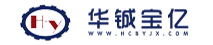
浙江巨化股份有限公司硫酸厂有两套硫酸生产系统,其中60kt/a装置采用水洗净化工艺,120kt/a装置采用酸洗净化工艺,两系统净化工序及其他生产装置产生的酸性污水经电石渣中和、沉降后送污水处理厂,经进一步处理后达标排放。电石渣处理法所产生的污泥量较大,过去该厂将一部分污泥送至矿渣熄灭器,代替清水对矿渣进行增湿,然后共同作为水泥配料外运;其余部分用槽车送到污泥处理场处理,经沉淀、晾干后作为砖瓦添加剂。几年来的运行情况表明,该厂污泥处理装置虽然基本能满足需要,但污泥处理场占地面积大(15000㎡),处理费用高,劳动强度大,还存在一定的污染。
为了进一步降低污水处理费用,提高外排水质量并取消污泥处理场,该厂决定寻找新的污泥处理途径。在对几种污泥处理技术及设备进行调研分析的基础上,该厂开展了采用卧式螺旋卸料沉降离心机对硫酸装置污泥进行脱水的攻关项目。经过不断地改进和完善,装置运行良好,脱水后的污泥混入矿渣外运,现将情况介绍如下:
1 离心机的工作原理及装置流程
卧式螺旋卸料沉降离心机主要利用物料中各组成密度的差异对物料进行脱水、浓缩、澄清及固体颗粒分级等操作,具有对物料适应性强、处理量大、连续作业、无滤布、操作简单、运行费用低、占地面积小等优点。
在分离过程中,悬浮液由进料管加入,经螺旋推料器内的物料加速器进入转鼓,在离心力的作用下,密度较大的固相被抛向旋转的转鼓内壁,再由螺旋推料器上的叶片推至转鼓右端排渣口排出,密度较小的液相则通过转鼓左端的溢流孔流出。螺旋与转鼓同向回转,但具有一定的转速差。由于沉渣在排出转鼓之前经过一段脱水区域进一步脱水,因此沉渣含湿量较低,且在一定的进料流量变化范围内保持不变。通过改变主、副机的转速等技术参数,该机可用于分离不同要求的物料。
该厂污泥脱水装置的工艺流程为:沉淀池底的污泥用立式污泥泵送至离心机进料口,脱水后的污泥(固相)从离心机下料口放至渣灰皮带上随矿渣一起外运,含有部分细小污泥颗粒的水(液相)从离心机溢流口连续排至污水处理装置的吸水井,用污水泵送至沉淀池再次进行沉淀。
2 装置运行及整改情况
根据该厂污泥的特性、主要成分、处理量等工艺参数,生产厂家对原有定型离心机做了适当改进,在此基础上该厂进行了污泥脱水试验,对设备出现的问题进行诊断,并进行相关的改进和完善。
硫酸装置的污泥处理是困扰企业的环保难题。据调查,国内未见用这类卧式螺旋卸料沉降离心机处理硫酸装置污泥的报道。该厂在使用初期出现的问题主要有:
(1)运行中经常出现离心机内叶结死,造成超负荷跳闸或脱水效率严重下降,必须将离心机解体冲洗干净才能恢复运行。
(2)分离液含固率太高,即脱水效率不高。
为此,该厂于离心机生产厂家一起多次进行试验及改进。针对硫酸装置污泥粘度和密度较大的特点,将离心机型号由LW500改为LW400,将转鼓的工作长度由1500mm缩短到860mm,差速器功率由7.5kW改为11kW,副电机功率由5.5kW改为7.5kW,主机转速从2300r/min调整为2100r/min,主、副机的差速比从23:1调整为28:1,下渣口也作了适当改进。
这些改进较好地解决了离心机的易堵问题,确保了离心机的稳定运行,脱水效率也有一定的提高。装置运行稳定后,其污泥处理量在8m³/h左右,脱水后污泥脱水率为13.5%左右,满足了与矿渣一起外运的要求。
离心机运行正常后又出现了另一个问题——分离液中含有大量的细小颗粒,这样就增大了沉淀池污水中悬浮物的含量,使其难以沉降,故而外排污水的悬浮物含量达不到国家一级排放标准(SS≤70mg/L)。对此,该厂在实验室试验的基础上,开始了向污水中添加阴离子聚丙烯酰胺絮凝剂的试验。从试验情况看,效果较为明显,外排污水中悬浮物含量的合格率由前3个月的37.5%上升到87.5%。
3 效益分析
通过整改,该厂成功地将卧式螺旋卸料沉降离心机应用于硫酸装置的污泥脱水,收到了 较好的环境效益和经济效益。离心机运行正常后,大大减少了去污泥处理场的污泥槽车数量;处理后污水中的悬浮物含量符合污水处理厂的进水要求,从而确保了污水处理厂的稳定运行及外排水的质量。
按离心机处理能力8m³/h、污泥(浆)密度1310.3kg/m³、每年运行时间300d、每辆槽车装污泥50t、每辆槽车运费250元计,每年可减少污水处理费用37.4万元,同时污泥回收作为矿渣出售,一年可增加收益5万元,除去离心机每年运行费用5万元,经济效益十分可观。
4 结语
通过多次的试验和整改,卧式螺旋卸料沉降离心机在我厂污泥脱水中得到了成功的应用,从而为硫酸装置的污泥处理又找到了一种方法。为了完全取消污泥处理场,减小污泥处理装置的占地面积,该厂决定再上一台卧式螺旋卸料沉降离心机。对沉淀池中细颗粒含量增高继而使处理后污水悬浮物含量增高的问题,该厂将从两方面入手:一方面继续进行添加聚丙烯酰胺絮凝剂的试验,以确定合适的絮凝剂加量及絮凝工艺;另一方面,将离心机脱水后产生的分离液送入焙烧工序的矿渣增湿器而不是返回沉淀池,以确保外排污水悬浮物含量达到国家一级排放标准。