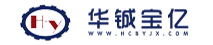
随着经济的发展,能源在人类生活中所占的比重越来越大。近年来,海洋石油资源的开采力度也在不断加大,但因前期保护措施的不充分,造成石油泄漏事件时有发生。海洋油污染绝大部分来自人类活动,其中主要为船舶运输、海上油气开采及沿岸工业排污等。由于石油产地与消费地的分布不均,世界年产石油的半数以上将通过油轮运输到各消费地。这就给占地球表面71%的海洋带来了油污染的威胁。特别是油轮相撞、海洋油田泄漏等一系列突发性事件,更是给人类社会造成了难以估量的损失。近年来,仅仅在我国境内发生的重大石油泄漏事故就高达多起,因其造成的经济损失与海洋环境污染更是触目惊心。
每年海上溢油量约占世界总产量的0.5%,因航运产生的石油污染物更是高达200万吨,其中约1/3为海上油轮失事造成。我国每年海上溢油事故均超过500起,沿海地区海水含油量达标准水质6倍以上,海洋油污治理迫在眉睫。
传统的油水分离技术主要有重力沉降法、液-液旋流法、气浮法、吸附法、聚结法等。
传统油水分离技术较注重浮油的清理,对环境造成的二次污染尚有欠缺。面对漏油造成的环境污染,必然会越来越受关注,发展新的漏油回收技术有望成为一个新的发展方向。近年来,随着高分子薄膜、脂肪晶体、多孔疏水/亲油材料(PHOMs)等新型高效的介质运用于油水分离,这类新型分离材料在外接泵的情况下,利用材料自身的疏水亲油性能实现连续的油水分离,在修复溢油的同时,还能进行回收。传统的做法是利用吸附材料吸附水面的油层,因此,吸附量受限于吸附材料自身的体积。新型分离材料可以很大程度上节约成本,油水分离效率更高,且不会造成二次污染。
1 传统油水分离技术
油水分离过程大致可分为两个步骤:
(1)从油水混合液中提取原油的原油除水过程。
(2)从含油污水中去除油和其他杂质的含油污水(含油率<1%)处理过程。传统分离技术利用油的密度比水小(油浮于水的上方),先通过重力沉降、离心旋转或气浮法实现初步分离,再结合波纹板或活性炭进行二次分离。但仪器造价高、能源消耗量大且工作效率低,不适合大规模处理。
1.1 重力沉降法
重力沉降式油水分离法是利用油水密度差及不相溶性,在静止或平衡流动状态下油滴会以Stokes进行上浮。油滴上浮速度与油水两相密度差和油滴粒径平方成正比,所以传统重力式分离器常通过结合波纹板对油滴的聚结作用增大油滴粒径和在水中添加NaCl提高水相密度,增大油水两相密度差,来提高油滴的上浮速度,从而提高分离效率。Pintor等通过测量植物炼油厂废水分离过程中24h油脂和化学需氧量(COD)的浓度变化曲线,发现刚开始沉降时油脂和COD浓度下降非常快,在4h左右达到平衡,能够去除废水中58%~90%的油脂,COD可降低90%以上。但重力式分离设备体型庞大且造价昂贵,分离效率相对较低,一般不作为单独的油水分离手段。
1.2 液-液旋流法
液-液旋流油水分离法也是借助油水两相的密度差,在油水混合液以一定压力进入旋流器后,油水两相由于受到不同程度的力,借助离心沉降作用达到分离目的。油滴粒径与油水两相密度差越大,越容易被分离。Xu等研究脱气水力旋流器中气泡聚结和破裂对分离效率的影响,当气泡直径从30μm变到100μm时,分离效率从29.67%增加到99.53%。液-液旋流法经过国内外专家多年的研究,取得了重大进展,正趋于成熟化规范化,在未来研究发展趋势中,不仅要进一步的改进它的特性,如设备特性、介质特性及操作特性,也要提高分离系统的工作效率。
1.3 气浮法
气浮油水分离法是向水中通入微气泡(有时还需要加入浮选剂或混凝剂),微气泡进入水相后,使粒径为0.25~25μm的油滴附着在气泡上形成气泡—油滴聚合体,这些聚合体在浮力作用下上升到液面,通过刮去表层泡沫实现油水分离。根据微气泡产生的方式,气浮法可细分为电解法、分散空气法和加压溶气气浮法。Al-Sabagh等采用溶气气浮法配合自制的乙氧基化破乳剂,研究pH、破乳剂浓度、进给速度和饱和压力等因素对从天然气中提取凝析油的影响,得出在pH值=2、150mg/L的破乳剂浓度、0.1L/min的进给速度和10psi的饱和压力下,除油率高达99.9%。气浮法的分离效率取决于气泡与浮油的碰撞几率,为了在较短的停留时间内能与浮油充分接触,须增大气泡的比表面积。因此,怎样实现微气泡粒径的减小将成为研究方向之一。
1.4 聚结法
聚结油水分离法可分为三个处理阶段:
(1)悬浮油滴接近已附着于聚结器之上的油滴。
(2)悬浮油滴与聚结器之上的油滴相黏附。
(3)油滴体积增大到一定程度,从聚结器表面脱落。
波纹板提供了油水两相来回流动的曲折通道,使分散液滴产生聚结。油水混合物在板内流动时,其中的小油滴在运动时聚结变大,通过润湿、吸附、聚结在波纹板的下表面形成油膜,沿表面脱落。Hou等对进液分布器的形式和倾角进行了研究。其试验结果表明,在各种角度中,45°倾角安装时液流较为平稳,而且此情况下液流宽度与容器宽度相当,较好地利用了封头处容器的空间,提高了容器的有效利用率和油水分离效率。在聚结过滤装置的设计改造方面仍要加强,对影响设备流动特性和分离特性的内部结构仍要不断创新,例如在入口、布液和集液等构件上要减小液体的流动阻力。
1.5 吸附法
吸附油水分离法是将表面具有活性的亲油粉末投入油水乳液中破坏乳液稳定,将浮油吸入其中后实现油水分离。活性炭内部含有大量孔隙结构,其比表面积高达2000㎡/g,粉体活性炭是分离效果较好的吸附剂,在4、6、8m/h三种滤速下,吸附柱内粒状活性炭对机油的吸附量为其吸附饱和量的20%~30%,在投加量达到12mg/L时,水中除油率可达90%以上。马伟等采用聚乙烯醇与甲醛反应,结合发泡致孔法制备出三维网络状活性炭/有机复合材料。在工艺条件下吸附量达到活性炭的1.5倍左右,相对于粉末活性炭和块体活性炭,所制柔性复合材料密度小(0.1977g/cm³),使用过程中可以完全漂浮在水面上,有利于吸附漂浮的油膜,方便回收再利用。传统吸附法大多使用粉体活性炭,其分离效率固然较高,但从中回收漏油困难。因此,利用高分子泡沫基体承载粉体活性炭的复合技术,将成为制备新型分离材料的一种途径。
2 新型油水分离技术
现基于高分子薄膜、脂肪晶体、多孔疏水/亲油材料(PHOMs)的新型油水分离技术,可直接达到二次分离的效果,且基体材料体积小、成本低、效率高。其中基于PHOMs和外部泵的原位抽取分离技术,可实现连续从水表面采集原位油。这种自我控制的集油系统不仅大量节省技术成本、制备工艺简单、反应条件温和,同时具有优良的两相分离和石油收集能力,易于工业化生产。
2.1 膜分离法
膜油水分离技术是借助半透膜的选择渗透作用,依据油水混合物中油滴分子的粒径大小,在外加压力或化学位差的推动作用下对混合物中油相或水相进行分离。按油滴在水中的粒径大小划分,可将其分为浮油(粒径150μm),分散油(粒径20-150μm),乳化油(粒径<20μm),溶解油(粒径<10μm)。
20世纪50年代以来,膜分离技术进入工业应用,在含油污水处理中,微滤膜(MF)(≥0.1mm)、超滤膜(UF)(10~100nm)、纳滤膜(NF)(1~10nm)和反渗透膜(RO)(≤1nm)技术的应用越来越受到重视。常见的油水分离膜有超滤膜和微滤膜,均能截留乳化油及溶解油。Ullah等采用宽4μm、长400μm的镍膜去除水中原油,镍膜在不同频率的振动下,其表面的剪切强度可变。测量结果表明,液滴运动程度与剪切强度成线性比例,分离效率高达92%。膜分离技术除以上两种,还有一种复合膜,其将有机聚合材料与膜制造技术相结合。随着科技的进步,膜分离技术在实际应用中不断增加。其特点主要体现在精度高,易自动化,局限在于膜本身,膜在压力下不可避免地会被栓塞、污染、断丝,必须定期清洁舒塞,后期运营成本很高,且易二次污染。
2.2 冷冻/解冻法
冷冻/解冻油水分离法是利用水相中油相内含有脂肪晶体,该脂肪晶体具有深入水相刺破水液滴界面膜的特性,使得液体易于聚结,再借助油的冰点低于水的特点,在温度为-20~-10℃时实现油水分离。其要求混合液稳定性高、连续相黏度大,并且工艺较繁琐,因此其不适用于工业油水分离,而适用于食品工程中的油水乳状物的破乳。
在北方地区,由于冬季低温,生化处理的能耗非常高,且废水中的有毒物质会对微生物的处理效果产生不利影响。作为一种废水处理方法,冷冻法已有多名学者对其进行研究和探索。试验中发现冷冻法对废水的COD和色度有良好的去除效果。Mao等采用多级冷冻法处理含油废水。在初始废水中CODCr和p(NH3-N)分别为36400mg/L和73mg/L的条件下,经过8级冷冻处理,CODCr和p(NH3-N)分别降至430mg/L和2mg/L,去除率分别可达98.82%和97.72%;在相同COD的条件下,p(NH3-N)较高时,COD去除率较高。由此可知,无机盐离子(如NH4+)的存在有利于有机物的去除。相对于其他水处理方法,冷冻法在环境影响、能耗、可靠性等方面均有优势。冷冻/解冻法的局限在于周期长,运用液氮速冻技术又对破乳不利,只有乳珠生长到足够大尺寸时,才会在冷冻/解冻后彻底破乳、分相,达到理想分离效果。
2.3 原位抽取法
原位抽取法是在多孔疏水/亲油材料(PHOMs)中插入一根导管结合外部泵抽取实现油水分离,这就要求材料具备一定的力学强度。其中PHOMs充当了过滤器的作用,富集水中的油相,并通过导管收集油相。聚氨酯(PU)海绵开孔率高且具有优异的机械强度和独特的耐水、耐油、抗溶剂的特性,常规PU海绵内部网络孔洞约为1.2~1.5mm,其表面粗糙,可通过化学喷涂、原位聚合等方法构筑疏水表面制备出一种微型油水过滤器。Ge等将海绵浸泡于纳米SiO2粒子改性的聚二甲基硅氧烷(PDMS)中一定时间后取出,在室温静置固化后,得到一种多孔疏水/亲油功能海绵。通过纳米SiO2-PDMS将亲水性内表面修饰为憎水性,再结合外部泵的抽取能够实现的连续油水两相分离。Ge等将0.02g疏水性纳米二氧化硅与0.02g聚氟蜡(PFW)超声分散在20mL乙醇中,立即将聚氨酯海绵放入上述溶液。5min后,取出海绵,在130℃下干燥0.5h,就得到一种亲油疏水的功能海绵(对水的接触角为142°、对油的接触角为0°)。该功能海绵在吸收黏度不同的油相时具有较高的选择性,并且在持续400个周期的压缩试验后仍不失其优良的疏水性能,具有耐久性、坚固性和高弹性。王倡春通过石蜡微球改性硅橡胶,运用原位聚合法将其修饰于PU海绵内表面,形成三维互穿网络型疏水/亲油材料。利用该材料结合外部泵抽取,可实现从水表面连续收集浮油,突破了传统油水分离材料吸附的局限,漏油收集效率得到较大提高。在油水两相分离同时,还能修复溢油对环境与生态的伤害。材料自身价格便宜、制作成本低廉,可大规模生产,且无二次污染,实际应用价值高。
三种油水分离技术比较如下:
油水分离技术 | 特点 | 适用性 | 使用成本 |
膜分离法 | 精度高、易自动化 | 工业污水处理 | 成本较高 |
冷冻/解冻法 | 精度高、工艺耗时 | 食品工程破乳 | 成本较低 |
原位抽取法 | 效率高、易自动化 | 海洋漏油回收 | 成本较低 |
油水分离过程:在PHOMs中间开一小孔,用导管将其与外部泵相连,将PHOMs置于油水混合物中,启动自吸泵即可不断地向外抽取油相。
3 研究发展趋势与展望
油水分离技术是处理海洋石油泄漏的关键技术之一,传统分离技术不能一次达到规定含油废水的允许排放浓度(10mg/L),需将两种及以上的技术相结合,如:波纹板聚结器(重力沉降法+聚结法)、浮升聚结器(气浮法+聚结法)。膜分离、冷冻/解冻分离或原位抽取分离等新型油水分离技术可直接达到处理要求,其中基于PHOMs与外部泵的原位抽取分离技术,可持续地从水表面快速消除油膜(特别是薄的低黏度油),在处理海洋溢油以及工业油水分离领域展现了巨大的潜在应用前景。利用疏水物质进一步改性PHOMs的基体材料,增强材料对油类物质的选择性,可进一步地改善原位抽取分离技术的分离效果。因此,制备出成本低廉、无二次污染的超疏水/超亲油PHOMs将是油水分离领域的研究热点之一。