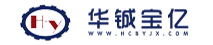
己内酰胺主要是合成聚酰胺6纤维和工程塑料的单体,也用于生产L-赖氨酸,是一种重要的石油化工产品。己内酰胺生产的工艺路线长、流程复杂,目前世界各国对己内酰胺生产工艺的研究都把精力放在缩短工艺路线、改造和优化反应器和分离设备、简化流程、减少副产物硫酸铵产量、减少环境污染上,实现节能降耗和减排。
酰胺化液是甲苯法产己内酰胺工艺中酰胺化反应后的反应液,为轻-重两相混合液,酰胺化反应后下一步是酰胺化液中的重相和环己酮肟溶液进行重排反应。由于酰胺化液含有轻相分,并且轻相分含量随机波动,使得进入重拍反应器的重组分流量不断变化,为了控制重排反应的质量和反应平稳,提高重排反应的选择性和收率,酰胺化液轻-重相必须分离,使其重相参与重排反应。
酰胺化液采用传统的静置分离方法,分离时间长,需30min左右,在70℃左右的高温容易发生环己烷羧酸和硫酸、三氧化硫的磺化副反应,产生磺化副产物,增加了环己烷羧酸的损失,停留时间长会产生更多的磺化副产物,同时静置分离流程厂、设备多、投资大且分离效果不好。酰胺化液的轻-重相两相分离是甲苯法产己内酰胺工艺的技术关键和难题。
离心萃取分离是借助离心力场实现液-液两相的接触传质和相分离,具有结构紧凑、处理能力大、运转平稳、功耗低、清洗维护方便等特点。由于离心力通常可达重力的几百倍,所以特别适合处理两相密度差小、黏度大和易乳化的体系,如在重力分相的分离中要求两相密度差大于0.1g/cm³,而在离心萃取分离机中,两相密度差可以小至0.01g/cm³。自离心萃取分离机问世以来,发展迅速,许多国家已经广泛应用于制药、冶金、废水处理、石油化工和核燃料后处理等领域。我国从1963年开始环隙式离心萃取机的研究,到20世纪80年代,试制了小型单级的环隙式离心萃取机。清华大学、合肥通用机械研究所等单位在原子能、废水处理和湿法冶金等领域开展了环隙式离心萃取的工业应用研究,并在有色冶金中得到成功应用。但近几年,我国离心萃取技术的研究一直未有大的进展,与国外的差距逐渐拉大,如国内在离心萃取技术的工业应用研究方面尚不充分和系统,应用领域有限,远不能满足社会和工业发展的需求。
本文采用离心萃取分离技术对酰胺化液轻-重相进行分离,解决现有技术存在的难题,可大大缩短酰胺化液的分离时间,减少磺化副产物的产生,提高装置的收率。
一、离心萃取分离原理
离心萃取分离机集混合与分离于一体,结构紧凑。当密度不同、互不相溶的两相液体分别从两个进料口进入环隙后,依靠高速旋转转筒的带动以及液层间的摩擦,在环隙内实现剧烈而均匀的混合,萃取传质过程因此加快。当高速旋转的混合液向下流动碰到固定叶片后,从转筒底部的混合相口进入转筒。混合液在离心力作用下分相,重相被甩到转筒外缘聚集到转筒壁外,通过靠近转筒壁的垂直孔道经重相堰流入重相收集室,从重相出口流出。轻相被挤向转筒内侧,经轻相堰和水平通道流入轻相收集室,从轻相出口流出。
二、实验部分
2.1 物料性质
酰胺化液由环己酮肟、环己烷羧酸、苯甲酸、SO3、H2SO4、亚硝基硫酸、正己烷、己内酰胺、副产物和六氢苯甲酰胺等组成,流量为20m³/h,在重力静止沉降条件下,可分成存在轻-重界面的不相溶两部分。酰胺化液中轻相主要为环己烷羧酸、正己烷,体积含量占酰胺化液总流量的15%~25%,在上述范围内是随机波动的。
2.2 离心萃取分离机
萃取离心分离机在本工业应用中只起到分离作用,因此,设置一个进口和两个出口。离心萃取分离机混合区出来的混合液进入澄清区中进行分离,澄清区为高速旋转的圆筒。为了能带动混合液与澄清区同步旋转,防止混合液在圆筒内打滑,圆筒内设置了4块径向叶片。
2.3 工艺流程
装置包括酰胺化反应器、重排反应器、离心萃取分离器、水解反应器等。由酰胺化反应器出口来的酰胺化液经离心萃取分离器入口进入离心萃取分离器。液体进入离心萃取分离器后在高速旋转的内筒作用下分成重相和轻相,重相从离心萃取分离器重相出口出去,通过重排反应器入口的混合器与胺肟化反应器出来的环己酮肟混合后进入重排反应器进行重排反应器。轻相从离心萃取分离器轻相出口出去到水解反应器回收溶剂。
2.4 分析方法
酰胺化液中轻相含量采用在量筒中密闭静止40min,读取分层后轻-重相体积的方法确定。
三、结果与讨论
3.1 转速对相同夹带的影响
按照正常酰胺化液流量20m³/h,改变转鼓转速,进行连续24h试验,考察转速对分离性能的影响。可以看出,随着转速的提高,相间夹带越来越少;当转速为900r/min时,分离效果好,此时,分离后重相中轻相的体积分数只有0.2%,分离后轻相中重相的体积分数只有0.26%;随着转速的再增加,分离性能恶化。这是因为:转速较低时,离心力小,所以分离效果差;随着转速的加大,离心力增大,分离效果较好;但转速增大到一定程度后,再增大转速,会造成轻、重相之间的乳化加剧,给分离造成困难,分离性能反而恶化。
3.2 进口流量对相间夹带的影响
转速为900r/min,改变离心萃取分离机的酰胺化液流量,进行连续24h实验。可以看出,随着酰胺化液流量的提高,分离性能变差,酰胺化液流量超过20m³/h后,分离性能急剧恶化。这是因为,在低流量下,流体在设备内的停留时间长,重相向壁面、轻相向中心的迁移时间长,因此分离效果好;随着流量的增大,流体在设备内的停留时间变短,流体来不及分离就流出了设备,造成分离性能恶化。酰胺化液流量在20m³/h以下,分离后重相中轻相的体积分数小于0.2%,具有较高的分离性能。
3.3 转速对处理能力的影响
研究设备转速对处理能力的影响,有助于了解离心萃取分离机的水力学性能,找到提高处理能力的途径。将不同转速的处理能力作为纵坐标,转速作为横坐标,可作出两者的关系曲线。可以看出,转速和处理能力基本成线性关系,即转速越高,处理能力越大。所以,提高转速可提高设备分离两相混合液的能力,从而使设备的处理能力提高。
3.4 进口流量对设备能耗的影响
能耗是评定设备性能的一个重要指标,因此,有必要对离心萃取分离机的能量损耗规律进行研究,得到降低其能量耗损的理论依据,以便对其进行结构改造、升级,从而可以提高其能源利用率。转速为900r/min,改变离心萃取分离机的酰胺化液流量,进行连续24h实验。可以看出,随着酰胺化液流量的提高,设备的能耗增加,能耗和流量基本呈正比关系。这是因为,离心萃取分离机是借助外加能力进行萃取传质操作的,处理量增大就要求输入大的能量,否则,会造成分离效果差而影响操作。
3.5 分离效果对比
离心萃取分离机从2009年10月份开始运行,运行比较平稳,震动值为1.3mm/s,噪声小。轻、重相互相夹带小,都小于0.3%,达到了预期效果。离心萃取分离机应用于酰胺化液分离是可行的,并且分离时间短,可有效减少环己烷羧酸和硫酸、三氧化硫发生磺化副反应的机会,降低了磺化副产物的生成。
四、结语
(1)离心萃取分离是一种新型的液-液分离技术,具有结构紧凑、处理能力大等特点,具有广泛的工业应用前景。
(2)实验表明,相同转速下,随着流量的提高,分离性能变差,设备的能耗增加;转速和处理能力基本呈线性关系。
(3)工业运行表明,离心萃取分离机应用于酰胺化液分离是可行的,对于减少副产物生成和提高装置收率具有重要意义。