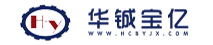
碟式离心分离机由于具有处理量大、分离效率高、分离效果好、可以连续生产等优点,在油脂精炼加工中得到越来越广泛的应用。在普通的油脂连续精炼中,碟式离心分离机主要用于油脂的脱胶、脱皂、脱水等工艺过程。在混合油连续精炼中,考虑到混合油易乳化、油皂比重差大等特性,混合油连续精炼一般不安排水化脱胶及水洗除皂工艺过程,只需安排中和脱酸过程。因此,碟式离心分离机在混合油连续精炼中主要用于脱皂,且性能好的离心机只需一次脱皂即能达到工艺要求。
1 碟式离心分离机的基本结构
应用于混合油精炼的碟式离心分离机,由于是在有溶剂存在的环境中运行,因此,对其防爆、防泄漏、防静电等方面的要求都非常严格。为了适应这种要求,相对一般运行环境而言,其结构必须作一些特殊的改进,这些改进一般包括:使用防爆型电动机及延时降压起动技术,去除常规的摩擦联轴器,采用机械密封式进出料装置。此外,考虑到防溶剂泄漏的可行性,一般采用人工除渣型转鼓为好,而且转鼓上可以不带有任何型式的冲洗水装置。
2 碟式离心分离机的基本分离操作原理
碟式离心分离机专用于比重差较小的不同相混合流质物料的分离,其中,比重较小的物料称为轻相,比重较大的物料称为重相。碟式离心机的分离工作原理可以简单解释为:在高速旋转的转鼓中存在强大的离心力场,进入转鼓并随着转鼓高速旋转的轻重相物料,由于存在比重差,在同一离心力场中受到的离心力并不完全相等,由此产生“离心压差”,并导致轻重相分别走向碟片的内外缘,直至完全分离。
我们把转鼓中轻重相开始互相分离的环形圆柱面叫做轻重相分离界面,简称界面。一般情况下,碟式离心机的转鼓结构在设计时,首先假定一标准液料,该标准液料的流量、粘度、温度、比重及其轻重相含量比例等参数在可控范围内都是恒定的,然后再设定一组均匀分布于碟片上的进料孔(进料孔可以为圆形或长圆形,所有的进料孔均匀分布在同一圆柱面上),使从该进料孔位置开始,轻相和重相通过碟片间隙分别到达碟片的内缘和外缘所需的时间一样长。这时,所有碟片上的进料孔中心点所围成的圆柱面就是理想分离界面。以理想分离界面为基础,设定轻重相出口流道在转鼓中的口径,使在离心力场下实际分离界面位置刚好落在理想分离界面上,此时的分离状态就是理想工作状态。
由于实际工作中待分离物料和标准液料总存在一些差异,实际的工作界面很少能正好落在理想分离界面上。因此,根据工作需要,就有必要通过外部操作来改变工作界面的位置,使其尽可能接近理想界面,以便达到较佳的分离效果。改变工作界面的方法一般有以下两种:一是通过改变轻重相出口流道在转鼓中的口径来实现;二是通过改变轻重相出口的压力(即操作背压)来实现。
当转鼓正在高速旋转时,要随时改变轻重相出口流道在转鼓中的口径是相当困难的,但轻重相出口背压却可以比较方便地随时进行调整。因此,一般情况下,重相出口流道在转鼓中的口径处都设计成一系列不同口径的可以拆卸的活动环(俗称比重环,比重环可以跟机械密封的动环做成一体,也可以单独分别设计;当然,轻相出口流道上也可以有类似的活动环),而轻相出口流道在转鼓外侧设计有可以调节出口压力(即轻相出口背压)的阀门装置。
离心机操作调整时,先选择一个比较合适的重相比重环,使工作界面落在理论界面(一般即为碟片组进料孔中心位置)附近。虽然实际工作界面位置很难直接观察到,但完全可以通过观察轻重相物料的分离状态来大致判断工作界面的位置。然后再通过调节轻相出口背压来微调工作界面位置,以达到预期的分离效果。
具体来讲,若重相比重环口径减小,则工作接线位置向碟片内缘靠拢(即内移),重相行程将相应加长,重相中的轻相含量相应减少;而轻相行程则相对变短,轻相中的重相含量就相应增多。就油皂分离而言,这时的情况就是皂脚含油减少但油中含皂增多,油色逐渐变浑浊。反之,若重相比重环口径增大,则工作界面向碟片外缘靠拢(即外移),重相行程相对变短,重相中的轻相含量相应增多;而轻相行程则相对加长,轻相中的重相含量就相应减少。就油皂分离而言,这时的情况就是油色变清,但皂脚含油增多。
另一方面,若减小轻相出口背压,则工作界面内移,其效果与减小重相比重环口径一致;而如果增大轻相出口背压,则工作界面外移,其效果与增大重相比重环口径一致。
3 实际操作中应注意的几个问题
3.1 背压及流量的调整
由于混合油的特性与不含溶剂的油脂的特性差别很大,因此,这两者对离心机的操作要求亦不尽相同。
3.1.1 背压的调整
在整个离心机工作周期中,轻相出口背压的调整呈现这样的规律,即从0慢慢调大,然后再慢慢调小,直至正常分离所需的数值,此后在整个工作过程中,背压又渐渐缓慢地不断提高,直到结束一个工作周期。
之所以如此,这是因为水的比重远比含有溶剂的皂脚大得多,因此,在同一离心力场下(即在同样转速的同一转鼓中),要使水从转鼓中流出,所需的轻相出口背压比使皂脚流出所需的轻相出口背压要大得多(这个背压的具体数值与混合油的粘度、比重、流量以及比重环口径大小等参数有关)。在实际操作中,当混合油从轻相流道流出时,有时轻相出口背压可超过0.75MPa,而有时则需把轻相出口背压调到不足0.15MPa。
进入正常分离状态后,随着分离时间的延续,皂脚中注入粕粒、泥渣等比重比较大的颗粒慢慢在转鼓内壁及整个重相流道上沉积下来,重相流道阻力随之慢慢相应增大,为了平衡这个阻力,所需的轻相出口背压也相应慢慢增加,直到结束一个工作周期为止。
3.1.2 流量的调整
刚开始进料时,混合油流量一般调到额定流量的1/2~2/3即可,等通过轻相出口背压的调节使分离效果达到要求后,再逐渐把进料流量调大,同时,注意调节轻相出口欧背压以保持分离效果。
如果一开始进料就把流量调大,往往欲速则不达。在实际开机操作中,有时也会出现这样一种情况,即当进料流量达到某一数值后,轻相变得较浑浊,但轻相出口背压刚一调高,重相皂脚含油即明显增加,而轻相混合油中含皂状况却改变不大,这就意味着实际的流量已超过了分离机的处理能力,此时应调小进料流量来解决。
3.1.3 背压与流量的关系
我们从操作中知道轻相出口背压与混合油流量的关系非常密切。其实,这两者之间的关系可以用能量守恒定律来解释。在这里,能量主要是在动能(表现为混合油流量)和势能(表现为轻相出口背压)之间进行转换,在同样条件下(即在同一离心力场中),轻相出口背压越大,则混合油流量就越小;反之,轻相出口背压越小,则混合油流量就越大。
因此,从经济角度来看,在分离效果达到要求的前提下,轻相出口背压应该尽可能调小,以便尽可能相应增大离心机的处理量。
当然,正常分离时轻相出口背压太小也不好,因为背压太小时,对皂脚中含油的调整幅度将非常有限,甚至有可能对皂脚含油完全失控。反之,加入正常分离时所需的轻相出口背压调得太大,如超过0.45MPa,虽然这时分离效果很好控制,但这是以牺牲处理量为前提的,也不是很经济的办法。一般情况下,轻相出口背压在正常分离时应以保持在0.20MPa左右为宜。
3.2 冲洗水的使用
在普通的油脂连续精炼脱皂工艺过程中,为了更有效地把皂脚及沉渣从离心机转鼓中及时地排出机外,往往通过专门的装置往转鼓中注入所谓的冲洗水。由于水的比重比油重且与皂脚比重相仿,这部分工艺用水进入转鼓后即沿着转鼓内壁经重相流道流出,在此过程中,皂脚被稀释,粘度降低,更易于排出转鼓。而沉积于转鼓内壁的残渣颗粒亦会被水流夹带冲走,这对延长离心机正常分离工作周期及有效保持分离效果无疑都是非常有利的。
在混合油连续精炼中,由于有溶剂的存在,含有溶剂的皂脚的理化特性与不含有溶剂时的特性具有很大的区别。这时在离心机转鼓中,水的比重不仅远远大于混合油的比重,且亦会比含有溶剂的皂脚的比重要大得多。另外,由于皂脚含有溶剂,这就使得皂脚与水的互溶性变得很差。此时,一旦有水进入转鼓中,必须形成油-皂-水三相物料,使转鼓中原有的油-皂两相物料的稳定分离状态遭到破坏,从而使离心机不能正常工作。
因此,一般情况下,碟式离心分离机在进行混合油连续精炼时无需使用冲洗水,只有在结束一个分离操作周期时,在停止进料后,方可以考虑注入冲洗水并相应减除轻相出口背压,以便把转鼓中残留的混合油更多地“撤”出来,并把残余的皂脚冲出,减轻清洗转鼓的负担。
3.3 基本的维护保养知识
作为离心机操作人员,首先必须熟读离心机的操作使用说明书,并严格执行说明书的各项要求。
事实上,在此我们仅就一般性的问题作了讨论,在混合油连续精炼中应用碟式离心分离机,涉及到的还远远不止这些。但是,了解了这些常识,或许总会更好地促进我们做好许多实际工作,而这正是本文写作的初衷。