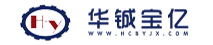
辽阳石化公司炼油和化工几大主体生产装置经扩能改造投产运行后下排污染质总量持续上升,污水处理装置运行时污泥产量相应增大。污水处理厂初沉污泥、含油污泥、剩余活性污泥(以下简称“三泥”),是污水生化处理装置的前置预处理单元产生。污泥中含有苯系物、酚类、硫化物、氰化物等具有恶臭味和毒性的物质,是国家明文规定的危险废物,比较难于生物降解。含油污泥已被列入《国家危险废物目录》中的含油废物类,《国家清洁生产促进法》要求必须对含油污泥进行无害化处理。含油污泥的处理与应用是国内外石油生产领域环境保护的重要内容,是较难解决而又急需解决的问题之一,也是制约石油化工环境质量持续提高和经济可持续发展的一大难题。多年生产实践经验告诉我们:对于“三泥”的收集和有效处理,其运行效率将极大地影响到污水微生物生化处理效果和水质排放达标,对改善周围生活环境和保护地下水资源意义重大。
1 生产概况及现状分析
该公司炼油污水处理装置主要负责处理炼油装置高含油污水、部分化工装置低含油污水及部分生活区污水。配套污泥脱水系统主体设备为德国产福乐伟离心脱水机,其设计处理能力为35m³/h,实际生产为间歇运行。污泥脱水系统每天处理约100m³含水率99%湿污泥及浮渣底泥,产生约10m³含水率90%左右干污泥装车外运至后续处理单元,脱水后滤液经检测悬浮固体含量(SS)为400mg/L左右,直接回流至装置入口。这些生产数据充分说明了污泥处理系统远没有达到连续运行负荷和较高的运行效率。
一般情况,收集和浓缩后的污泥含固率为1%~2.5%,经过化学药剂调质后泵送至离心机脱水处理后干污泥含固率达10%以上,分离出来的滤液含固率不高于0.5%。大部分污水处理厂污泥经脱水后滤液直接回流至污水装置入口,如泵前池或者初沉池入口进行再次沉淀分离。这样,经常出现集水池淤积堵塞提升泵吸入口管道和底阀的情况,也常常造成初沉池排泥困难。主要的是实际生产过程中,待脱水污泥是来源于初沉池的池底淤泥、气浮池底泥和浮渣、中间沉淀池脱落生物膜等混合介质,经过脱水分离出来的滤液成分比较复杂,如果含固率(SS)含量较高的情况下,不加以处理直接流入某一预处理单元易造成不利于后续工艺稳定运行的问题。因此,污泥压滤系统优化运行无疑是污水生化装置平稳运行、达标排放的重要环节。
2 技术改造及工艺完善
为了使污泥处理单元达到更高的运行效率,滤液再处理不失为有效可行的技术方向。经过研究论证,通过对滤液增加后续处理设备,一方面不仅使滤水SS含量降低而极大提高脱水系统对污泥处理量的综合回收率,另一方面将使离心机的操作条件更加宽松和达到更高的脱水率,污泥减容效果十分明显。结合以往运行经验和经过研究论证,认为污泥脱水含水率低于80%,滤液处理SS达30mg/L以下是较经济合理的运行方式和生产目标。气浮技术作为一种高效、快速的固-液分离技术,已广泛应用于石油化工废水的处理,去除废水中油脂和悬浮物。
目前石化行业普遍采用的气浮技术是加压溶气气浮工艺和涡凹气浮工艺。涡凹气浮工艺采用水力切割法制造微气泡,产生气泡较大,一般在100um以上,生成浮渣稳定性差,出水SS偏高,在实际运行过程中经常出现中空管堵塞和诸多机械故障问题不利于长周期稳定运行。经过考察和技术交流,发现加压溶气气浮产生气泡一般在60~100um,对乳化油和较高SS浓度去除效果明显,具有能耗低、易于维护和利于长周期运行等特点,已成为含油废水处理的优选工艺。经过改造升级后,增设了配套溶气气浮装置,处理能力为50m³/h。同时,增设了相应污泥调节池和工艺联络管道,经调试后确实解决了滤水悬浮固体含量较高的问题,提高污泥脱水效率同时取得了十分稳定的处理效果。
3 优化控制参数及运行数据
3.1 离心脱水机
污泥颗粒与水相之间的密度差是含油污泥离心分离的前提条件,为了提高和保证离心分离效率,可增大污泥颗粒粒径和密度,减少自身黏度,适当提高离心速度。调试过程中要特别注意的是脱水污泥含水率和滤液中SS水平较佳平衡点。在相同运行负荷下,若要取得脱水污泥较低的含水率势必造成滤液较高的悬浮固体(SS)含量,增加了后续工艺处理负荷和降低了离心脱水机的处理效率;同样,如果达到了较好的滤液排放水平必然也会增加污泥含水率,大大增加了排放容积和处理成本。
采用PAM药剂用量与运行参数优化实验,将主机转速、差转速、污泥量、药剂量4个因素,每个因素采用3个稳定运行档差(位级)进行正交实验,得出主要的并已经过稳定运行验证的参数:主机转速为2600r/min、差转速为3~5转、药液配制浓度0.3%、污泥流量32m³/h、药剂流量800L/h。脱水机在稳定运行同时取得了较好的处理效果,确保了污泥较大限度减容,解决了以往剩余污泥脱水后容积大的问题。生产中脱水后外运“干泥”含水率低于80%,污泥外运体积减少了约48%,经过初步统计泥饼含水率平均值为78.8%。
3.2 溶气气浮装置
溶气气浮装置在进水SS低于800mg/L、油含量低于500mg/L的情况下出水水质稳定。在调试过程中,滤液处理量约30m³/h,将溶气压力控制为0.40MPa达到气泡均匀,经过反复对比控制,分离的滤水回流比为20%左右,浮渣达到较好的上浮效果。同时,反应器设置扩径及速率控制在约0.80m/s;0.3%PAM药液配制浓度下投加量为300L/h;20%浓度PAC投加量为500L/h。气浮出水经过分析取样化验,悬浮物含量低于30mg/L,含油量低于2mg/L。
滤液经过稳定运行的气浮装置处理降低了出水悬浮物浓度,生产现场絮凝药剂PAM优化筛选及合理加药浓度确保污泥絮凝性能和较佳泥水分离效果,提高该系统处理效率和回收率,使污泥脱水系统下排滤液悬浮物SS低于30mg/L,平均值为27mg/L,去除率达95%以上。
4 效益分析
节约污泥运输费用:脱水污泥含水率达到78.8%,与原含水率89%相比,污泥体积为原体积的(1-89%)/(1-78.8%)=52%,体积减少48%。原含水率89%的湿污泥产量10m³/d,污泥运输及后续填埋或焚烧处置费用按200元/m³计算,每年减少外排污泥运输费用为365天×(10×0.48)m³/d×200元/m³=35万元。同时,仅从污泥减容和节省堆放土地考虑环保效益和社会效益也是十分显著的。
5 结论
含油污泥脱水与气浮组合工艺经实践充分证明技术路线成熟可靠、生产操作灵活快捷。尤其在石油化工污水装置中应用,在取得较大经济效益同时社会效益意义重大,相关行业可作为技术借鉴并具有较大的推广价值。