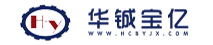
攀钢煤化工厂二期煤气净化系统采用AS循环脱硫洗氨工艺,由于剩余氨水带油和悬浮物,造成系统换热器、洗涤塔、脱酸蒸氨塔堵塞,影响煤气净化效果。为此,通过离心分离技术对剩余氨水进行了油水分离,由试验的结果表明,离心分离能使油和水得到很好的分离,基本上能解决后续的系统堵塞问题。
1 离心分离技术除油原理
1.1 剩余氨水中焦油的存在形态分析
剩余氨水是一个含有乳化液滴和胶体的复杂体系,其中所含焦油不溶于水,焦油是一种十分复杂的多组份混合物,特别是其中的有机物如酚类、吡啶碱等的分子结构中既含有亲油基,又含有亲水基,在细小的油滴表面上会形成亲油基向油滴内部、亲水基向水侧的定向排列,而将油滴保护起来。因此,在油滴之间的表面同性电荷相互排斥,很难相互碰撞凝聚成大油滴,焦油中的酚类,吡啶碱类这些物质在氨水中起着乳化剂的作用。焦炉的集气管用循环氨水喷洒冷却煤气,以及高压氨水喷洒无烟装煤过程中,会有焦、煤粉以及石墨粉尘进入液相。克劳斯尾气经尾气冷却器也会带入细小的硫粉等进入液相。这些固体微粒有些是亲水性的(或有亲水表面区),有些是亲油性的(或有亲油表面区),常常位于油与水的界面处,固体微粒进入剩余氨水后,亲水性微粒的大部分处于水层中,而在油滴侧则要小得多,在油滴表面就形成了保护层,保护着油滴不能聚集分离,也起到乳化剂的作用。从以上分析不难看出,含焦油的剩余氨水中存在着形成乳化液和胶体的必要条件。而液体在泵中的搅拌及在管路中的湍流运动,则是形成乳化液和胶体的充分条件。由此可见,剩余氨水中的焦油除了悬浮部分外,另外部分是与氨水呈溶融状态存在的。
静止水层中,油滴的沉淀速度可用斯托克斯定律计算。计算结果表明:粒径大于3.04μm的油滴在48小时内从液面沉淀距离超过10cm;而小于3.04μm粒径的油滴,尚在液面下10cm的高度范围内。含油滴粒径小于3.04μm的水属于乳化液,经48小时沉淀后,呈乳化状态的油仍然很多,所占比例为32.0%,乳化状油与剩余氨水呈互溶状态,在实际生产中它们堵塞换热器和蒸氨塔的可能性不大。堵塞换热器和塔的主要是悬浮在剩余氨水中的悬浮物。因为悬浮物与剩余氨水不互溶,所以在剩余氨水流动的过程中,悬浮物就容易附在设备的管壁上,时间一长就堵塞设备。
通过对剩余氨水进行静置沉降实验,分别静置2h、4h、6h、8h、10h、12h、14h、16h、20h、24h、30h、36h、42h、48h,测其含油量,从实验结果可以看出,随着时间的延长,剩余氨水的除油效率提高,但超过8h后,曲线变得平缓。因此,剩余氨水仅靠静置沉淀48h仍然不能把焦油彻底除去。
1.2 离心分离原理
离心分离除油技术是目前一种应用较为广泛、技术成熟的油水处理技术。通常需被分离的物料按理论说,只要有密度差,均可以通过自然沉降法将其分开,但是分离后的澄清度在很大程度上是由时间和容器的沉降面积而定。而离心机的工作原理,则是利用其高速旋转所产生的几千倍于地球重力加速度的离心作用力,和相对大的碟片沉降面积的情况下,使被分离的物料在极短的时间内分离开来。即所谓的高分离因数、极大的沉降面积,依靠被分离物料——即剩余氨水、焦油和固体颗粒之间的密度差在高分离因数、极大的沉降面积作用下,使剩余氨水、焦油和固体颗粒同时分离开来。
根据单一颗粒离心分离公式,可知,该物料在一定的圆周加速度和一定的旋转半径作用下,其分离沉降速度就可被确定。而另外部分数据是由物料本身决定。
如果要分离无数多的颗粒(无论是固体颗粒,还是液体的液滴),其离心分离的原理公式需引入沉降面积的因素。物料分离的效果好坏与物料本身的参数如密度、颗粒、粘度及流量有关,同时也和离心机的参数相关,即转速、转鼓直径、碟片大小、碟片顶部的半夹角、碟片的片数(也就是碟片之间的间隙大小)等有关。
无论是固体颗粒,还是液体液滴,它们与轻相液体的分离,均在大于5000倍地球重力加速度的离心力作用下,在碟片离心机中,上百个碟片间隙不足0.5毫米的通道中进行分离。
选择适当大小的碟片离心机,适当的碟片离心机转速以及适当大小的碟片间隙,在适当的流量及适当的温度下,就可以将具有一定密度差的物料分离得足够好。
2 试验过程
2.1 试验主要设备及工作流程
试验所选离心机为瑞典阿法拉伐公司的生产型号为MAPX207碟片离心机。该碟片离心机具有间歇排渣功能,适合分离轻相多,重相少的流体物料。
2.2 试验方案
攀钢煤化工厂回收二系大氨水泵旁,安装了阿法拉伐的MAP×207离心机,将原来剩余氨水放空管处安装了一个三通管,一个口作为离心机物料的进料口,另一个口用阀门连接,保证能正常取样,出口直接接入酚水道。重油出口也直接接入酚水道,排渣处用一个高10cm左右的废酚桶底接住。冷却水和电均在回收二大氨水泵旁边接。进、出离心机的物料稳定后10分钟开始对进液、出液同时取样,连取三个样品。样品化验数据应当以算术平均值为准。
3 结果与讨论
3.1 悬浮物的讨论
在试验初期,能清楚看见剩余氨水进离心机前和出离心机后处的剩余氨水颜色差异非常大。但是为什么看上去很透亮的氨水液中仍有那么高的含油数值?从静置层降的理论分析中获知,剩余氨水中有部分与氨水的密度比较接近的轻油,用分离因数在5000-6000G的碟片离心机很难将其分离干净,除非采用分离因数在12000G以上的高速碟片离心机。要解决的主要问题是系统的堵塞,就涉及到悬浮物含量的问题。离心前的悬浮物含量(9854mg/l)是用离心机后的悬浮物含量(29mg/l)的340倍。现有工艺条件下除油后的剩余氨水的悬浮物平均值为293.8mg/l,是用离心机后的10倍。
3.2 H2S富液出口处的试验讨论
进入离心机前H2S富液的油平均含量为0.6g/l,离心后H2S富液的油平均含量为0.385g/l,油的去除率为35.8%。进入离心机前H2S富液的悬浮物平均含量为125.5mg/l,离心后的H2S富液悬浮物平均含量为33.5mg/l,悬浮物的去除率为73.3%。
4 结论
通过以上试验数据分析,得出以下结论:
(1)堵塞换热器、蒸氨设备的主要是剩余氨水中的悬浮物和重油。
(2)用离心分离技术能够去除剩余氨水中堵塞设备的悬浮物和重油,离心分离对剩余氨水进行除油,去除率为80.5%。比现有工艺条件下的剩余氨水含油下降了55%。
(3)用碟片离心机去除悬浮物,能够使悬浮物去除到29mg/l,比进离心机前的9854mg/l,去除率为99.7%。现有工艺条件下除油后的剩余氨水的悬浮物平均值为293.8mg/l,是用离心机后的10倍。
(4)在H2S富液出口可以用离心机来除油及悬浮物。油含量的去除率为35.8%,悬浮物的去除率为73.3%。