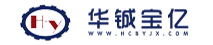
1 卧式螺旋卸料沉降离心机的结构、原理和工艺
1.1 结构
离心机主要由转鼓、螺旋输送器、大小端盖、左右轴承座、差速器、电机传动部件、机座、机罩、电气控制箱等部件组成。
1.2 工作原理
离心机的转鼓与螺旋输送器启动到全速后,由于旋转产生一个强大的离心力场,悬浮液物料由进料管加入螺旋内,物料通过螺旋筒体内的出料孔进入转鼓,在离心力场的作用下,比重较大的固相物料沉附到转鼓壁上,形成一个环形的固相层,螺旋输送器在差速器的作用下,使螺旋与转鼓产生一个恒定的差转速,将脱水后的固相沉渣从圆锥转鼓的小端出渣口推出,而比重轻的澄清液从圆柱端的溢流口流出,如此连续不断地工作,达到连续分离的目的。
1.3 差转速的计算
差转速=(转鼓转速-差速器辅皮带轮转速)/差速器速比
1.4 工艺参数的确定
(1)根据悬浮液物料的特性。物料中固相粒子越大,则越易分离,固相颗粒大小不一时,小粒子固相决定其分离效果,该机一般能除去3~5μm以上的固相粒子,固相粒子特别细小时,则不会沉降分离出来,而随澄清液一起排出。分离效果取决于物料的固相粒子的分布,3~5μm以上粒子越多,分离效果越好,反之分离效果越差。液相粘度越小越易分离,液相粘度越高时,澄清液中夹带固相增多,分离效果变差,这时可提高物料温度,降低粘度,来改善分离效果,一般情况进料温度不宜大于95℃。
(2)进料流量(即处理量)的选择。从分离效果的角度上,进料流量越小,物料在转鼓内轴向流速越小,则物料在转鼓内的停留时间越长,则分离效果越好。随着进料量增大,轴向流量增加,物料在转鼓内停留时间减小,分离效果变差,离心机的进料量还受螺旋的排渣能力限制。进料量过大,被分离出的沉渣将无法及时排出而引起转鼓的堵料,所以在使用时应按物料特性分离要求和物料的含固量大小,选择适宜的进料流量。
(3)溢流调节板直径的选择。转鼓的溢流直径小,则沉降区变长,干燥区变短,固相沉渣的含水率增高,澄清液变清,液相液体的分离效果较好。反之溢流直径越大,沉渣越干,液相液体分离效果变差。在实际使用时,应根据对固相沉渣含湿率和液相含固率的要求,通过操作实验来合理选择溢流直径。溢流直径的大小,可通过改变转鼓大端盖的一组溢流板来调整。
(4)转鼓转速的确定。转鼓的转速越高,则分离因数越大,通常分离效果也越好。这里要特别注意:每一种物料都有其合适的分离因数,过大了分离效果提高并不明显,有时还下降,转速增高随之会带来离心机的振动和噪声的增大,电机负荷增大,轴承寿命下降。选用过高的转速并不经济,一般在满足分离工艺要求的前提下,尽量选用较低的转速作为工作转速,转速的调整可通过变频器来实现。
1.5 主要结构特点
(1)转鼓部件由大小端盖、锥形转鼓、柱形转鼓等装配而成,大端盖装有可以调换的溢流挡板,以此获得不同的溢池深度,从而改变转鼓内的液体容积和沉降区与干燥区的长度。转鼓小端均布若干个出渣口,出渣通道内衬以可更换硬质合金或陶瓷,以提高磨损性,沉渣在离心力作用下从出渣口甩出,转鼓内衬有筋条,以减少沉渣对转鼓内壁的磨损。转鼓锥筒体表面上有环状凸缘与机壳挡板组成迷宫密封,以阻止分离液在高速运动下形成的水雾渗入排渣室内。
(2)螺旋输送器。该部件由螺旋叶片、筒体、大小端盖等组成。螺旋叶片按设计的螺距焊在中心管外表面,叶片圆周和推料面喷有耐磨层或镶有耐磨硬质合金块,以防止螺旋叶片过快磨损,提高了螺旋整体的使用寿命。在螺旋筒体适当部位均布开有圆形出料口,出料口位置呈螺旋线排列。与物料接触处都喷有硬质合金层。进料通道根据进料实际情况设计,使物料能均匀进入转鼓内部,不会产生死区,且能减少对转鼓内已沉降沉渣的冲刷。
(3)螺旋辅传动部分装有扭矩传感器。设定好扭矩传感器,即可实现机器在恒扭矩或变差速状态下运行,输料扭矩发生变化,该变化由扭矩传感器传递给控制器,改变辅助电机输入速度,从而达到改变差转速的功能。
(4)电气系统,包括电气联锁装置、扭矩过载自动报警装置、振动传感器装置、联锁控制开关装置、有紧急停车开关装置。
2 卧式螺旋卸料沉降离心机在尾矿处理中的应用实例
样品分析方法和固相回收率的计算:卧式沉降离心机作为固、液分离设备,进行固体和液体的分离,所以在测试分析离心机进料浓度和分离液的含固率时,必须要完全去除料浆和分离液中的溶解物质。分析时要均匀应用定量滤纸进行过滤,同时还要在过滤过程中,用蒸馏水洗净漏斗中样品里的可溶物质,再衡温称量,否则会导致测试数据不准确。
经济效益:用卧式沉降离心机处理尾矿废水的优点是:处理效果好,处理量大,全封闭进行,现场清洁无污染,絮凝剂、清洗水用量少,人工费用低,日常运行成本低廉,设备布局紧凑,占地面积小,尾矿综合利用,变废为宝。既保护了资源,又充分利用了资源,同时还净化了环境,一举多得。
3 结语
卧式螺旋卸料沉降离心机的种类在随着科技的发展,不断地多样化,性能也越来越优越,在尾矿废水处理中必然有着良好的应用前景。