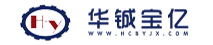
高庄煤业有限公司是年入洗能力3.3Mt的矿井型炼焦选煤厂,主要产品为六级冶炼精煤。该厂于2014年开始改造,分两期建设完成。一期改造生产工艺流程为原煤预先脱泥,50~1mm粒级采用无压三产品重介旋流器分选,1~0.25mm采用TBS粗煤泥分选机分选,0.25~0mm粒级采用XJM型浮选机分选,浮选精矿选用卧式沉降离心机脱水回收,尾矿进入浓缩池沉淀后压滤。二期改造增加二次浮选,卧式沉降离心机滤液进入浮选机再次浮选,二次浮选精矿利用快开压滤机处理。
1 存在问题及原因分析
一期改造完成后,即投入正式生产,但在生产中发现卧式沉降离心机脱水回收效果差,固体回收率仅有50%,不仅造成精煤回收率低、滤液浓度大,还在进入煤泥水系统时,增加系统细煤泥循环量,恶化浓缩效果。
1.1 处理量低
高煤公司选煤厂浮选精煤脱水回收设备采用卧式沉降离心机,该机理论处理量40~50t/h。按照日常生产过程中积累数据计算,按浮选机入料量约为30t/h,浮选产率为68%计算,浮选精煤量仅为20.4t/h。离心机入料三通阀开度仅为40%,设备利用率低。
1.2 浮选精煤极细粒含量高
选煤厂浮选入料由水力分级旋流器溢流、弧形筛筛下水组成。对浮选精煤进行全级小筛分试验后可知,粗煤粒级组成较细,<0.045mm含量占42.14%,而卧式沉降离心机要求<0.045mm粒级不能>40%。
1.3 固体回收率低
按照选煤厂技术检查标准对卧式沉降离心机进行单机检查,采样时间2h,间隔20min,采样量1L/次。由检查结果可以看出:固体回收率仅为50.3%,滤液浓度高达12.83%,相当于有一半的细粒级物料又重新进入系统再次循环。循环煤泥量的增加,加大了煤泥水系统的压力。
2 改进措施
为解决卧式沉降离心机处理效果不佳的问题,综合考虑分析处理能力、入料粒级、工艺流程等,提出将一期重介系统干扰床分选(一种粗煤泥分选设备)的部分精矿掺入浮选精煤,共同进入卧式沉降离心机。改进后,首先降低入料中<0.045mm粒级的含量,满足该设备的入料粒级要求;其次可增加处理量,提高设备利用率;节省干扰床分选精矿的脱水回收设备,节能降耗。
(1)入料粒级:对混料后精矿进行全级小筛分试验,确定物料掺和后<0.045mm粒级含量为26.55%,满足设备要求。
(2)处理能力:一期重介系统干扰床分选精矿采用煤泥立式刮刀离心机脱水回收,按日常生产过程中积累数据计算,干扰床分选精矿量约为15.6t/h。如掺和浮选精煤后,卧式沉降离心机入料量约为35.6t/h,符合设备要求。
(3)工艺流程:将干扰床分选精矿掺入浮选精煤,一起进入卧式沉降离心机。
3 应用效果
改造完成后,按照选煤厂技术检查标准对卧式沉降离心机进行单机检查,采样时间2h,间隔20min,采样量1L/次。
(1)改造后固体回收率提高23.62%,滤液浓度降至4.47%,精煤回收率明显提高,灰分未见明显变化。
(2)固体产物外在水分由24.3%降至18%,水分明显降低。
(3)卧式沉降离心机三通入料阀由40%开度提高至70%,设备利用率提高近30%。
4 经济效益
改造完成后,精煤产率增加约为1.38%,按照年入洗330万t,多产精煤45540t。按照当前市场价格精煤490元/t、煤泥170元/t,年增加效益约1457.3万元。