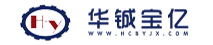
石油天然气勘探钻井作业时,会产生大量的钻井固体废弃物,通常称为钻井固废,一般产生量为0.3~0.4m³/m进尺,以设计井深为5000m的单井计算,将产生1500~2000m³的固废,其主要由钻屑、除砂除泥器脱出的砂泥、清掏方井和循环罐产生的废弃渣泥、废水处理时产生的渣、钻井作业时及完井时产生的废弃钻井液等组成。钻井固废组分复杂,包含了钻井液处理剂的所有成分,如不先对其进行固液分离脱水而直接对其进行处置和资源化利用,将会大大增加处理的成本费用。因此,固废处理减量化是处理三原则中十分重要的一个环节,而固废处理减量主要依赖于固液分离技术及装备。在分析论述钻井固废特点的基础上,分析论述了各种固废固液分离技术装备,比较了各种分离技术装备的适用范围及其优缺点,对油气田环保管理决策者和相关专业人员具有一定参考价值和指导作用。
1 钻井固废的主要特性
从钻井固废的来源组成可看出,钻井固废性质除与井下地质岩石性质相关外,主要决定因素为钻井液性质,而钻井液性质又主要决定于所用的钻井液处理剂。对一口井来说,浅井段往往对钻井液性能要求不高,所加钻井液处理剂品种少,加量也少,对应产生的钻井固废污染物种类相对少些,含量也低些;随井深增加,地下地质构造越复杂,钻井液性能要求越来越高,否则就会出现卡钻等工程事故,所加钻井液处理剂品种多,加量也多,对应产生的钻井固废污染物种类相对多些,含量也高些。对不同区域的油气钻井作业,如油气勘探地质构造复杂,所钻井更深,钻井液性能要求更高,相对应产生的固废污染物就更复杂,污染物含量更高,比如四川、塔里木和新疆等油气田;反之则相反,如长庆、大庆、吉林等油气田。
钻井固废的主要特点:
(1)固相含量高。经钻井振动筛脱浆后的钻屑,含水率较低,固相含量很高,主要为地层岩屑等软硬固废;而经除砂除泥器脱出的渣泥含水率更低,主要为地层细砂泥及重晶石料等加重材料;而其它固废虽有一定量的含水率,但固相含量都很高。
(2)粘附性强。主要原因是这些固废都与钻井液有关,钻屑及除砂除泥器脱除的渣泥表面粘附并包裹着泥浆,其它钻井固废主要来源于钻井液,钻井液都有一定粘度,因此造成钻井固废与其他多数工业固废相比,粘附性更强,脱水分离困难,加药混搅混匀困难,处置效果也相对较差。
(3)色度高。主要原因是钻井液多数为黑色,进而造成固废色度高,特别是三开后采用磺化或聚磺化泥浆体系对应产生的固废。
(4)组分复杂,有机物含量高。因钻井液组分复杂,并大多以各种有机处理剂原料生产而成的高COD贡献值的钻井液处理剂配置而成。其组分复杂,有机物(COD)含量高,但持久性有机污染物含量低,给生物降解处置资源化土壤利用奠定了基础。
(5)有害重金属含量低。虽然钻井固废都与钻井液相关,但由于行业坚决杜绝高含难降解有害重金属钻井液处理剂的使用,同时,各油气田都要对钻井液处理剂进行入厂质量把关检验,从源头杜绝含难降解有害重金属钻井液处理剂的使用。因此,只要地层岩屑不含有害重金属,钻井固废中有害重金属含量就低。这给生物降解处置资源化土壤利用创造了条件。
(6)pH较高。主要原因是为确保钻井液性能要求,pH一般都控制在8.5~10.0,而钻井固废都与钻井液相关,因而钻井固废pH一般都在7.5~9.0。
(7)油含量不是很高。一般水基钻井液体系钻井产生的固废油含量都不高。主要原因一是钻井地面用油设备如发电房、机房和储油罐区域都建有隔油设施;二是钻井液中不允许直接加柴油来提高钻井液防卡能力;三是用油设备注重防跑、冒、漏。这些措施有效控制和减少了钻井固废中的油含量。但如采用油基钻井液钻井,则产生的固废中油含量就高,如四川长宁威远和昭通页岩气的勘探钻井,油基钻屑中油含量在5%~20%。
(8)组分含量不固定。就一口井而言,由于井深不同,地层岩性不同,所造成的钻井固废组分也将发生变化。同时,一口井在浅井时,往往采用聚合物无固相钻井液体系钻井,随井深增加,转变为聚合物磺化体系钻井液钻井,钻井液体系发生变化,其主要组分也将发生变化,相应产生的钻井固废组分性质和污染物含量也会发生变化。同时,由于不同地质构造,不同地区采用不同钻井液体系钻井,钻井固废组分性质和污染物含量也有所不同。
(9)产生排放具有连续性。由于钻井为连续作业,只要钻井作业进行,钻井固废就会产生。
(10)产生量总体具规律性。在正常情况下,因使用的钻头尺寸大,前期钻井钻速也快,掏泥浆罐次数相对较多,对应产生的钻屑多,固废量多;后期钻头尺寸小,钻速也相对较慢,对应产生的钻屑少,固废量也少。但废弃泥浆的产生不具规律性,其产生对钻井固废量的贡献量十分大,同时完井阶段,由于清掏泥浆罐和泥浆储备罐,加之完井后,该井所用泥浆不转运到其它井再使用,而转化为固废,将会大大增加固废量。
2 国内外钻井固废固液分离技术装备
2.1 振动筛技术装备
油气勘探钻井用振动筛是钻井必配设备,其作用对钻井液而言,主要是减少钻井液中的含砂含泥量,净化钻井液;对钻井固液而言,主要是减少钻屑固废的含液(水)量。其原理是通过高频振动筛,将粘附在钻屑上的水或钻井液去除,从而达到固废减量的目的,此技术也可算作过滤技术。近年来,国内外很多厂家对振动筛做了改进研究,一是激振器采用防爆型振动电机,全封闭轴承润滑系统,惯性激振力比常规激振器提高1.5~1.7倍;二是增加筛网长度,增加固废振动分离过程和时间等;三是采用多层叠加筛网,如三维波浪形筛网面积比平板网增加50%~125%;四是采用可调筛网坡度的筛箱支座,使筛网处置量和处置效率尽可能增大等来增强固液分离效果。振动筛技术装备适合于固相有一定粒径的钻井固废的固液分离减量,如钻屑的固液分离减量,其主要有以下几种类型:
2.1.1 平动椭圆振动筛
SWACO公司的第三代平动椭圆振动筛,一是采用全不锈钢结构,双层筛框设计,结构紧凑,处置量大,占地面积小;二是能够保持合适的运动轨迹,减少筛网的磨损,寿命长,并具更好的排泄能力和钻井液的回收率;三是配置有采用可分离的进液槽、气动筛网锁紧等的自动筛面坡度调整装置,筛网更换更快更安全,钻井液回收更有效等。
2.1.2 双轨迹振动筛
此类振动筛以SWACO公司的MEERKAT型为代表,采用平动椭圆运动轨迹设计,在一个振动筛上可形成两种运动轨迹,即平动椭圆运动和直线运动。由于延长了固相在筛面的驻留时间并减少了抛掷指数,使脱除的固相含水率更低,提高了钻井液回收率并延长了筛网寿命,减少了运行费用。
2.1.3 双筛面振动筛
斯伦贝谢M-I SWACO公司研发的MD-2双筛面振动筛占地面积较小,它与DURAFLO复合筛网结合使用可以使它的处置能力几乎为标准单筛面振动筛的两倍。
2.1.4 长筛一体机
此技术装备由中国石油集团川庆钻探工程有限公司长庆钻井公司研发生产。
优点体现在:
(1)设备更精简、使用更简便、钻井液净化效率更高、钻屑含水率更低。
(2)筛布的总有效面积和三联式两级振动筛一样,但由于振动长度大大增加,钻井液固相清除能力较三联式两级振动筛提高5~7倍,极大地提高了固相清除效率。
(3)能使钻屑含水率降低50%左右,可降低固化剂量消耗70%左右。
(4)能极大提高钻井液过筛处置能力,极大限度抑制跑浆现象发生,钻井液的固相含量控制更好。
(5)二级固控系统使用的设备大大减少,使用功率降低51.1%,配套费用降低38.9%,经济效益显著。
2.2 离心技术设备
离心技术装置原理是利用高速旋转产生的离心力,由于固废组分比重不一样,达到固液分离目的。固相在螺旋输送器的推动下,被输送到转鼓的锥端,由出口连续排出;液环层的液体则由堰口连续“溢流”排至转鼓外靠重力排出。离心技术装备适合固液相有一定比重差的钻井固废的固液分离减量,如钻屑的固液分离减量。
2.2.1 密闭式钻屑脱液离心机
密闭式钻屑脱液离心机由美国SWACO和Hutchison Hayes International 2个公司联合开发。这种离心机通过控制固体颗粒在转鼓里的停留时间而得到较佳的干燥效果。能够在某一设定的分离因数或者变化的分离因数下操作,具有良好的分离性能;对于柴油基质、含矿物油或合成基钻屑的脱液效果尤佳。
结构特点:
(1)结构设计独特新颖。鼠笼状结构设计,在一串环板上穿过10来个钢管,结构质量分散,刚度和强度好;采用圆筒形筛网结构,在筛网区域固相颗粒和有均衡持续的分离因数,分离效果确保较佳;由于螺旋和筛网之间间隙微小,较佳分离工况下的堵料减少;在机器设置进料口,结构紧凑。
(2)主电动机和副电动机可调节。可实现生产能力可调节(30~90t/h),可调节变动分离因数,可以变化固相颗粒停留时间。
(3)钻屑进料无需稀释。不需要稀释物料,能够让滤饼达到较佳的干燥效果。
(4)电力需求小。
(5)符合环保要求。可实现沉渣含油(质量分数)为3%~5%。
2.2.2 SWACO414型离心机
M-ISWACO 414型离心机能高效的回收95%的重晶石,能大大减少泥浆的流失,坚固的机械结构和抗腐蚀的材料确保了其使用寿命和较低的维护费用。
2.2.3 大排量低速离心机
大排量低速离心机通过改变内部结构,扩大固相清除范围,提高了钻井液清除速度。与中速离心机相比,固相清除范围由6~45μm扩大为15~105μm,基本涵盖了中速离心机的范围;钻井液处置速度由原40m³/h提高到80m³/h,与中速离心机处置钻井液时相比,钻井液的固相清除效率可提高一倍。
2.3 压滤技术装备
压滤技术在固液分离上的作业原理是采用挤压作用,把固相中包裹吸附的水分挤压分离出来。压滤技术装备适合处理废弃泥浆和废水处理水渣泥,不适合处理含粒子钻井固废的固液分离,如钻屑的固液分离。由于使用压滤技术装备时往往需预先加入化学脱稳处理剂对固废中的固相进行脱稳处理,因此,分离出的液相含有化学脱稳处理剂,回用配制钻井液时可能会使钻井液性能受影响,钻井固废脱除液通常不被钻井液处理管理方再使用,进而在减少固废含水量的同时,增加了废水产生量。
2.3.1 板框式污泥脱水机
选型板框式压滤脱水机设备时应重点考虑的因素:
(1)泥饼含固率。与其他类型脱水机相比,一般板框式压滤机泥饼含水率低,含固率高,可达35%,板框式压滤机是减少污泥堆置的占地考虑因素的首选方案。
(2)滤板及滤布的材质。要求耐腐蚀,滤布要具有一定的抗拉强度。
(3)滤布振荡装置,以使滤饼易于脱落。
(4)滤板的移动方式。为减轻操作人员劳动强度,选择通过全自动或半自动完成液压-气动装置。
板框式压滤机与其它型式脱水机相比,由于为间断式运行,效率低,操作间环境较差,有二次污染,并存在占地面积较大的缺点。
2.3.2 带式污泥脱水机
带式污泥压滤脱水机设备选型时应考虑的因素:
(1)滤带。要求应具有较高的抗拉强度、耐曲折、耐酸碱、耐温度变化等特点,同时还应考虑污泥的具体性质,选择适合的编织纹理,使滤带具有良好的透气性能及对污泥颗粒的拦截性能。
(2)辊压筒的调偏系统。一般通过气动装置完成。
(3)滤带的张紧系统。一般由气动系统控制。滤带张力一般控制在0.3~0.7MPa,常用值为0.5MPa。
(4)带速控制。不同性质的污泥对带速的要求各不相同,即对任何一种特定的污泥都存在一个较佳的带速控制范围,在该范围内,脱水系统既能保证一定的处置能力,又能得到高质量的泥饼。
2.2.3 叠式污泥脱水机
主要特点和优点:
(1)占地空间小,便于维修及更换;重量轻,便于搬运。
(2)不易堵塞。具有自清洗功能。可减少冲洗用水量和内循环负担。擅长含油污泥的脱水。
(3)低速运转,约2~3转/分的转速,耗电量极低。
(4)操作简单。能无人连续实现24小时运行。
(5)噪音振动小,故障少,操作安全。
(6)维护作业简单,时间短。
(7)经久耐用。机体主要采用不锈钢材质,使用寿命长。
(8)需更换的部件只有使用周期长的螺旋轴和游动环。
2.3.4 德国琥珀螺旋挤压机
其由废弃液体进料单元、螺旋挤压单元、自动控制系统组成。其能在较小的压力下,达到较高的脱水能力,得到含水量较低的污泥。
其特点和优点:PLC控制,自动化程度高;出液回流絮凝反应器,可节省处置剂用量;低噪声标准,封闭设计;固液分离效率高;易磨损部件少,使用寿命长;低运行和维护费用;适合移动使用。
2.4 过滤技术装备
过滤技术是根据钻井固废不同组分颗粒的粒径差异,在外力作用下使固废中的固体颗粒被截留在介质上,水分(液体)通过多孔介质的孔道分离,从而实现固液分离脱水目的。过滤技术装备适合处理有一定粒径差的钻井固废,如钻屑和掏泥浆罐渣泥,往往不需预先加入化学脱稳处理剂进行固废脱稳,因此,分离出的液相可再回用配制钻井液。
2.4.1 筛分脱水技术装备
河南新乡高服筛分机械有限公司生产了一系列筛分过滤脱水设备,如概率筛、直线振动筛、脱水筛、旋流筛、气流筛和摆动筛等。
2.4.2 真空过滤脱水机
真空过滤脱水机是以真空负压为推动力实现固液分离,是一种能连续操作、高效、新型的固液分离设备。它能实现滤饼洗涤液与母液分段手机,过滤、滤饼洗涤、卸渣、滤布再生等工艺操作也可以连续自动完成。其与压滤法的基本理论相同,只是压滤法推动力为正压,而真空过滤法为负压。真空过滤机有转筒式、烧绳式和转盘式三种类型。
技术特点:
(1)整体结构模块化设计,可灵活组装,便于运输和安装。
(2)自动化程度高。主要工序连续自动化,工人劳动强度小,生产效率高,运行成本低。
(3)工艺方便。可任意调整真空度、逆流洗涤级数、滤布速度,达到过滤效果较佳。
(4)速度快。物料经沉淀区,形成小颗粒在上层,大颗粒在底层的滤饼结构,滤液通透阻力小,过滤速度快。
(5)洗涤效果好。可分别收集、再利用母液和洗涤液,可实现均匀彻底的多级平流或逆流洗涤。
(6)应用了DCS技术的控制系统,可实现现场和远程自动控制。
2.4.3 离心过滤脱水机
在过滤离心机转鼓壁上有许多孔,转鼓内表面覆盖过滤介质。加入转鼓的悬浮液随转鼓一同旋转产生巨大的离心压力,在压力作用下,悬浮液中的液体流经过滤介质和转鼓壁上的孔甩出,固体被截留在过滤介质表面,从而实现固体与液体的分离。悬浮液在转鼓中产生的离心力为重力的千百倍,使过滤过程得以强化,加快过滤速度,获得含湿量较低的滤渣。固体颗粒大于0.01毫米的悬浮液一般可用过滤离心机过滤。
2.5 浓缩真空蒸馏技术装置
日本Telnite石油公司的浓缩真空蒸馏装置主要用于钻井废弃液体的浓缩处置,它主要由钛合金盘管、热交换器、真空负压反应釜、循环泵几个部分构成。
由于浓缩真空蒸馏装置利用了高原反应原理,在真空负压状态下进行热蒸馏,温度不需要达到正常压力下水的沸点。比起传统蒸馏设备,大大降低了能耗成本。
钻井废弃液体固相含量很高,进入该装置的废液,首先需要通过化学分离处置,再经过自然沉降,将固相物的含量降低到10%左右,才能进入浓缩真空蒸馏装置进行蒸馏。得到的蒸馏水经过净化处置,回收至井场再利用。
3 各种钻井固废分离技术装备适用性及优缺点分析
3.1 离心分离技术装备
(1)适用范围:适用存在一定密度差的水基钻屑的脱水减量及含油钻屑的脱油分离,但不适用于掏泥浆罐和处理水产生的渣泥及废弃泥浆等钻井固废的脱水减量分离。
(2)主要优点:
①分离出的液相主要是钻井液,由于脱水减量时没有添加化学脱稳剂,脱除液不影响再配置泥浆性能,可重复利用。
②设备少且操作简单。
③脱液时不需添加化学脱稳剂。
④脱除固相含固率较高。
⑤设备占地面积少。
(3)主要缺点:运行噪音大,能耗高。
3.2 压滤技术装备
(1)适用范围:带式压滤脱水技术装备主要适用于不含硬质固相的钻井固废的脱水减量分离,如掏泥浆罐和处理废水产生的渣泥、废弃泥浆等固废的脱水减量分离,但不适合于钻屑的脱水减量分离;板框式和叠式压滤脱水技术装备适合于所有钻井固废的固液脱水分离。
(2)主要优点:
①脱除的泥饼含固率高、含水率低。
②固废减量化率高。
③脱除的液相中固相含量少,可回用作为压滤设备的反冲洗水。
(3)主要缺点:
①配置化学脱稳处理剂配制设备、处理剂加药系统设备等,配套设备多。
②设备占地面积大。
③设备操作维修复杂。
④由于钻井固废性质变化波动大,脱稳和絮凝条件较难控制,对操作人员的素质要求较高。
⑤反冲洗用水量大、能耗高。
⑥由于需预先加入化学脱稳处理剂对固废进行脱稳,压滤水中含有化学脱稳剂成分,如再利用来复配泥浆,有可能会对泥浆性能造成影响。
3.3 过滤技术装备
(1)适用范围:
①离心过滤脱水技术装备适用于所有钻井固废的脱水减量分离。
②真空过滤脱水和加压过滤脱水技术装备适用于掏泥浆罐及处理水产生的渣泥和废弃泥浆的脱水减量分离。
③振动筛脱水技术装备主要适用于钻屑的脱水减量分离,但不适用于废掏泥浆罐及处理水产生的渣泥和废弃泥浆的脱水减量分离。
④干化床式和砂滤床式技术适用于所有钻井固废的脱水减量分离,特别适用于风大干旱,雨水少,日照时间长的西北地区。
⑤直接过滤布技术装备所有适用于所有钻井固废的脱水减量分离,特别适用于掏泥浆罐和处理水产生的渣泥及废弃泥浆的脱水减量分离,但实际应用案例较少。
(2)主要优点:
①此类技术装备多数要求不高,设备少操作简单。
②脱水减量时不需添加化学脱稳剂。
③脱出液可直接用于调配泥浆,由于其不含化学脱稳剂成分,因此不会对泥浆性能造成影响,并且其含有一定泥浆处理剂成分,还可减少泥浆处理剂的使用量。
④设备占地面积少,特别是直接过滤布技术、振动筛脱水技术、真空和加压过滤脱水技术。
⑤一些技术装备可实现较高的固废减量,固废含水率低,如真空和加压过滤脱水技术。
(3)主要缺点:
①多数技术装备脱出的固相含水率较高。
②干化床式和砂滤床式技术实现固废固液分离时间长,占地面积大,使用区域受限。
③真空和加压过滤技术装备操作要求较高。
④离心过滤脱水技术装备通常需添加化学脱稳剂,脱出液再利用于配置泥浆可能会对其性能造成影响。
4 结语
“减量化、无害化和资源化”是钻井固废处置的三原则。钻井固废减量化措施是钻井固废处置中重要的环节。而固废分离技术装备是减量化的关键,由于油气勘探钻井作业的特殊性,不仅造成钻井固废产生量波动大,同时造成其来源组分复杂且差异性大等特点,决定了只有针对性组合实施各种减量化技术装备措施,才能获得较佳的固废减量化效果,才能为实现固废的无害化、资源化和处置的经济性、环境安全性创造条件。