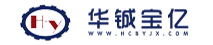
三元复合驱油技术可大幅提高原油采收率,已成为大庆油田稳产的重大技术措施之一。但由于三元复合驱注入液中含有聚丙烯酰胺、碱、表面活性剂,其采出水性质较水驱、聚驱发生很大变化,主要表现在如下方面:污水粘度升高,油珠上浮速度变慢、油珠之间难以聚并;悬浮固体粒径变小,难以上浮或下沉,在水中呈悬浮状态;固液界面存在较高的电动电位,颗粒间相互排斥,胶体分散系非常稳定。以上因素使油水更难分离,悬浮物去除难度加大。目前大庆油田已建的三元复合驱采出水处理站,采用高效污水分离装置或横向流聚结/气浮组合分离装置等,都必须辅助化学药剂来实现油、泥、水的有效分离,但药剂处理成本高,加药后产生泥渣量大,给生产及管理造成沉重负担。
目前,碟片离心机在市场份额占有率较高的有Alfa Laval公司(瑞典)和Westfalia公司(德国),但是价格是国产碟片离心机的数倍。笔者在大庆油田采油六厂某强碱三元污水处理站采用国产碟片离心机进行现场中试,旨在优化国产碟片离心机的技术参数,同时考察其处理三元采出水的稳定性。
一、试验材料及方法
1.1 离心机结构及参数
所用国产碟片离心机(AF-KYD304SD-23)主要用于液(水)-液(油)-固(悬浮固体)分离。转鼓装在立轴上端,通过传动装置由电动机驱动而高速旋转。转鼓内有一组互相套叠在一起的碟形零件即碟片,碟片相互之间留有很小的间隙。待分离物料由位于转鼓中心的进料管加入转鼓后,在高速旋转的转鼓内,在离心力场下,比液体重的固相物沉积在转鼓壁而形成沉渣并经排渣口排出,轻液相沿锥形碟片外(上)锥面向轴心流动至上部轻液相出口排出,重液相则沿碟片内(下)锥面向上流向转鼓壁由重液相出口排出。由于转鼓高速旋转产生的离心力远远大于重力,因此离心分离只需较短时间即能获得重力沉降效果。
试验离心机的技术参数:过水通量为3m³/h、转鼓转速为8280r/min、分离因数为10800、转鼓直径为304mm、进口压力≤0.05MPa、出口压力≥0.2MPa、电机功率为4.0kW。
1.2 原水水质
试验期间原水水质如下:温度为37℃、聚合物含量为780~910mg/L、表面活性剂含量为34.2~42.4mg/L、总碱度为8490~8870mg/L、粘度为7.50~10.7mPa·s、总矿化度为10800mg/L、pH值为10.9。
1.3 分析项目及方法
含油量:分光光度法,悬浮固体含量:重量法,均执行《碎屑岩油藏注水水质推荐指标及分析方法》(SY/T 5329-2012);油(泥)中含水率:蒸馏法,执行《原油水含量的测定(蒸馏法)》(GB/T 8929-2006);粘度:流变仪AR1500ex,执行《旋转粘度计测试方法》(GB 10247-1988);聚合物含量:分光光度法,表面活性剂含量及总碱度:滴定法,均执行大庆油田企业内部标准。
二、结果与讨论
2.1 比重环的筛选优化
现场实验所选比重环分别为φ62、φ65、φ70、φ73、φ75mm,处理量为0.5m³/h,排渣周期为1h。试验分别对不同比重环的水相出口含油量、悬浮固体含量,油相出口排油含水率以及油相出口排量占总处理量的比例(轻相百分比)等指标进行了检测与分析。
结果表明,随着比重环内径的变大,出水水质逐渐变差;以出水含油量及悬浮固体为考核指标,比重环由好到差依次为φ62mm>φ65mm>φ70mm>φ73mm>φ75mm。出水含油量从33mg/L升高到102mg/L,去除率从98.6%降低到94.3%。出水悬浮固体含量从54mg/L升高到78mg/L,去除率从58.8%降低到42.9%。
随着比重环内径的增大,油相出口排油含水率及轻相百分比均逐渐降低;以排油含水率及轻相百分比为考核指标,比重环由好到差排序为φ75mm>φ73mm>φ70mm>φ65mm>φ62mm。排油含水率从0.27%升高到92.9%,轻相百分比从0.20%升高到62.5%。
综上可知,不同比重环水相出口含油量及对悬浮固体的去除率相差不大,但油相出口排油含水率及轻相百分比相差较多。Φ62mm和φ65mm两种比重环虽然水相出水水质要好于其他比重环,但油相出口排油含水率及轻相百分比过高,将来实际生产站很难保障系统平稳运行,因此这两种比重环难以应用。另外三种比重环中φ70mm比重环水相出水水质好,且油相出口排油含水率及轻相百分比都很低,因此综合考虑各种因素后,选择比重环为φ70mm。
2.2 处理量的筛选优化
采用φ70mm比重环、排渣周期为1h,考察不同处理量下水相出口含油量、悬浮固体含量以及油相出口排油含水率、轻相百分比等指标。随着处理量的加大,对油及悬浮固体的去除率呈降低趋势,其中除油率由95.5%降到86.1%,对SS的去除率由50.3%降到22.1%;油相出口排油含水率及轻相百分比则呈上升趋势,其中排油含水率由4.5%升到77.5%,轻相百分比由0.60%升到25.0%。以三元复驱采出水的滤前水含油量≤100mg/L来评价碟片离心机的去除效果,可以看出只有处理量在0.5m³/h左右的情况下,出水含油量达到了要求。
2.3 排渣周期的确定
采用φ70mm比重环、处理量为0.5m³/h且24h不排渣,对碟片离心机进出水含油量、SS含量进行了检测。
24h不排渣试验主要为了确定碟片离心机在该种水质条件下的排渣周期。当运行到12h后,出水含油量、SS含量有一个明显的升高趋势。在0~12h,水相出水平均含油量为62.3mg/L,平均去除率为98.8%;12~24h之间,水相出水平均含油量为172mg/L,平均去除率为95.5%。
在0~12h之间,水相出水SS平均含量为161mg/L,平均去除率为54.6%;12~24h之间,水相出水SS平均含量为306mg/L,平均去除率为27.4%。
12h以后出水水质变差的原因:碟片离心机的渣腔容积为定值,当离心分离出的悬浮固体已经积满渣腔后,再分离出来的悬浮固体会堆积在碟片束之间,甚至会堵塞碟片间隙进行影响分离效果,因此排渣周期应小于12h。为了保证碟片离心机出水水质稳定,该中试设定排渣周期为8h,排渣周期主要和碟片离心机的渣腔容积、物料的处理量及其含固量有关。
2.4 稳定运行试验
采用φ70mm比重环、处理量为0.5m³/h、排渣周期为8h、运行时间为144h,对碟片离心机进出水含油量、SS含量以及排除泥渣的含水率、含油率等进行检测,考察碟片离心机运行稳定性。检测结果显示,稳定运行累计144h(6d),来水含油量在2840~9150mg/L之间,出水含油量都在100mg/L以下,平均为59.4mg/L,平均除油率为98.9%。来水SS含量在170~510mg/L之间,出水SS含量大多在100~200mg/L之间,平均为138mg/L,对SS的平均去除率为54.3%。
同时对于碟片离心机排出的泥渣进行了分析,其密度为1.07g/mL、含水率为32.8%、含油率为2.2%、含固率为65%。排出的泥渣含水率较低,无需后续离心或压滤处理就可以装车拉运;排出的泥渣含油率接近于《油田含油污泥综合利用污染控制标准》(DB 23/T 1413-2010)中用于铺设油田井场、通井路2%的要求,与普通污泥掺混后可达到要求。
碟片离心机分离效果是各种参数相互制约的结果,不仅受到离心机自身结构的影响,同时还受到进液物料的理化特性、现场使用工况及其工艺运行参数的影响。对于不同的物料,只有选择合适的工况及运行参数才能达到较佳的分离效果。现场试验表明,碟片离心机处理三元采出水具有良好的适应性及稳定性,特别是对于乳化严重的污油具有较高的去除效率。
三、结论
针对大庆油田三元采出水乳化程度高、处理难度大的问题,在大庆油田采油六厂某强碱三元污水处理站开展国产碟片离心机现场中试研究。结果表明,碟片离心机在进液温度为37℃、不加药剂、采用φ70mm比重环、额定处理量为0.5m³/h、排渣周期为8h的条件下运行稳定,除油率达到了98%以上,对SS的去除率则达到了50%以上,去除效率较传统自然沉降罐平均提高了30%以上。现场中试结果为今后三元采出水的处理提供了一种新的方法。