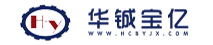
1 离心脱水干化一体技术(Centridry)
离心脱水干化一体系统主要包括脱水干燥一体机(又称脱水干化离心机)、热介质发生装置、絮凝剂投配装置、旋风分离器、文丘里冷凝洗涤器、循环风机及排气风机、尾气净化装置等设备。
脱水干化离心机是系统的核心设备,浓缩污泥(含水率为95%~99%)与调配后的絮凝剂分别通过进料泵、加药泵送入脱水干化离心机进口,在离心力作用下,在离心机转鼓内实现固液分层,固渣由螺旋推料排出转鼓,而澄清液经溢流口排出,完成脱水阶段;其中澄清液(SS≤500mg/L)通过收集罩收集,排至积水井进行后续处理,而固渣在离心机转鼓出渣口通过特殊的专利设计结构分散成比表面积更大的固相颗粒,提高后续干化阶段的换热效率。离心机转鼓外的罩壳为干燥腔体,固相颗粒在干燥腔内与热介质发生器提供的热空气(220~350℃)快速进行热交换,完成干燥作用,并由循环风机产生的循环风带出离心干化机,完成干化阶段。整个污泥的脱水及干化过程在脱水干化离心机这一个设备中完成。
干燥后的固体粉末和蒸汽(150~280℃)一起被送至旋风分离器,完成气固分离,固体粉末(含水率为8%~40%)则通过输送系统送至干粉料仓或直接装袋。
旋风分离后的气体(140~270℃)仍然具有一定的热量,这些热介质大部分会进入循环管道,回到热介质发生器中进行再次加热和燃烧“除臭”,充分利用这部分热能,降低能量损耗。而小部分的气体通过排气风机输送至文丘里冷凝洗涤器,完成气体的净化和冷凝,排放至大气(约80℃)。
2 工艺特点
离心脱水干燥一体化技术兼具卧螺离心机和热干化的特点。首先,卧螺离心机是在离心力场作用下,悬浮液在转鼓内形成环形液流,固相颗粒在离心力作用下快速沉降到转鼓内壁上,由差速器产生转鼓和螺旋输送器的差速,由螺旋输送器将沉渣推送到转鼓锥端的干燥区,经过螺旋输送器推料和沉渣离心力的双向挤压,使沉渣得到进一步挤压脱水后,从转鼓小端排渣口排出。分离后的清液经溢流口排出。该设备具有连续高效、设备体积小、封闭卫生条件好、自动化程度高、日常维护工作量小等特点。而热干化是应用较广泛、较成熟的干化技术,它利用热能将污泥中的水分变为水蒸气而散失,进一步降低污泥含水率,同时利用高温灭菌作用,杀死病原体和寄生虫,加速污泥干燥,避免污泥对环境的二次污染,实现污泥的无害化和资源化利用。
传统的污泥脱水干化工艺技术通常采用先对污泥进行机械脱水(前处理),产生的80%含水率的泥饼再通过存储、输送、返混等一系列设备和设施送入到干化设备内进行污泥干化或深度处理。离心脱水干化一体技术与传统的污泥脱水干化技术不同,它是将污泥的脱水、干燥过程集成在一个紧凑的设备空间内,省去了一系列的附属设备,直接涵盖污泥的前处理和深度处理过程,同时也大大减少了设备的投资和运行成本。
由于该技术采用传热效率更高的接触式热干化法,且污泥颗粒化,因此其干化效率更高。
3 案例
3.1 项目概要
南京某化工企业在生产过程中会产生有害化学污泥,若不妥善处理,将对环境造成严重污染。该公司若按照原有的设计方案,仅对污泥进行机械深度脱水,其化学污泥经过浓缩处理后,采用机械压滤脱水之后再进行后续的危废处置(填埋或焚烧)。机械脱水后的污泥含水率仍很高(约75%),其中的水分主要为细胞内部结合水和部分颗粒吸附水及毛细水,而且该公司污泥属于危险固废,脱水后污泥后续处置费按当地价格为6500元/t,后续的污泥运输及处置费用高昂。因此,该项目主要的目的就是实现污泥的较大程度减量化,以降低后续的污泥处置费用。
3.2 设计选型
根据该项目的设计要求及污泥参数,每天需处理污泥(绝干基)3.6t,则每天处理浓缩污泥量为180m³左右,脱水干化后的污泥为4.5t。
系统主要技术参数:处理量为7.5m³/h,绝干泥量为150kg/h,蒸发水量为480kg/h,燃料为0#柴油,循环介质温度为220~250℃,循环风量为17000~20000m³/h,转速为3900r/min,出粉含水率≤20%,滤液SS≤500mg/L,干粉温度≤70℃,排放废气温度≤40℃。
3.3 运行成本
根据系统配套设备的装机功率及处理过程中的热能、水、絮凝药剂的消耗等费用,结合详细的工艺计算(包括物料平衡和热量平衡等),分析了该项目的运行成本。运行费用按照处理1m³含水率为98%的浓缩污泥计算,虽然污泥是在一个设备中完成了整个脱水及干化阶段,但为了便于与传统机械脱水的运行费用进行分析比较,也将其费用分解为机械脱水及热干化两部分。
机械脱水阶段处理1m³含水率为98%的浓缩污泥费用为5.45元,与其他机械脱水设备费用相当,热干化阶段处理对应的污泥至20%含水率,费用为24.69元,所以整个脱水干化阶段所需费用约为30.14元,根据该项目工艺设计参数,每天污泥处理的绝干泥量为3.6t,处理费用为5425.2元/d。
3.4 经济分析
按当地危废处置费用为6500元/t计算,后续处置费用为29250元;若该项目采用原来的机械脱水工艺设计方案,每天处理的绝干泥量同样为3.6t,而产生的脱水污泥总量却为14.4t,虽然每天的处理费用只考虑脱水部分,约为981元/d,但后续处置费用却为93600元。该项目干化后的污泥为脱水后污泥的31.25%,减量化明显;另外,每天的污泥干化费用增加了约4444.2元,但后续处置费用却减少了64350元,可大幅降低企业的运行成本。
4 结论
我国危险固废源头产生量大、危害性大、不易处理的现状难以在短时间内得到扭转,源头减量控制是较基本的方法。污泥离心脱水干化一体技术在该领域具有技术和经济双重可行性,是一种新型的污泥减量化处理工艺,其安全可靠、工艺运行稳定,运行环境封闭卫生,操作简单、自动化程度高,工艺简明、占地空间小,维护成本低等特点使其具有了较大的推广应用价值。另外,其干燥后污泥含水率低至10%以下,较大程度地进行污泥减量化、稳定化,更使得污泥的后续处置方式更灵活,也极大地降低了后续处置的难度及成本,尤其适用于危险固废行业。