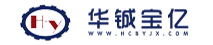
在污水处理过程中,活性污泥是常见的工艺,活性污泥法的基本原理是利用微生物在污水中的有机物分解成CO2(好氧工艺)或CH4(厌氧工艺)和水的同时、自身也得到不断繁殖增长,即剩余污泥是活性污泥法的必然产物。剩余污泥不能得到妥善处理将会产生二次污染,因此,剩余污泥的处理决定了污水处理工艺是否完善。利用离心、带式压榨、板框压榨等工艺将剩余污泥脱水后,再经过干化处理后填埋或焚烧是一种很好的污泥处理途径。
1 干化工艺简介
在天津100万吨/年乙烯及配套项目建设中,新建了一套污泥干化装置,属于配套环保设施。装置由湿污泥输送及储存系统、干化系统、干泥输送及储存系统等几部分组成,采用薄层干燥工艺处理污水处理装置产生的剩余活性污泥。
2 湿污泥进料及储存
含水率为85%的脱水后活性污泥,用卡车运送至现场后卸入活性污泥料仓。湿泥储存设活性污泥料仓两座,每座容积100m³,均为全地下料仓,料仓下部设有滑架和螺旋给料机,滑架受液压装置驱动,在料仓的平底上往复运动,将仓内湿污泥平稳地推送入螺旋给料机。螺旋给料机为有轴双螺旋,可产生足够的挤压力,将湿污泥压入污泥输送泵。污泥输送泵为螺杆泵,共2台,可将湿污泥送到干化系统。料仓顶部设有臭气风机,将料仓内的恶臭气体抽出送至位于污水场内的催化燃烧脱臭系统。
在控制上,湿泥料仓不仅设置了保证自身安全的仪表和控制程序,还和干化机的运行有互为因果的控制程序。比如,当两个储料仓都装满后,系统会给出报警信号,通知操作员停止继续卸料;这时,装卸料舱门不能打开,喂料螺旋和输送泵不能启动。在运行一段时间、当一个存储料仓排空后,系统自动切换到另外一个料仓。当两个料仓都排空后,向干化系统发送连锁信号,由干化系统的控制系统判断干化机停机时间。另外,在脱水活性污泥料仓装有料位检测传感器和硫化氢气体检测传感器。在此料仓装满的情况下,给系统发出报警提示,通知操作员停止卸料,装卸料仓舱门不能打开。当检测到硫化氢气体超标,给系统发出报警提示,装卸料仓舱门不能打开,同时给臭气风机信号,风机启动强制排风将硫化氢排出。
3 污泥干化单元
3.1 设计能力数据
干化机设计额定蒸发量为1000kg/h,折合设计处理含固率为15%的脱水污泥量为1250kg/h,设计干化后污泥含固率为75%,干化污泥量为250kg/h。同时,考虑了一定富余能力,设计蒸发量可以达到1200kg/h,即处理含固率为15%的脱水污泥量为1500kg/h,相应含固率75%干污泥300kg/h。
3.2 热源及其他配套条件
加热介质为饱和蒸汽,正常入口蒸汽压力0.8MPa,入口蒸汽温度180℃。至于其他公用工程条件,除了电外,还需要新鲜水和二沉池出水作为冷却水、氮气作为保护气和一定量的仪表风。污泥干化过程中,从气体洗涤和冷凝段排出的具有需要进行处理的污水,还要排出一些空气与不可凝工艺气体组成的废气。
3.3 工艺流程简述
在污泥干化单元,活性污泥被干燥至含固率约70%~75%,工艺过程可分为污泥干化、干化产品输送、工艺气体冷凝及排放等三个部分。
(1)污泥干燥器
污泥的干燥是基于涡轮技术,污泥通过单螺杆泵被送到卧式圆柱体涡轮干燥器的喂料仓,再由双螺旋以1m³/h左右定量送入涡轮干燥器。干燥器的污泥入口也是工艺气体的入口,即工艺气体与污泥在干燥器内同向运动。污泥进入干化机后,涡轮转子将其高速离心到内壁上,紧贴着圆柱形的内壁形成一个薄层,这种薄层可以得到很高的换热效率和热利用效率。污泥在干燥器内很强的涡流作用下,紧贴着圆柱形的内壁,连续地移动和很好地混合。
干燥器内的热交换主要是依靠污泥与圆柱形容器同轴的夹套中的蒸汽热传导实现的,经过预热的循环气体进入干燥器后对污泥起到输送和辅助加热的作用。预热气体在干燥器内与污泥的接触、并流运动,不会引起污泥的化学分解。事实上干燥器的进口处的热气体与高含湿量的冷产品接触,可以避免干泥的过热。污泥在涡轮干燥机中的停留时间很短,因此干燥器内的干泥量只有数十公斤(根据工作状态略有变化)。涡轮的外缘的旋转速度大约在20~30m/s之间。即使发生突然断电,整个工厂停顿的情况下,旋转涡轮的机械惯性也可以保证涡轮干燥器基本清空,避免了干燥器内因留存物料而影响设备重启,从而保障系统安全。
干燥器涡轮是由旋转轴和镀有耐磨材料的特殊形状的桨叶构成。涡轮安装在两个法兰连接端板中心线上的悬架轴承上。涡轮支撑和转动的轴承组安装在蒸发室外,因此没有污损和过热的风险。干燥的污泥离开涡轮干燥器后,与水蒸气一起进入分离段,通过旋风分离器进行固体和气体的分离。
(2)气固分离
经过涡轮干燥器干化的污泥和工艺气体一起进入旋风分离器,旋风分离器外部进行绝热处理以避免蒸汽产生冷凝。在旋风分离器内固形物和气体因密度差别而被分离,干燥后的污泥产品被收集在底部,而气体从顶部离开。在旋风分离器中收集的细颗粒落入具备冷却功能的螺旋输送机,约100℃的干化污泥被冷却至40℃以下,再提升到干泥料仓。
旋风分离器出口的工艺气体被送往湿法除尘器进行粉尘分离,除尘器装备外部进行绝热处理以避免蒸汽产生冷凝。气体从立式静态分离器底部进入,与填料接触产生聚结,固体被从气相中分离出来。洗涤水由顶部喷入,捕捉固体和液体物质,并起到对填料进行清洁的作用。液体/固体混合物收集在底部,液态物收集在底部由离心泵循环回到除尘器以保证洗涤效率,浓缩的粉尘定时用泵排到废水池。
气相从顶部排出,捕雾器将气相流可能携带出的液滴去除后,工艺气体将重新回到闭环循环。循环工艺气体由离心风机抽取并循环到闭环干燥回路中,该循环气体被送入以蒸汽为热源的热交换器中,加热后的气体返回涡轮干燥器。
(3)工艺气体冷凝及排放
在湿污泥被干化的过程中,蒸发处理的水汽及气体挥发性气体必须及时从循环气体中分离出来,以实现系统的平衡的微负压。
由风机抽取的水蒸气和气体挥发性气体首先被引入冷凝塔进行冷凝,在冷凝塔内气体通过一个颇尔环填料层被水逆向淋洗,冷凝液被收集在冷凝塔底部,泵送到废水池。液体由离心泵循环输送至冷凝塔的顶部之前,通过板式换热器将循环液进行冷却。为节约水耗,冷却介质采用含油污水处理系统的二沉池出水。经过洗涤后的不凝气体,再进入除雾器处理后,用废气风机引至污水场的脱臭装置处理。
(4)工艺的控制
涡轮薄层污泥干化工艺的上述三个部分采用一套PLC对工艺进行自动控制。在基本条件设定后,可以通过在线仪器仪表,准确地实现对工艺的控制。
涡轮薄层的工艺控制主要是对干燥器出口工艺气体温度的控制。蒸汽进入换热器,加热工艺气体,使工艺气体不断升温。当达到设定工艺温度后,系统开始定量喂入湿泥,湿泥与热壁和热介质接触,产生蒸发。随着湿泥喂入量分步到位,干燥器出口温度稳定在一个合适的温度区间,该温度与产品含固率有较为准确的对应关系。干泥的含固率变化可以通过多种调节方式来进行,其中除了桨叶角度为冷机机械调整外,均为热机在线调整。因湿泥状况变化而需要作出的临时调整可由操作人员现场随时进行。
(5)运行安全的控制
干化系统的开机和关机均按照一个预先设定好的程序进行。开机的目标是在确保安全和温度合适的条件下,建立系统内的物料和热平衡。关机的目标是在确保安全和阻断湿泥进料的同时,实现干燥器的缓慢降温和冷却。
对避免臭气和粉尘泄漏到环境中,干化系统为微负压状态,但微负压可能造成周边环境中少量空气进入系统,使气体中氧含量增加。为确保工艺回路获得必要的惰性化,防止干化过程出现爆燃,污泥干化采用测氧仪作为安全运行监测的重要手段。工艺气体中的氧含量将设置两个探头连续监测,当氧含量超过限值时,将产生报警,安全用氮气进气阀将打开,在风机和换热器之间喷入氮气,直至氧含量减少到正常水平。当处于非常高位时,干燥工厂将会紧急停车,安全氮气阀将处于持续打开状态。
4 干泥输送及储存
冷却至40℃以下的干泥由提升机提升送入干泥料仓。干泥料仓容积为30m³,设置在户外。料仓底部装有破拱器防止污泥架桥,并有闸板阀,控制干泥的出料量。需装车时,打开闸板阀,干污泥经卸料机斜至车内。
在现场设控制按钮箱,可以手动操作设备的启动、停止。干泥料仓内装温度传感器和可燃气体传感器。当达到危险值时,启动氮气保护装置。打开氮气输送阀门并报警通知操作工。干泥料仓安装料位传感器,当仓位高时,向干化系统发出停车连锁信号并报警。同时干污泥提升停止运行。干泥料仓装有破拱器,当卸料时,卸料阀打开的同时,破拱器工作。
5 结论
天津石化污泥干化系统于2010年11月开工,2011年10月26日开始投料试车,12月12日~14日完成了性能考核。性能考核期间,此套装置实际处理污泥含水率11.3%的脱水污泥为1535kg/h,实际蒸发能力达到了1296kg/h,干化污泥产品的含水率为27.3%。目前,装置根据污水处理系统排泥量的多数间歇运行,即将湿泥料仓用脱水污泥装满后即投入运行,2012年每个月的运行时间都在10天以上。