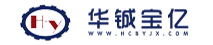
1 引言
对于液相为煤沥青、油浆、矿浆,固相为催化剂颗粒或其它微米级球状颗粒的高粘度物料,固液分离设备的开发是需要解决的问题之一。高粘度物料固液分离设备可用于外甩油浆除催化剂、井下控砂、原油除砂、废高分子材料回炼除砂等领域。随着世界经济的快速增长,炼油技术朝着重油轻质化和清洁汽油燃料生产及多产低碳烯烃的方向发展。催化裂化已成为加工重油(常压渣油、减压渣油、焦化蜡油)的重要手段。为解决催化裂化操作条件恶化,热负荷加大,易生焦,处理能力反而下降的问题,许多炼油厂采用外甩油浆技术。由于外甩油浆中通常含有一定量的固体催化剂粉末,而灰分含量较高,必须采取措施脱除,以满足油浆进一步利用的要求。油井出砂会造成砂子在集输管道及集输设备(沉降罐、分离器、电脱水器和计量装置等)中沉积,这将减小管道的流通面积使井口回压上升,分离器和电脱水器有效容积和工作效率下降,也会增加设备的磨损,使仪表的计量精度降低。
固液分离设备根据物料的分离特征可分为两种类型:一种是分离物料中的液相受到限制,固体颗粒处于运动状态的浮选,重力沉降和离心沉降。另一种是固相受到限制,液相则处于流动状态的滤饼过滤,深层过滤,离心分离和筛滤。前者取决于固体颗粒和液体间的密度差,而后者则以具有过滤介质为前提,深层过滤只适用于固体颗粒相当小的场合,筛滤则是借重力使液体得以分离的设备。对于高粘度液体中的固体的分离,由于常温下物料的粘度很大,过滤分离阻力大,沉降分离效率低,普通的沉降或过滤很难将微颗粒去除,所以通常需要将油浆加热以降低粘度。
2 过滤分离
2.1 高温过滤法
过滤分离法具有操作简单、分离效率稳定,催化裂化装置操作条件或原料性质变化对分离效果影响不大,设备简单,且宜于高温条件下分离等优点。但一般说来,过滤阻力大,特别是油浆中胶状物含量过大时,会加剧过滤阻力,采用高温过滤面临介质难以选择的问题,而普通过滤则很难将微米级的颗粒去除。高温过滤法是将高粘度固液混合物换热至300~350℃,使物料的粘度随温度的升高而降低后,再进入过滤系统进行过滤分离。
2.2 筛滤法
筛滤法主要采用多孔金属筛分反洗系统。多孔金属筛分反洗系统一般由多个体积相当的压力容器组成,每个容器内都装有面积相当的复合不锈钢丝网筛,以圆筒形排布,各个容器之间并排。处理油浆温度可为204℃~371℃,催化剂浓度可达6000×10-6(6000ppm)。
3 静电分离法
静电分离法是近年来发展起来的一种新型液固体系分离技术,适用于固体颗粒直径很小(10-5~10-6m)、颗粒浓度相对较低且液相电阻率又较大的液固体系。静电分离法是当含微颗粒的液流流经电场作用下的填料床层时,微颗粒在高压电场中被极化,并被吸附在填料上(如玻璃球),从而使液流得以净化,当填料床层因吸附微颗粒达饱和后,采用反冲洗液流经床层使填料得以再生,然后再进行下一轮的吸附操作。
4 沉降分离
4.1 重力沉降
重力沉降法包括自然沉降和化学沉降法。
4.1.1 自然沉降法
自然沉降法具有设备简单、运行成本低、操作容易等特点,被很多炼油厂采用,但其净化效率不高,小于20μm的颗粒去除十分困难,不仅分离时间长,而且设备也很庞大。如当温度为250℃时,沉降深度为60cm,催化剂微粒去除率达85%时,所需的沉降时间为20000多小时,显然沉降时间太长,无法工业化。
4.1.2 沉降剂沉降法
在油浆中加入一种添加剂,使催化剂能够快速沉降。国外于20世纪80年代初期完成开发,目前已有50多家炼油厂使用。用化学沉降助剂改善油浆催化剂粉末分离技术的突出优点是工艺和设备简单。
4.2 离心分离
离心沉降法的主要设备是高温试管沉降离心机。离心沉降法的主要设备是GC5高温试管沉降离心机。GC5高温试管沉降离心机是利用油浆在高温时流动性明显增大的粘温特性研制的,该离心机的离心腔周围配置有加热和保温设备,同时为便于操作还配有控温、控时和控制转速的装置。将油浆经换热器换热至30℃~150℃,进入高温离心分离机进行分离,离心时间约2~10min,离心转速为3000~5000r/min,脱固率为92%~98%,得到固含量为0.02%的脱固油。GC5高温试管沉降离心机技术指标为:转速5000r/min,容量60mL,温度达300℃,定时范围0~6min。
4.3 旋流分离技术
4.3.1 旋流分离技术简介
旋流分离技术由旋流分离器、旋流分离流程系统、泵送系统和检测控制系统四大部分组成,其中关键部分是旋流分离器。旋流分离法具有设备结构简单、工艺流程简单和操控容易等优点,因而成为固液分离方法中简单可行的技术路线。
用旋流器作为固液分离设备,具有结构简单、易操作、可靠性高、投资和操作费用低、节能、环保、安全等特点。作为分离设备在炼油和石油化工过程中有很大的应用潜力。对于旋流器在高粘度物料固液分离方面的应用,国内已有了一定的研究成果。
4.3.2 粘度对旋流器分离过程的影响
随着液相粘度增大,旋流器分离效率会降低,主要有以下三个原因:液相粘度大,会减小液相与固相的密度差;颗粒迁移阻力增大;旋流场旋转衰竭加快。
旋流器在高粘度流体中的运用,主要是解决粘度增大导致的分离效率降低的问题,可以从以下三个方面考虑:增大沉降速度;增加停留时间;减小沉降距离。
当物料是处于牛顿流体范畴矿浆粘度与剪切速率无关。粘度同样会影响水力旋流器的水----底流分率R的大小,R中的所有颗粒不管形状和大小如何都进入到底流,旋流器中的液体速度在粘度增大及粘度阻力增加时下降,因此造成R增加。
4.3.3 高粘度物料旋流分离实验研究
对于旋流器在高粘度液体中分离固体方面的应用,国内已有了一定的研究成果。张士瑞等人用模拟实验装置,初步研究了应用微型旋流器脱除催化裂化油浆残留固体的可行性。实验操作条件为常温,以水为液相,固相为催化裂化催化剂粉末。采用的单管旋流器,其公称直径为10mm。进行5个进料速度、4个底流分率、4种进料固体含量的全方位正交实验,共操作试验方案80种,采集并分析样品143个,获取作为分析结果的数据文件295份,经整理计算,获得完整数据68组。实验对于底流分率、进料固体含量、进料速度对分离效率的影响做了详细的研究,并得出结论。在不考虑其他因素的情况下,采用所开发的旋流器脱除催化裂化油浆残留催化剂微粒在技术上是可行的,分离效果能够满足其绝大多数下游利用过程对固体含量的规格要求。
杜海洋等人用实验的方法研究了用高温旋流分离装置分离加氢裂化尾油中甲苯不溶物、胶质、沥青等物质的分离效果。实验对不同温度下的分离效率做了研究,并得出结论,在较低温度下旋液分离器对甲苯不溶物、胶质、沥青等物质的分离效率很低,但随着温度的升高,油浆粘度显著降低,分离效率显著提高。实验还对不同粘度下旋液分离器的进出口尾油密度、物料粘度和样品颗粒进行了测定,同时对进出口尾油密度、粘度和颗粒的比较,来进一步对旋流分离器的分离效果进行说明。
华东理工大学根据多年的研究和工程经验,采用微型旋流器分离工艺对催化裂化外甩油浆进行分离,并设计了公称直径为10mm的专用微型旋流管。该旋流管采用单锥、双入口结构。白志山等人通过试验研究,以催化外甩油浆为对象,在1.8×106t/s重油催化裂化装置上开发了外甩油浆微型旋流净化工业实验装置,考察了微型旋流芯管压力、分离效率和流量的相互关系。结果表明,在合适的操作条件下分离效率可以达到60%以上,分离后油浆中固体含量低,仅为680mg/L。净化油浆催化剂颗粒的平均粒径采用先灼烧后库尔特粒度仪分析,3μm粒径的催化剂颗粒去除率达到75%。
5 结论
当物料粘度大时,采用过滤分离进行固液分离时阻力大,容易堵塞。旋流分离器内无有形介质,不会堵塞,靠无形的超重力场分离。当不能通过升温将粘时,开发用旋流分离是一种选择。
目前国内高粘度物料固液旋流分离设备研究主要处于试验阶段。对比分析上述几种分离方法,在各种高粘度物料分离方法中旋流分离法具有设备低成本、低能耗、结构简单、工艺流程简单和操控容易等优点,因而成为简单可行的技术路线。
选择适当的操作条件,应用固液旋流分离器实现高粘度物料固液分离在技术上有望可行,分离效果可满足绝大多数下游利用过程的要求,实际工业操作对处理能力的要求可通过将多个旋流器并联实现。