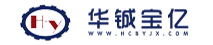
食品级磷酸是目前世界各国应用广泛的食品添加剂和食品级磷酸盐产品的主要原料,一般由工业热法磷酸经脱砷、脱重金属后制得。
1 食品级磷酸生产原理、工艺流程及主要设备
1.1 生产原理
食品级磷酸工业生产通常用H2S作为脱砷剂脱除工业磷酸中的砷和重金属。沉淀下来的As2S3(三硫化二砷)和PbS(硫化铅)经过滤除去,然后由空气鼓泡气提除去磷酸中残留的硫化氢气体即可制得食品级磷酸。
1.2 工艺流程
云南磷肥工业有限公司下属昆明宝益磷化工有限公司的3kt/a食品级磷酸装置采用传统的过滤盘过滤工艺,生产工艺包括反应、分离、曝气等过程。
工业磷酸和脱砷剂(硫化钠溶液)按比例加入带搅拌的反应釜中,然后流入溢流槽,砷和重金属离子在反应釜和溢流槽中与硫化氢进行反应,生成As2S3和PbS沉淀;将带有沉淀的酸悬浮液放入铺有硅藻土过滤层的过滤盘中,经真空抽滤送入循环酸槽,然后再用泵送入脱气塔,由空气鼓泡气提吹出酸中残余的硫化氢气体。脱除了硫化氢气体的酸即为成品食品级磷酸。反应釜、溢流槽、循环酸槽都设有夹套,用蒸汽加热,以保证物料有适当的反应温度。进入脱气塔的空气需先经蒸汽加热。
1.3 主要设备
3kt/a食品级磷酸装置的主要设备如下:
序号 | 设备名称 | 规格 | 材质 | 数量/台 |
1 | 反应釜 | 800L | 搪瓷 | 1 |
2 | 溢流槽 | 1500L | 搪瓷 | 1 |
3 | 循环酸槽 | 2500L | 搪瓷 | 1 |
4 | 脱气塔 | Φ325mm×4500mm | 316L | 1 |
5 | 风机 | qr=570m³/h | CS | 1 |
6 | 真空泵 | qr=5.3m³/h | GS | 1 |
7 | 过滤盘 | Φ1200mm | 316L | 2 |
2 传统工艺存在的问题
从装置整体来看,在反应、过滤和脱气三大系统中,除反应系统能满足设计要求外,过滤、脱气两系统仅能满足年产1kt的生产规模。其主要原因是:
(1)过滤盘生产能力严重偏低。经过生产现场考核,过滤盘的抽滤能力只能满足日产3t的需要,过滤强度仅为55kg/(㎡·h),远远低于185kg/(㎡·h)的设计过滤强度和日产10t的设计产能。
(2)脱气塔和脱气风机能力过小。经过生产现场考核,脱气系统能力亦仅能满足每日3t的需要。
从产品质量看,产品可以满足w(As)低于1×10-6的国标要求,但难于满足w(As)低于0.5×10-6的用户要求,原因在于过滤中未能除尽酸中的固体物质。
3 技术改造
食品级磷酸的产能不足已成为制约企业进一步发展的重要因素。因此公司决定在原有装置基础上进行技术改造,使装置食品级磷酸生产能力达到10kt/a,以满足生产经营的需要。
3.1 改造思路
从反应系统看,原反应釜+溢流槽容量为2300L,按反应停留时间2h计算,可达到日产量50t、年产量15kt,能满足食品级磷酸年产10kt的技改目标要求。制约装置产能的关键在于现有装置过滤和脱气系统能力不足,因此技改重点放在过滤和脱气工艺的改造上。
针对原过滤系统能力低的问题,考虑采用离心机过滤工艺替代原有的固定盘式过滤器过滤工艺。离心机一般应用于固液分离,特别是在水相和固相的分离中应用广泛。水相和固相分离,当固相颗粒较粗、液相黏度较小时,固液分离容易,离心机中仅需铺设滤布即可满足分离要求。含有砷渣的磷酸中虽然固含量相对较少,但砷渣主要是由大量又黏又细的被还原硫黄和少量的三硫化二砷、重金属硫化物组成,并且磷酸还具有腐蚀性,因此过滤操作较一般的固液分离困难,离心机中除铺设滤布外还须铺设硅藻土作为主过滤层。由于离心机过滤具有生产强度大、占地少、投资省以及不需要真空系统等优点,决定在原食品级磷酸生产装置的技改中设置3台离心机,具体实施时先建1台,取得经验后根据实际情况再续建2台。
针对原脱气系统生产能力过小的问题,改造中决定不再利用原脱气系统,采用因过滤工艺改变而闲置的真空泵和循环酸槽组成新的脱气系统,设备容量和气量都比原来增加几倍,完全可以满足改造后的脱气需要。
3.2 技改后食品级磷酸生产工艺
原料磷酸槽中的工业磷酸首先用泵送入高位酸槽,经计量后按比例与硫化钠溶液(P2S5与NaOH反应制得)一起被送入反应釜,搅拌反应后进入溢流酸槽,反应完成后溢流进入中间酸槽,然后进入离心机过滤。过滤后如果得到的是清亮酸则流入清酸槽,如果酸液混浊则进入浑酸槽;清酸槽的清酸用泵送入高位重力过滤器,除去可能存在的机械杂质,然后进入循环酸槽,经空气鼓泡脱气检验合格后,被送入成品酸槽待用。溢流酸槽中沉降的砷渣定期排入砷渣过滤器,由真空泵抽滤,以除去积存的砷渣,避免大量砷渣从溢流口流出,影响离心机过滤,砷渣被抽干后排出装置堆存,抽出的酸返回系统。
3.3 离心机工艺技术条件探索
3.3.1 硅藻土粒度的选择
硅藻土的粒度规格很多,选择合适的粒度配比对生产工艺控制很重要。原过滤盘工艺中采用较粗的硅藻土,且要求铺设的滤层较厚。改造后采用离心机过滤,由于操作过程中物料运动易对硅藻土滤层造成破坏,决定采用腾冲产TD-1型(细型)和TG-1型(粗型)硅藻土进行配合使用。经过多次摸索找出了适宜的配比:TD-1型硅藻土占35%~60%,TG-1型硅藻土占40%~65%。
3.3.2 硅藻土滤层厚度的选择
通过测定硅藻土滤层厚度变化对产品酸清亮度、离心机过酸能力以及对滤层损坏情况的影响来确定合适的硅藻土厚度。测定极限条件以离心机过酸能力因酸不能通过而造成离心机振动计,用w(H3PO4)85%的磷酸测试。经过反复比较,硅藻土滤层厚度8~19mm较为适宜。
3.3.3 滤层铺设方式
离心机内件为内空转鼓,为保证离心机硅藻土主过滤层具有一定的机械强度,稳定而不易破损,必须按照一定的方法铺设滤层。铺设时首先在转鼓内铺设一层耐酸滤布,该层滤布要求严格按照转鼓的尺寸认真缝制;在完成内层滤布的铺设后启动离心机,匀速加入用磷酸、硅藻土悬浮液,利用离心机的离心力将硅藻土密实均匀地铺在滤布上形成滤层,滤层厚度控制在8~19mm;铺设硅藻土层后,再在硅藻土层上铺设一层滤布,其作用是使过滤时产生的砷渣多数沉积在该层滤布上,便于清理;用不锈钢丝网作为支撑。
3.4 主要设备
本次技改尽量利用原有设备以降低技改投资。新增主要设备只有Φ800mm及Φ1000mm离心机2台。第一台Φ800mm离心机安装后实测生产能力就已达到3kt/a。在取得了实际操作经验后,续建了第二台Φ1000mm离心机。第二台离心机投运后经现场实测,以w(H3PO4)75%磷酸为原料生产食品磷酸的能力已经达到了10kt/a。
3.5 主要工艺控制指标
改造后主要工艺控制指标:
(1)脱砷剂用量为按工业磷酸中砷含量计算的理论用量的2~2.5倍,脱砷剂w(Na2S)7%~8%;
(2)反应温度60~75℃;
(3)脱气温度60~65℃;
(4)脱气时间4~6h。
3.6 分析控制
(1)原料酸:应成批取样分析浓度、色度、砷含量和易氧化物含量。
(2)中间控制:在清酸槽中取样进行色度的定性分析和砷含量的定性分析。
(3)成品酸:按国标进行全分析。
4 技改效果、存在问题及应对措施
4.1 技改效果
该装置技改完成后,经过1年多的运行,生产稳定,生产能力大幅度提高。经测算,技改后w(H3PO4)85%食品级磷酸年产能达6kt,w(H3PO4)80%食品级磷酸年产能达9kt,w(H3PO4)75%食品级磷酸年产能达10kt。过滤和脱气能力都达到设计要求。同时产品质量提高,w(As)可控制在0.5×10-6以下。
4.2 存在问题及应对措施
(1)运行中发现溢流槽砷渣有时会翻滚,带出的过多砷渣增加了离心机的运行负荷,降低了过滤能力,严重时必须暂停离心机,不能完全实现连续运行。因此,考虑再增加1台溢流槽进行并联交替操作,这可保证离心机完全连续运行。
(2)装置产能弹性不足的问题突出,一旦其中一台离心机出现故障就会影响整个生产,因此考虑有必要再增加第三台离心机。
据初步估算,装置在完成上述两相改进后,生产能力还可在现有基础上再提高30%~50%,而且整个装置的操作弹性将大幅度提高,装置应对突发事故的能力将大大增强。