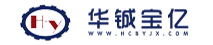
制浆造纸企业产生的污泥,成分较复杂,除水分外,还含有难以降解的有机物、重金属和盐类以及少量的病原微生物和寄生虫卵等,且常常伴有恶臭的气味,这类污泥很难通过沉降进行固液分离。其中的水分,按存在的形式大致分为四类:间隙水、表面吸附水、毛细结合水、颗粒内部水。
经过十几年的发展、实践,国内外污泥处理处置虽然在厌氧消化、好氧发酵(堆肥)、土地利用、制备活性炭等途径在污泥处理上取得了进展,但实践证明污泥的脱水、干化与掺煤混烧及制作环保砖等建筑建材是目前污泥资源化处置行之有效的方式,能真正实现其减量化、稳定化、无害化、资源化。
1 回转式滚筒干燥
工艺过程:
湿污泥(含水量75%以下)经输送设备送入干燥机之前的螺旋喂料机(料塞螺旋),将物料均匀地喂入专用干燥机,在此物料被预热、球化、干燥。系统所用烟气取自锅炉引风机后、脱硫塔之前。在干燥机内的烟气经过热交换后温度降低至约70℃,尾气进入助力风机之前先经过除尘,然后回到脱硫塔之前或经过烟气道直接放空。通过电动闸板阀和风机调节所用烟气量的大小。针对高温物料的特点,干燥机采用逆流干燥。
回转式滚筒污泥干化工艺具备以下特点:
(1)形成的污泥颗粒粒度均匀,大多在Φ5~Φ10mm,干度不低于70%。这样避免了粒度过小、干度过大造成的瞬间燃烧而不能保持连续性,也避免了过小的粒度产生大量粉尘。
(2)污泥颗粒由计量秤稳定计量后落入上煤皮带,混合均匀,避免了高温风送颗粒对设备和管道的严重磨蚀。
(3)滚筒干化所形成的颗粒比较稳定地将纤维吸附在成球中,低温出料。避免了风送污泥颗粒时,细小纤维和粉尘对后续布袋的堵塞而损伤布袋。
2 喷动流化床干燥
工艺过程:
锅炉除尘器后烟道里烟气(约140℃),由引风机切向引入旋流喷动干燥机。湿污泥经加料机送进干燥室内,与切向进入的高温高速旋转干燥烟气相撞击,使之微粒化并呈激烈的喷动流化状态。这样较大、较粘的湿污泥在干燥的同时由安装在干燥室底部的搅拌装置进行机械破碎。处于流化状态的污泥颗粒,由于增加了比表面积及气固间的传热传质系数,湿污泥中的水分被迅速地蒸发、干燥。干燥室底部采用喷动床技术,提高了干燥室底部的气速,以防较大污泥颗粒沉入底部堵住进风口。达到一定干度的干污泥颗粒被气流带出干燥室外,进入捕集系统(旋风和布袋除尘器)而被捕集。离开捕集系统的湿气体,再送入原锅炉除尘器经除尘与脱硫后进入烟囱排放。干燥过程控制参数为干燥室内的温度、差压及搅拌电流。调节方式为调节污泥加料机转速。干燥后的干污泥,输送进入锅炉燃烧。
3 流化床造粒干燥塔干燥
工艺过程:
系统所用热烟气取自锅炉引风机后、脱硫塔之前,热烟气由流化造粒干燥塔的上部进入,经布风装置后均匀地送入流化塔内。污泥料浆(水分约75%)由污泥泵输送,流量计计量,经喷枪装置喷入流化塔形成喷射状的雾化汽柱,与自上而下的热气流进行逆流接触,充分进行热交换,在料浆水分适宜、温度适合的状态下迅速成粒,且均匀撒落。在流化塔的中下部区域设有倒置的锥形布料器,在锥形布料器内部设有引风装置,干化后的物料经过此锥形布料器时在圆周环向上均布下落的同时,细小粉尘颗粒由引风装置引出塔外,经旋风除尘器及布袋除尘器回收。尾气进入湿法脱硫塔,随系统烟气排空,或经过烟风道直接放空。经锥形布料器下落的成品颗粒经流化塔底部的风机卸出。此处可设分级筛筛除大块及细粉,≤30%水分的成品由输送设备运走,或与煤混烧,或它用,成品粒径Φ3~5mm。
整套系统由PLC全程自动控制,所需烟气量的大小通过电动闸板阀和风机进行调节,由变频器及流量计控制污泥料浆的进料量,整套系统的生产过程由1人在控制室内监视即可。
整套系统具备以下特点:
(1)热利用率高,干燥强度大。
(2)制作成本及运作成本低。
(3)动力消耗低。
(4)原料适用范围广。
(5)占地面积小,运行稳定、可靠。
4 因地制宜选择污泥干化资源化处理处置工艺
根据企业自身条件及实际现场,建议选择切实可行的污泥处理方案:
(1)对无热源的用户,宜采用化学改性干化技术。该技术是通过向污泥添加适量生石灰,可使污泥迅速升温至100℃以上,短时间内蒸发大量水蒸气,达到干燥、脱水及杀菌目的。
(2)对有剩余蒸汽热源的用户,宜采用蒸汽滚筒、网带式或桨叶式干化技术。
(3)对有烟气热源的用户,宜采用回转式滚筒、喷动流化床、流化造粒干燥塔或网带式干化技术。
(4)对于新建项目,本着能量守恒、运作经济的原则,建议采取冷机械压榨脱水工艺及利用烟气余热脱水工艺相结合的方法。因为将污泥(约75%水分)浓缩至60%,此阶段的水分主要是游离水形态,便于采用冷工艺机械脱水,而不宜采用热能脱水工艺;60%水分的污泥浓缩至30%,此阶段的水分主要是表面吸附水、内部水的形态,还含有少量游离水,此段污泥宜采用热能脱水工艺。