%。
卧螺离心机过滤糖液为连续操作过程,糖液进入卧螺离心机连续分离出液相和固相,分离过程无需添加助滤剂,固相可回收利用。工人劳动强度低,并且整个操作过程在密闭环境下进行,卫生条件好。卧螺离心机分离出的糖液固形物含水率约为25%~35%。对比发现,采用卧螺离心机过滤糖液可明显调高液相回收率,降低固相烘干能耗。
2.5 卧螺离心机与板框过滤糖液固形物经济效益分析
以年产10万吨淀粉糖浆生产线为例,卧螺离心机与板框过滤机相比,每年可增加副产品收入约131.6万元,成本降低10.6万元,综合计算每年可增加收入142.2万元。
三、结论
卧螺离心机能够较好的分离淀粉糖生产中由淀粉原来带来的蛋白质、脂肪和灰分等杂质,具有自动化程度高、分离效果好、运行平稳等优点,可完全替代传统过滤设备进行糖液过滤。
STNV944S卧螺离心机适宜运行参数为:进料温度75~80℃,进料流量14~14.5m³/h,差速度10r/min。
卧螺离心机与板框过滤机相比,具有无助滤剂添加、副产品回收价值高、劳动强度低等优点,通过副产品回收可增加企业效益。