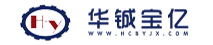
1 概述
随着现代炼油技术的改进,燃油的品质发生了急剧变化,其运动粘度、密度、油渣含量、乳化程度等因素都大大提高,这对燃油净化系统中的关键设备——碟式分离机及系统设计要求更高,并且由于燃油品质的下降,尤其是含硫量的增加,柴油机在运行过程中不同程度地影响了滑油的清洁度。为满足现代燃油的要求,离心机制造厂家都在该领域进行了不同程度的探索。
2 碟式分离机的工作原理及结构
2.1 工作原理
互不相溶的液-液或液-液-固在强大的离心力场中,根据其密度的差异进行离心分离。分离出的物料通过一定的机械结构分别导出机身外。
2.2 结构
碟式分离机主要由电机、水平轴、垂直轴、配水装置、转鼓、进出装置、测连装置、刹车装置等部件组成。其中转鼓是该机的核心,物料的分离即在该区域完成。
根据转鼓的排渣方式分为人工排渣和环阀排渣,其中环阀排渣又分为部分排渣和全部排渣。
部排:离心机在排渣过程中把转鼓中的部分积渣和水排出机外。其特点是:排渣过程中不停止进料、不损失物料,适用于含渣量较高(其含渣质量比在0.1%~2%之间),排渣频繁的场合。
全排:离心机在排渣过程中把转鼓中所有物料包括油、水、渣全部排出机外。其特点是排渣过程中停止进料,并且损失一部分油料,适用于含渣量较低(其含渣质量百分比小于0.1%),排渣次数较少的场合。
3 燃油离心机及系统设计
3.1 燃油离心机的主要设计参数
处理密度:991kg/m³/15℃
处理运动粘度:380cst/50℃
排渣方式:部排
净油输出方式:向心泵
净油输出压力:<0.4MPa
分离性能(经一级分离)分水效率≥70%,分杂效率≥65%
在燃油离心机的设计过程中,原先的机带齿轮泵改成了独立供油泵,分离后的物料出口方式由敞开式改为由向心泵压力输出;转鼓部件的液压设计计算全部按密度991kg/m³/15℃进行;油水界面移至碟片大端外侧,以取得较佳分离效果。
通过以上改进,离心机在燃油净化处理上取得了长足进步,经工厂517cst/50℃重油试验以及用户长期使用,均达到了设计指标。
3.2 燃油离心机的系统设计
为满足无人机舱操作要求,提高机器运行可靠性,对燃油离心机及整个燃油净化系统进行了程序控制。离心机的操作实现了自动化,并在整个系统中设置了温度恒定系统、高低温、高低压、不排渣报警等功能。
在系统的设计过程中应注意以下两点:
(1)为避免水在油中乳化,平稳和顺利输送是很重要的,为此在分离前必须避免节流。但在以前的设计中,输油泵往往是离心机机带的,其流量控制是靠吸入口前的节流阀来进行的。这样极易引起水在油中乳化和粒子细化,影响分离效果,这样的设计已不再被推荐,机带齿轮泵已被取消,取而代之是独立正排量螺杆泵或齿轮泵,并且增加流量恒定装置使得多余流量回流到沉淀柜。这样泵始终在它的较佳流率状态下运行,泵的增压室始终充满着燃油,吸入端不存在节流现象。
(2)分离温度控制。温度直接影响到燃油的运动粘度、密度,从而影响到分离界面。燃油较佳的分离温度应为98℃。此时,油和水之间存在较大的密度差。为保持恒定的分离温度,需选用精度为±2℃的温度控制器。
4 滑油离心机的设计
4.1 滑油离心机的主要设计参数
排渣方式:全排
净油输出方式:向心泵
净油输出压力:≤0.4MPa
分离性能(经一级分离)分水效率≥85%,分杂效率≥70%
滑油消耗:≤1.2L/h
滑油离心机的设计和燃油离心机基本相同,主要不同点在于排渣方式的不同,滑油离心机的排渣方式采用了全排结构。
4.2 滑油系统设计
滑油的处理较燃油来说简单些,基本引用燃油的净化系统,只不过是一些工艺参数的调整以及离心机的程序运作稍有不同而已,在此不再叙述。
5 燃油、滑油离心机的选型
燃油、滑油离心机的选型主要集中在排渣方式上。由于燃油含杂量高,排渣频繁,故选用部排系列的离心机,而滑油的杂质含量较低,排渣次数较少,故选用全排系列离心机。
如果在选型上两者颠倒,将会产生什么样的效果呢?首先如果选用全排离心机用于燃油净化系统中,分离性能应不受影响,由于含渣量的限制,排渣频繁,损失较大,且分离效率不高。如果部排离心机用于滑油净化系统中,从表面上看似乎更加合理,因为部排离心机用于含渣量小的滑油中分离更加轻松。可是不能忽视一个问题,那就是滑油的乳化,由于滑油净化系统的循环油柜较大,在操作产生失误时或机器出现故障时,加入的赶油水容易混入净油中,进入循环油柜,引起全柜油乳化。而全排离心机在上述问题产生时,加入的赶油水始终进入不了净油中。因此滑油选用全排离心机更加合适。
6 结语
燃油、滑油离心机及其自动控制系统经多套电站运行,证明离心机运行平稳,分离效果良好。自动控制系统灵敏、正确、可靠,完全满足现代燃油、滑油净化要求,保证柴油机安全可靠运行。