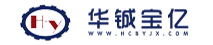
目前,市政污水处理厂处理的污泥为生化系统的剩余污泥,不含污油,大多采用带式压滤机,滤后污泥采用填埋处理。部分大中城市,市政污水场污泥产生量大,在带式压滤机脱水后,采用干化进一步降低含水率后再处置。随着环境污染治理力度的加大,对污水处理厂产生的污泥处置要求更加严格。因此,进一步降低污泥含水率、降低污泥处置费用是目前面临的新课题。
庆阳石化公司污水处理厂设计处理能力300t/h,污泥的组成为油泥、浮渣和剩余活性污泥,污泥处理采用污泥浓缩脱水+离心机脱水的方法,主要脱水设备有离心脱水机两台,一台为两相,处理量为5m³/h;一台为三相,处理量为10m³/h。在离心脱水过程中污泥含水率由99.8%降至60%~80%,减量效果良好,有效地降低了处置费用。但还可采取优化工艺参数、加强运行管理等措施,进一步降低含水率。
1 炼化企业污泥来源性质及污泥量
1.1 含油污泥的来源及性质如下:
污泥分类 | 罐底、池底油泥 | 一、二级气浮浮渣 | 生化池剩余污泥 | |
污泥来源 | 调节罐排泥 | 隔油池排泥 | ||
污泥原液性质 | 密度 | 1.001g/cm³ | 0.99g/cm³ | 1.005g/cm³ |
含水率 | 99.44% | 99.48% | 99.81% | |
浓缩沉降时间 | 8h | 18h | 10h | |
浓缩污泥性质 | 密度 | 1.002g/cm³ | 0.995-1.001g/cm³ | 1.008-1.01g/cm³ |
含水率 | 97.58% | 96.82% | 98.19% | |
含油率 | 5745.5mg/l | 1531.75mg/l | 0 | |
特点 | 含大量无机质和污油,相对密度大于1,易于自然沉降 | 含大量无机质和少量污油,含有大量气泡,沉降性能差 | 含大量有机质,含有病原菌和寄生虫卵,易腐化发臭。含水主要为细胞内含水,沉降性能好,含水率高 | |
处理方法 | 重力沉降浓缩,离心脱水,焚烧(外委) | 重力沉降浓缩,离心脱水,干化,焚烧 | 重力沉降浓缩,离心脱水 | |
去向 | 危废:焚烧,外委 | 危废:焚烧,外委 | 一般固废:堆肥,填埋 |
1.2 含油污泥量
污水厂设计处理水量7200m³/d,设计总进口污水悬浮物200-300mg/l,污泥产生量65.5m³/d,设计脱水后,油泥浮渣污泥量(含水率80%)为1.98m³/d,剩余活性污泥污泥量(含水率80%)为0.39m³/d,每天产生的污泥总量(含水率80%)为2.37m³/d。
在运行中发现,随着原油劣质化,污水中悬浮物、石油类、COD远高于设计指标,导致三泥产生量增至500m³/d,设计脱水后污泥量在10m³/d,两相离心脱水机,处理量为5m³/h;三相离心机脱水机,处理量为10m³/d。
2 主要工艺原理及流程
2.1 工艺流程
污泥分为油泥、浮渣和剩余活性污泥。油泥、浮渣污泥含水率高达99%~99.5%,活性污泥含水率约99.7%。排泥过程间断、不连续。油泥、浮渣重力流至油泥浮渣池,然后由油泥浮渣泵压力输送到污泥浓缩罐;来自生化池的剩余活性污泥进入活性污泥池,再经剩余污泥泵送入污泥浓缩罐,与油泥浮渣混合静置16小时后,分层切水,经浓缩后的污泥含水率约为97%~98%。浓缩后的污泥投加聚丙烯酰胺,机械搅拌混合反应。投加量为干基量1%~3%。经加药调质后的污泥,由污泥螺杆泵加压进入离心脱水机进行脱水,脱水干化后外委处置。分离后的污水和污油进入污水厂进行处理。
2.2 离心脱水机工艺原理
离心脱水机主要由转鼓、螺旋、差速系统、液位挡板、驱动系统和控制系统组成。
离心机利用固液两相的密度差在离心力作用下,以加快固相的沉降速度实现固液分离的目的。由三步相对独立的步骤完成:
(1)固体的沉降。物体高速旋转时受到离心加速度,不同密度的物体受到不同的离心力,且二者的差异随着转速的增大而增大,加快了沉降速度。
(2)固体的输送。由与转鼓相对运动的螺旋叶片推动。
(3)固体的去湿。固体在出口前离开液面,在离心力的作用下,固体间隙处的水被排出。
3 主要工艺及设备技术参数
3.1 脱水机进料性质
进料含固量:2%~5%wt;进料含油量:5%~30%wt;进料温度:20~60℃。
3.2 污泥脱水效果
脱水后泥饼含固率≥20%wt,分离液含固率(SS)≤0.20%wt,油相去除率:≥90%。
3.3 主要建构筑物
名称 | 数量 | 规格型号及主要参数 |
油泥浮渣池 | 1 | L×B×H=3m×4m×2m,有效水深:1.7m,有效容积:20.4m³,砼 |
剩余活性污泥池 | 1 | L×B×H=9.3m×5.3m×3.5m,有效容积:22m³,砼 |
污泥浓缩罐 | 3 | 浓缩罐:φ3.2×6m,3具,材质Q235B;有效水深:3.5m;污泥深:3m;有效容积:28m³;浓缩时间:10~20h;脱水前污泥含水率:99.5%,脱水后污泥含水率:98%;浓缩罐内设置蒸汽伴热管 |
污泥脱水提升池 | 1 | L×B×H=2m×4.4m×3.0m,有效容积:22m³,砼 |
污泥脱水间 | 1 | 平面20.7m×16.5m,砼 |
3.4 主要设备
名称 | 数量 | 规格型号及主要参数 |
三相离心脱水机 | 1 | Q=10m³/h,电机功率:2.25kW,材质:SUS304;污泥脱水后含水率:80% |
二相离心脱水机 | 1 | Q=5m³/h,电机功率:2.25kW,材质:SUS304;污泥脱水后含水率:80% |
离心脱水机进料泵 | 3 | 2开1备,Q=5m³/h,H=25m,N=1.1kW |
螺旋输送机 | 1 | 材质:SUS304,Q=3m³/h,与离心机配套 |
污泥斗 | 1 | 材质:SUS304,规格:10m³,2.0m×2.5m |
污泥脱水提升泵 | 2 | Q=5m³/h,H=20m,N=2.2kW,1用1备 |
油泥浮渣泵 | 2 | Q=5m³/h,H=20m,N=2.2kW,1用1备 |
剩余污泥泵 | 2 | Q=8m³/h,H=20m,N=4kW,1用1备 |
加药设备 | 2 | 200GFZP(全自动型),供粉量200ml/min,料斗容积40L,材质:SUS304,配液槽容积1.3m³,材质:SUS304 |
污泥脱水机反洗泵 | 2 | Q=30m³/h,H=38m,N=5.5kW |
4 与板框式污泥脱水机相比的优缺点
4.1 板框(滤带)式污泥该工艺的主要缺点:
(1)板框(滤带)式压滤机工作效率低,不能连续运行。
(2)板框(滤带)式压滤机不能进行油、水、泥三相分离,处理后的污泥含水率高,滤后水色度、悬浮物高且难以处理,严重影响污水处理系统的正常运行。
(3)不适用于含油污泥,滤布易被污油堵塞,仅适用于市政污泥处理。
(4)板框式压滤机是敞开式操作,占地面积大;设备运行时,各种有毒有害气体弥漫操作间,严重影响操作人员身体健康。
(5)滤布需定期清理,工作强度大,操作环境差。
4.2 离心脱水机的优点
(1)技术成熟可靠,可实现连续自动化操作,工作效率高。
(2)可进行油、水、泥三相分离,处理后污泥含水率低,可由97%降至60%~80%,分离后污泥含油、含水低,滤后水含固量低;处理后的产物可实现再利用和处理。
(3)用途广泛,适用于市政、炼厂等各种污泥的处理。
(4)污泥离心压滤机为全封闭式操作,占地面积小,改善了工作环境。
(5)离心机清洗采用清水反冲洗操作,工作强度小。
5 运行效果
5.1 处理水量
污水处理量:180~200m³/h。
5.2 处理效果
经取样监测,脱水机进料污泥含水率99.5%,脱水后污泥含水率达到80%~85%,分离液悬浮物浓度(SS)≤300~800mg/L。从数据分析,因多种因素造成离心脱水机未达到较佳运行工况,脱水后的污泥含固率未达到较佳值(20%~30%),分离液含固率较高。
6 存在问题及解决方法
6.1 存在问题
目前,在使用离心脱水机过程中,还存在以下问题:由于三泥配比、进料性质不稳定;因原油劣质化造成系统污泥产生量远大于设计值,重力沉降浓缩时间不够、操作不规范等因素造成脱水后污泥含水率高达80%~85%,且不稳定;滤后水含固率高,影响污水厂污水处理效果。脱水后污泥外委处置污泥费用高(2800元/吨),因此降低脱水后污泥含水率,进而降低污泥处置费用是当务之急。
6.2 分析原因
(1)目前离心机进料管线上缺少流量监测设备,污泥浓缩罐无搅拌机,三泥的配比、进料量、含水率稳定。
(2)离心机的进料的较佳温度控制在60~90℃,确保离心机进料的物料可分离特性保持连续稳定可靠。离心脱水机进料无温度控制措施,冬季受环境影响进料温度很低,影响离心机对物料的分离效果。
(3)离心机加药系统存在缺陷。离心机分离效果受药剂性能、加药浓度、配比、加药量等因素影响。目前该系统的配药采用人工手动加药粉,药剂浓度在量比上缺少有效的连续控制,加药流量也没能有效显示和控制,针对物料特性药剂没有筛选报告和说明,影响了离心机处理物料的效果。
(4)离心机操作运行和维护保养及管理不够完善,设备运行效能不高。
(5)污泥系统设计容积偏小。随着污泥量的增加,污泥浓缩罐容积偏小,造成重力沉降时间不够。浮渣泵、污泥脱水提升泵等流量偏小,制约着污泥处理系统的正常运行。
(6)运行参数未能调整到较佳工况。
6.3 解决方法
(1)在离心机进泥管线上加装流量计以便对进料量进行监控;在污泥浓缩罐增加搅拌机;调整进料配比以保证进料的连续均匀和稳定。
(2)在离心机的进料管线上加装蒸汽加热系统,控制进料温度在60-90℃,保证分离效果。
(3)完善加药设施的计量和自动控制系统;同时针对污泥性质对药剂进行试验筛选,保证加药的效果。
(4)对离心脱水机进行维护保养,保证设备性能正常;加强运行管理,保证脱水效果。
(5)重新核算污泥量,放大污泥系统设备,包括增加污泥浓缩罐、放大机泵流量和建构筑物容积,保证污泥浓缩时间。
(6)调整污泥脱水机运行参数到较佳工况。
(7)根据污水三泥的性质,将生化剩余污泥同油泥和浮渣区分开,分别进行处置,提高油泥的处理效率,较大限度地降低污泥含水率和含油量,达到缩短污泥干化时间,有效降低干化后的污泥含水率,降低处理成本。
7 结论
污泥离心脱水机性能可靠、分离效果好,但在使用过程中,药剂配比和进料温度的控制是关键。可通过优化工艺参数、强化运行管理等措施,使其运行达到较佳工况,进一步降低污泥含水率,从而降低污泥处理成本。
炼化企业含油污泥、剩余污泥处理设计时,可将含油污泥、剩余污泥的脱水处理系统分开设计,对脱水后的污泥分类处理,降低脱水后污泥的后续处理费用。
含油污泥处理的减量化、无害化及资源化还需进一步摸索和研究。