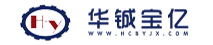
空心桨叶干燥机是一种以热传导为主的卧式搅拌型干燥机。因内部空心的搅拌叶片形似于船桨,固称之为空心桨叶干燥机。桨叶干燥机国外已经开发多年,由德国开发成功,之后我国引进了该项技术,并进行了改进,现已开发了双轴和四轴两种结构、十多种规格的系列产品。近年来国内各行业的广泛应用,国产桨叶干燥机技术已经十分成熟。
某厂油渣萃取项目作为新型技术,物料性质具有特殊性。由于其自身高黏度特性,干燥机还没有相关业绩。针对该物料性质,通过实验验证桨叶干燥机对高黏度物料的可行性进行了验证,为桨叶干燥机应用提供更广阔的领域。
1 桨叶干燥机原理
空心桨叶干燥机是由互相啮合的二根或四根桨叶轴、带有夹套的W形壳体、机座以及传动部分组成,物料的整个干燥过程在封闭状态下进行,有机挥发气体及异味气体在密闭氛围下送至尾气处理装置,避免环境污染。干燥机以蒸汽,热水或导热油作为加热介质,轴端装有加热介质进出的旋转接头。加热介质分为两路,分别进入干燥机壳体夹套和桨叶及轴内腔,将壳体和桨叶轴同时加热,以传到加热的方式对物料进行加热干燥。被干燥的物料由螺旋送料机连续的送入干燥机的加料口,物料进入干燥机壳体后,通过桨叶的转动使物料翻转、搅拌,不断更新加热介面,与壳体夹套和桨叶接触,被充分加热,使物料所含的表面水分蒸发,蒸发水分通过气相出口连续排出。同时,物料随桨叶轴的旋转成螺旋轨迹向出料口方向输送,在输送中继续搅拌,使物料中渗出的水分继续蒸发。干燥均匀的合格产品由出料口排出。
干燥机空心轴上密集排列着楔形中空桨叶,热介质经空心轴流经桨叶,循环加热。单位有效容积内传热面积很大,热介质温度为-40~320℃,可以是水蒸气,也可以是液体,加热水、导热油等。通过间接传导进行加热,热量均用来加热物料,热量损失很小,仅为通过气体保温层向环境的散热。楔形桨叶传热面具有自清洁功能,物料颗粒与楔形面的相对运动产生清洁作用,能够除去楔形面上的附着物料,使物料在运动中一直保持着清洁的传热面。
2 桨叶干燥机的应用
随着国内各行业的发展,桨叶干燥机已成功地用于食品、化工、石化、染料、工业污泥等领域。设备传热、冷却、搅拌的特性使之可以完成以下单元操作:煅烧(低温)、冷却、干燥(溶剂回收)、加热(融化)、反应和灭菌。
(1)用导热油做加热干燥介质,桨叶干燥机可完成低温煅烧工作。如:二水硫酸钙(Ca2SO4·2H2O)煅烧转化为半水硫酸钙(Ca2SO4·1/2H2O)。碳酸氢钠(NaHCO3)经煅烧转化为纯碱(Na2CO3)等。
(2)通入冷却介质,如水、冷却盐水等即可用来冷却。如用纯碱行业的桨叶式凉碱机取代老式的空气冷却凉碱机,节省了能源及尾气处理设备,降低了操作费用,还可用于钛白粉、镍铁合金粉及各种粉粒状物料的冷却。
(3)干燥,桨叶干燥机应用较广泛的用途,不使用热空气,使溶剂回收、能源消耗、环境控制处于易处理的理想状态。对需回收溶剂、易燃易氧化热敏性物料尤为适应,已广泛用于精细化工、石化、染料行业。
3 干燥机的特点
3.1 设备结构紧凑
干燥机主要的传热部件是壳体夹套、轴、楔形的桨叶,这些密集的桨叶按照规定的间隔交叉排列在固定的旋转轴上,因此单位容积的传热比较高。基于这一原因,这种设备的结构非常紧凑,占地面积小。
3.2 传热效率高
由于相对旋转的楔形的桨叶和倾斜的桨叶表面以及机体的加热、冷却,保证了所有与产品接触的表面能够均匀地传递热能。物料充分混合搅拌,干燥机本体热量损失很小,热量利用率高,提高了设备的传热效率。
3.3 自洁性能
桨叶具有自洁能力。桨叶相向旋转,叶片的两个斜面反复搅拌、压缩、松弛并推进物料,使叶面具有独特的自洁能力,防止物料在桨叶轴与轴间累计黏结,影响干燥机正常运行。同时桨叶干燥机的传热系数也高于其他任何传导干燥方式。
3.4 处理物料范围广
使用不同热介质,既可处理热敏性物料,又可处理需高温处理的物料。常用介质有水蒸气、导热油、热水、冷却水等。既可连续操作也可间歇操作,可在很多领域应用。
3.5 控制简单
干燥过程和停留时间都可以检查、控制和调整。它们都可以根据被干燥产品的物理性能单独进行设定和调整,对轴或者桨叶的数量、转速、传热体的温度和干燥停留时间进行设定和调整,达到干燥效果。
3.6 适合于湿度很大产品的干燥
由于使用了桨叶式的干燥元件和连续的混合搅拌,能够对黏度很大的、高湿度的材料进行干燥。它的结构设计避免了产品在死角处的积留和因产品积留而带来的过热或者腐败变质。
3.7 材料的损耗及磨损很小
由于桨叶的转速很低,只有10~40r/min,这就有效地避免了磨蚀和由磨蚀带来的机床设备快速的磨损,延长了设备使用寿命。另外,也将金属材料的破裂风险降低到了极小程度。
4 高黏度物料实验
中国神华煤制油有限公司鄂尔多斯煤制油分公司2016年成立油渣萃取项目组,以使液化油渣合理高效利用。根据煤液化油渣溶剂萃取特性,能被溶剂萃取部分称为沥青相,不能被溶剂萃取部分称为固相。本项目选择煤焦油洗油作为溶剂的萃取工艺,使油渣中的沥青与溶剂混合相溶,随后采用固液分离设备分级分离,得到不同灰分含量的分离液,分离液经减压蒸馏后,得到不同等级的煤液化沥青。
物料经过分离设备分离后,固相物料中含有35%的洗油,只有将这部分洗油提取出来循环利用才能证明此工艺的可行性。所以此项目中干燥设备选型至关重要。通过我们前期技术交流及设备考察,选定桨叶干燥机为本项目的重点论证方案之一。桨叶干燥机虽然在化工行业应用广发且成熟,但高黏度物料干燥方面没有运行业绩。为了验证桨叶干燥机在本工艺的可行性及可靠性,进行桨叶干燥机实验。本次实验主要就桨叶干燥机处理项目高黏度物料在结垢、黏壁、处理量、干燥效果等方面进行实验验证。
4.1 物料特性
名称:含洗油的类沥青物;状态:黑色粘稠状;进料温度:120℃;绝干物料比热:1.3kJ/(kg·℃)(设计计算值);湿分比热:2.677kJ/(kg·℃)(设计计算值);湿分蒸发潜热:650kJ/(kg·℃)(设计计算值);黏度:8350mPa·s(120℃);堆密度:1000kg/m³(估算);干燥目的:回收洗油。
4.2 设计要求
处理量:3500kg/h(湿基);湿分名称:洗油;初始湿含量:≈35%;产品湿含量:≤5%;干燥过程中料温:≤260℃;设备台数:10台/套。
4.3 实验参数及流程
4.3.1 技术参数
干燥机型号:JG-3.0;传热面积:3㎡;设计温度:壳程260℃,管程250℃。
设计压力:壳程;壳程/管程:50kPa(a)/0.2MPa(g);干燥机材质:与物料接触的部分304。
电机名称:隔爆型三相异步电动机;电机型号:YB132S-4;电机功率:5.5kW。
4.3.2 实验流程
流程简述:湿物料通过锁气器连续加入到真空桨叶式干燥机中,热源通过真空桨叶式干燥机空心的热油、叶片和夹套将热量传递给物料。在热轴的带动下,叶片把物料打散,同时将物料向出料口输送。蒸发的湿分进入冷凝器进行冷凝,尾气经真空泵抽出排空,干燥后的物料通过锁气器间歇排放收集。
4.4 设备选型
针对本项目物料黏度大,易燃易爆等特性,选择为双轴薄膜真空干燥机。双轴薄膜真空干燥机是根据桨叶干燥机和圆盘干燥机优化组合设计的新型干燥机,其主要由薄膜热轴、壳体、传动系统、密封系统等组成,工作过程中具有较好的密封性、耐磨性和耐高温性能,使用过程中操作弹性大,传热系数高等优点,尤其是对较黏物料具有自清理功能,是油渣和黏性物料的较佳选用设备。
4.4.1 热轴系统
热轴是薄膜干燥机的核心部件,主要由轴管、轴头、矩形叶片等组成,叶片形式为矩形叶片,径向剖开为矩形,轴向为扇形,但扇形面同一个平面,这一点与其他叶片完全不同,由于本部件选用较厚的钢板或锻件制造完成,具有较强的耐磨性能,与轴管焊接时强度较高,有效防止轴本身产生的挠度,进一步保证密封性。两片盘片、内外侧扇形板、侧板及加强筋焊接而成,设计了加强筋和传热导体柱,既可以承受高温引起的变形,也可以增强侧板的耐磨性能,同时也能承受高压。能保证长时间下该轴不会产生变形和泄露,也能进一步降低用户使用过程中的维修费用。
4.4.2 热源进出系统
传统型干燥机的油或蒸汽进出口采用主动端进蒸汽,从动端出油、冷凝液或蒸汽的结构,而双轴薄膜干燥机采用从动端进高温油和出低温油的新型结构,该结构避免高温对主动端的传动精密度产生影响,从而增加轴的传动平稳度,同时也减少了一端面的漏点,为后续检维修降低费用。
4.4.3 轴端密封系统
双轴薄膜干燥机的轴端密封是整个系统的安全保证,如果密封失效或有漏点,空气进入干燥机会有闪爆的可能性。本密封系统采用迷宫密封将大量的油渣阻挡在壳体内部,然后用硬质环将大部分遗漏的渣再次进行阻挡,少部分溢流的油渣进入缓冲仓进行收集,根据使用经验约两年清仓一次。缓冲仓内部填满后发现有气体外漏,备用的反吹氮气进行反吹再次密封,该系统安全可靠无风险。
4.4.4 自清理系统
自清理系统是双轴薄膜干燥机和传统干燥机的设计要点,在黏性较高的物料干燥过程中,防止物料黏附热油。如果物料黏附在热轴表面,使传热系数降低,干燥效率变差,因黏附物料使热轴重量增加,导致干燥机的传动功率增加。本项目中干燥机设计有刮刀,在矩形叶片上增加抄板掏料结构,双轴啮合时可极大限度减小死区,尽可能增大搅拌区间。
4.4.5 热膨胀设计要点
双轴薄膜干燥机在较高温度场必须考虑膨胀移动,较合理的设计能减少设备故障,降低维修率,双轴薄膜干燥机设计温度按照350℃考虑,膨胀量约62mm,主动端为固定端,从动端为滑动端,机架与地基连接部位采用滑动结构,有效释放膨胀应力,防止因膨胀应力导致热轴弯曲变形、叶片根部泄露和损坏密封系统等缺陷。
5 实验情况
5.1 实验条件
试验物料:煤液化油渣离心干相;物料含油量:35%;干燥机换热面积:3㎡;导热油进温度:246~250℃;导热油出温度:243~246℃;真空度:46~71kPa;桨叶电机频率:25Hz;桨叶轴转速:12.25r/min;计划进料量:120kg/h;进料温度:100℃;进料方式:人工添加,旋转阀进料;出料方式:手动间歇排料。
5.2 实验情况
2017年6月16日进行真空桨叶干燥机高黏度物料实验。12:57分开始加料,实验开始。为了保证物料连续进料,操作人员严格控制2kg/min加料,干燥机真空度稳定在71kPa,设备运行稳定。13:40分固相开始出料,物料表面温度125℃,技术人员开始取样进行分析,取样频率为20min/次。14:41分进料结束,15:14分出料结束,本次实验结束。整个实验过程中,干燥机运行稳定,气固相出料连续稳定。停机后设备人员打开干燥机进行内部检查,内部存在轻微黏结挂壁情况,残余物料干燥充分,可以通过排放口排出。6月20日取样分析结果提交:5次取样分析固相含油率分别为0.61%、0.38%、2.25%、1.64%、4.41%。
5.3 实验结果
(1)本次实验累计进料205.86kg,耗时104min,实际进料量为118.8kg/h,折合每平方米干燥面积干燥能力约为40kg/h。满足设备实验要求。
(2)桨叶干燥机从开始进料至出料时间间隔为42min,说明物料在干燥机内停留时间为42min。
(3)通过对不同时间干相出料进行分析,固相含油量平均值为(0.61+0.38+2.25+1.61+4.41)/5=1.86,远小于本项目5%的设计要求,经济效益可观。
(4)干相出料呈颗粒状(粒径0~8mm,其中90%<3mm)。
6 真空干燥系统的实验运行结论
(1)桨叶干燥机运行中物料分散效果良好,平均固相含油率小于2%,满足本项目小于5%的设计条件。
(2)实验进料为118.8kg/h,能够满足设计条件;折合每平方米干燥面积干燥能力约为40kg/h,为满足本项目3.5t/h设计能力,工业放大机的干燥面积约为87.5m。考虑本次实验进料温度较设计温度低约12~40℃,导热油温度较设计温度低约80℃,实验条件(实验机无保温)差散热损失大等不利条件影响,工业放大时所需的干燥面积会更小。
(3)干燥机内部检查存在轻微黏结挂壁及死角结块情况,但对设备运行没有影响。通过优化桨叶结构,效果会更好。
(4)实验证明真空桨叶干燥机能处理高黏度物料。
7 真空桨叶干燥机的工业应用前景
本次真空桨叶干燥机处理高黏度物料实验是成功的。验证了真空桨叶干燥机在油渣萃取项目应用的可行性。接下来将进一步优化设备性能,确保设备干燥高黏度物料的可靠性,提高设备干燥效率及运行周期,也为干燥机在高黏度物料干燥领域积累宝贵经验。