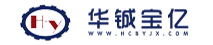
老化油也称为老化污油,主要来源于原油储存、含油油泥和污水处理中产生的含有大量表面活性剂、污水和泥砂的复杂油包水、水包油型乳液。老化油的状态稳定,现有原油处理系统很难或无法处理。老化油的存在不仅占据了大量的储存空间,而且因油水过渡层导电性强,电脱水器易出现跳闸或直接导致电脱水器极板击穿等生产事故;还会腐蚀设备、缩短设备使用寿命;因频繁跳闸还大幅增加了工人劳动强度;老化油回掺则加大了采出液处理难度,导致脱水温度升高和处理剂用量增加,提高了处理成本;老化油含水率在50%以上,密度介于油与污水之间,大量存在于沉降罐油水界面处,造成油水界面模糊,混油层厚度达5m以上,排水、计量困难。老化油脱水净化处理一直是人们急需解决的难题。鉴于上述原因,开展老化油脱水和油品精制的研究是解决困扰企业生产经营问题以及提高效益、降低安全和环保风险的必要措施。
本文介绍了老化油的来源、成分、数量、对生产的危害以及特点和处理难点。总结了老化油现有的处理方法,分析了各种方法的优缺点,对老化油的管理和研究方向提出了建议。
1 概述
1.1 老化油的来源
老化油的来源主要有以下途径:一是含油污泥、污水处理回收的原油,包括污水沉降罐上部的浮油、污水处理站回收水池内的污油、脱水设备内位于油水界面上的中间过渡层;二是在曝氧条件下原油乳状液受空气、温度和阳光等环境因素的作用发生化学反应,以及各种乳化剂、沙尘的混入经过一段时间乳化、聚结在油水界面膜上使原油乳状液的稳定性增强形成的老化油;三是井上实施洗井、酸化、压裂等措施后的残液掺入原油中,使原油品质恶化而成为老化油;四是边缘单井的开发致使原油多次储存、运输、装卸而乳化加重形成的老化油;五是因集输工艺或条件限制,一些高含水或成分复杂的原油无法及时处理而长期储存形成的老化油;以及油田开采进入中后期时,原油重质化及三次采油技术的使用使大部分采出的原油乳化严重并逐渐稳定,形成油水界面聚结的老化油。
1.2 老化油的成分
不同来源的老化油成分是不同的,一般而言老化油的成分包括污油、化学药剂、无机盐、细砂和黏土矿物等。污油组分包含胶质、沥青质、环烷酸皂、微晶石蜡等,老化油存放时间越久,原油轻质组分挥发越多,重质油的比例越大。老化油中的化学药剂主要有修井液、钻井泥浆及采油过程中加入的杀菌剂、阻垢剂和缓蚀剂,采出液分离时加入的破乳剂,污水处理中加入的絮凝剂(如大分子有机絮凝剂),聚合物开采产生的老化油中还含有一定量的聚合物。无机盐主要是无机助凝剂,包括金属硫酸盐类、胶态硫化亚铁粉粒、二氧化硅、铝硅酸盐等,且存放时间越久,无机成分含量越高,胶态硫化亚铁粉粒的大量存在是老化油生成的重要原因。
1.3 老化油的数量
据统计,我国油田与炼油厂每年都产生大量的老化油,仅油田每年就产生不少于800万吨的老化油,数量甚至接近我国第三大油田——新疆油田的原油产量。塔河油田2012年累计产生老化油25万吨,辽河油田每年产生老化油约6万吨,大庆油田2014年产生老化油42万吨,这些老化油处理后的经济效益极为可观。
1.4 老化油对生产的危害
老化油对生产的危害主要有:影响输油品质,占用大量的储罐,严重干扰主工艺流程中电脱水系统的正常运行,大幅增加运行成本,影响准确计量,恶化水质,引起金属表面腐蚀和结垢,产生环境污染和安全生产的事故隐患。
1.5 老化油的特点及处理难点
老化油的特点是污油成分复杂,含水含砂率高,乳化状态稳定,轻质成分含量较少,沥青质、胶质含量高,无机盐含量极高,如铁和硫的含量均达5000mg/kg以上。因此,老化油乳状液性质极为稳定,难以破乳脱水。
2 处理方法
2.1 物理法
2.1.1 回掺处理
回掺处理是将老化油按比例掺入外输净化油中,并控制水、杂质含量符合外输要求。黄家孝等进一步发展了曲径回收方法,将老化油打入计量间干线,再经转油放水站进行水洗和加热炉沉降,脱水并去除一部分杂质。2005年,大庆油田采油一厂采用该方法处理老化油,既保证了外输油含水合格,又使脱水器放电现象明显减少,脱水成本大幅下降。
采用定量控制、合理配比回收老化油是一种非常实用的创效方法,但混入比例不能大于6%,且污水和杂质并未去除。
2.1.2 旋流分离
旋流分离工艺流程为:老化油乳液在压力作用下沿切线进料口进入分离旋流器,在快速旋转产生较强的离心力作用下,使密度相对较大的物质抛向器壁形成外旋流,从底流口排出,密度相对较小的物质留在内圈形成内旋流,并聚结成大的液珠上浮分离,从溢流管排出。王秀莲利用水力旋流分离技术处理含水60%以上的油水混合液时,其分离效率达到40%以上。
利用旋流分离器进行分离的两个必要条件,一是混合物料必须具有压力能,二是混合物料之间必须存在密度差,且密度差越大分离效果越好。旋流分离器作为一种分离设备,尽管结构简单,但影响因素却相当多,装置设计参数非常严密,对现场条件的要求也非常苛刻,在现场试验系统中旋流动力和破乳时间均很难达到要求。因此,应用时,根据实际生产情况确定合理的结构参数和工作参数非常重要。
2.1.3 超声破乳
超声破乳是基于超声波作用于性质不同的流体介质产生的“位移效应”,水粒子不断向波腹或波节运动,聚结并发生碰撞,生成直径较大的水滴;因密度差异,水滴借助重力从油中沉降、分离,从而达到脱盐、脱水的目的。张玉梅针对扬子炼油厂污油优选出超声脱水参数:混响场中声强1.168W/cm³,频率40kHz,作用时间15min,破乳剂用量375mg/L,温度70℃,沉降时间4h;驻波场中声强0.66W/cm³,频率10kHz,作用时间5min,破乳剂用量375mg/L,温度70℃,沉降时间4h。该条件下污油脱水后含水量可达0.2%(φ)以下。
超声破乳一般要与破乳剂联合使用。陈永红等采用破乳剂和超声波联合作用可以进一步提高原油的脱水效率。超声波对化学破乳脱水的促进作用相当明显,同等条件下(如相同的破乳剂量、温度等),污油脱水率可提高2~3倍,和单纯热沉降相比具有显著优势。超声波处理老化油的缺点是声强过大、辐照时间过长均会造成老化油的二次乳化,因此要谨慎使用。
2.1.4 微波辐射
微波辐射是利用微波对物质的内加热特性,以及产生的高频变化的电磁场,在破乳方面显示出独特的优势。微波破乳的机理是:极性分子高速旋转,影响了油水界面膜的Σ电位,Σ电位的降低促进了分散相颗粒的聚集,从而加速分离过程,提高破乳率。
刘文等将从中原油田采油一厂文一联合站提取的老化油,含油率分别为1%、5%和10%,以及含水率为50%的油品进行微波辐射脱水实验。结果表明:在新油中添加不同比例的老化油后,采用微波破乳脱水,其效果与全是新油的差别不大;而微波与水浴加热破乳效果相比,脱水速率提高了175%~450%,脱水率提高了129%~150%。
微波辐射处理的优点是省时、高效、清洁且处理效果好,缺点是低含水量的老化油需要小功率、长时间处理,以防止高温导致水滴微小化,脱水难度加大。
2.1.5 蒸发脱水
蒸发脱水是利用老化油初馏点较高及油水沸点不同的特点,通过加热破坏油水界面的膜结构,使水分子从老化油乳状液中分离。
梁宏宝等研制出一套老化油深度脱水装置——U形管半布管形式的管壳式换热器,建立了老化油蒸馏装置温度精准控制系统的数学模型,有效避免了因过多气泡互相靠近融合产生的暴沸现象,极大提高了脱水效率,处理后老化油含水率可由1.0%降至0.5%,精馏装置可使含水率降至0.05%以下。
老化油蒸发脱水不受油水密度差的影响,无需添加药剂,不易引起二次乳化,具有普适性,脱水处理后的老化油含水量低,是一种适应性强、高效的老化油脱水处理方法。其缺点是成本高,需加入老化油质量1/5~1/3、直径0.5cm的沸石以防止暴沸,且无机杂质未被去除。
2.1.6 其他
其他物理法还有高频高压、变频脉冲、负压脱水等技术,处理后可使原油含水率低于2%,但无机污染物仍存留在原油中,脱水后油的品质较差。
2.2 化学法
2.2.1 热化学脱水
热化学脱水是将老化油加热到一定温度,并加入适量的破乳剂(这种药剂吸附在油水界面膜上,可降低油水界面薄膜的表面张力)破坏乳状液的稳定性,以达到油水分离的目的。应用较为广泛的是热化学沉降法,破乳剂的作用至关重要。热化学脱水的主要影响因素是破乳剂,加入适宜的破乳剂处理后原油含水率均可控制在5%以下,部分甚至可达0.5%以下,符合外输要求。
热化学脱水法的优点是工艺简单、投资少、见效快,缺点:一是乳化剂使用不当会增强乳化,从而形成更多难以处理的老化油;二是单独沉降效果不好,且不易使油相中的杂质脱除,需配合离心机使用;三是破乳剂使用量大,运行费用高。
2.2.2 氧化破乳
氧化破乳是采用氧化剂等对老化油进行处理,将大分子乳化剂降解为短链小分子物质,或将硫化亚铁氧化为三价铁离子和硫酸根离子,降低油水界面膜强度以实现老化油破乳的目的。氧化剂主要有二氧化氯、双氧水、硝酸-硝酸钾氧化体系等,在较佳工艺条件下采用上述氧化剂处理均可使净化油含水率达到出厂要求。
氧化法的优点是见效快,缺点是部分氧化剂(如双氧水)的不稳定性易引发安全事故。
2.3 生物破乳法
生物破乳法是通过加入微生物发酵培养液而使乳化液破乳脱水的方法,其机理是利用微生物细胞本身或其代谢过程、代谢产物来破坏油水界面的乳化膜,降低油水界面的表面张力,破坏乳状液的稳定性,以达到破乳油水分离的目的。在老化油脱硫过程中,通过微生物直接消耗硫化物来降低硫化物含量,从而降低导电性,使老化油易于脱水处理和回收净化。左研采用生化破乳剂处理华北油田赵一联合站内的老化油,处理后硫酸盐还原菌总数由6.0×107个/mL降至22个/mL,硫化物含量由126.0mg/L逐渐降至10.8mg/L,原油的界面张力由加药前的68.20mN/m降至37.16mN/m,击穿电压由9500V增至29000V,为电脱水器形成电场并稳定运行提供了前提,很好地解决了老化油的脱水问题。
与传统物理和化学处理方法相比,生物技术具有处理量效果好、综合成本低、单位能耗小、无二次污染等优势,具有广阔的开发与应用前景。其缺点是处理周期长,需要针对不同的原油优选不同菌种。
2.4 组合工艺
为提高老化油的处理效果,降低运行成本,一般要将不同的工艺联合使用。
2.4.1 热化学联合离心脱水
中国石油采用热化学联合离心脱水工艺处理稠油老化油,处理后净化油含水率平均值为7.62%,油品回收率平均值为83.26%。张洪君采用该工艺处理稠油老化油,处理后净化油含水率平均值为2.92%,油品回收率平均值为95%,达到工业化生产的要求。侯兆凯采用该工艺处理大庆采油十厂朝一联存放1a的高乳化陈旧原油,处理后油中含水率降至0.3%以下。
离心分离技术在老化油处理中效果显著,能充分回收原油,并避免了老化油在生产中的恶性循环和二次加工过程中对装置生产的影响,是老化处理的有效手段。
2.4.2 化学法联合电场法
魏立新等在老化油样品中加入15mg/L破乳剂,混匀后恒温60℃进行脉冲电场脱水,脉冲电场的频率为2kHz,电极板之间的强度为2000V/cm。脱水实验持续90min后,原油含水率低于0.3%,分离后的污水含油量均小于500mg/L,油水界面清晰且整齐。
2.4.3 超声联合化学破乳
李锋等采用超声联合化学破乳工艺处理流花油田胜利号浮式生产储油卸油装置老化油,较佳脱水条件为:处理温度80℃,破乳剂GLT-131加入量400mg/L,有机高分子絮凝剂加入量800mg/L,超声功率400W,声场强度1500W/m³,沉降时间1h,处理后含水率可降至1.3%。
2.4.4 其他
其他工艺还有超声热洗、化学热处理、超重力分离和负压脱水的组合等。
3 结语
老化油的有效处理是保证系统正常运行,减轻污水处理和集输系统压力,增加油品质量和产量的重要措施。加强和改进管理、提高油品质量的措施主要有:一是源头治理,加强管理,减少老化油的产生;二是分类储存,分开处理,不仅老化油要与新鲜原油分离,不同来源的老化油因成分不同、性质各异也要分开;三是加强科研攻关力度,开发先进环保型药剂和处理工艺,实现低成本、高效处理;四是要与污染治理相结合,既实现油品精制回收,也实现污水处理、残渣的无害化处理或资源化利用。