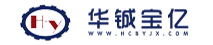
大庆油田第八采油厂肇Ⅰ站成立于1999年,经过多次改扩建,于2004年增加热化学脱水器2台,由中转站规模升级为联合站管理。担负6座站来液脱水、净化、外输的任务,目前每天处理量为4900m³/d。
1 集油系统硫化物的主要成因
一是清洗集油管线时,产生的老化油回收到肇Ⅰ联合站,含有大量硫化物及胶质。
二是注水井洗井产生的污水还有部分硫化物,经泄油台回收到肇Ⅰ联合站。
三是各转油站清淤产生的老化油及污水运送到卸油台,回收到肇Ⅰ联合站。
四是各小队回收的落地油,含有大量泥沙和微生物细菌等,经泄油台回收到肇Ⅰ联合站。
五是肇Ⅰ联合站内污水处理系统,回收速度较慢的老化油,和脱水效果差的老化油,反复系统中循环,慢慢滋生大量硫化物。
2 老化油对系统造成的危害
2011年9月份以来,由于肇Ⅰ联合站系统中存在大量硫化物,造成热化学脱水器运行不稳,外输含水严重超标,影响外输油含水指标。严重时,造成掺水系统含油过高,被迫停井循环,已经直接威胁到整个系统正常运行。由于硫化物始终在系统中循环,没有有效的处理方法,为了维持系统正常生产,站内不断把系统内老化油压入1000m³事故罐内临时储存,事故罐储存空间有限,系统面临停产危险。
3 离心除硫脱水技术原理与工艺
老化油处理设备的技术原理:通过来液泵将加热过的老化油输送到主处理工艺,辅助化学药剂,通过离心法,利用两级分离即卧式螺旋分离器和碟式分离器将油、水和硫化物杂质分开。卧式螺旋分离器主要用于除机械硫化物杂质,分离出来的机械硫化物杂质装袋环保处理。碟式分离器主要用于油、水精细分离,合格的油、水分别净化油罐和污水沉降罐,完成老化油脱水处理任务。
4 老化油处理方案制定
经过现场勘察和化验分析,肇Ⅰ联合站事故罐内老化油是含有大量固体物质的油水强乳化液,固体含量约为10%,主要成分以硫化亚铁为主的硫化物。水的含量约为40%,原油含量约50%。通过多次现场调查和方案优化,确定了试验方案,由超导车加热老化油,通过老化油离心脱水处理技术进行分离处理,分离出的净化油输至1000m³净化油罐,分离出的污水进污水沉降罐回掺,分离出的机械硫化物杂质现场装袋,进行环保处理。
5 现场试验情况
2012年2月26日,老化油处理设备进入肇Ⅰ联合站,按照拟定方案连接好油、气、水管道。由于老化油长期沉积,板结严重,没有流动性,现场配合3台锅炉车蒸罐加热。起初罐底污水加热较快,处理比较理想,从3月2日起,罐内污水基本处理完,开始出现老化油成块掉落现象,胶态硫化物和大量的杂质进入供液泵,很快将泵进口堵死,给现场施工带来麻烦。由于罐内老化油夹杂着泥垢含水低,流动变差,锅炉车加热困难,无法保证处理效果。通过综合研究,现场调整加热方案,用掺水反顶方式加热罐内老化油,采取边涮边处理方式,解决了加热难题。
6 除硫脱水实验效果分析
老化油共处理25天,累计处理液量1453m³,其中输出净化油727m³,分离出机杂145m³,净化污水581m³。处理后的净化油现场化验含水为2.1‰,污水水中含油16.5mg/L,均达到处理标准。
7 结论与认识
(1)本次共处理液量1453m³,成功回收好油727m³,处理完达标污水581m³,分离出机杂145m³,成功解决了困扰肇Ⅰ联合站多年的老化油问题。
(2)处理后的净化油含水达到3‰以下,污水含油达到50mg/L以下,可以直接外输与污水处理。
(3)分离出的机械硫化物杂质含油量小于1%,经过风化后可作为铺路材料使用,环保效益明显。