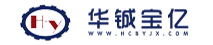
某炼化企业污水处理场在运行过程中产生大量的污泥:生化剩余污泥、油泥及浮渣。该污水场将污泥混合后只进行了离心脱水处理,脱水后污泥外委处置,由于外委处置费用高,且当地的有资质的危废处置单位能力有限,因此必须要进行污泥减量化处理。
本文考察了国内几家炼厂的污泥处理与处置案例,比较了污泥减量化处理技术,通过现场试验并结合以往的工程设计经验。设计了污泥干燥-焚烧一体化处理技术对该企业的污泥进行处理,以此达到污泥的减量化要求。
1 污泥的来源及污泥量
该炼化企业污水场的污泥主要有三种:含油污泥(来源于调节除油罐和隔油池),占总污泥产生量的5%;浮渣(来源于气浮),占总污泥产生量的55%;剩余污泥(来源于生化系统),占总污泥产生量的40%。
三种污泥混合后,经离心脱水机脱水,脱水污泥的含水率≤85%,含油量为5%~8%,脱水污泥的总量为3000吨/年。
2 污泥的组分和性质
2.1 剩余污泥
含有大量的生物絮团,少量的油,可挥发性固体含量占总固体含量的80%以上。含水率高,比重较小(约为1.006~1.02)。
2.2 浮渣
主要成分为油粒、泥、渣、灰等,含有较多油类、化学药剂和大量气泡。含水率高、粘性大,属于危险废弃物。
2.3 油泥
主要成分为比重较大的重油、悬浮物等。含油量高、粘性大,属于危险废弃物。
3 脱水污泥减量化技术
目前,国内炼化企业污水场脱水污泥的减量化技术主要有污泥干化、污泥焚烧等。
3.1 污泥干化
常用的污泥干化设备主要有薄层干化机、带式干化机、真空圆盘干化机、低温真空脱水干化机、旋风干燥机等。
3.2 污泥焚烧
目前,主流的污泥焚烧设备主要有流化床和回转窑。
4 工艺选择
通过比较污泥干化和污泥焚烧工艺,调研了正在运行的国内若干家炼化企业的实际工程案例:常用的污泥干化设备不适用于干化含油量(>3%)较高的污泥,炼化企业的混合污泥及油泥浮渣的含油量均高于3%,因此尚未有干化混合污泥和油泥浮渣的工程案例,只是对剩余污泥进行干化。
目前,绝大多数炼化企业的混合污泥及油泥浮渣均通过脱水后外委,极少部分企业进行了焚烧。
本项目的混合污泥中含油量超过了3%,因此不能采用常规的干化工艺。
经过实地考察天津某地一种用于处理市政脱水污泥的干燥-焚烧一体化设备,并利用该设备进行了含油污泥的处理实验,实验结果显示:设备的安全性及处理效果均优良,本项目采用污泥干燥-焚烧一体化工艺进行设计,并对原设备进行了部分优化和调整。
5 工艺设计
5.1 工艺介绍
污泥干燥-焚烧一体化工艺与常规的污泥干化+焚烧在设备形式上是有区别的,常规的污泥干化焚烧是分别设置污泥干化设备和污泥焚烧设备,将污泥先干化,再进焚烧炉焚烧。污泥干燥-焚烧一体化则是巧妙的将干燥与焚烧结合,设计成一体,在干燥段采用特殊设计的喷嘴将进料污泥进行雾化干燥。
在污泥干燥-焚烧一体化炉内完成污泥的焚烧、烟气二次燃烧和污泥一次干燥。该设备自下而上分为流化焚烧段、烟气二燃段和喷雾干燥段。
在焚烧段采用流化床炉焚烧工艺完成污泥颗粒的焚烧,焚烧温度大于850℃。
在二燃室采用天然气助燃,实现烟气1100℃,停留时间大于2s的二次燃烧。燃烧充分,并有效分解二恶英等有害物质。
直接利用污泥焚烧产生的高温烟气作为热介质,采用“喷雾干燥工艺”的干燥方式完成污泥的一次干燥,将泥雾干燥成含水率约30%的半干污泥微粒,连同余热烟气和蒸汽一起从干燥塔塔顶排出,进入二级喷雾干燥塔。与该塔入口气流雾化器喷射的高湿泥雾混合干燥,干燥后的污泥含水率为40%~50%,经过造粒后进入振动干燥机进一步干燥至含水率约20%,输送到焚烧炉进行焚烧。
5.2 工艺参数
干燥处理能力:含水率85%的脱水污泥≥2000kg/h。
污泥焚烧能力:含水率20%的干化污泥≥400kg/h。
污泥(炉膛)焚烧温度:≥850℃。
烟气(二燃室)焚烧温度:≥1100℃;停留时间≥2s。
燃烬率:≥98%。
生产负荷率:60%~100%。
尾气处理量:≥8000m³/h。
占地面积约600㎡。
5.3 工艺安全性
(1)二恶英的控制
①污泥及烟气焚烧满足“3T”要求,可以使大部分二恶英高温分解。
②高湿污泥喷雾干燥的同时可以使烟气温度从1100℃骤降至250℃以下,避开了300~500℃的温度环境,可有效防止二恶英的合成。
③二级污泥喷雾干燥、活性炭、袋式除尘等工艺,能有效地吸附烟气中的飞灰和二恶英。
(2)重金属的控制
重金属污染物在焚烧过程中被蒸发。熔点高的重金属随温度降低会凝结成粒状物而被捕集。熔点低的重金属会在飞灰表面催化作用下,形成熔点温度较高且较易凝结的氧化物或氯化物,特别是汞和镉大部分吸附在飞灰颗粒上而被捕集下来。必要时,向布袋除尘器捕集的粉尘中加入螯合剂,使其中的重金属在焚烧时进入螯合态,进入污泥残渣。
(3)粉尘及挥发性气体混合爆炸控制
采用并流式污泥喷雾干燥技术,可以有效地防止爆炸的风险:高温烟气与雾化污泥同向(并流)进入喷雾干燥塔并混合,使高温烟气处于高湿的污泥雾滴包围中得到极速蒸发降温;在污泥雾滴被蒸发干燥成半干颗粒时,烟气温度已经下降至250℃以下;烟气自身的含氧量较低(通常<12%);系统运行始终处于引风机抽风形成的快速气流流通状态。由此形成低含氧量、高湿、温度骤降、快速流通的环境,有效地降低了爆炸的风险。
将污泥焚烧炉与喷雾干燥塔一体化设计,构成在持续明火中的污泥喷雾干燥,更能防止粉尘和有机挥发性气体混合爆炸的风险。
在喷雾干燥塔、振动干燥床设置应急水喷淋装置。当污泥雾化喷嘴发生堵塞等故障时,系统自动切换至水喷淋,以降低烟气温度,防止自燃和粉尘爆炸的发生。
6 结束语
本项目设计的污泥干燥-焚烧一体化技术,设备结构紧凑,占地面积小,干燥、焚烧效果好,外加辅助燃料少,污泥焚烧彻底,减量化效果显著,工艺安全性较高。
本项目总投资约1900万元,远低于传统的污泥干化+污泥焚烧工艺(约4000万元)。
该工艺的运行废液约900元/t脱水污泥,低于传统的污泥干化+污泥焚烧工艺(约1800元/t污泥)。