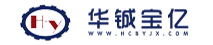
目前,发酵废水的处理常采用絮凝沉降加带式过滤法。抗生素废水可用此流程处理,使出水达到去除固形物55%,COD去除率为65%的作用,所得泥饼含固率仅为17%,且此工艺流程较长,占地多,操作较烦琐。我们希望能够找到一个操作简单,菌丝等固形物与COD去除率高的方法。
1 用卧螺机处理废菌丝液的设计思路
1.1 两种设备从理论上对比
(1)卧螺离心机利用离心沉降原理进行固液分离,由于没有滤网,不会引起堵塞。而带机利用滤袋进行固液分离,为防止滤袋堵塞,需高压水不断冲刷。
(2)离心机适用各类菌丝的浓缩和脱水,带机也适用各类菌丝,但对某些菌丝需投药量大且脱水困难。
(3)离心机在脱水过程中当进料浓度变化时,转鼓和螺旋的转差和扭矩会自动跟踪调整,所以可不设专人操作,而带滤机在脱水过程中当进料浓度变化时,转鼓和螺旋的转差和扭矩会自动跟踪调整,所以可不设专人操作,而带滤机在脱水过程中当进料浓度变化时,带速、带的张紧度、加药量、冲洗水压力均需调整,操作要求较高。
(4)在离心机内,细小的污泥也能与水分离,所以絮凝剂的投加量相对较少,菌丝回收率为95%以上,脱水后菌丝的含水率为75%左右,而带滤机由于滤带不能织得太密,为防止细小的菌丝漏网,需投加较多的絮凝剂以使污泥形成较大絮团,菌丝回收率为90%左右,脱水后泥饼含水率80%左右。
(5)离心机全天24h连续运行,除停机外,运行中不需清洗水;而带机滤布需松弛保养,一般每天只安排两班操作,运行过程中需不断用高压水冲洗滤布。
(6)离心机占用空间小,安装调试简单,配套设备仅有加药和进出料输送机,整机全密封操作,车间环境好。而带机占地面积大,配套设备除加药和进出料输送机外,还需冲洗泵,空压机,污泥调理器等,整机密封性差,高压清洗水雾和臭味污染环境,如管理不好,会造成泥浆四溢。
(7)离心机易损件为轴承和密封件,卸料螺旋的维修周期一般在3年以上。而带机易损件除轴承、密封件外,滤带也需更换,价格昂贵。
1.2 菌丝废水直接沉降速度测试
菌丝废水中的菌丝是有机物质,生长周期存在不同步现象,并且存在部分自溶现象,部分菌丝出现大空泡,造成菌丝混合物成分不均一,比重不同,容器中的菌丝悬浮液经过沉降一段时间后将逐渐分层。自然沉降出现分层现象需要数小时时间,菌丝悬浮液的重相下沉到容器底部,而轻相则浮在上部,轻重相之间形成某种的分界面。分层的速度受到组成悬浮液轻重相密度差的影响,密度差越大,分层的速度越快。在实际操作中,我们通过实验确定菌丝自然沉降分离需要3~8h时间不等,这样的情况不利于离心机进行分离,所以必须对絮凝剂进行筛选,是这个课题的关键难点之一。
1.3 菌丝废水絮凝分离测试
同常规无机高分子絮凝剂相比,有机高分子絮凝剂有其独特的优越性,尤其在改善强化混凝带来的负面影响方面有突出的效果。而选用助凝剂助凝可以增大絮体粒径和密实度,提高沉降效果和除浊能力,同时降低絮凝剂投量,有利于强化常规絮凝效果。
1.3.1 絮凝剂的选择
本着絮凝效果与成本投入兼顾的原则,对国内外的絮凝剂均进行了选取。根据污泥脱水应用中聚丙烯酰胺溶解时间越短效果越好,同时粘度高的聚丙烯酰胺对菌丝中胶体悬浮粒子的吸附和“架桥”能力强,用量少而效果好。为此,对6种型号为Ⅰ、Ⅱ、Ⅲ、Ⅳ、Ⅴ、Ⅵ聚丙烯酰胺的溶解性能、粘度性能和污泥脱水效果进行比较,使用前均用超纯水配制成0.2的溶液。
聚丙烯酰胺 | 外观 | 相对分子量(104) | 粘度(mPa*s) | 固含量(%) | 溶解时间(min) |
Ⅰ | 白色粉末 | 1200 | 1567 | 97 | 2.3 |
Ⅱ | 白色粉末 | 1400 | 2456 | 98 | 2 |
Ⅲ | 白色粉末 | 1600 | 3344 | 97 | 2.6 |
Ⅳ | 白色粉末 | 1900 | 2211 | 97 | 2.9 |
Ⅴ | 白色粉末 | 2100 | 1233 | 95 | 3 |
Ⅵ | 白色粉末 | 20000 | 11123 | 96 | 5 |
1.3.2 实验方法
在1000mL的刻度烧杯中加入500mL待处理的青霉素发酵提取废水,检查pH值,用碱液调整pH值到6.5~8.0(这样可以减少用量),分别加入2.5~7.5mL稀释后的上述絮凝剂,然后以100r/min的速度快速搅拌1min,直至有大的絮状物形成。停止搅拌,让样品静置至少15min,使絮状物沉到底部,滗出上清液,从菌丝絮凝效果与絮凝时间上进行数据记录并进行分析,结果如下:
絮凝剂种类 | 絮凝剂用量(mL) | 絮凝时间(min) | 絮状物大小与紧密程度 |
Ⅰ | 7.5 | 2 | 未见絮状物 |
Ⅱ | 4 | 3 | 絮状物小,不紧密 |
Ⅲ | 46 | 3 | 未见絮状物 |
Ⅳ | 3 | 1 | 絮状物大,紧密 |
Ⅴ | 3 | 6 | 絮状物大,不紧密 |
Ⅵ | 5 | 3 | 絮状物小,紧密 |
通过以上数据综合分析,我们选定Ⅳ号絮凝剂作为上机实验的絮凝剂。
1.4 废水离心分离实验
离心沉降分离的原理,是利用悬浮液或固体颗粒在液体中沉降速度不同的特点,在离心力场的作用下迅速沉降分层,实现液-固分离目的。
离心分离机分离性能的重要指标是分离因数,它表示被分离物料在转鼓内所受的离心力与其重力的比值,分离因数越大,通常分离也越迅速,分离效果越好。
分离因数计算公式Fr=w2r/g。
式中,w为转鼓角速度,rad/s。r为细颗粒回转半径,m。g为重力加速度,9.8m/s2。
在实验室我们选用了转速4000r/min,回转半径0.1m,分离因数2000的电动离心机分离菌丝废水。取菌丝废水(SS值为20000mg/L)放入离心试管中,置于离心机内,开启电源,运行40s后关机,测定离心清液的SS浓度。另取相同浓度的菌丝废水加入所选絮凝剂,令其水中浓度达到絮凝效果,搅拌后以同样操作进行实验,并测定离心清液SS浓度。所得结果如下:
絮凝剂 | SS处理前情况(mg/L) | SS处理后情况(mg/L) | 去除率(%) |
加入 | 20000 | 700 | 96.5 |
不加入 | 20000 | 2880 | 85.6 |
本实验用分离因数为2000的离心机,实验结果表明,用离心机处理菌丝废水是可行的,只要分离因数足够或加入絮凝剂,完全可以通过直接使用离心法处理菌丝废水,实现达标排放。在实验过程中加入絮凝剂的作用,是由于废水中存在微细的菌丝废水和其他杂质,由于同性相斥,不易凝聚成大颗粒,以本身重量产生沉降非常困难,因而会形成较为稳定的悬浊液,若能利用与悬浮微粒带相反电荷的化学药剂吸附中和这些微粒表面上的电荷,使表面电位减少,胶体微粒的稳定状态因此被破坏而发生凝集而加速沉降。因此,我们选用了可在碱性条件下应用的某型号聚丙烯酰胺作为絮凝剂。
2 离心机的选择
卧螺离心机不需过滤介质(滤袋)而是通过电机带动无孔转鼓及同心安装的输料螺旋,以一定的差速同向高速旋转。物料由进料管连续引入输料螺旋内筒,加速后进入转鼓,在离心力作用下,较重的固相物沉积在转鼓壁上形成沉渣层。输料螺旋将沉积的固相物连续不断地推至转鼓锥端,经排渣口排出转鼓及机外。较轻的液相物则形成内层液环,由转鼓大端溢流口连续溢出转鼓,经排液口排出机外。进水、排水、排泥连续进行。它克服了过滤式离心机的缺点,能在全速运转下,连续进料、分离和卸料。具有结构紧凑、连续操作、运转平稳、适应性强、生产能力大、方便实现自动控制和维修方便等特点。基于上述分析,我们选择了卧螺离心机。
按实验情况分析,必须选择分离因数大于2000的离心机才能将菌丝废水从中分离并使排水达到公司排放标准,结合抗生素膜过滤废水的状况和卧螺离心机的系列产品,我们选择了进料量为10~15m³/h的卧螺离心机进行生产实验。
3 工艺流程及运行结果
3.1 工艺流程说明
菌丝废水由车间管道流入污水调节池中。废水由泥浆泵抽入卧螺离心机,在离心机的作用下,固体物在离心机转鼓内壁上堆积,被螺旋推向转鼓的小端,脱水后从排渣口排出,清水从离心机转鼓大端的溢流孔流出。调节池可设液位高低位自动控制。整个系统的运行可通过PLC实现全自动控制,进水、排水、排泥连续进行。分离出的清水可进一步进行浓缩处理,实现综合利用和菌丝废水零排放。
3.2 运行结果测试及结论
中试装置建成后经长期运行,一直能正常稳定,测定结果如下:
进水流量(m³/h) | 进水浓度SS(mg/L) | 出水浓度SS(mg/L) | 固形物去除率(%) |
10 | 20000 | 660 | 96.7 |
12.5 | 20000 | 650 | 96.75 |
15 | 20000 | 680 | 96.6 |
进水流量(m³/h) | 进水浓度COD(mg/L) | 出水浓度COD(mg/L) | 固形物去除率(%) |
10 | 50000 | 15300 | 69.4 |
12.5 | 50000 | 16004 | 67.99 |
15 | 50000 | 14980 | 70.04 |
以上数据表明:在使用絮凝剂的情况下,该型离心机在其操作范围10~15m³/h情况下,都可以使出水COD降低70%,SS降低96%以上。
4 结论
利用卧螺离心机处理菌丝废水,在絮凝剂聚丙烯酰胺的存在下,以10~15m³/h的进水流量,可实现连续进水、出水、出渣,实现稳定运行,达到COD去除70%,SS降低96%以上,所得菌丝可进一步制成有机肥料,可产生一定的经济效益。