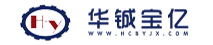
石油工业的气液物理分离过程多是利用气液组分密度的差异进行的,气体与液体的密度不同,相同体积下的液体具有比气体大得多的质量,因而具备较大的惯性。给整个体系提供有效的空间及速度分布,可以实现气液的顺利分离。依托气液分离原理,科学研究及工业实践中进行了多种分离技术的开发及应用,常用的分离技术包括:重力沉降、折流分离、填料分离、离心分离等。
1 重力沉降
重力沉降分离是利用气液两相的密度差异导致单位体积气液两相所受重力不同而实现两相的分离,即液滴所受重力大于其所受气体的浮力时,液滴将从气相中沉降出来,而被分离。应用重力沉降分离技术,关键在于给气液两相提供足够的空间,在突然扩大的压力容器中,流速降低后,在主流体转向的过程中,气相中细微的液滴下沉而与气体分离。常见的重力沉降式气液分离器主要有立式与卧式两种。重力沉降式气液分离器的结构简单,制造方便,而且分离时流体所受的阻力小,操作弹性大,使用范围广,但是由于重力的分离需要较长的停留时间,为了达到一定的分离效率,因此需要的分离器体积较大,投资费用也较高。在对操作空间要求十分苛刻的海洋平台,其适用性及经济性遭到了挑战。
2 折流分离
由于气体与液体的密度不同,液体与气体混合一起流动时,如果遇到折流板阻挡,气体会折流而走,而液体由于惯性,继续有一个向前的速度,向前的液体附着在阻挡壁面上由于重力的作用向下汇集到一起,通过排放管排出。此类分离折流板结构简单、处理量大,分离效率比单纯的重力沉降要高。但也有其缺点,比如气液两相流经折流板时,会对流动造成一定的阻碍,且在气体出口处有较大吸力容易造成液滴二次夹带,气体在折流的同时也推动着已经着壁的液体向着气体流动的方向流动,如果液体流到收集壁的边缘时还没有脱离气体的这种推动力,那么已经着壁的液体将被气体重新带走。液体没有固定的形状,容易碎化,在着壁的同时,会产生更细的液滴重新返回气相中,随着流速的增大,液体收集壁的碰撞力越大,其碎化的倾向越大。现在折流板分离构件的分离理论和数学模型已经基本成熟,对其研究集中在结构的优化及操作参数方面来提高脱液效率。
3 填料分离
填料分离的基本原理同折流分离相同,也是利用液体与气体混合一起流动时遇到阻挡,气体折流而走,而液体由于惯性,继续有一个向前的速度,向前的液体附着在阻挡填料表面上由于重力的作用向下汇集到一起,通过排放管排出。由于填料相对普通折流分离来说具有大得多的阻挡收集壁面积,而且多次反复折流,液体很容易着壁,所以其分离效率比普通的折流分离高,而且结构简单,只需制作一个填料架,体积比普通的折流分离器要小。但是它的分离负荷范围更窄,超过气液混合物规定流速或者液气比后,分离效率会急剧下降。填料分离器的阻力比普通的折流分离器大,而且还具有工作不稳定,容易带液,填料易碎、易堵等缺点。填料的种类较多,经过多年的发展,出现了多种形式的规整填料及不规整填料,其分离性能各不相同,所以对于不同的分离填料的选择很重要。
4 离心分离
离心分离是根据液体和气体的比重差别,利用气流方向和速度改变时的离心力作用,使液体和气体简单的相互分离,过程中不存在化学反应。利用该分离原理,研究了各种结构来促进气液分离。典型的气液分离结构就是旋流器,进料流体中的颗粒随流体从切向进料口进入旋流器后,在一定的向下倾角作用和受器壁的约束而迅速旋转向下变为高速的外螺旋运动。由于往下器壁为圆锥面,比流体密度较大的颗粒借助这一运动产生的惯性离心力向外运动抛向器壁,被迫与器壁碰撞降速而分离,再沿锥面落至底流管排出,同时经分离后的流体变更运动方向,产生向心的径向运动,沿中心线转而由下向上作内螺旋运动,通过上流管流出。通过离心旋转运动,可以在比较小的流速下产生几百倍乃至上千倍于重力的离心力,能够促使气液两相快速分离,因此其结构比较紧凑。离心作用作为一种使气液产生分离的有效手段,在石油、化工以及其他相关行业进行了广泛的应用。但它也具有其自身的缺点,强大的离心力有助于气液完成分离,但过分强大的离心力会造成流场的极度紊乱,会使着壁的液滴产生剪切破碎,重新混入气相中,使分离效率降低。对气液两相旋流场的深刻认识以及其压力匹配关系等方面,是离心分离器研究的重点部分。
5 结论
在石油化工行业中需要进行气液混相流体分离的场合众多,分离技术与形式多样,在应用中应进行能耗与效率的综合考虑,选择合适的气液分离技术与分离结构。