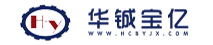
1 引言
含油污泥是指石油开采,存储及生产过程中产生的大量的废弃油泥,油泥是指含石油烃、水、无机物固体等的混合物,是一种高危污染物,我国已经将油泥列入《国家危险废物目录》,含油污泥常伴有恶臭气体产生,含油重金属,及苯系类等有害物质,若不及时处理,对环境有污染隐患。
目前,国内外对含油污泥的处理方法主要有焚烧法、热解析法、生物处理法、热化学洗涤法、溶剂萃取法、固化处理法等,其中热解与溶剂萃取法技术虽然回收率较高,但工艺复杂,技术不成熟,设备投资费用高。其中热化学洗涤法污泥产量大,回收率较低。固化处理法是应用较为普遍的技术,但存在以下缺点:固化剂加量大,固化时间长,存在环境风险。同时,固化剂的稳定性也有时效性。生物处理法周期长,占地面积大,易受气候影响限制,对高含油污泥及含油生物毒性成分的污泥不适用。
本研究是针对浮渣油泥与氟化钙油泥的混合泥作为研究对象,根据混合油泥特性,通过考察油泥混合比例,确定脱水比例。同时,以SXZJ-60型双向自净污泥浆叶干化系统为研究对象,通过对脱水后含油污泥进一步干化,大大降低了危废污泥的产生量,减轻了进一步处置压力。同时对干化过程中存在的问题进行了分析,提出了解决办法。
2 工艺流程
混合油泥经叠螺式脱水机初步脱水后,污泥含水率降至85%左右,然后经带式输送机送至双向自净干化机。污泥干化过程中产生的废气和粉尘被引风机抽出干化主机系统,其中粉尘经过旋风分离器时被收集,尾气依次经过喷淋塔、活性炭吸附罐,处理后达标排放。双向自净干化机出泥含水率≤35%。
3 脱水时浮渣油泥与氟化钙油泥混合比例的确定
3.1 试验
(1)试验样品
试验用的油泥为烷基苯厂浮渣油泥及氟化钙油泥,泥样呈黑色,并伴有气味,油泥的含水率、含油率均较高,难以与水分离。
(2)试验过程及方法
试验过程主要是油泥絮凝,考察合适的絮凝剂,浮渣油泥与氟化钙油泥混合比例。试验步骤:将浮渣油泥、氟化钙油泥分别充分摇匀,取100g。加入絮凝剂,其中加量以试验为准,以120rpm快速搅拌2min,并以30rpm速率慢速搅拌1min,絮凝形成的固液两相1mm×1mm滤网进行过滤,直至没有水的滤出,其中絮凝效果的好坏根据过滤后的絮体大小、滤出液含固率进行综合判断。
3.2 小试试验结果讨论
(1)絮凝剂的筛选
依次选用阳离子PAM,阴离子PAM,非离子PAM三种絮凝剂,分别考察其脱水效果,其中絮凝剂加量为5mg/L,以120rpm快速搅拌2min,并以30rpm速率慢速搅拌1min,试验结果如下:
絮凝剂种类 | 试验现象 |
阳离子絮凝剂 | 絮体大,密度大,沉降速度快 |
阴离子絮凝剂 | 絮体小,沉降速度慢 |
非离子絮凝剂 | 絮体一般,沉降速度快 |
从上表可以看出:向油泥中加入阳离子絮凝剂,都有很好的分离效果,脱出水清澈。加入阴离子絮凝剂,泥水分离困难,水相中会出现细小颗粒,浑浊。非离子絮凝剂絮体大小一般,沉降速度快。
(2)絮凝剂的加量
阳离子絮凝剂投加量分别按2mg/L,5mg/L,8mg/L的不同比例加入到油泥中,考察其对絮凝效果影响以120rpm快速搅拌2min,并以30rpm速率慢速搅拌1min,试验结果如下:
絮凝剂加量 | 试验现象 |
2mg/L | 絮体小,沉降速度慢 |
5mg/L | 絮体大,沉降速度快 |
8mg/L | 絮体大,水粘性大,搅拌后容易松散 |
(3)浮渣油泥与氟化钙油泥混合比例
采用阳离子絮凝剂,投加量按照5mg/L,单独对氟化钙油泥进行絮凝试验,效果差,没有絮凝效果,采用浮渣油泥与氟化钙油泥掺合处理,逐步提高浮渣油泥与氟化钙油泥的混合比例,当达到5:1体积比后,絮凝效果显著,出现大的矾花,满足叠螺脱水要求。通过试验后发现:在阳离子絮凝剂投加量为5mg/L的情况下,浮渣油泥与氟化钙油泥的混合比例为5:1时,污泥絮凝效果良好,具备脱水压滤条件。
4 干化过程中存在问题及对策
4.1 干化后污泥含水率确定
由于双向自净浆叶干化机初次在本装置使用,没有现成的经验可以借鉴。干化前污泥的含水率均在85%左右,污泥干化后含水率控制在什么范围才是较佳状态还是未知数。为了摸索经验,在污泥含水率均在85%的条件下,对干化机运行参数进行调整,具体分析数据和成品如下:
序号 | 变频器转速(Hz) | 进口温度(℃) | 出口温度(℃) | 进口含水率(%) | 出口含水率(%) | 进口含油率(%) | 出口含油率(%) |
1 | 12 | 135 | 98 | 84.2 | 0.7 | 2.16 | 13.62 |
2 | 15 | 135 | 98 | 84.4 | 3.1 | 2.08 | 13.49 |
3 | 15 | 115 | 86 | 84.1 | 7.2 | 2.12 | 13.62 |
4 | 18 | 115 | 82 | 84.4 | 10.2 | 2.21 | 12.67 |
5 | 18 | 105 | 78 | 84.3 | 15.1 | 2.18 | 11.17 |
6 | 21 | 105 | 72 | 84.2 | 2.07 | 2.11 | 9.18 |
由上表可以看出:干化后污泥含水率在5%以下时,污泥成粉末状,现场干化环境粉尘较大,不利于环境保护。污泥含水率在5%~10%之间,污泥成颗粒状,不仅属于较好的理想状态,也有利于进一步处置。污泥含水率超过10%以上,污泥成胶乳状,水分脱除不彻底,增加了运行成本。综上所述,通过控制干化机主机转速和进口温度,将干化后污泥含水率控制在5%~10%之间是比较合理的状态。
4.2 运行过程中的其他问题
由于危废污泥含有大量石油类,含有可燃性有机物。同时,污泥输送口为半封闭,与空气接触,也就是说在污泥输送入口处可能形成爆炸性油气混合物,一旦遇到明火或机器本身机械摩擦产生的火花,极易发生爆炸危险。为了避免事故的发生,可在污泥输送入口处增设氮封,保持入口处处于微正压,阻止空气进入干化机内部,这样就可以有效避免安全事故的发生。
另外,在干化机运行过程中由于污泥含有大量石油类,干化污泥输送皮带极易打滑和跑偏,为了避免皮带打滑和跑偏,在皮带两侧增设纠偏挡板,在皮带上部增设压紧罗盘,有效避免了上述问题。
5 经济效益和社会效益
危废污泥经双向自净浆叶干化机干化后,含水率由干化前的85%降至干化后的10%左右,危废污泥总重量下降80%。按照目前危废处置费4500元/吨计算,装置内共有1000吨危废污泥,全部干化处理后经济效益显著。另外,危废污泥干化处理后,大大降低了危废量,保护了环境,同时避免了运输过程中的抛、洒,社会效益显著。
6 结语
(1)阳离子絮凝剂投加量为5mg/L的情况下,浮渣油泥与氟化钙油泥的混合比例为5:1时,污泥絮凝效果良好,具备脱水压滤条件。
(2)干化后污泥含水率控制5%~10%之间,污泥成颗粒状,不仅属于较好的理想状态,也有利于进一步处置和节约成本。
(3)通过在干化机出口和尾气引风机之间增加一台固定管板式换热器,不仅降低了尾气排放温度,同时尾气的排放量也得到相应减少。通过控制活性炭的更换周期和喷淋塔的溢流,在实现尾气达标排放的基础上,降低了现场异味的产生。
(4)通过在污泥输送入口处增设氮封装置,可以有效避免安全事故的发生。