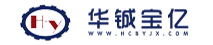
1 引言
锦西石化含油污泥主要来源于污水处理场和生产装置的罐底油泥。含油污泥中一般含油率在70%~75%,含水率在20%~25%,含无机物5%。含油污泥中的原油罐底泥的含油量高,可达到75%。如将其回炼能极大的节约资源。然而由于其中含泥沙量高,装置回炼过程中很容易堵塞塔盘,从而只能将其排放到下水,循环往复于污水处理系统中,增大了污水处理难度,而且造成油资源的浪费。污水处理车间根据现有的工艺流程,采用离心分离技术,并运用脱水剂对污泥进行调质,使含油污泥中的固体组分得到有效去除,从而使污油较大程度的回炼,变废为宝,实现含油污泥的资源化利用。
2 炼油厂含油污泥的特点及其危害
炼油厂含油污泥主要来源于隔油池底泥、浮选池浮渣、原油罐底泥,俗称“三泥”,这些含油污泥组成各异,通常含油率在10%~75%之间,含水率20%~90%之间,同时伴有一定量的固体。含油污泥中含有大量的病原菌、寄生虫(卵)、铜、锌、铬、汞等重金属,盐类以及多氯联苯、二恶英、放射性核元素等难降解的有毒有害物质。污泥体积庞大,若不加以处理直接排放,不但占用大量耕地,而且对周围土壤、水体、空气都将造成污染。
3 含油污泥资源化利用的必然性
含油污泥处理与应用是国内外石油生产领域环境保护的重要内容,是较难解决而急需解决的问题之一,也是制约石油化工环境质量持续提高和经济可持续发展的一大难题。据不完全统计,我国石油化工领域产生油泥量达(10~44)×104t/a。根据国家新排污标准,未经处理的含油污泥排放收费标准为1000元/吨,这将大大增加企业的生产成本,同时石油炼制过程中所产生的隔油池底泥、罐底泥、浮渣以及剩余活性污泥中含有苯系物、酚类、蒽、芘等具有恶臭味和毒性的物质,是国家明文规定的危险废物,含油污泥已被列入《国家危险废物目录》中的含油废物类,《国家清洁生产促进法》要求必须对含油污泥进行无害化处理。含油污泥中富含大量烃类,实施油泥资源化符合可持续发展的战略方针和循环经济的要求。
4 含油污泥的离心分离试验
4.1 试验原理
含油污泥通过离心机中心进料管被引入转子,在离心力的作用下很快分为两层,较重的固相(泥沙)沉积在转鼓内壁上形成沉渣层,由螺旋输送器推出,送固废场填埋或焚烧;而较轻的液相(污油和水的混合物)则形成内环分离液层,从滤液管线排出,送往污油罐进行加温脱水,送装置回炼,从而完成污油回收的过程。
4.2 离心机原理
污泥悬浮颗粒在离心机内的沉降速度和其粒径的平方、粒径和水相的密度差、离心机的离心因数成正比,而和污泥混合液的粘度成反比。因此,污泥粒子与水相之间存在密度差是含油污泥离心分离的前提,要提高和保证离心分离效果,应从增大污泥颗粒粒径和密度,减少粘度,提高离心速度着手。
4.3 含油污泥的化学调质
含油污泥的化学调质主要是通过投加助剂、加温和投加絮凝剂等手段改变含油污泥性质,使高度分散的污泥颗粒、油珠或乳化油进行电中和、网联架桥,从而使污泥颗粒间发生凝聚,变成大颗粒以至大块凝聚体,从而改善其固液分离性能。
4.3.1 加温预处理
将储存有含油污泥的污油储罐T-12/1~3通过罐底蒸汽蛇管加温至70~80℃,破坏乳化油(W/O,O/W)的乳化状态,进行脱水操作。同时,通过加温可降低石油烃类物质的粘度,有利于油、水、固三相分离。
4.3.2 絮凝剂的选择
该试验用无机絮凝剂聚合铝和有机絮凝剂聚丙烯酰胺对含油污泥分别进行絮凝试验,分子量PAM3>PAM2>PAM1>聚合铝,试验结果如下:
药剂型号 | 极性 | 质量分数(%) | 用量(ml) | 静止后液相体积(ml) | ||
5min | 10min | 15min | ||||
聚合铝 | 阳性 | 0.25 | 100 | 80 | 100 | 110 |
PAM1 | 阴性 | 0.25 | 100 | 120 | 150 | 190 |
PAM2 | 阳性 | 0.25 | 100 | 200 | 220 | 250 |
PAM3 | 阳性 | 0.25 | 100 | 170 | 180 | 230 |
由上表可知,阳离子絮凝剂好于阴离子絮凝剂,这是因为阳离子能中和含油污泥胶体表面所带的负电荷,使体系脱稳。有机高分子絮凝剂的絮凝效果要好于无机絮凝剂,是因为分子量增大,分子链增长,有利于对胶体颗粒的捕集和桥连。但分子链太长,也不利于对胶体颗粒的网捕和吸附。
4.3.3 絮凝剂投加浓度
投加絮凝剂的溶质浓度太大,絮凝剂在污泥中的分散效果明显降低不利于扑俘粒子;而浓度太小又会使絮凝速度减慢而导致絮凝剂的用量增加以及增加离心机的容积负荷。经反复试验,确定投加絮凝剂的溶质浓度以0.2%~0.3%为宜。
4.3.4 絮凝剂的投加量
絮凝剂的投加一定要有准确的可调手段。投加量小起不到作用,絮凝效果差,而投加量大一方面造成浪费,另一方面加药量超过一定的限度会形成反胶体,使得介质无法分离。絮凝剂主要是通过架桥和电中和产生作用。当絮凝剂用量过大时,会产生两个副作用:一是使电荷中和过量而逆转;二是对胶粒表面产生保护作用。所以在生产过程中选用流量可调的计量泵,并在药泵的出口安装小流量流量表进行准确投加是必要的。药剂投加量与离心机入口含油污泥的固含量有关。如果油泥固含量较高,药剂投加量较大;如果油泥固含量较低,药剂投加量较小。药剂的投加量是否合适,在其他条件不变的情况下,主要根据出口泥饼含水率(一般在70%~80%)的高低和滤液固含量的浓度确定。药剂投加量一般控制在300~500L/h。
4.3.5 使用化学药剂调质
该实验向含油污泥中投加脱水剂,破坏含油污泥中胶体的稳定性,使水、固、油三相有效分离,提高离心效果。在保证药剂的投加不增加离心机容积负荷的前提下,确定投加量为100~200L/h为佳。
4.4 离心机参数的选择
4.4.1 转鼓转速
根据离心机的工作原理,一般情况下,转速越高分离效果越好,滤饼越干,滤后液越清,轴功率亦越大。但并不是转速越高越好,对于易沉降的介质,转速越高,轴功率越大,容易引起固料来不及推出,造成物料堵塞;对于不易沉降的含油污泥,转速高到一定的数值后,会出现分离效果下降,产泥量减少,滤液中固含量上升的现象。主要因为油泥通过絮凝剂作用而凝结成的胶合物不很稳定,在一定的外力作用下又会分开。因为含油污泥内部包含由架桥作用和范德华力牵引而成的两部分----高分子絮凝剂和含油较高的胶粒。虽然作为整体后,其终合密度略大于油水混合物,然而作为内部个体,含油较高的胶粒的密度小于高分子絮凝剂的密度,因此随着离心机转速增大,含油较高的胶粒和高分子絮凝剂的密度差引起的离心力随之增大,当该离心力大于相对稳定的胶合物内部两组成之间的架桥作用和范德华力合力时,絮凝作用失败,胶合物稳定系统被破坏。因而出现分离效果下降,产泥量减少的现象。在静置时间相同的情况下,PAM2比其他絮凝剂效果要好,故选择作为离心试验的絮凝剂,同时做空白试验。经试验发现只有当离心机的转速在2000r/min以上时污泥絮体才能形成明显的固液分层现象。测定转速在2000、2500及3000r/min时絮凝体系的固液分离情况,测试表明分离效率随着转速的增大而显著提高。
4.4.2 差转速
差转速的大小主要取决于离心机所需排渣量的大小,污泥脱水时,离心机差转速不能过高,因为差转速过高时,由于转鼓内流体的挠动加快会增大流体对湿沉渣的冲刷,增大分离液中的含固量,降低固体回收率从而影响分离效果。差转速过低又会明显降低螺旋的输送效率,使差速器受到的扭矩过大损坏差速器。由于含油污泥粘度大,固液难分离,和絮凝剂反应时间长,因此差转速不宜过大。试验研究证明,用于含油污泥脱水时,离心机的差转速以3~5r/min为宜。
4.4.3 离心机处理量
离心机的处理量是指能达到分离要求的进机流量。当进料流量过大时,离心机转鼓内的渣层增厚,沉渣层表面松散的微粒容易被冲刷,从而明显降低分离效果。离心机油泥的固含量和处理油泥的量有较大的关系。离心机入口油泥固含量较高,虽然在一定程度上提高了离心机的处理量,但是必须选用较高的药剂溶解浓度,不利于油泥与药剂的快速混合,影响分离效果。控制较低的油泥处理量,就可以选用较低的药剂溶解浓度,有利于药剂与油泥的快速混合,可以得到较好的分离效果。处理含油污泥时离心机处理量一般控制在3~5m³/h。
4.5 工艺参数确定
为保证达到处理效果的同时,又能节约成本,节省 水、电、蒸汽药剂等,本试验确定了较佳的处理工艺参数,如下:
项目 | 指标 |
泥渣温度(℃) | 70~75 |
进料量(m³/h) | 3~5 |
絮凝剂浓度(%) | 0.25 |
絮凝剂量(L/h) | 350~450 |
脱水剂量(L/h) | 100 |
离心机转鼓转速(r/min) | 3265~3266 |
离心机差转速(r/min) | 3~4 |
4.6 回收油品质分析
离心机滤液线流出的分离液(污油)送往装置回炼,该污油经滤液线送往集油井,再经泵拣到污油罐进行加温脱水。回收油采样分析数据如下:
样品编号 | 含油率(%) | 含水率(%) | 灰分(%) |
1 | 90.3 | 8.97 | 0.73 |
2 | 88.6 | 10.92 | 0.48 |
3 | 90.2 | 9.36 | 0.44 |
4 | 87.2 | 12.28 | 0.52 |
5 | 85.4 | 14.21 | 0.39 |
平均值 | 88.34 | 11.15 | 0.51 |
5 结论
(1)通过对含油污泥进行加温,投加化学药剂调质等预处理,可有效降低含油污泥的粘性,从而实现固液快速分离。
(2)通过对含油污泥投加有机高分子絮凝剂,可使高度分散的污泥颗粒、油珠或乳化油进行电中和、网联架桥,使污泥颗粒间发生凝聚,从而改善其固液分离性能。
(3)经过卧螺式两相离心机处理过的含油污泥,分离液含油可达88%,可送往生产装置回炼,泥饼可进行填埋或焚烧。
(4)锦西石化污水处理车间运用离心分离技术处理含油污泥成功解决了长期困扰企业的高含泥污油无法回炼的难题,实现污油回炼及含油污泥的资源化利用,避免了企业资源浪费和能源损失,在取得环境效益的同时,又产生一定的经济效益。