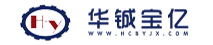
大规模推广聚驱采油技术增加了油井采出液携砂量及悬浮物含量,造成污水处理系统负荷大,处理后水质不达标等问题。为保证水质达标,油田生产中缩短清淤周期,污水系统采用连续排泥工艺,有效缓解了采出液携砂量大幅度增加带来的问题。但污水系统连续排出的污泥中含水率高达90%以上,导致污泥存积、拉运和后续处理的量显著增大。常用的后续污泥无害化处理方法有超声波法、焚烧法、热解法、萃取法等,这些处理方法的成本较高,因此,需要对连续排泥工艺产生的污泥进行减量化处理,减少拉运费用和后续处理的处理量,保障无害化处理装置高效运行。
油田污水站具有数量多、分布远的特点,综合考虑处理量、能耗、费用,选用调质-机械分离法进行污泥减量化处理。该方法通过调整污泥固体粒子群的性状和排列状态,使之适合机械分离处理以改善脱水效果,在污泥含水率为30%~70%的工程中应用良好。但是污水系统连续排出的污泥含水率高达90%,因此,需要对工艺进行设计,并通过现场试验得到影响因素对减量效果的作用规律,优化工艺参数。
1 油田污泥离心脱水减量处理工艺
根据卧螺离心机的结构、工作原理及效率影响因素,设计了油田污泥离心脱水减量处理工艺。人工清淤中通过加压锅炉热水射流剥离含油污泥,排放至沉降罐外的缓冲水池,缓冲水池内的沉没泵将高含水污泥泵送至调质搅拌罐内进行加热、搅拌、匀化,加入絮凝剂使污泥中的悬浮物及固体进行絮凝,减轻高速离心运动中固相的破碎分散,调质罐内的搅拌可以显著减少药剂的用量。采用螺杆泵替代离心泵输送污泥,防止破坏絮团。离心处理后,污泥中的水相进入回收水池,浓缩减量后的污泥装车外运。
2 工艺参数对减量效果的影响
2.1 转速对减量效果的影响
调整离心机的转速,以处理后污泥含水率为评价指标,在进泥量保持一定(8m³/h)的条件下,为了确保转速与样品对应,在调整转速10min后取样。具体工艺参数:转速为2000~2600r/min,差速为9.5r/min,加药量为175g/m³,温度为45℃。
试验结果显示,当转速在2031~2437r/min的范围内,转速越高分离效果越好,泥出口含水越少。但并不是转速越高越好,含油污泥不易沉降,当转速超过2437r/min后,出泥中含水率升高。这是因为含油污泥是一种通过架桥作用和范德华力将高分子絮凝剂、固相和含油胶粒絮凝在一起的胶合物,在过高转速作用下分开的结果。虽然三者作为整体,密度略大于油水混合物。然而作为单相,含油较高的胶粒的密度小于高分子絮凝剂的密度,因此,当离心机转速增大,由密度差引起的离心力随之增大。当离心力大于相对稳定的胶合物内部组成之间的架桥作用和范德华力合力时,絮凝作用减弱,胶合物失稳破坏。因而出现转速过高,处理效果变差的现象。
2.2 差速对减量效果的影响
离心机主要通过转鼓和螺旋输送器的差速推动固相实现固液分离。在转速为2370r/min,加药量为175g/m³,温度为45℃,差速为9~11.5r/min的工艺参数下进行现场试验。
试验结果显示:随着差速的增加,离心处理后的污泥出现含水率升高的现象,当差速在9~10.5r/min范围内,变化较快,超过10.5r/min后,变化较慢。这是由于差速的大小影响离心机排固量的大小,差速过高时,转鼓内流体的扰动作用加强,会增大流体对转鼓内壁沉积固相的冲刷,影响分离效果。因此,差速应该保持在较低水平。
2.3 加药量对减量效果的影响
絮凝剂CPAM的投加可以使污泥中分散的物质絮凝,增强离心作用下的液固分离效果。在转速为2377r/min,差速为9.7r/min,温度为45℃,加药量为150~275g/m³的条件下进行试验。污泥中的固相和含油胶粒通常带有负电荷,相互排斥,加入絮凝剂后,降低了粒子电位,使粒子相互吸引形成絮团。同时絮凝剂本身的吸附架桥作用又将大量的絮团吸附形成了更大的絮团,在离心作用下固相下沉。
试验结果显示,随着加药量的增加,处理后的污泥含水率下降。在加药量由150g/m³增加到225g/m³时,污泥含水率随加药量的增加急剧降低。加药量在225~275g/m³之间含水率降低缓慢。
2.4 温度对减量效果的影响
温度对水质粘度和絮凝剂的作用具有一定的影响,在转速为2392r/min,差速为9.5r/min,加药量为175g/m³,温度为35~65℃的条件下进行试验。
试验结果显示,随着温度的升高,处理后污泥含水率不断下降,尤其是35~45℃范围内下降明显。这是因为温度升高,降低了水相黏度,同时减弱了界面膜强度,使更多的水滴和含油胶粒分开。温度升高加剧了固相、含油胶粒的热运动强度,增加碰撞机会,有利于固相、胶粒脱稳凝聚。
综上所述,温度对污泥处理效果的影响主要是通过改变油水黏度和增加聚并频率实现。随着温度的进一步升高,含水率下降趋势放缓。
3 工艺方案优化
3.1 参数优化
转速、差速、加药量、温度4个因素的综合作用决定了油田污泥离心脱水减量处理效果,采用正交试验设计方法优化工艺方案。离心后的污泥含水率越低说明处理效果越好,转速是影响离心处理效果的主要因素,其次是差速、温度和加药量。试验的较优运行方案是:转速为2500r/min,差速为9r/min,加药量为225g/m³,温度为55℃。
3.2 工艺稳定性分析
将工艺在较佳方案下连续运行2h,每小时取样5次,考察工艺运行的稳定性。离心机入口、出水口、出泥口取样测试结果表明,排出的污泥物性参数平稳,出泥口的含水率和含固率波动较小。处理后,平均含水率从入口的97.37%下降到出泥口的59.17%,平均含固率从污泥入口的1.73%上升到出泥口的33.72%。离心机出水口和出泥口分流比范围是24.14:1~33.19:1,对应的污泥减量比例为96.02%~97.08%,达到了污泥减量的目的。
4 结论
(1)依托污水站现有工艺,以卧螺离心机为关键设备,与缓冲水池、沉没泵、调质罐、絮凝剂加药装置、回收水池等组合成一套油田污泥离心脱水减量处理工艺。
(2)现场试验分析减量工艺的影响因素,包括转速、差速、加药量和温度。结果表明,在一定范围内,离心机的转速越高,差速越低,絮凝剂加药量大,温度较高,有利于降低出泥口的污泥含水率。
(3)采用正交试验方法优化得到较佳离心减量处理工艺参数为:转速为2500r/min,差速为9r/min,加药量为225g/m³,温度为55℃。处理后,平均含水率从入口的97.37%下降到出泥口的59.17%,平均含固率从污泥入口的1.74%上升到出泥口的33.72%。工艺运行稳定,离心机出水口和出泥口分流比范围是24.14:1~33.19:1,对应的污泥减量比例为96.02%~97.08%,达到了污泥减量的目的。