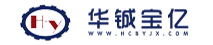
利用无机陶瓷膜浓缩分离技术及膜亲水疏油的特性,在步需要破乳的情况下,可直接实现乳化悬浮液中的油和超细颗粒与它们存在的介质的分离。但在实际工作中,过滤一段时间后由于浓差极化作用,使无机陶瓷超滤膜的表层附着一层污染物,这将会大大降低膜的渗透通量;同时也有可能由于非正常操作,导致膜的严重污染,需要合适的工艺进行化学清洗。
目前,国内外文献对无机陶瓷膜处理悬浮液的报道较多,但很少涉及到陶瓷膜污染后再生的研究。南京化工大学赵宜江等对陶瓷微滤膜回收偏钛酸过程中膜的清洗问题进行了研究;抚顺石油学院孙杰等在陶瓷微滤膜处理钛白废水过程中采用反冲方式对膜进行清洗;中北大学刘有智、高松平等在探讨用陶瓷超滤膜对乳化悬浮液的净化处理时提及用渗透液清洗污染膜的再生工艺,但未对其进行系统的研究。因此,本文以膜处理催化剂生产过程中废氨液后的再生工艺为例,分别采用物理和化学方法,对被污染的陶瓷超滤膜进行了再生工艺研究;并通过探讨清洗工艺如动态清洗、温度、清洗剂浓度、操作方式等对膜层清洗效果的影响,确定其适宜的再生工艺参数。
1 实验
1.1 膜的选择
采用自制的19通道管式α-Al2O3陶瓷膜,内径3.5mm,有效过滤面积为0.2㎡,管长为1m,膜孔径为0.08μm。
1.2 实验料液
由某厂提供催化剂生产过程中的废氨液,是一种含有超细固体颗粒的白色不透明浑浊乳化悬浮液,含有以乳化油和溶解油形式存在的矿物油、表面活性剂以及粒度为0.01~0.1μm的超细氢氧化铝和氨水,pH值为13.5。
1.3 试验装置及流程
储料罐中的原料液以一定的流量进入膜组件中,在压差的推动下错流过滤,清液从膜组件的侧面经透过液出口流出,浓缩后的料液返回储料罐中循环过滤。由阀门调节控制料液的流速和过滤压差;压力表测量膜进口压力和膜的出口压力。
1.4 检测方法
原料液的固含量用重量法检测,透过液的固含量用分光光度法检测;原料液和透过液的含油量通过测定其COD来判定。
2 试验结果和讨论
2.1 动态膜清洗工艺研究
在超滤中,浓差极化不可忽视。用陶瓷膜处理含有超细颗粒的乳化悬浮液,过滤效果和过滤阻力主要受由浓差极化而形成的动态膜控制,因此在对此类膜进行再生时,不应该将动态膜破坏。普通的直接用水反冲的物理方法或用化学方法直接清洗的方法都是不合适的,而应根据逆向浓差极化对其动态膜的外层部分进行清洗,首先选择用透过液(或稀料液交替过滤)进行物理清洗的方法。
在0.15MPa的操作压力下,先过滤0.72%的料液后再过滤0.35%料液。当过滤浓度为0.72%的料液时,膜通量逐渐衰减,当换成浓度为0.35%的料液过滤时,发现膜通量逐渐恢复到过滤浓度为0.72%料液的初始通量,且透过液澄清透亮;对过滤液进行分析可知,固含量去除率达到98%,去油率达到99.6%。
当过滤浓度为0.78%料液后再过滤浓度0.41%的料液,膜通量逐渐恢复至初始通量的96%以上,去油率达99.2%。这些现象充分说明用于稀浓度料液过滤的过程就是膜清洗的过程。
膜通量之所以能基本恢复是因为低浓度的料液进入膜内,其本体浓度小于前次过滤高浓度的料液因浓差极化而积累到膜面上形成极化层的浓度。所以,高浓度料液过滤完后,再过滤低浓度料液,一方面,不可能出现因浓差极化而造成的膜污染;另一方面,正因为低浓度的料液的浓度小于膜面极化层的浓度,所以膜面上高浓度极化层上的颗粒向低浓度的料液的本体相扩散,减小了过滤阻力,膜通量逐渐增大,低浓度的料液对膜面起了清洗作用,当料液本体浓度与膜面上积累的颗粒浓度再达到平衡后,膜通量趋于稳定。
2.2 温度对膜清洗效果的影响
经研究发现,膜被严重污染后在温度为35~40℃和常温两种条件下用相同的清洗液清洗膜层,膜通量有着明显的差距。在0.15MPa的操作压力下,在常温(18℃)条件下循环清洗后,膜通量始终是11.7L/㎡/h,洗40min膜通量都没变化;在温度为35~40℃的清洗液中循环清洗后,膜通量比在常温时明显上升。在实验中还发现,经常温清洗后,透过液澄清透明;而在温度为35~40℃的清洗液中循环清洗时透过液上面浮有油脂。这说明升高温度有益于油脂的流动性能增强,穿透膜的能力增强,有益于膜的清洗,但从整体清洗效果来说,对膜通量的恢复没有明显效果,35~40℃下洗液通量仅有20L/㎡/h,与正常通量相比小得多(一般膜的正常通量为85L/㎡/h)。因此在工业化应用中,选择常温下进行清洗较为适宜。
2.3 后处理工艺
2.3.1 清洗剂浓度对清洗效果的影响
量取200mL的0.5%、1%、2%、3%的氢氧化钠溶液倒入盛有相同质量的上述油污的三角瓶中,剧烈摇动大约20min,大片白色絮状油脂分散成不溶的浑浊的小颗粒,静止一会沉于下部。说明清洗时,用低浓度的碱液就可以。因此选用0.5%和1%的碱液作为碱性清洗剂。
在剧烈摇动下,碱与油脂结合后,酸就很容易与无机盐氢氧化铝反应。把上述浑浊液分别用漏斗过滤洗涤成中性,用0.1mol/L、0.2mol/L、0.5mol/L、1mol/L的盐酸进行中和反应,浑浊液都变成清亮溶液。说明用酸清洗时用低浓度的盐酸就可以了,选用0.1mol/L盐酸和1%的柠檬酸作为酸性清洗剂。
2.3.2 操作方式对清洗效果的影响
量取3份200mL的1%的氢氧化钠溶液,分别放入盛有相同质量上述油污的瓶中,采用不同的操作方式,对比效果如下:
编号 | 操作方式 | 现象 |
1 | 剧烈摇动 | 大片白色絮状油脂分散成不溶的浑浊的小颗粒 |
2 | 静止放置7天 | 大片白色絮状油脂仍存在,状态没有改变 |
3 | 静止放入55℃烘箱内4h | 大片白色絮状油脂仍存在,状态没有改变 |
由上表可知,短时间的剧烈摇动比长期静止和升温处理的效果都要好。
同时做了放大实验,放大的碱洗操作方式对清洗效果影响如下:
操作方式 | 膜通量的变化 |
膜在1%碱液中浸泡一次 | 膜通量基本保持在浸泡前的通量 |
由泵循环1%碱液冲洗膜一定的时间 | 膜通量由24.6L/㎡/h恢复到103.5L/㎡/h |
由上表可知,短时间循环碱液冲洗膜层的清洗效果明显优于在碱液中长期浸泡。这是因为:碱洗对油污的作用主要是通过碱液高速流动对膜面上的油污进行剪切冲洗,破坏油污的紊凝状态,使油污变成小颗粒状;一方面有利于碱液与油污的充分作用,化解油污;另一方面,有利于高速流动的碱液夹带走小颗粒油污,达到清洗的目的。因此,应选择碱液在高速流动状态下来清洗油污较为适宜。
酸洗操作方式对膜层清洗效果的影响如下:
操作方式 | 膜通量的变化 |
膜在0.5mol/L的酸中浸泡一夜 | 初始膜通量为94L/㎡/h,然后逐渐恢复到103.5L/㎡/h |
泵循环0.5mol/L酸冲洗膜一定时间 | 初始膜通量为94L/㎡/h,然后逐渐恢复到103.5L/㎡/h |
由上表可知,酸洗的操作方式对清洗效果影响不大。这可能因为碱液冲洗掉一定的油脂后,酸就比较容易和氢氧化铝接触进行比较快速的、有效的反应,从而酸洗操作方式的影响显得不太明显。
2.3.3 混合清洗工艺
由0.15mol/L碱液、0.15mol/L盐酸和1%的柠檬酸组成混合清洗剂。先用碱液在0.15MPa的操作压力、高膜面流速下剪切污染物一定时间,然后用清水洗成中性,再用酸浸泡或循环一定时间,然后用清水洗成中性,测量其通量,若膜通量未恢复,继续加入清洗剂交替清洗。混合清洗剂进行交替清洗,效果良好。清洗后膜通量可恢复到原稳定膜通量的95%以上。
3 结论
(1)用透过液或低浓度料液清洗受污陶瓷膜,操作简单方便,不产生二次污染;又由于此类清洗对动态膜的影响较小,所以这样不但可以恢复膜通量,而且也可显著延长膜的使用寿命,确保膜超滤的稳定运行,是既经济有效,又实现了生产过程连续化的适宜方法。
(2)升温操作有益于膜的清洗,但从整体清洗效果来说,对膜通量的恢复没有明显效果,35~40℃下洗液量仅有20L/㎡/h,与膜正常通量85L/㎡/h相比小的多,因此在工业化应用中,选择常温下进行清洗较为适宜。
(3)膜停止工作后的后处理工艺中,酸碱清洗剂的浓度对陶瓷膜清洗效果的影响不大,可选用0.5%和1%的碱液作为碱性清洗剂,选用0.1mol/L盐酸和1%的柠檬酸作为酸性清洗剂。酸碱液的操作方式对清洗效果有很大的影响,剧烈摇动的清洗效果明显优于长期浸泡和升温清洗,因此应选择酸碱液在高速流动状态下来清洗油污较为适宜。采用0.15mol/L碱、0.15mol/L盐酸和1%的柠檬酸组成混合清洗剂进行交替清洗,既可减少油脂对膜的污染,也可对膜通量起到一定的恢复作用。