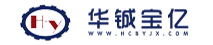
天津某钢业有限公司在金属制品加工过程中产生大量的酸洗废水,废水的主要污染指标是Fe2+、PO43-和H+,废水处理工程设计规模为7000m³/d,其中一期的处理规模约为3000m³/d。酸洗废水经熟石灰调碱后,其中的Fe2+、PO43-与Ca(OH)2生成沉淀,再采用膜过滤技术进行固液分离处理,进而会产生大量的污泥,污泥的主要成分为Fe(OH)3、Ca3(PO4)2和废水中存在的其他悬浮杂质。该工程一期的污泥产量为8m³/d,满负荷运转后污泥产量为18m³/d,污泥含水率在98%左右。由于该工程的产泥量较大,因此采用离心脱水机对污泥进行脱水处理。离心脱水机具有自动化程度较高、操作环境好、不会产生异味、产泥含水率较低、占地面积较小等优点。
1 离心脱水机简介
离心脱水机的工作原理:悬浮液在高速旋转产生的离心力作用下,密度较大的固相颗粒沉积在转鼓内壁上,与转鼓做相对运动的螺旋叶片不断将沉积在转鼓内壁上的固相颗粒刮下并推出排渣口,分离后的清液经液层调节板开口流出转鼓。该工程中采用国产离心脱水系统,主要包括:卧螺离心机1台,处理量为15~20m³/h;絮凝剂投配装置1套,产药量为2m³/h;加药泵1台,Q=0.4~2.0m³/h,H=0.2MPa;污泥泵1台,Q=25m³/h,H=0.2MPa;无轴螺旋输送机1台,长度为5.5m,输送能力为3m³/h。卧螺离心脱水机的参数如下:转鼓内径为430mm,长径比为3.7,转速为3200r/min,分离因数为2466,采用行星齿轮差速器,差转速为2~32r/min无级可调,扭力矩为5000N·m,液层深度为124~136mm,物料密度为1.2g/cm³。
2 离心脱水机的调试
离心脱水机调试工作历时半个月,主要包括絮凝剂的选择、主电机转速范围的确定、扭力矩运行范围的确定、进泥量范围的确定、进泥量与药剂量的合适配比等。
2.1 絮凝剂的选择
污泥脱水采用的絮凝剂主要是聚丙烯酰胺(PAM),其主要作用是对污泥进行化学调理,改善其脱水性能,PAM药剂的选择对污泥脱水系统至关重要。离心脱水机依靠高速旋转的离心力进行泥水分离,必须采用阳离子PAM才能够得到较清的分离液和较低的污泥含水率,若采用阴离子或中性离子PAM,因其与污泥结合性能较差,在离心力的作用下会使形成的絮体被打散而影响脱水后的污泥含水率。选择絮凝剂的具体方法是先进行烧杯试验再进行上机试验。该工程中选用某进口品牌的阳离子PAM药剂,有3个种类,编号为Ⅰ、Ⅱ、Ⅲ,其离子度分别为30%、40%、50%,分子质量分别为4000、6000、8000ku。
2.1.1 烧杯试验
取3个1L的烧杯,将3种阳离子PAM分别配制成浓度为0.2%的溶液。配置过程如下:在烧杯中不断搅拌溶液的同时,缓慢加入粉末状的PAM,直至粉末完全溶解、未见“果冻状”絮团,搅拌时间约为45~60min。取3个50mL的烧杯,每个烧杯内分别加入30mL污泥,污泥含水率约为98%;再分别向3个烧杯内加入10mL的Ⅰ、Ⅱ、Ⅲ号絮凝剂,快速搅拌,然后静沉。首先观察絮凝后污泥的沉降速度和泥水界面高度,以沉降速度快、泥水界面低为佳;然后将形成的絮体污泥取出置于水平面上,以絮团内间隙水较少为佳。通过上述判断,确定Ⅱ号和Ⅲ号PAM较为适宜。重复上述工作,将絮凝剂用量增至15mL,继续判断Ⅱ号和Ⅲ号PAM的效果,确定Ⅱ号PAM较为适宜。
2.1.2 上机试验
上机试验主要检验通过烧杯试验选取的絮凝剂在离心机实际运行条件下的效果,主要考察指标为处理后的污泥含水率和分离液中悬浮物的含量。为选择合适的絮凝剂,对Ⅱ号和Ⅲ号PAM均做上机试验,絮凝剂配制浓度为0.2%。由于该工程调试时间是夏季,因此熟化时间采用1h,絮凝剂用量为25kg。离心机运行参数根据经验确定,主机转速为2400r/min,采用扭力矩控制方式,扭力矩控制范围为12~18N·m,每种絮凝剂分别取3个样品进行试验。
由于启动初期离心机的运行参数未完全稳定,Ⅱ号PAM处理后的污泥含水率偏高,随着各参数运行稳定,Ⅱ号PAM处理后的污泥含水率明显低于Ⅲ号PAM的。另外,两种絮凝剂处理后的分离液中悬浮物含量较接近,一是因为分离液中的悬浮物含量主要与离心机液层调节片有关;二是因为两种阳离子絮凝剂的性能较接近,效果不会相差太大。根据上述试验分析,该工程确定采用Ⅱ号PAM作为污泥脱水絮凝剂。随着离心脱水机各项参数的调节,污泥的脱水效果还将有所提高。
2.2 主机转速的调整
转速的调整会直接影响离心机在单位时间内的处理量和分离效果。主机转速越高,则分离因数越高,处理后的污泥就越干;但当转速过大时,离心力相应增大,会降低絮凝剂的效率,进而增加药剂量,另外也会增加电耗。因此,确定合适的离心机转速至关重要。在Ⅱ号PAM浓度为0.2%、扭力矩为15N·m的条件下,离心机转速以2000r/min为基础,每次升高50r/min,检测处理后污泥的含水率。结果显示,随着离心机转速的升高,处理后污泥的含水率不断下降,当转速升至2500r/min时,处理后污泥的含水率低至70.5%;当离心机转速继续升高时,处理后污泥的含水率呈升高的趋势。综合考虑,确定采用Ⅱ号PAM时的转速为2500r/min。
2.3 扭力矩的调整
该工程中的离心机具有两种控制方式:差速控制和扭力矩控制。采用差速控制的优势在于能使螺旋推料速率始终保持稳定。差速反映了离心机螺旋推料速度的快慢,差速越大则污泥在转鼓内的停留时间越短,脱水越不充分,泥饼含水率越高,但污泥处理量越大;反之,差速越小,则泥饼含水率越低,但处理量越小。采用扭力矩控制是目前水处理行业较先进的一种自动控制方式,是通过调节差速达到推料力矩的稳定,螺旋推料扭矩反映了离心机的负载情况,扭矩过大容易引起离心机堵机,严重时损坏差速器,扭矩过小则分离效果不理想。采用扭力矩控制能够使螺旋推料力矩始终保持稳定,使转鼓内的沉泥不易产生物料堆积现象,其优势是即使在进泥含水率经常变化的情况下也可以避免堵料的发生。因此,力矩控制更适用于对离心机操作了解不深和进泥含水率经常变化的情况。确定合理的力矩大小,有利于离心机的稳定运行以及对污泥的脱水效果。在Ⅱ号PAM浓度为0.2%、离心机转速为2500r/min的条件下,采用扭力矩控制,扭力矩以5N·m为基础,每次升高约3N·m,检测出泥含水率。结果显示,当进泥含水率在99%左右、扭力矩<11N·m时,出泥的含水率过高,处理效果差。当扭力矩在11N·m左右时,出泥含水率在85%以下;当离心机力矩为25N·m时,离心机发生堵料。因此,本工程中离心机的扭力矩调节范围为10~23N·m。另外,当离心机的扭力矩为17N·m时,出泥含水率均能达到75%以下,可作为离心机日常运行的扭力矩值。
2.4 进泥量和进泥含水率
离心机都有一个进泥量和进泥含水率的要求,实际运行中若超过该极限值,离心机会受到损坏,因此运行中应严格控制离心机的进泥量及进泥含水率在允许的范围内。同时,在正常运行范围内,离心机的进泥量与进泥含水率成正比,即进泥含水率越大,则离心机的处理量越大。但是,当进泥含水率偏大时,耗药量将会骤然上升,当进泥含水率达到99.5%以上时,基本无法处理,这是因为固体物体积不够大,离心机的螺旋不足以将推料段封住,泥饼无法产生,导致离心机排水系统和出泥系统同时排出泥水混合物,无法形成泥饼。当进泥含水率过小时,会使离心机内产生的干泥过多而导致螺旋不能及时将污泥推出,从而发生堵料。因此,在调试过程中必须根据该工程污泥含水率的情况,确定合适的污泥处理量,以方便日常运行过程中的参数调节。
采用差速控制,控制范围为8~15r/min,在离心机转速为2500r/min,Ⅱ号PAM浓度为0.2%的条件下,进泥含水率越低,则出泥含水率也越低,但进泥量会降低。当含水率为96%时,进泥量只能达到20m³/h,且运行参数非常不稳定,离心机的电流偏大。当进泥含水率>99%时,污泥处理量明显大于其标称处理量,但此时的出泥含水率偏高。
3 结论
(1)通过烧杯试验和上机试验确定采用Ⅱ号阳离子PAM作为污泥脱水的絮凝剂,其离子度为40%,分子质量为6000ku。但由于调试期间只试验了3种絮凝剂,具有一定的局限性,在离心机稳定运行后,可以扩大絮凝剂试验范围,一方面可以采用价格相对较低的絮凝剂,降低污泥处理成本;另一方面可以发挥离心机的处理能力,提高离心机的效率。
(2)在絮凝剂参数确定的前提下,通过调试确定主机转速为2500r/min,扭力矩为17N·m。但当进泥含水率和进泥量发生变化时,相应的转速和扭力矩均会发生变化,需根据实际情况再进行调整。
(3)在离心机选型时,一定要明确污泥含水率参数范围,否则在实际运行时,当污泥含水率偏低时,会大大降低离心机的处理能力,从而影响污泥脱水系统的运行。