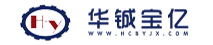
油脂精炼中使用的离心分离机主要从国外进口的两大品牌:韦斯伐里亚和阿尔法拉伐。虽然国产也有两大品牌相似产品,但离心机是油脂精炼的核心设备,其功能与质量对生产效率和产品质量起决定性作用,故目前国内油脂生产企业仍以选用国外的 两个品牌为主。一般国内企业订购成套设备包括机体和控制柜,使用几年后一旦控制系统发生故障,往往需要国外生产厂家派技术人员来国内技术服务,不便于操作与维护。
1 离心机工作原理介绍
油脂行业中使用的是沉降式离心机,用于分离难分离的物料(粘性液体与细小固体颗粒组成的悬浮液或密度相近的液体组成的乳浊液等)。碟式分离机以其结构紧凑,占地面积小,生产能力大等特点,因而在油脂加工行业的生产部门获得广泛应用,离心分离机是利用混合液(混浊液)中具有不同密度且互不相溶的轻、重液和固相,在离心力场中获得不同的沉降速度的原理,达到分离分层或使液体中固体颗粒沉降的目的。分离机中的碟式分离机是应用较广的沉降离心机。
碟式分离机是立式离心机,转鼓是离心机主要动作部件,位于立轴上端,由转鼓体、上分配器、下分配器等主要组件组成,通过传动装置由电动机驱动而高速旋转,高速旋转部件通过高精度的锥度配合与立轴相连获得动力,立轴部分是传递动力,并装有增速齿轮(小螺旋齿轮),横轴是将电机的动力传递到立轴和转鼓的主要部件,由电机、联轴器、压力耦合器、传动轴、大螺旋齿轮和刹车轮等零件组成,起到过载保护作用(液力耦合器)大螺旋齿轮在运转中将润滑油飞溅到各传动轴承,使轴承润滑,当油温超过110℃时,横轴的液力耦合器上的易溶合金保护塞自动溶化,使分离机失去源动力。转鼓内有一组互相套叠在一起的碟形零件——碟片,若干层由定距条间隔成碟片组,装于碟片与碟片之间留有很小的间隙。待分离物料由位于转鼓中心的进料管加入转鼓。下分配器的作用是使进入转鼓的悬浮液和冲洗液隔开,并将冲洗液引向转鼓壁,以稀释和冲走沉积在转鼓上的杂质。当混合液(混浊液)流过碟片之间的间隙时,固体颗粒在离心机作用下沿碟片下表面滑动而脱离碟片并积聚在转鼓内直径大的部位形成渣层,通过排渣机构(人工、连续、间隙)排出转鼓;轻相液体沿碟片上表面向转鼓中心运动,通过离心力从转鼓上部出液口排出转鼓;转鼓顶端装有向心泵,向心泵的作用是将液体旋转动能转化为压力排出机外。即借助于向心泵分别引出轻相和重相。被分离的物料在强大的离心力场作用下,经一组碟片束的分离间隔中,以碟片中性孔 为分界面,比重大的液体(重相)沿碟片壁向中心孔外运动,其中重渣积聚区,皂脚等则流向大的向心泵处。比重小的液体(轻相)沿碟片壁向内向上运动,汇聚到小的向心泵处,轻、重相分别由小向心泵和大向心泵输出。
离心机电控部分主要有启动电机、6只气动电磁阀(分别是密封水阀、排渣阀、冲水阀、活塞阀、注水阀、冷却水阀)。主要检测参数:启动电流、出口压力、振动幅度、液体流量及循环运行步序时间的设定与显示。
2 离心机的使用要点及控制方案
以韦斯伐里亚离心机的控制程序为例作详细说明。
(1)分离机采用液力耦合器和一对螺旋齿轮传动,利用液体传递动力,既增速平稳又能进行过载保护。滑动活塞的排渣动作由程序控制,一般电机功率为15~20kW,可采用Y-△或变频器启动,高速约达6600r/min,启动电机一般为15~20kW,由于分离机的高速运行,启动到正常运行,需要时间30s以上且启动电流大,启动时出口压力检测不投入联锁保护和报警,启动时间在上位机上可设定,并显示运行时间。启动过程中检测启动电流,设定启动电流报警值,以防止飞车,做好应急处理程序。
(2)启动准备:
①加润滑油到油箱内。
②检查操作水压力,打开手动操作水供水阀。
③启动电机电流不超过65A,全速后不超过30A。启动时间一般设定5min,达到全速后,指示盘65r/min,启动过程控制系统会自动检测电流、温度、振幅等状态参数,如果不满足正常运行条件,则报警或停机。如果满足则再加速至额定转速,具备正式投入工作状态。正常运行按生产周期时序图要求由PLC程序控制,正常生产周期是自动循环过程,各阀控制根据系统时序图动作,动作的时间由计算机界面设定并显示运行参数。
(3)在画面上设置好时间参数。“启动时间”为电机的启动时间内不投入开阀和排渣,是电机的启动和检测过程的时间。“密封周期”、“密封时间”是密封水阀、注水阀间隔时间和打开时间,在排渣周期前进行的反复活塞注水保持密封水,以防止出水口漏油,在渣聚结区域还有部分污油聚结在此,加密封水后由于油密度比水轻而被排到此区域外,并封住出水口。注水阀也同时间断补水,置换出从油中分离的污水,由出水口排出机外。运行一定时间后进入排渣时间,可设置“排渣时间”大小,部分排渣时间包含在一个生产周期中,设定的“排渣周期”即进入部分排渣程序,这时打开冲水阀进行预先冲洗,同时打开活塞阀,利用气压推动活塞,保持一定水压,滑动活塞下移而打开离心机下部的排渣口。滑动活塞打开排渣口的时间不宜太短,应大于排渣阀的开启时间。预冲时间(可设定“预冲时间”)到后,打开排渣阀(“排渣时间”可设定),部分排渣阀打开的时间一般为1s,时间较短,打开排渣阀后进行排渣。排渣冲洗后进入“关闭延时时间”(可设定)计时,计时过程中密封时间到,密封水阀关闭。“关闭延时时间”2s后打开注满水阀进行注水,为下次排渣冲水用。“关闭延时时间”到后,关闭注满水阀和密封水阀。并冲水阀仍打开,直到并冲时间(可设定)到关闭。部分排渣打开的时间过程结束后,一个循环周期结束,又重新循环一个新的循环周期。
(4)下盒为排渣的主要通道,并设计有专用于拆装的小活塞、阀体的通孔。进水罩是用专分配操作水的不锈钢焊接壳体,通过与其连接管道排出机外。
(5)全排渣为手动操作,按下“全排”按钮,程序执行全排渣过程,阀的开启按全排渣时序执行,过程与部分排渣基本相同,只是排渣阀和注水阀开启的时间长些。全部排渣是手动操作,当“全排”按钮按下,进入全排渣的控制程序,各控制阀具体由上述时序图顺序控制。全排渣时离心机暂停进料,打开排渣冲水阀约10s,同时打开注满水阀和并冲水阀,这样冲洗强度大。排渣冲水阀关闭后打开密封水阀约5s,5s后同时关闭密封水阀和注满水阀,这时并冲水阀仍打开,直到并冲时间(可设定)到关闭。这时运行等待间隔时间,等待间隔时间结束后,即全部排渣程序结束,离心机恢复进料。全排渣是通过将转鼓内残渣、油脚等重相排出机外,由操作员间隔一定时间(一般半天或一天)进行一次全排渣。生产过程中可按下“部排”、“全排”按钮,随时执行手动的部分排渣和全部排渣操作。
(6)正常生产过程中PLC不断检测机器的状态参数,可通过各自模拟量画面,查看历史记录曲线,设置高低限值,当实际参数超限值,报警或转入待机状态。离心机再循环运行排渣周期,所有上述控制流程由PLC和计算机编制控制程序自动控制运行。动作的时间参数由计算机界面设定,同时计时运行时间,这样完全集成于总工艺流程,操作方便,显示直观。
控制系统硬件可采用西门子PLC模块,一般在大的油脂精炼整个系统配置一块数字量输入(DI)模块、一块数字量输出(DO)模块、一块模拟量输入模块(AI),电机和气动电磁阀由数字量按程序控制其开关。通过模拟量输入模块(AI)和各种模拟量变送器(在订购机器时选配)检测离心机的运行状态的参数:如电流、振幅等。调试时先不启动主电机,主要模拟运行各开关阀是否按时序要求运行正常,运行正常后可启动电机正式试运转。
3 结语
上述离心分离机控制程序的编写,能够克服单机设备单独操作的设置及操作不方便的缺点,同时可设置各种非正常状态的报警,随时掌握机器的运行参数,发现异常及时排除,在油脂精炼生产线中实际应用效果较好。