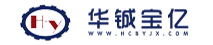
1 前言
卧螺沉降离心机作为一种高效的固液分离设备,被广泛地应用于石油、建筑、化工等行业,利用固液两相的密度差及离心作用力来实现固体与液体的分离。在离心脱水过程中,卧螺离心机的结构参数、操作参数以及物料性质都会对脱水效果造成影响。由于离心分离过程的复杂性、悬浮液特性的易变性、特别是固相颗粒的形状和粒径分布的多态性,给理论和试验研究造成了极大的困难。对于物料性质来说,污泥的调质将会对后续的脱水工艺与设备产生较大影响,是污泥浓缩和脱水重要的前处理过程,其方法主要包括化学法、加热法、淘洗法、冷冻法和加骨粒法等,新型调质技术主要有超声、微波、热水解、磁场、电渗透、生物絮凝等。
为进一步提高脱水效果,降低污泥的含水量,国内外学者进行了大量的理论和试验研究。大量理论和试验研究结果表明,可以从提高分离因数、增加机械挤压和延长停留时间三个方面来改善脱水性能。但试验研究因不能任意改变离心机的结构尺寸,不能同时针对多个工艺参数进行,不能系统考虑调质技术使用前后污泥脱水效率的变化而具有一定的局限性。
近年来,计算机技术与计算流体动力学(CFD)的发展为卧螺离心机流场的研究开辟了新的方向。本研究结合污泥调质技术对卧螺离心机进行CFD模拟,旨在研究卧螺离心机的长径比、螺旋及污泥黏度对分离性能的影响,同时考察不同粒径的物料在不同转速下的分离效率。
2 数值模拟方法
2.1 几何模型和网格划分
卧螺离心机中转鼓和螺旋输送器以一定的转差运转,以实现悬浮液的分离和沉渣的排出。模拟所用卧螺离心机的主要尺寸如下所述:转鼓圆柱段外直径420mm,圆锥段长度325mm,锥角8°,液层深度45mm,进料管外直径60mm,进料管长度1200mm。考虑螺旋的情况下,先通过NX6.0建立螺旋输送器的模型,用螺旋输送器切转鼓实体即可得到液流区域,然后将模型转换为CAD图形,读入Fluent进行模拟计算。
2.2 边界条件和求解策略
计算所用液体密度为1015kg/m³,液体黏度为0.001003Pa·s。进料管入口设为速度入口边界,指定入口处的液流速度为0.5m/s,入口湍流强度按经验公式来估算。卧螺离心机出口为溢流出口,设定出口为Outflow边界条件。转鼓外壁设定为无滑移固壁边界条件,自由液面处壁面设定为滑移切应力为0,给定卧螺离心机转鼓的转动角速度设为30~50rad/s,转差设置为2~5rad/s。
应用控制容积积分法离散控制方程组,各方程对流项的离散采用精度较高的QUICK差分格式,压力与速度的耦合采用SIMPLE算法。卧螺离心机内部流场为较为复杂的旋转占优流动,因此选取精度较高的RSM湍流模型封闭控制方程组。模拟固体颗粒的运动过程时选取DPM模型,考虑螺旋输送器时选取滑移模型。
3 结果与分析
3.1 整体流场
选取离心机长径比为4,转鼓角速度为50rad/s,做z=500mm和y=0mm两处截面的静压分布。可以看出,静压沿径向从中心向外逐渐增加,自由液面处静压小,在转鼓壁面处达到极值。由于入口与溢流口都与大气相连,所以此两处的静压接近于零值。
选取离心机长径比为4,入口速度升为0.5m/s,做整体速度场在截面y=0mm上的流场速度云图,转鼓轴向方向z=900mm截面的等速度线图。可以看出,流体以一定的速度进入卧螺离心机,由于分料作用在分料口速度降低,然后随高速旋转转鼓的带动进入分离场,在接近转鼓处速度开始升高,当流体到达分离场中部时流场中心位置处的速度梯度小;流体接近溢流口处,流场中心近壁面的速度降低但速度梯度增大,由此可知此时固液仍可进行分离过程,这表明增加转鼓长度的重要性。如果转鼓长度不足,将严重影响分离过程的进行,甚至不能完成分离过程。因此,大长径比有利于离心机的固液分离。
3.2 长径比对卧螺离心机流场的影响
3.2.1 长径比对流场压力分布的影响
从静压力的径向分布可以看出,不同长径比下静压沿径向的分布规律基本一致,即静压力沿径向从中心向外逐渐增加,基本呈线性分布,自由液面处静压小,在转鼓壁面处达到极值,说明增加液环层的厚度静压力值会显著增大。当长径比从2.5增大到3.5时,同一径向位置处的静压随着长径比的增大而减小,说明此时增大长径比可以减小阻力损失。但是进一步增大长径比,即长径比由3.5增大到4.0时,同一径向位置处的静压随着长径比的增大而迅速增大,说明此时增大长径比将增加阻力损失。
从截面平均压力沿轴向的分布可以看出,同一长径比下截面平均压力沿轴向的变化不大,但是同一轴向位置处截面平均压力随长径比的变化较大,随长径比压力的变化与径向分布规律类似。
3.2.2 长径比对切向速度分布的影响
卧螺离心机转鼓内液流的流动方向可以分为轴向、切向和径向三个方向,其中轴向速度和切向速度可以表征离心机分离过程的效果。轴向速度是表征卧螺离心机生产能力的一个物理参量,轴向流速越大,表示生产能力越强,但轴向速度过大又会导致脱水效果下降,致使沉渣含湿率上升。
卧螺离心机的工作原理使分离液中的固体颗粒在离心力的作用下沿径向向外运动并产生分离,切向速度是分离液中固液发生分离的关键,在研究卧螺离心机时一般采用旋转角速度进行分析。转鼓的转动带动液层一起旋转,但液体的旋转和转鼓的旋转并不一致,存在滞后现象。
经过模拟,结果显示在液层深度、转鼓转速和入口流速不变的情况下,长径比变化对切向速度影响不大,说明长径比对切向速度滞后系数的影响不明显。然而,长径比增大会使分离空间增大,从而促进固液分离,因此增大长径比有利于提高卧螺离心机的分离性能。与静压分布的研究相结合,继续增大长径比会使阻力损失显著升高,因此选择长径比时应综合考虑分离性能和阻力损失两方面的因素。
3.3 黏度对卧螺离心机流场的影响
3.3.1 黏度对压力分布的影响
黏度升高对自由液面附近的静压力基本没有影响,在转鼓近壁面附近静压力随黏度的升高而有一定的升高,本文考察的范围内黏度对阻力损失的影响不大。
3.3.2 黏度对切向速度分布的影响
在黏度变化相对较小时切向速度变化也较小,随着黏度的增大,切向速度逐渐降低,因此流体的黏度对切向速度有一定影响。当黏度大时切向速度相应较小,而较低的切向速度对于分离过程是不利的,因此降低流体黏度更有利于固液分离。
3.4 污泥调质对脱水特性的影响
目前已有多种调质技术,使用调质技术如热水解、超声与微波等可以使污泥的特性如黏度与粒度等发生改变。下面将对有螺旋和无螺旋两种情况进行对比,结合污泥的调质分析悬浮液黏度、颗粒的粒径分布及离心机中螺旋对分离效率的影响。
3.4.1 悬浮液黏度对脱水特性的影响
悬浮液的黏度主要取决于液相的黏度和悬浮液的浓度,通过理论分析和单相流场模拟可知,黏度对离心机分离效率有影响。现选取本课题组污泥调质特性研究测得的污泥黏度作为模拟数据,分析调质技术对污泥脱水效率的影响。
从结果可以看出,在无螺旋情况下,随着黏度的增大,离心机分离效率略有降低,由于黏度变化值较小,所以分离效率的变化幅度不是很明显。相同黏度下,分离效率随着长径比的增大而增大,说明大长径比有利于固液分离,上述结果与单相流场的模拟结果以及理论分析结果相符合。而在有螺旋情况下,随着黏度的增大离心机分离效率有增有减,这是由于黏度的变化幅度不大,而且在螺旋的作用下流场内湍流变化明显,与层流理论不相符合。但在相同黏度下,分离效率随长径比增大而增大,说明即使在有螺旋的情况下,大长径比离心机也利于固液分离。有螺旋与无螺旋这两种情况相比,由于螺旋的推进作用有促使颗粒向离心机圆锥段运动,其次螺旋还可阻挡部分回流的固体颗粒,因此离心机中的螺旋设计促进了固液两相的有效分离。
3.4.2 粒径分布对脱水效果的影响
粒径分布是影响固液分离的重要因素之一,相同体积分数下不同粒径分布的污泥其脱水效率也有所不同。为了研究固液分离时的较佳粒径分布及离心机中螺旋对分离效率的影响,指导污泥的调质改性方向,采用DPM模型、滑移网格对不同粒径下固体颗粒的运动过程进行模拟仿真,从长径比为4.0、入口速度为0.5m/s时各转速条件下颗粒的分离效率出发,对于悬浮液中不同的固相粒度分布得出不同的分离效率。
从结果可以看出,随着转鼓转速的增加,分离效率随之增大,而悬浮液中颗粒粒径越大,其分离效率越高,反之越低。这是由于转速越大、颗粒粒径越大,颗粒所受离心力越大,越有利于固液分离。根据粒径分布来选择合适的转鼓转速并选用有螺旋设计的机型,在降低离心机能耗的同时,也能保持卧螺离心机分离效率维持在较合理的水平。
4 结论
本文采用流体力学软件FLUENT,将离心机三大基本方程与CFD仿真软件有效结合,分析了理论和试验中尚难以处理的结构复杂的卧螺离心机旋转流场。研究了流场速度和压力分布的变化规律,并有针对性地得到了部分操作参数对分离场的影响规律。
(1)在单相无螺旋流场中,随着长径比的增大,转鼓内壁处压力值先变小后增大,因此就本研究的研究范围来看,大长径比有利于固液分离,但过大会使阻力损失显著升高,长径比为3.5为较佳选择。
(2)黏度的增加不利于离心机分离效率提高,在本文考察范围内由于污泥黏度较低且变化不大对分离效果总体影响不大。相同黏度下,分离效率随长径比增大而增大,说明大长径比利于固液分离。
(3)离心机中螺旋的设计使得流场内层流理论发生变化,模拟结果表明离心机的螺旋设计使分离效率明显优于无螺旋情况,因此螺旋的存在有利于固液分离。