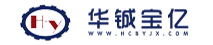
1 引言
城市污泥显著的特征是含水率高,初步沉淀的活性污泥含水率高达97%~99%,经过浓缩与消化后的污泥含水率仍在95%以上,经过机械脱水后的污泥滤饼含水率为65%~80%,这为污泥的长距离输送和后续处理带来经济上和技术上的困难;因污泥含水率较高,填埋土力学性质差,需混入大量泥土,从而导致土地的容积利用系数明显降低。《城镇污水处理厂污泥处置 混合填埋用泥质》(GB/T 23485-2009)和《生活垃圾填埋污染控制标准》(GB 16889-2008)中都明确规定,污泥混合填埋含水率应小于60%。脱水泥饼直接焚烧也因其含固率低不能达到维持过程自行运作所需的能值,需加入辅助燃料,使处理成本明显增加,难以承受。污泥的低温热裂解制油是近年来处理有机污泥的一种可望达到能量平衡的新技术,但低温热裂解前必须对污泥进行干燥处理。综上所述,污泥含水率高是难以处理与处置的关键。因此,污泥的干化处理是解决目前在污泥处理所遇到的许多问题的关键,也是污泥进行资源化(农用、焚烧、液化等)的前提。
2 传统的污泥干燥工艺与设备
2.1 转筒干燥
转筒干燥主体是一各略带倾斜并能回转的圆筒体,同时圆筒体内壁上安装有顺向抄板或其他类似装置,随着圆筒体的转动,抄板或其他类似装置不断地把物料扬起又洒下,使湿物料的接触表面增大,提高干燥速率,并在重力作用下,物料顺着圆筒体倾斜方向往出料口方向移动,尾气则经过分离器和除尘器净化后排出。
污泥转筒干燥有直接和间接两种,湿污泥与干污泥混合后送入直接干燥转筒内,转筒转速5~8r/min,抄板翻动混合污泥,并与热气流(1.2~1.3m/s、649℃)混合接触,经20~60min干燥得到含水率低于10%的干污泥。而在间接转筒干燥中,蒸汽或热油则在中空的套壁内流动,同时将热量通过受热壁传至污泥,使污泥受热干燥,其干燥效率随着筒体内部温度和污泥停留时间的增加而增加,而随着污泥量增大而降低。
转筒干燥生产能力大,适用范围广;除蒸汽管式转筒干燥外,热效率低;物料在干燥器内停留时间长,且物料颗粒之间的停留时间差异较大;混合污泥的含水率需控制好,否则污泥在抄板或壁面上,很难脱落,使干燥无法进一步进行。
2.2 卧式桨叶式干燥
卧式桨叶干燥是一种以热传导为主的干燥器,其主要结构为带有夹套的W型壳内装有成对的空心低速回转中空轴,轴上焊接若干搅拌空心桨叶,夹套和空心桨叶内均通以热载体,2个加热面同时对物料加热,随着回转中空轴旋转,干物料会在桨叶推动和重力的联合作用下,向出料口方向移动。
徐小宁等得出,在相同的导热油(或蒸汽)温下,回转空心轴提速2倍后,污泥的出口含水率由42%上升到60%。而当回转空心轴的转速一定时,导热油的温度从160℃上升到200℃,干燥机出口污泥的含水率由54%下降到32%。所以回转中空轴的转速和导热油(或蒸汽)的温度对出口污泥的含水率有重要的影响。
卧式桨叶式干燥产物粒度均匀;热介质可重复使用;干燥颗粒运动规律性强,对器件磨损较小;可根据桨叶干燥能力的大小对污泥进行分类干燥。但污泥卧式桨叶式干燥存在较大死角,干燥机限定了有效容量,以及胶污泥粘壁、转轴寿命不长等问题。
2.3 流化床干燥
流化床干燥原理是将物料颗粒放置于内部多孔分布板上,并由底部输送热气体,使物料颗粒呈现悬浮状态,物料颗粒与热气体充分接触,促使物料与气体之间进行热传递与水分传递,干燥后的物料从出料口收集,废气则经分离器分离其挟带的粉尘后排放。
侯凤云等将污泥与河砂混合后进入流化床干燥,得出当床料河砂处于临界流化状态时,污泥的干燥速率较低,当流化速度增加到2倍时,河砂充分流化起来后,污泥的干燥速率增加,此后再增加流化速度,污泥的干燥速率没有明显变化,这表明当床料达到充分流化状态后,流化速度对干燥速率没有明显影响。
流化床干燥器内颗粒的停留时间可任意调节;气流速度小;物料与设备的磨损较轻,压降小;传热面大,物料的含水率低;但因颗粒在床层中高度混合,可引起物料的短路、返混和尾气分离复杂问题。
3 改进的污泥干燥工艺与设备
含水率高的污泥在干燥过程中有一个特殊的胶粘阶段(含水率约为40%~60%),出现污泥表面易结块,而内部却是稀泥的“糖心现象”。此时,污泥与介质间的传热传质效率低,导致干燥时间长,能耗高,干燥效果差。因此,单一形式的干燥,往往达不到质量要求,或者虽达到质量要求,但是干燥时间长、耗能大、干燥效果差。所以采用把2种或者是2种以上的不同(或相同)形式的干燥器串联组合起来,充分利用各自干燥器的优点,优化操作过程,降低能耗,提高干燥污泥的质量和经济效益。
3.1 多级卧式桨叶式组合干燥
多级卧式桨叶式组合干燥是在卧式桨叶式干燥的基础上开发出来的。典型的有污泥两级卧式桨叶式干燥,湿污泥通过一级卧式桨叶式干燥后,变成半干污泥,然后进入二级卧式桨叶式干燥内,再次干燥,经二级干燥后的干污泥送到污泥焚烧锅炉进行焚烧。产生的蒸汽用于半干污泥的干燥。经二级卧式桨叶式干燥后的尾气以蒸汽形式存在,经旋风除尘后进入第一级干燥机内,对湿物料进行预干燥,一级干燥后的尾气,经洗涤塔洗涤后被送到污泥焚烧锅炉中参与燃烧,防止有害气体的排放。焚烧后出来的烟气经过洗涤分离塔和布袋除尘后从烟囱排出。
污泥的两级卧式桨叶式干燥用第二级干燥的尾气对污泥进行预干燥,充分利用能量;整个干燥系统封闭循环,干燥中产生的尾气直接被送到污泥焚烧锅炉进行燃烧,将有恶臭气味的成分燃尽,改善干燥环境。但还存在死角、污泥粘壁和转轴寿命短等问题。
3.2 过热蒸汽对流与传导联合干燥
过热蒸汽对流与传导联合干燥就是对流干燥与传导干燥2种干燥的联合,且热介质为过热蒸汽。湿污泥通过加料器进入一级以传导为主的干燥器内,其热介质来自于二级对流干燥所产生的多余过热蒸汽,经过一级传导干燥后的半干污泥送入二级对流干燥器内。一级干燥后的尾气经过分离器把气体和污泥颗粒分离开来,气体再经过冷凝器变成冷凝水,排入污水处理厂,而不能冷凝的气体收集后进一步处理。半干污泥在过热蒸汽对流干燥器内进行干燥,干燥后产生的气体经过分离器分离,分离的污泥粉尘经由排料器进入对流干燥器内,而分离后的一部分过热蒸汽通过风机、过滤器及加热器与蒸汽发生器产生的过热蒸汽混合后再进入对流干燥内,如此形成一个蒸汽气流回路;另一部分过热蒸汽通过节流阀进入一级传导干燥器,作为其热介质;符合要求的干污泥从二级对流干燥器的出料口进行收集。
污泥过热蒸汽对流与传导联合干燥实现了能量的梯级利用,能效率比单级高;过热蒸汽形成气流回路,提高了过热蒸汽热能的利用率;热介质为过热蒸汽,其具有节能效果显著、潜热可回收利用、传热系数大、无传质阻力、比热大、蒸汽用量少及无爆炸失火危险等优点,再者由于过热蒸汽温度高,能对物料进行灭菌消毒,有利于保护环境。但过热蒸汽干燥设备复杂,启动和停车时易产生结露现象;过热蒸汽干燥设备的材料如果选择不当易产生腐蚀或锈损现象。
4 结论
综上所述,传统的污泥干燥各有优缺点,而且发展至今技术已经比较成熟,相比之下多级卧式桨叶式组合干燥和过热蒸汽对流与传导联合干燥应用较少。由于过热蒸汽对流与传导联合干燥用水蒸汽为干燥介质,存在停车会出现结露难点,又因污泥日产量大,除设备检查维护停车外,设备连续不断运行,所以结露出现次数也有所限制;热介质为水蒸气,干燥机内不存在氧化、爆炸和着火危险,这与热空气干燥相比设备安全性高;蒸汽潜热可以通过冷凝回收,节约能源;蒸汽温度在水的沸点以上,能在干燥时对污泥进行高温灭菌、消毒、除臭;所以面对城市生活过程中产生的大量污泥,过热蒸汽对流与传导联合干燥有望实现标准化、规模化、产业化,并实现污泥干燥后尾气零排放的目标。