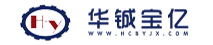
中国PCB行业一直在快速稳步发展,在全球PCB领域的影响越来越大。目前,中国PCB企业已进入世界100强,在国际上的竞争力越来越强。然而,在线路板废水处理过程中,因化学法技术成熟,成本低廉,故普遍采用化学法进行处理,通常用石灰、碱液、硫化钠等进行沉淀。化学法的应用会导致大量污泥的产生,因此,线路板废水处理后产生的污泥也在迅速增加。
根据检测统计,大部分线路板污泥经压滤机脱水后,污泥含水率约为65%~80%,重金属铜含量约为1%~5%,属于危险废物,在国家危险废物名录中的编号为HW22。然而其铜品味又远高于天然铜矿0.1%的金属品位,因此,线路板含铜污泥是属于可以开发的再利用资源。针对线路板污泥特性,如何实现线路板含铜污泥减量化、稳定化和资源化一直是国内外研究的重点。目前处置线路板含铜污泥的方法主要有热处理、化学处理、固化处理,但不管采用哪种方法处置,污泥的预处理是其后续处置及资源化再利用的关键。本文主要对双桨叶式干燥机在线路板企业含铜污泥处理中的干化应用进行分析。
1 双桨叶式干燥机简介
1.1 双桨叶式干燥机结构
双桨叶式干燥机主要由箱体、上盖、两根有叶片的中空轴、端盖、旋转接头等组成,主要部件为装在箱体中的两根相对转动的空心低转速回转中空轴和轴上排列的中空搅拌叶片,通热源后,不仅可以传热,还有搅拌的功能。
1.2 工作原理
利用热能将污泥烘干,干燥水分所需的热量由带有夹套箱体和中空叶片壁传导给物料,物料在干燥过程中,带有中空叶片的空心轴在给污泥加热的同时又对物料进行搅拌,从而进行加热面的更新。污泥从入泥口输进叶片将污泥边推进边搅拌烘干,干化的污泥从出泥口排出,干化后的污泥呈颗粒或粉末状,是一种连续间接传导加热干燥机。
2 工程应用
2.1 工程概况
珠海某电子有限公司,是一家专业生产单双面板和多层面板的高科技线路板企业,年生产能力在20万平方米以上。废水处理站设计规模为8000m³/d,废水处理目前主要采用化学处理法,废水处理所产污泥经板框压滤机脱水后平均每天产湿污泥9吨左右,含水率75%~80%,含铜率1.2%~1.5%。
2.2 工艺流程设计
2.2.1 进料和出料
用进料螺旋输送机将板框压滤机脱水后含水率在80%~86%的污泥送至烘干机的进料口,湿污泥经干燥机干燥后通过出料螺旋输送机输送至料仓。
2.2.2 加热
使用蒸汽作交换的热源,蒸汽温度为150~160℃,蒸汽被分别引入中空的烘干机壳体和传动的轴、桨叶等所有与污泥接触进行热交换的加热金属表面。
2.2.3 污泥干燥
加热后的金属表面与湿污泥均匀接触,加热污泥并蒸发污泥中的水分。沿烘干机的轴向长度,水蒸气蒸发会经历恒定蒸发和低蒸发率两个阶段,污泥的温度则呈快速上升→稳定→快速上升的趋势,污泥经塑化、破塑、块化、颗粒化4个步骤后达到所需烘干标准。
2.2.4 废气处理
污泥干燥废气采用喷淋塔处理,使所排放的废气达到除尘、除臭效果,符合环保所需排放要求。
2.3 工程主要设备选型
根据工程污泥处理量的需求,考虑到余量,干化系统每天运行7小时,本工程选用(1)处理量为10t/d双桨叶式干燥机,数量1台;(2)进料螺旋输送机:输送量Q=0.5t/h,数量1台;(3)出料螺旋输送机:输送量Q=0.5t/h,数量1台;(4)喷淋塔:φ800*H4500mm,数量1台;(5)加压风机:Q=3800m³/h,数量1台;(6)循环冷却水泵:Q=6m³/h,扬程10m,数量2台。
3 运行结果分析
3.1 进出泥质
本工程经板框压滤机脱水后,泥量为9t/d,即为干燥机进泥泥量,干燥机进出污泥泥质如下:
序号 | 泥类 | 含水率(%) | 湿基含铜率(%) | 污泥量(平均值)/(t/d) |
1 | 进泥 | 75~85 | 1.2~1.5 | 9 |
2 | 出泥 | 10~30 | 3~5 | 3 |
由上表可知,污泥含水率由75%~85%降至10%~30%,污泥量由9t/d减至3t/d左右,体积缩小4~5倍,大幅度减少了污泥体积,实现了污泥的减量化。同时,污泥湿基含铜率由原来不足2%升高到3%~5%,提高了污泥出厂的湿基含铜率。
3.2 二次污染控制
干燥机里的物料里含有水分、脂类、硫化物等多种不同物质,在热干化过程中,这些不同的物质沸点不同,随着温度的变化而成为固态或气态,因此不可避免的会产生二次污染,不但产生废液,而且产生少量影响环境的气体。
本项目中,污泥干化所产生的尾气均用管道密封收集,通过喷淋塔将尾气进行处理。高温尾气进入喷淋塔后,经喷淋清洗,水蒸气冷却形成冷凝水,粉尘、硫化氢等其它污染杂物则被喷淋液捕捉、吸收后形成废液,和热干化过程中产生的冷凝水一起排入现有污水厂处理达标后排放。净化后的达标尾气排入大气,有效控制二次污染。
3.3 经济计算
3.3.1 能耗
双桨叶式干燥机按加热介质可分为蒸汽型、导热油型和热(冷)水型。不管采用哪种加热介质,均是在两根空心轴和空心桨叶内通入导热介质,不同在于不同的介质需要配置相对应的旋转接头,蒸汽流动路线是上进下出,导热油型和热(冷)水型流动路线则为下进上出。能耗因加热介质不同而不同,本项目因厂内有蒸汽供应,为充分利用原有资源,节省成本,采用蒸汽作为加热介质,蒸汽耗量如下:
序号 | 温度(℃) | 过热蒸汽压力(MPa) | 耗量(kg/吨污泥) |
1 | 100~160 | 0.4 | 410~480 |
2 | 120~230 | 0.7 | 380~430 |
本工程实际运行中,选用压力0.7MPa过热蒸汽,据长期统计,每天干化污泥蒸汽耗量为3500~3700kg平均为3600kg。
3.3.2 成本
根据每天处理板框压滤机脱水后污泥平均9吨,干化一吨原污泥的蒸汽大约在400kg左右,每吨蒸汽按目前收费180元计算,则热能成本为:400kg*0.18元/kg=72元。
日处理量为10t/d的烘干机,每小时处理量为0.42t,烘干机用电量为8kW/h,可变频。整套烘干系统总功率为30kW,除烘干机外所需功率为30-15=15kW,运行时间约为22小时,每吨总耗电成本约为:(1÷0.42×8+15×22/9)=55.7元。
则每吨湿污泥处理成本约为:72+55.7=127.7元。
3.3.3 投资回收期
根据调研,对于线路板废水处理厂,通常污泥含铜率超过2%可以免费外运甚至外卖收费,本工程中原污泥湿基含铜率为1%~2%,烘干后含铜率提高至3%~5%左右。污泥烘干前外运费为1300元/吨,烘干后免费外运计算,则烘干后每吨污泥节省成本:1172.3×3=3517元/天。
本工程污泥干化项目总投资为531900元,因此投资回收期为:531900÷3517=151.2天,取整需要152天。
4 结语
双桨叶式干燥机在线路板企业污泥干化中的应用,不仅可降低污泥的含水率,实现了污泥体积的大幅度缩减,节约污泥的堆放空间,减少了污泥的输送量,而且提高了出厂污泥的含铜率,进一步满足含铜污泥的资源化需求,节省成本,投资回收期短。同时,二次污染容易控制,安全可靠。所以,对于实现线路板含铜污泥的减量化、稳定化和资源化,双桨叶式干燥机是一种较理想的污泥干化设备。