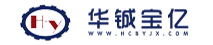
污泥是污水处理过程的衍生物,其成分以好氧微生物为主,同时包含污水中的泥沙、纤维、动植物残体等,根据所处理污水性质的不同,污泥中还可能包含有害金属、虫卵、病菌等对人体有害的物质,如果污泥不经妥善处理会对环境以及人体健康造成巨大危害。目前污泥的主要处置方法有填埋、焚烧、堆肥和土地利用,然而污水处理厂产生的污泥含水率高达80%左右,无法直接处理,因此污泥干化就成了污泥处置的前提。
污泥热干化是利用热能将污泥中的水分进行蒸发从而达到方便后续对污泥处理的一种方法。该技术早在20世纪40年代就已有应用,20世纪60年代发展成熟,但真正成熟地大规模应用于市政污泥处置是在20世纪90年代。污泥热干化技术的特点是集约化、机械化、减量化、无害化、稳定化、资源化。干化后的污泥产品呈粉末状或颗粒状,体积减小到原来的1/4,含水率降低到10%以下,并且很好地抑制了污泥中所含微生物的活性,因此干化后的污泥产品用途广泛,并且增加了污泥管理系统的灵活性和可操作性。目前欧美采用的干化工艺以转鼓干化、流化床干化、盘式干化为主,此外还有碟片式、带式、日光式、闪蒸式等干化工艺,但后面几种工艺在大型工程中用的很少。
1 热干化技术分类
热干化技术通常按照传热方式的不同进行分类。热干化技术包括直接干化(热对流)、间接干化(热传导)和直接-间接干化。
1.1 直接干化
在直接干化过程中,湿污泥与热气体(空气或水蒸气)直接接触,热气体为污泥中的水分蒸发提供热量,随后蒸发的液体被热气体带走。其特点是传热效率高,干化效果好。直接干化工艺较具代表性的是欧盟的英国Bransunds水厂(可蒸发水量为7×5000kg/h)。国内的大连、秦皇岛和徐州等地也对污泥直接干化工艺进行了深入研究。
1.1.1 转鼓干化技术
早在20世纪40年代美国、日本等发达国家已率先应用该技术对污泥进行干化。在该工艺中,脱水污泥进入污泥混合器与充分干化后的污泥进行混合形成含水率为50%~60%的混合污泥。混合污泥经螺旋传送机传送至转鼓干燥器,同时转鼓一侧通入温度700℃,流速1.2~1.3m/s的热气。热气直接与混合污泥相接触使污泥受热,经过25min左右处理后,污泥进入分离器,在这里排出的湿热气体被集中回收重复利用,热介质的重复利用率可达85%。污泥中的恶臭气体则被送到生物处理器进行达标处理。经过处理后的污泥干化率可达到85%~90%,污泥成颗粒状且粒径可控(粒径大约1~4mm)。污泥干化过程中无烟尘产生。该工艺中所使用的热对流介质一般为沼气、天然气或热油等燃料。
1.1.2 闪蒸式干化技术
闪蒸式干化机是集干燥、粉碎、筛选功能于一体的干化设备。热空气由通气入口沿切线方向进入干化机并成螺旋流上升,流速约20~30m/s,反混后的混合污泥由进料口进入干化机直接与热空气进行接触。较大的污泥颗粒在高速旋转搅拌桨的作用下被打碎,从而加大了与热空气的接触面积;较小的污泥颗粒随旋转气流上升并在气固分离器进行分离。整个干燥过程中污泥始终呈悬浮状态,干化时间仅为5~8s,污泥中水分蒸发迅速、彻底,干化后的污泥含水率可降低到8%~10%。早在20世纪30年代,美国就已经将该技术应用于污泥的干化处理,目前闪蒸式干化机的代表性生产厂家是美国ABB Raymond公司。
1.1.3 带式干化技术
带式干化机的主要工作部件为2条张紧的压滤带,污泥脱水时污泥被平铺在压滤带上,随着压滤带的传动,压滤带的张力对带上的污泥形成挤压剪切作用,从而产生含固率较高的泥饼,同时通以热空气进行干燥,热空气在鼓风机的作用下在干化机内循环流动,充分与泥饼进行接触从而实现污泥脱水过程。该设备的主要生产商为琥珀公司和德利满公司。带式干化技术在我国污泥处理中应用比较普遍,如深圳南山热电厂采用低温带式干化工艺,干化后污泥含水率为10%~40%。该技术蒸发强度高、干燥速度快、产品质量好,但产品为滤饼状物料,需要经后续加工方可使用。
1.2 间接干化
间接干化主要利用热传导效应,污泥不直接与热源接触,而是与通入高温加热媒介(通常为蒸汽或热油)的金属管外壁接触将污泥中的水分蒸发掉。间接干化的典型例子为世界上规模较大的间接加热污泥干化厂——西班牙巴塞罗那城市污泥干化厂,其每小时干化污泥量可达到20000kg。
1.2.1 转盘干化技术
转盘式干化机主要由贯穿整体的空心转轴和圆筒形状的定子组成,转轴上布满中空转盘,热介质被注入中空转盘,热量通过转盘外壁传递给圆筒中的污泥,使其受热,水分蒸发。转盘采用双面传热设计,可以在很小的空间内形成较大的换热面积,提高换热效率,同时转盘的缓慢转动(转速约为3~5r/min)可以使污泥向指定方向流动并起到搅拌的作用。设备外壁有固定的刮刀,可以将2个盘面之间的污泥刮去以免造成堵塞。受传热影响,从污泥中蒸发出来的水蒸气向转盘上方的穹顶聚集并从通风口排出干化机。该技术可采用低温热源加热(≤180℃),热介质可采用蒸汽或热油,由于所需空气量少,因此所产生的尾气量也少,减轻了环境污染。
转盘干化技术应用较早,具有代表性的工程实例有:荷兰SNB污泥干化焚烧站,干化后污泥含水率在50%左右;德国德雷斯顿污水处理厂,干化后污泥含水率在10%左右。
1.2.2 多盘干化技术
干化机内分布有大小不同的转盘,转盘呈交替垂直排布,通过循环热油加热。脱水污泥(含固率25%~30%)在涂层机内与湿污泥混合,脱水污泥被湿污泥包裹在中间形成干燥内核。随着圆盘转动,污泥颗粒由造粒机顶部向造粒机底部移动,移动过程中污泥颗粒得到干化。由于污泥颗粒在转动的同时直接与加热表面相接触并且颗粒逐盘增大,因此多盘工艺也被称为“珍珠”工艺。该技术在20世纪70年代就已经被应用到污泥的干化处理当中,并且在欧美地区应用较为广泛。
1.2.3 桨叶式干化技术
桨叶式干化机的壳体和桨叶都采用中空设计,热空气或热油被注入到壳体和桨叶当中使外壳和桨叶得到加热,污泥进入干化机内部与外壳和叶片接触受热并得到干化。由于叶片的连续转动对污泥进行连续切割搅拌,使污泥上下翻滚均匀受热,于此同时,桨叶的搅拌作用可以推动污泥向出料口方向移动从而实现连续运转。由于桨叶式干化机中部没有固定刮泥刀,因此对于黏性较大的污泥处理效果不是很好。
该技术应用较为成熟,也是较早传入我国的干化技术之一。目前国内主要代表生产商有三原重工、苏州自动化工等公司。绍兴中环能源有限公司采用该技术对日产量500t的污泥进行处理,处理后污泥含水率为40%。
直接干化和间接干化各有优缺点,其对比如下:
干化类型 | 能耗 | 粉尘量 | 尾气排放量 | 运行成本 | 干化效率 |
直接干化 | 大 | 高 | 高 | 高 | 高 |
间接干化 | 小 | 低 | 低 | 低 | 低 |
1.3 直接-间接干化
1.3.1 流化床干化技术
流化床干化工艺通过流化的高温气体和通入热油的加热管对污泥进行干化,流化床干燥器包括一个底部多孔的固定立室,热气体(通常为空气或者蒸汽)在立室内部流动。脱水污泥通过进料器进入圆形干燥器。在流化床中,气体与污泥处于交叉逆流状态,气体作为高效热交换介质,而污泥中的水分则在流体运动中得以蒸发,干化后的污泥经干污泥斗以颗粒状排出。废气中的小部分粉尘在旋风分离器中回收,进入污泥进料斗。气体经过湿式洗涤器净化并部分冷却后由烟囱排出。
流化床干化工艺所使用的惰性材料一般为石英砂或者矿渣。载热体温度为500~600℃,干燥时间为10~15min,污泥干燥温度为300~900℃,燃烧室的气体温度为800~1100℃。加热到如此高的温度需要大量热量,因此,系统需配备能量回收设备。
该工艺的主要优点是干燥时间的可控制性和高强度的热传递,流化床干燥器均为固定部件,设计简单。其缺点是废气中的粉尘含量高,大概为0.6~0.7g/m³。目前该流化床干燥器的主要生产商为德国WABAG公司和安德里兹公司。我国上海石洞口污水处理厂和北京清河污水处理厂所使用的污泥干化工艺就是流化床干化工艺。
1.3.2 涡轮薄层干化技术
在干化机内,含水污泥在高速转动的桨叶所形成的漩涡的作用下在反应器内壁形成物料薄层,该薄层以一定的速度从进料口向出料口移动,在此过程中,污泥通过与被热介质加热的干化机衬套及干化机内的热蒸汽接触而得到干化。污泥颗粒、蒸发气体和其他气体在气旋分离器中被分离出去。经过该工艺处理后的污泥含固率在60%左右。该技术灵活性高,无污泥反混,换热效率高,气体排放量少。
2 污泥热干化技术性能分析
2.1 能耗分析
污泥热干化的能耗主要指热能消耗和电能消耗,能耗支出占整个标准化工艺运行成本的80%以上,因此能耗分析是热干化工艺的重点指标。
2.1.1 热能消耗
污泥热干化工艺中热能的消耗主要包括污泥升温和水分蒸发所需的理论热能以及系统自身的热能损失。造成热能损失的主要因素有:
(1)热源的类型及污泥运输、存储和利用条件的不同,热损失会不同。无论是热传导还是热对流均会在换热过程中产生一定的热损失,一般热损失为8%~15%,且这部分热损失很难再降低。由于污泥的复杂性,加热方式采用间接加热方式,另外污泥运输中管线粗细、运输距离、运输压力等均会对热损失产生影响。因此为了减少热损失应该注意热源和换热器的选择与组合,尽量短距离运输并且注意保温。
(2)污泥颗粒自身性质不同,所消耗的热能不同。进料污泥粒度、黏度各不相同且污泥含水率较高,因此常常采用干泥返混工艺对其进行处理,然而在处理过程中污泥颗粒的反复加热和冷凝会导致大量的热损失,因此合理降低产品含固率、改善冷凝条件可以有效减少热损失。
(3)干化工艺不同,热损失不同。污泥含水率较高时,间接干化技术干化效率较高,但是难以将污泥中20%~30%的水分去除。对于含水率小于50%的污泥,直接干化技术的干化效率要高于间接干化技术的干化效率。此外,半干化热能消耗要低于全干化热能消耗。因此减少干化工艺步骤,缩短工艺线路可提高干化效率,减少热损失。
2.1.2 电能消耗
电能消耗主要指干化工艺中干化系统、污泥运输、存储以及安全控制、照明等系统所消耗的电能,其占干化总成本的20%左右。
2.2 安全性分析
对干化工艺安全性具有重要影响的因素主要有粉尘含量、工艺允许含氧量、颗粒温度(点燃能量)和含湿量4个方面。
2.2.1 粉尘含量
污泥在运输、筛分、存储等过程中会产生大量粉尘,由于这些粉尘粒径较小、比表面积较大,因此极易燃烧和爆炸。不同干化工艺所产生的粉尘量不同,同一干化工艺在不同的步骤当中所产生的粉尘量也不同,一般认为粉尘达到爆炸质量浓度的下限为60g/m³(以粒径小于150um的粉尘颗粒为例。间接干化工艺气体量较小,粉尘含量低,相对于直接干化工艺更安全。有效控制干化过程中的粉尘产生量是安全生产的重要保障。
2.2.2 工艺允许含氧量
由于粉尘颗粒较小且很难进一步减少污泥干化过程中的粉尘产生量,因此在含湿量、温度及粉尘含量不变的情况下,降低干化系统中的含氧量成为避免安全事故的有效手段。一般要求工艺中氧气含量不得超过12%。对于含氧量较高的工艺常采用惰性气体对氧气进行稀释,常用的惰性气体主要有水蒸气、二氧化碳、氮气和烟气。
2.2.3 颗粒温度(点燃能量)
污泥粉尘的点燃能量很低,从几毫焦到几百毫焦不等,当粉尘含量和含氧量满足要求时,任何细小的火花都有可能造成粉尘的爆炸。通常当干化体系温度为85℃时,点燃能量在100mJ左右,而且该点燃能量无法消除。
2.2.4 含湿量
干化系统含湿量越高,气体惰性化程度越高,则粉尘颗粒的点燃能量和爆炸下限也越高。当含湿量达到一定程度时,即使粉尘含量及含氧量很高,粉尘也不会发生爆炸。所以含湿量是评价工艺安全的一个重要因素。
2.3 环境友好性分析
污泥中含有许多有毒有害物质,其性质不稳定,易腐烂挥发,在污泥干化过程中容易造成二次污染。其中苯及其化合物是污泥干化过程中所释放的一类重要污染物质。根据污泥挥发气体释放试验,污泥中具有毒性的苯、酚类化合物的挥发温度在200℃以上,值得注意的是,二甲苯的挥发温度在150℃左右,且随着干化温度的升高,其挥发量逐渐增加。因此,为了降低有毒气体的挥发量,应该尽量降低污泥的干化温度,干化工艺尽量选择采用闭路循环设计的间接加热技术,对于直接加热干化工艺尽量采用气体循环回用设计。尽量减少外排的废气量,并且对外排气体进行必要的处理。
2.4 灵活性分析
污泥热干化技术的灵活性指的是热干化技术以高效、稳定地满足污泥干化产品为前提,对原污泥初始含水率的适应能力。由于污泥来源不同,污泥初始含水率、粒径、颗粒黏度及污泥中有毒有害物质各不相同,因此不同污泥干化工艺对不同的泥质有一定的针对性,比如多盘干化工艺和闪蒸式干化工艺等无法直接处理含水率较高的初始污泥。因此应合理选择组合工艺对污泥进行处理以达到高效、稳定、长期的发展目标。
此外,由于污泥产品的用途不同(堆肥、建材利用、焚烧、土地利用等),对于干化后污泥含水率的要求也不尽相同,因此应该充分遵循“以处置定干化”的原则选择适当的污泥热干化处理工艺来对原污泥进行处理。
3 结语
污泥热干化技术作为一种较为成熟的干化技术,以其处理效果好、处理周期短、处理规模大、成品安全卫生等优点,成为主流的污泥干化技术。在进行污泥处置的同时结合能耗分析、安全性分析、环境友好性分析和灵活性分析,并结合中国国情合理选择热干化工艺,达到污泥处置的资源化、无害化、减量化、稳定化目标,真正实现变废为宝。并努力改进传统污泥热干化技术,提高处理效率,开发新技术,提高传热效率。