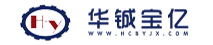
近年,处理废弃钻井完井液的固液分离技术已有新的进展,为油气田综合治理废弃钻井液提供了科学依据。
1 废弃钻井完井液固液分离原理
1.1 固液分离的工程意义
根据钻井工程技术的要求,钻井液中常常加入许多不同种类和性能的添加剂,多种护胶剂协同作用,使钻井完井液胶体体系十分稳定。经过固控设备处理后,废浆中的固相主要是粒径小于20μm的超细颗粒,它们与残余的添加剂构成了水基废浆的胶体分散体系。随着颗粒粒径的减小,破坏废浆胶体体系的难度增大,固液分离也就更困难。
通过加入适当的絮凝剂和助凝剂可以改变钻井液体系的物理、化学性质,彻底破坏钻井液胶体体系,改变废钻井液中粘土颗粒表面性质,让更细的颗粒产生聚结,使其在机械辅助分离条件下更容易被除去。固液分离法,是减少钻井废弃物的排放量、提高水的循环利用率和解决环境污染问题的基本步骤,也是目前行之有效的技术之一。
1.2 钻井完井液胶体稳定性
配置钻井液用的膨润土本身就具有很强的水化能力,而在钻井液中又加入了大量的各种有机高分子护胶剂,这些处理剂自身的稳定性越来越好,护胶能力越来越强。这些物质本身在溶液中都可形成较强的阴离子或阳离子稳定胶团。正是由于它们的存在,严重地影响着废弃钻井液的化学脱稳脱水。存在于废弃钻井液体系中具有表面活性的固体比普通污泥要高的多,钻井液中固相的平均尺寸为30~40μm,而膨润土的平均粒径为0.2~4μm,从而使膨润土离子成为钻井液体系高效的固体乳化剂和胶体稳定剂。可以说,废弃钻井完井液是一个具有高度稳定性的胶体体系,脱水难度也大大增加。
1.3 钻井完井液胶体脱稳方法
对于废弃钻井完井液这个含有许多护胶剂的特殊胶体体系,到目前为止尚没有哪一种絮凝剂能处理所有类型的废钻井液。实践中都是针对某种特定类型的废钻井液,采取对应的絮凝剂和助凝剂,使其达到脱稳脱水的效果。
美国路易斯安那州大学的固控环保实验室分别以室内研究和放大中试的规模,对现有的管式离心沉降、垂直螺旋压滤、皮带压滤和真空抽滤等几种化学强化固液分离技术做了综合评价。采用硫酸、盐酸、三氯化铁、硫酸铁及明矾等调节废钻井液的pH值,使其控制在5.5~6.5,再加入非离子型或低电荷量阴离子型的高分子量聚合物,辅以皮带压滤或离心沉降的办法,可使废弃钻井液达到较好的固液分离效果,脱出泥饼的固含量为59%。
1.4 钻井完井液胶体脱稳机理
研究发现,絮凝剂与水中胶粒物发生作用,从而达到絮凝除杂目的的过程分3步:
(1)溶剂的絮凝剂离子扩散迁移到固液界面。
(2)絮凝剂离子快速压缩双电层并吸附结合到固体表面。
(3)吸附化合态在胶体表面上缓慢地进行结构和化学重排,朝向更稳定的表面层组成变化。
这个阶段的低速是由于吸附和重排需较长的时间才能达到稳态,此时,胶体颗粒脱稳从而破坏其沉淀稳定性,导致絮凝沉淀。
20世纪80年代以来,对凝聚絮凝机理有许多研究和论述,可概括为4种作用机理,即压缩双电层理论、吸附电中和理论、吸附架桥理论和卷扫絮凝理论。这4种絮凝理论,各自解释了凝聚絮凝过程中的絮凝剂与胶体颗粒的相互作用机理。在实际絮凝过程中,往往是几种絮凝机理综合作用的结果,或者在特定水质条件下以某种机理为主。
2 废弃钻井完井液固液分离用絮凝剂
絮凝剂和助凝剂在废弃钻井液化学脱稳脱水固液分离中的重要作用已被人们所认识。特别是废钻井完井液中粒径小于20μm的那部分超细颗粒必须依靠絮凝作用才有可能被清除。在油田常用的钻井液体系中加入阳离子絮凝剂,絮凝剂吸附在颗粒表面,中和颗粒表面负电荷,造成Σ电位下降。当Σ电位降到一定数值(零电点附近)后,体系即脱稳絮凝。但是,若加入过量的絮凝剂,颗粒表面吸附过量的正电荷,改变颗粒表面双电层的性质,Σ电位反转为正值,并且当其超过一定值时,体系重新稳定,反而不利于絮凝及分离处理。因此,絮凝剂的选择和絮凝过程中固相颗粒表面Σ电位的演变研究,对提高固液分离效率和效果至关重要。
目前,絮凝剂种类很多,从组成上可分为无机型、有机型和复合型。从结构上可分为低分子型和高分子型。从电性上又可分为阳离子型、阴离子型和非离子型。
在实施固液分离处理时,如能使胶体体系的稳定性破坏,导致废液中的主要钻井完井液处理剂失去护胶作用,进而破坏胶体悬浮体系的稳定性,将对固液分离起到极大促进作用。试验证明,除选择合适的絮凝剂外,在废液,特别是高浓度的钻井完井废液中加入一定量的无机混合酸酸化,也能使废液中的主要钻井完井液处理剂失效,产生固液分离,达到初步沉降处理的目的,成为实现高效固液分离的有效手段之一。
3 影响废弃钻井完井液固液分离效果的因素
3.1 絮凝剂
影响固液分离的首要因素当然是絮凝剂及其优化加量。作为絮凝剂主要品种的聚丙烯酰胺及其衍生物,其在废浆固液分离中具有良好的性能,其在碱性或中性溶液中可以很好地溶解。分子中水化基团离解成-COO-离子,增强了分子链节间的静电斥力,卷曲的分子得以伸展。而当溶液中加入酸后,使水化基团-COONa变成-COOH,不利于大分子链伸展,同时HPAM分子内、分子间可发生亚胺化作用,使得HPAM大分子链产生严重卷曲,将已吸附的黏土颗粒和钻井液添加剂紧紧地包裹在大分子中,充分体现了大分子的卷扫作用,从而实现固液分离的目的。
不同分子量的HPAM对固液分离自然出水率的影响不同。但分子量在700万以上的HPAM配制时溶解困难,不易在粘稠的废钻井液中分散,只能使用很稀的溶液,这样会增大絮凝剂的体积,给施工带来不便。因此,建议现场选用分子量为300万~500万的HPAM,即能基本达到固液分离要求。
另外,还可以通过调节HPAM的水解度控制它的吸附、带电、水化的能力和分子链形态,从而获得不同的絮凝能力。一般来说,水解度在50%左右时,分子中的-COONa基团和-CONH2基团比例刚好既能满足溶解快的要求,又使分子整体具有较强的吸附性,试验证实的自然出水率和抽滤出水率均可达到较大值。
HPAM的吸附、架桥作用和絮凝固相颗粒的能力与废钻井液中的固相含量有关。HPAM的加量与废钻井液中的固相含量成线性正相关,因此,为提高絮凝脱水效率,在实施固液分离时,应先向体系加入水进行稀释。
单一的有机絮凝剂和单一的无机絮凝剂用于处理钻井完井废液固液分离时均有一些缺点,一般将二者配合使用,这样既可以降低絮凝剂的使用量,又可以提高固液分离的效率,还能提高分离出的水的质量。
3.2 助凝剂
前已述及,选择合适的助凝剂可以改善絮凝剂的絮凝效果,降低固液分离出水的浊度,而对以中强碱性为主的钻井完井废液来说,强酸是一种性能良好的廉价助凝剂。对多数絮凝剂来说,无论是有机型、无机型还是复合型,一般是较佳作用范围均在中性附近,此处其用量相对较少,絮凝处理效果较好,且处理后的水呈中性,便于利用。
但是,若想进一步提高废弃钻井液固液分离的质量,仅靠强酸作助凝剂是不够的,毕竟酸不像无机絮凝剂那样可在水中水解生成聚合态水合物,并吸附于胶体颗粒上使之脱稳。
除此之外,硫酸铝、三氯化铝、硅藻土等也是钻井废液固液分离的优良助凝剂。硫酸铝、三氯化铝的溶液本身也是强酸性的(pH值约为2~3),它们可以很好地中和废浆体系的pH值,提高有机絮凝剂的絮凝能力,同时本身对废浆也具有很好的脱稳絮凝能力,对废弃钻井液的固液分离起到了较强的协同作用。这实际上也是有机絮凝剂与无机絮凝剂配合使用的结果。
3.3 废液稀释比
既要脱出废浆中的水,又要在废浆中先加入一定量的水,这是很令人费解的。在绝大多数情况下,不加入水是不可能脱出水的。废弃钻井液的黏稠性严重地妨碍着絮凝剂在其内部的分散和絮凝,加入絮凝剂和助凝剂以前对其进行加水稀释处理是必要的。未经稀释的废钻井液无法进一步使固液分离。因为当固体颗粒上的电荷被中和或部分中和的同时,也起了破坏水化层保护膜的作用,使水化程度降低。这时,黏土颗粒开始聚结,连接成网状结构,并把水包在网状结构之中。稀释加大了颗粒间的距离,加入絮凝剂之后,就减少了形成网状结构的可能性。不同的废液体系和脱水条件,较佳稀释比不同。
尽管如此,由于各种护胶剂的作用使得稀释后的废弃钻井液仍是一个稳定的胶体体系。除少量的加重材料和大颗粒的钻屑在重力作用下自然沉降外,其它残留的细小固相颗粒仍稳定地悬浮在废浆体系中,废弃钻井液整体的脱水分离仍需要絮凝剂的脱稳脱水处理。
加水稀释后的废弃钻井液不仅密度降低了,而且体系的塑性黏度也大大降低了。显然,经稀释处理后的废弃钻井液,随着黏度的降低,絮凝剂在废浆中的溶解分散性能会得到改善,絮凝剂的絮凝脱稳脱水作用能得到充分发挥。稀释倍数的增加无疑会加大处理废弃钻井液的工作量。从废弃钻井液稀释后塑性黏度的降低效果可以看出,用1~2倍体积的水稀释废弃钻井液就可以达到稀释降黏的作用。
用于稀释废弃钻井液的水不需经过任何特殊处理,也可以使用废弃钻井液固液分离后分离除的水,只要出水的质量能达到工业排放污水的要求就行。
3.4 絮凝动力学
絮凝动力学讨论絮凝的速度问题,只有具有一定速度的絮凝过程才能满足水处理对出水量的要求,因而才具有实际意义,所以絮凝动力学是水处理絮凝学的重要研究内容。胶体微粒间存在Van der Waals吸引作用,而在微粒相互接近时因双电层的重叠又产生排斥作用,胶体的稳定性就决定于此二者的相对大小。以上2种作用均与微粒间的距离有关,都可以用相互作用位能来表示。
20世纪40年代,苏联学者与荷兰学者分别提出了关于各种形状的微粒之间的相互吸引能与双电层排斥能的计算方法,并据此对憎液溶胶的稳定性进行了定量处理,被称作胶体稳定性的DLVO理论。
根据DLVO理论可知,胶体之所以稳定是由于综合位能曲线上有势垒存在;倘若势垒为零,每次碰撞必导致聚沉,称为快速絮凝;若势垒不为零,则仅有一部分碰撞会引起聚沉,称为慢速絮凝。无论是对快速絮凝还是对慢速絮凝,微粒之间的相互碰撞是首要条件,而它们的相互碰撞是由其相对运动引起的。造成这种相对运动的原因可以是微粒的布朗运动,也可以是产生速度梯度的流体运动,前者导致的微粒聚沉称为异向絮凝,后者导致的微粒聚沉称为同向絮凝。
在异向絮凝中微粒的碰撞是由布朗运动造成,碰撞频率决定于微粒的热扩散运动。由于钻井完井液中的固相粒子主要是直径为10~20um的胶体粒子,其自然聚沉过程非常慢,这就是说即使在完全脱稳的情况下,异向絮凝过程也是极其缓慢的。
依靠布朗运动的异向絮凝速度太慢,不能单独应用,特别是当微粒相互碰撞聚集变得较大后,布朗运动就会减弱甚至停止,絮凝作用就会减弱甚至不再会发生。但是,长期以来人们观察到,缓慢地搅动会助长絮凝,这是因为搅动会引起液体中速度梯度的形成,从而引起微粒之间的相对运动而造成微粒的相互碰撞。当体系中的粒子体积浓度太小,有可能影响其碰撞效率时,就有必要加入一定量的所谓“助凝剂”。如果分散体系中的粒子以不同的速度沉降,较快沉降的粒子就会与较慢沉降的粒子碰撞,而导致聚集,由于聚集使粒子质量增大,聚集体就会更快地沉降,并可能与其它粒子进一步碰撞和聚集,这种聚沉称为差速沉降絮凝(差降絮凝)。差降絮凝也可以看作是一种特殊形式的同向絮凝。
絮凝过程动力学的研究指出,快速絮凝和慢速絮凝的结合,以及梯度絮凝和多级串连絮凝的结合,有利于同向絮凝和差向絮凝的形成,这为固液分离装置的设计提供了理论依据。通过优化絮凝动力学条件,在絮体(絮花或矾花)的形态、结构、粒度、密度、强度等方面获得较佳组合,才能实现钻井完井废液强化固液分离的过程。
4 固液分离工艺技术和装备
钻井污水成分复杂,稳定性特强。由于产生的地点不同,污水水质差别非常大,不可能以一种固定的装置及流程有效地处理不同油田的污水。常规处理工艺及设备对药剂依赖性较大,而且对具有相互性质差别大的高悬浮物、高COD、高含盐、高色度等特征的钻井污水的处理费用居高不下。这一切都使得国内外已有的钻井污水处理装置既多样化,又难以大面积推广应用。
为适应钻井工程野外作业和周期短的特点,近年来美国、加拿大、法国对钻井污水处理装置的研究和设计都趋向于橇装化以便于安装、拆卸和搬迁。美国NEW PARK废弃物处理公司研制了一种由钻井液脱水装置、固体颗粒控制装置和污水处理装置组成的油田污物净化装置,在其中的污水处理装置中,设有容量为16~320m³的药剂混合罐、沉淀池和离心机。乌克兰石油工业联合公司研制的YOB钻井污水处理装置采用化学混凝和多级沉淀方法处理污水,并提供密闭式钻井供水系统、这种装置的优点是没有地槽沉淀池,大大减少了占地面积,并能利用处理后的净化水。法国PAU国际石油设备公司的橇装闭路式污水处理装置,采用中和、混凝和离心分离工艺,可连续操作,也可间歇式操作,具有很大的灵活性,处理量达0.58m³/min,净化水可再利用。美国还研制出过滤-吸附和反渗透处理装置,钻井污水经过处理可达到较高的出水水质,可灌溉农田甚至饮用,适用于干旱地区的钻井作业。
在国内,江汉机械研究所研制的钻井污水处理装置,采用混凝、沉淀、气浮、过滤等单元设备联合处理的方式及模块化、橇装式设计,所有设备均布置在一个橇座上,移运性好,放置在井场接上电源即可运行处理,不影响井队的正常生产,达到了小型高效的目标、设备运行自动控制,可做到无人监守。从运输、拆装、操作上与同类装置相比,大大降低了运行费用,节约了人力、物力,在国内具有领先水平。
为实现上述强化固液分离处理的目的,有各种实现的途径,其中典型的组合式移动处理装置的实施方案包括混凝-斜管沉降-气浮-过滤工艺流程、脱稳-离心-电气浮-过滤工艺流程、混凝-静态旋流-动态旋流-电气浮-过滤工艺流程等。
4.1 絮凝-离心式固液分离装置
江苏油田利用现场泥浆循环系统,加装离心机和加药系统改造而成,其加药罐和沉降罐是由一个大的钻井液罐加隔板后一分为二加工而成的。罐高2.0m,离心机置于隔板上方,通过管线、离心泵和柱塞泵等与钻井液罐的加药区和沉降区相连,钻井液由潜水泵泵送至加药(反应)罐,同时在58r/min下搅拌约2min,使处理剂充分分散到钻井液中。分别静置约10min、30min、60min、3h和5h。开动柱塞泵和离心机,观察絮凝效果,根据需要测定并优化加药量、加药浓度、搅拌时间、小样沉降时间、离心机脱水分离时间等有关数据。
4.2 絮凝-离心絮凝式固液分离装置
也可以采用两级串连絮凝方式进行固液分离处理,先经过第一级初步絮凝处理,强化离心分离,使大部分固相去除,然后对脱除的废液进行第二级絮凝处理后达到配浆水或进一步深度处理达到外排水水质标准要求。江汉石油学院采用的钻井完井废液化学强化固液分离装置是化学强化造粒絮凝与高效固液分离相结合的过程,其工艺流程为两级三步处理:第一步对废弃钻井液强化造粒絮凝形成近似球形的密实絮体颗粒(称之为弹丸絮体),第二步用离心分离弹丸絮体,使固液两相分开;第三步对分离出的液相再进行絮凝处理至达标排放或再利用。
4.3 JZW-3沉淀-气浮-过滤式固液分离装置
江汉机械研究所在分析了各种污水处理技术特点后,结合钻井污水的特点,研制的JZW-3钻井污水处理装置采用了沉淀、气浮、过滤等3项分离技术。JZW-3系统由药液箱、加药射流器、反应池、气浮分离池、沉淀池、过滤池、流量计及管线、底座等构成。其中沉淀池、气浮分离池、过滤池直接用于泥水分离。
JZW-3钻井污水处理装置的技术特点如下:
(1)沉淀池采用上向流斜管沉淀技术。泥水沿相反方向流动,其斜管直径为25mm、倾角为60°、斜长为1000mm的斜蜂窝管。用于完成钻井污水的一级处理。
(2)气浮分离池为竖流式气浮分离池,采用部分回流加压溶气技术。由溶气泵、溶气塔、分离池和清水箱等构成。采用了空间大气通过射流器直接与水混合而制造溶气水的技术,减掉了空压机。用于完成钻井污水的二级处理。
(3)过滤池采用普通快滤池结构。滤料为特殊处理的植物果壳。过滤精度适中,工作周期长。用于完成钻井污水的三级处理。
4.4 PDW-Ⅱ型絮凝-沉降式石油钻井污水处理机
由中国科学院生态环境研究中心与某工厂协作开发的PDW-Ⅱ型石油钻井污水处理机,在冀东油田进行过工业试验。该机处理能力为4t/h污水,连续操作,整机带活动房可用卡车拉运。
该装置运行时,絮凝剂聚合硫酸铁加量为0.6~0.8kg/t,配成0.2kg/L溶液使用。聚丙烯酰胺投加量为2.5~5.0g/t污水,配成0.1%溶液使用。氢氧化钠投加量为60~100g/t污水,配成浓度为20g/L溶液使用。混凝时控制pH值为5左右,中和后的pH值略高于6。投药量视原水的状况可作相应变化。如原水色度浊度低,只须混凝至pH值为6即可,不必再用碱中和。若色度和浊度较高,混凝剂的用量需增加,而且在投加混凝剂的同时,另外投加一部分碱以防混凝槽受腐蚀。沉淀后的污水经过滤后回用或排放,沉淀污泥排入污水坑。
4.5 钻井废弃液-废水处理一体化设备
CNPC环境工程技术中心在对钻井废弃液污染处理技术长期研究的基础上,针对四川石油管理局高温深井聚磺钾盐钻井液体系钻井作业产生的复杂钻井废弃液所做的大量室内研究,设计研制出实现过程处理即边排污边处理的“钻井废弃液-废水处理一体化设备”,并且已投入川东地区使用。
该设备的工作原理是首先采用化学强化固液分离技术,将废弃钻井液通过化学脱稳处理后,然后在机械力的作用下实现固液分离。其次分离后固相采用无害化处置技术安全处置,分离出的废水进行混凝-沉淀-过滤,可通过进一步化学处理后达标外排或回用于井场冲洗用水或冲洗设备。分离后的固相采用固化处理技术处理后清洁安全处置。
5 结论
固液分离技术是废弃钻井完井液治理的关键技术之一。固液分离的效率和效果主要取决于对废弃钻井完井液体系的胶体稳定性的破坏,这是由絮凝剂、助凝剂、废液稀释比和絮凝动力学等因素共同作用的结果。为实现废弃钻井完井液固液分离工艺在现场的实施,国内外开发了多种组合式橇装化技术和装备,采用混凝、沉淀、气浮、过滤、氧化等单元联合处理,已经可以经济地处理废弃钻井完井液。