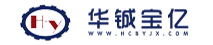
1 前言
随着钻井技术的发展,对泥浆固控设备提出了越来越高的要求,而卧式螺旋沉降离心机以其分离粒度细、沉渣干燥、自动连续操作并能长期运转以及维护方便等优点广泛应用于钻井液固相控制系统。它对提高钻速、延长钻头的使用寿命、减小水力机械磨损、降低钻井成本,起到了明显的效果。但从现场使用的情况看,无论在什么情况下,离心机的工作参数和供液量基本不变,为此,如何根据不同地层、不同钻井阶段、不同钻井液的净化需要,来调整离心机的工作参数和供液量,提高其固相清除率,是目前离心机使用中急待解决的问题。
2 卧螺离心机的结构及工作原理
卧式螺旋卸料沉降离心机的主要构件有转鼓、螺旋推进器、差速器、过载保护装置、卸载装置。
工作原理:机壳内有两个同心装在主轴承上的回转部件,外面是无孔转鼓,里面是螺旋叶片输送器。主电动机通过三角皮带轮带动转鼓旋转。转鼓通过左轴承处的空心轴与行星差速器的外壳相连接,行星差速器的输出轴带动螺旋输送器与转鼓作同向转动,但转速不同,其转差率一般为转鼓转速的0.2%~3%,泥浆从右端的中心加料管连续送入机内,经过螺旋输送器的内筒加料隔仓的进料孔进到转鼓内。在离心力的作用下,转鼓内形成了一个环形液池,重相固体粒子离心沉降到转鼓内表面上而形成沉渣,由于螺旋叶片与转鼓的相对运动,沉渣被螺旋叶片推送到转鼓小端的干燥区,从排渣口甩出。在转鼓大端盖上开设有若干溢流口,澄清液便从此处流出,经机壳的排液室排出。
调节溢流挡板溢流口位置、机器转速、转鼓与螺旋输送器的转差、进料速度,就可以改变离心机的固相清除率和沉渣的含湿量。
3 应用分析
LW-450卧式螺旋沉降离心机的主要参数如下:
项目 | 数值 |
转鼓内径(mm) | 450 |
圆柱锥体长度(mm) | 842 |
处理量(m³/h) | 40 |
分离点(μm) | 5~7 |
转鼓转速(r/min) | 1800 |
分离因数 | 824 |
液层深度系数 | 0.2 |
主电机功率(kW) | 22 |
辅电机功率(kW) | 7.5 |
当离心机转鼓的转速分别为1400、1600和1800r/min时,钻井液性能参数不变的情况下,计算出离心机的分离效率、分离粒度与处理量之间的关系。从计算结果可以看出:当钻井液的性能参数不变时,随着离心机供液量的增加,分离粒度增大,固相清除率降低,同一流量下,随着转鼓转速的提高,分离粒度减小,固相清除率提高。
为保证离心机的处理效果,应根据钻井液的性能,调节离心机的供液量和转鼓的转速。
4 结论
(1)在进行离心机转鼓应力分析时,传统离心机转鼓强度计算方法往往要对转鼓筒体、拦液板、转鼓底及边缘区等作较大的简化,不仅计算比较烦琐,而且计算值与实际值可能出现较大偏差。而同传统法相比,采用有限单元法,只须作较小的简化就可进行计算,而且计算值与实际值更为接近。
(2)在转鼓壁应力计算中,分别采用有限法和传统方法进行计算。比较结果发现,二者的计算结果基本保持一致,从而说明运用ANSYS软件进行离心机的应力分析的准确性和可行性。此外从转鼓的变形和应力分布可知,离心机转鼓满足设计要求。但在拦液板和转鼓底边缘设计过于保守,可在保证其刚度和强度的前提条件下,减少其边缘连接处的厚度,提高其经济性的同时使机器的受力情况更合理。
(3)转鼓底的应力水平较低,但在转鼓与转鼓底的连接处开有凹槽,容易产生较大的局部应力。因此,在离心机设计中,尽量避免在连接处开凹槽或者小的倒角,以防止产生较大的集中应力。由于局部应力具有局限性和自限性的特点,其许用值可根据安定性原理加以选定。