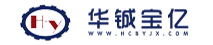
1 引言
钻井污水主要由废弃钻井液、岩屑、油、冲洗水和各类添加剂组成,悬浮物含量高,组分复杂多变,可降解能力差,是石油行业比较难以处理的污染源。卧式螺旋卸料沉降离心机具有单机处理能力强、能够连续自动化运行以及对物料适应力强等优点,在钻井污水处理领域占有重要地位。
2 模型与边界条件
模型的结构形式来自实际使用中的LW-250型卧螺离心机,其主要尺寸参数如下:
转鼓内径:250mm
半锥角:8°
转鼓长径比:4
螺旋推料器的螺旋内筒外径:170mm
叶片倾角:0°
螺旋导程:60mm
对出渣段予以适当简化,并做出以下假设:
①转鼓内充满液体且流动稳定。
②液相是连续不可压缩流体。
③固相是密度均匀等粒径球形颗粒,运动过程中无变形与破碎。
④不考虑重力作用。
分离物料选择体积分数20%的滑石粉浆液,滑石粉的颗粒形状均匀,不易发生破碎和聚结现象,能够巧妙地回避絮凝影响。粒度分布由Malvern激光粒度仪测得,颗粒中径为28.73μm,体积平均粒径为32.59μm。由于Fluent中的Mixture模型不能直接对正态分布的颗粒进行计算,模拟取单一粒径30μm,颗粒堆积极限取理论值0.72。
模型采用Pro/E与Gambit联合建立,在进料管、溢流口和螺旋流道中心区域采用结构化网格,其他区域采用非结构化网格。经无关性验证,确定的网格数目约为54万。
边界条件设置如下:进口采用速度进口,流速取1.2m/s;溢流口与出渣口采用Outflow边界,出流质量权重取0.45:0.55;流道内与流体接触的壁面均采用无滑移条件;螺旋与转鼓间差转速通过SRF模型指定。进料的物性参数和离心机的操作参数如下:固相粒径30μm,固相密度2621.2kg/m³,液相密度998.2kg/m³,液相黏度1.003mPa·s,处理量2.0m³/h,液池深度20mm,转鼓转速4000r/min,差转速20r/min。
3 求解策略及过程
用RSM湍流模型来模拟卧螺离心机内部流动。颗粒的沉降与输送过程采用Mixture模型模拟,Mixture模型采用单流体方法,但允许相与相之间的相互贯穿,也允许各相以不同的速度进行运动,因此能够比较全面地反映卧螺离心机的内部流动状况。
4 结果分析和验证
4.1 颗粒直径对分离性能的影响
当粒径较小时,沉渣含湿量沿转鼓轴向的变化不大,分离效果不佳。随着颗粒直径的增加,沉降速度变快,沉渣含湿量在转鼓轴向的下降速度明显变快,出渣含湿量也更低。当颗粒直径大于50μm时,不同粒径下沉渣含湿量曲线的斜率基本保持不变,说明粒径的增加对脱水速度影响较小,但对脱水效果仍有一定影响。
评价卧螺离心机分离性能的指标主要有固相回收率与出渣含固率。在粒径大于10μm后,固相回收率不再明显变化,说明在现有结构和操作条件下,直径大于10μm的颗粒几乎都不会从溢流口逃逸,符合卧螺离心机保持高回收率的情况。出渣含固率随颗粒直径变化而提高,增加幅度先快后慢,逐渐逼近颗粒的堆积极限对应的质量含固率82.7%。
4.2 颗粒密度差对分离性能的影响
当颗粒密度大于液相密度时,颗粒密度越大,离心沉降速度越快,分离效果越好。但当固相密度接近甚至小于液相密度时,转鼓内的固相体积分数分布将发生很大变化。当颗粒密度与水接近时,此时的出渣含固率与固相回收率都比较低,这说明两相没有实现有效分离。固相含量在靠近排渣口附近为13%~15%,在溢流口附近为25%~28%,即出现了“排渣口排水,溢流口溢渣”的情况。其机理可概括为:密度较大的液相分布在螺旋流道外侧,颗粒漂浮在液体内表面,在转鼓锥段,液相流动半径缩小,开始挤压分布在转鼓内侧的颗粒相,迫使其反向流动至转鼓大端。此时,液固两相虽然也发生了分离,但固相只能集中在转鼓中部,分离效果很差,溢流口的出渣也容易导致出口的堵塞,这些显然都违背设计意愿。因此,采用传统的螺旋卸料式离心机难以实现轻质固体的分离。
4.3 液相黏度
液相黏度表示物料中液相水的黏度,区别于物料的混合黏度,显然混合黏度与进料浓度有关,而进料浓度的影响通过Mixture多相流模型进行考虑。因此,分析黏度对分离性能的影响时只需考虑不同操作温度下液相黏度的变化范围即可。
温度降低时,液体黏度增加,切向速度略有下降,而低切向速度对分离过程不利,因此降低液体黏度有利于固液分离。对于一些难分离物料,机械脱水前一般要进行调质处理,使颗粒絮凝,从而变得容易沉降。然而,调质有时也会增加物料的混合黏度,因此,虽然调质对分离性能的改善比较明显,但仍要以分离效果较佳为宜。
5 结论
(1)卧螺离心机的分离效果随颗粒直径增加而提高,但当粒径增加到一定程度时,固相回收率不再明显变化;出渣含固率的增长先快后慢,但不会超出等粒径颗粒堆积极限所对应的质量分数。
(2)当颗粒密度大于水时,一定范围内,颗粒密度越大,分离效果越好;当颗粒密度与水接近甚至小于水时,轻质固体与液相虽然也会分离,但由于无法有效排渣,只能堆积在转鼓中心。
(3)物料温度越高,液相黏度越低,越有利于分离;絮凝剂的添加有时会增加分离液的混合黏度,但也能显著改善颗粒的沉降效果,因此要合理选择用法和用量,避免不必要的运行成本。