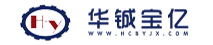
焦油含水、带渣量的控制是焦油加工的重要环节。2005年湘潭钢铁公司焦化厂使用了三相卧螺离心机,经过近2个月的调试,焦油含水、带渣量明显下降,质量有了很大提高。
一、存在问题
自从4#焦炉投产和实行高压氨水无烟装煤后,该厂焦油带渣带水严重,再加上机械化氨水澄清槽实行间断性压油,靠操作经验判断油位、油质,导致压出的焦油含水量达10%,带渣更是一大难题。由于焦油渣沉积覆盖了加热器,使焦油温度无法达到80~90℃,焦油含水达不到4%的质量要求。焦油加工系统常常出现阻力大、炉管穿孔等问题,在生产中需将焦油再次脱水,这对设备的腐蚀非常大,给生产带来恶性循环,增加了劳动强度和生产成本,同时减少了焦油贮槽的有效容积。
二、方案选择
经方案比较后,我厂决定使用三相卧螺离心机,并将生产工艺改为:从机械化氨水澄清槽压出的焦油进入新焦油中间槽,用焦油泵将焦油送入离心机处理。分离出的焦油送入焦油贮槽再次脱水,氨水进入地下槽,焦油渣进入渣池后送到煤场处理,将原有的焦油中间槽保留作为备用。另外,在新建焦油中间槽内增添搅拌器和加热器,以防止焦油渣沉积。
2.1 离心机的生产原理
该厂使用的Z4E-4/441卧螺离心机,处理能力(理论值)为15m³/h,转筒速度为4000r/min(可调),转筒与螺旋差速为1-20r/min。其工作原理为:物料通过供料管进入高速旋转的螺旋,在离心力的作用下,密度大的固相焦油渣沉降到转筒壁上,由螺旋输送器输送到转筒的锥体端,从排料口排入焦油渣槽。焦油和氨水形成同心圆环,轻相液体(氨水)在转筒的内层,通过轻相液体排放口排出,重相液体(焦油)在转筒外层,通过重相液体排放口排出。不同液体环的厚度通过可变叶轮来调节。要使离心机生产达标,必须调好焦油的温度、流量、转筒转速、扭矩、堰高几大因素。
2.2 离心机的调试
因为该厂只用1台卧螺离心机,而该厂的焦油产量约为160t/d,从机械化氨水澄清槽出来的焦油含油6%~10%的水和大量焦油渣,调试方案如下:
(1)控制进料量为8~12m³/h,使离心机稳定运行,进料量少则无法满足生产需要,进料量过大则会出现断料现象,离心机生产就会出现波动,相关参数就需要重新设定调试。
(2)在确定进料量后,逐步调试焦油的温度、离心机的转速、扭矩和堰高。经过近2个月的生产调试,找到了较合理的参数和相应规律。
(3)焦油温度必须达到80℃以上,但又不能超过95℃,因为油温越低,焦油黏度越大,对焦油的水渣分离不利;油温越高,对离心机本身损害越大,设备本身不允许。
(4)离心机转速越快,脱水分离效果越好,但轴承温度也越高,在高温天气运行时,容易造成轴承高温报警。
(5)焦油质量的稳定性。从生产数据来看,焦油含水在不大于6.5%的情况下,脱水后能达到含水2%左右。但焦油的含渣量会对离心机的稳定生产造成较大影响。焦油含渣越多,进料管道和进料泵易堵塞,对进料泵的磨损也越大,同时也会使离心机扭矩增大,造成报警停机。目前离心机的出渣量在1t/d左右,但由于焦油含渣和水给生产带来的问题已由7次/月降到2次/月,效果还是理想的。
通过比较和分析,总结出理想的操作参数如下:
转速:3500~3650r/min。
扭矩:19%。
堰高:275~280mm。
处理量:8~12m³/h。
焦油温度:80~90℃。
三、实施效果
(1)焦油贮槽的含渣量明显减少。以前需1年清渣1次,现在为5年1次。
(2)焦油含水明显减少。原来静置脱水后的焦油含水量在4%~6%,现在基本小于2%,使焦油蒸馏系统生产正常。
(3)操作工的劳动强度大大减小,节约了大量蒸汽、检修成本和二次脱水成本,每年还可节约清渣费用4万元左右。
四、结论
从总体情况看,该厂焦油质量有很大的改善,含水率基本保持在2%以下,但还有较大的提升空间。通过加强对机械氨水澄清槽的压油操作,可以将离心机处理后的焦油含水降到1.5%以下,这样就可以减少甚至不需要焦油再次澄清时间,节约焦油贮槽空间。