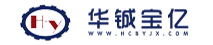
啤酒生产中排放的剩余酵母和罐底沉积物约占总产量的2.5%,其中绝大部分为啤酒,如果能回收其中一半的啤酒,可获得可观的经济效益,以年产20万千升啤酒的企业为例,每年约能回收2500千升啤酒,经济效益约150万元。已有少数啤酒企业用陶瓷膜从中回收啤酒。本文针对用陶瓷膜回收啤酒工艺流程中常用的错流过滤工艺和近来出现的再生球过滤工艺进行对比。
1 错流过滤和再生球过滤
1.1 错流过滤
错流过滤让悬浮液在陶瓷膜管内循环流动,流速一般大于3m/s,依靠较高的流速将沉积膜表面上的滤渣冲刷掉,从而使膜污染保持一个较低的水平,从而提高过滤速度,延长过滤周期。
1.2 再生球过滤
该技术是在循环流动的悬浮液中加入一定数量的再生球,用再生球清洁膜表面,达到错流过滤高速循环的效果,将过滤速度保持在较高的水平,再生球过滤循环速度仅为1m/s左右,可大幅降低电力消耗,减少啤酒回收的成本。
2 两种过滤工艺回收实验
2.1 实验材料
啤酒发酵过滤前排放的剩余酵母,温度0℃~4℃。
陶瓷膜管采用7芯管式陶瓷膜,膜孔径0.5μm,通道直径7mm,膜管长度1000mm。
与该陶瓷膜管相配合的再生球若干,材质为满足食品行业要求的硅橡胶。
2.2 实验设备
实验设备包括:清酒罐、膜组件、再生球系统、换热器和酵母罐等。
为适应啤酒特殊要求,酵母罐和清酒罐采用密闭罐,备有CO2进出口、换热器,保证在过滤过程中酵母罐和清酒罐内压力在0.2MPa左右、温度在0℃~4℃。
2.3 实验过程
实验在某啤酒公司过滤车间进行,为消除剩余酵母稀稠度不一致对实验结果的影响,将同一后酵罐内排放的剩余酵母存入暂存罐,并阻止酵母沉淀,每次实验从暂存罐装入剩余酵母的数量为酵母罐容积的80%;实验过程中自动控制酵母罐和清酒罐内温度和压力,收酒过滤压差0.1MPa,错流过滤循环流速约为3m/s,再生球过滤循环流速约为1m/s。每次实验持续收酒时间2小时~2.5小时。
2.4 结果与分析
再生球过滤的速度在整个实验中明显高于错流过滤,但错流过滤速度下降较为平缓;再生球过滤的平均过滤速度为33L/(㎡·h),错流过滤的平均过滤速度为23L/(㎡·h)。
3 回收酒的质量
实验结束后,由啤酒公司检验科对回收得到的啤酒进行相关检测,将回收酒与经硅藻土过滤机过滤的成品酒进行质量比较,回收明显比成品酒清亮,陶瓷膜滤除了部分高分子物质,回收酒原麦汁浓度略有下降。将回收啤酒按不超过5%的添加量直接加入成品酒,经专业人员测试,对于啤酒的整体口味毫无影响。
4 经济效益分析
当实验进行一段时间后,根据再生球过滤回收酒总量、动力消耗、清洗水和各种清洗剂、正常生产时人员费用进行综合统计,进行经济效益计算。
4.1 经济效益估算依据
(1)每生产1千升酒,可回收酵母酒12.5千克。
(2)每千升酒价格700元。
(3)每回收1千升啤酒所需辅助费用约40元。
4.2 以年产20万千升的啤酒厂为例进行估算
全年共可回收酵母酒2500千升。
2500千升酒水价值:175万元。
回收酵母酒所需费用:10万元。
全年实际增加收入:165万元。
再生球过滤收酒速度比错流过滤约高50%;再生球过滤循环速度只有错流过滤的1/3,电力消耗也降低65%左右,吨酒回收费用比错流过滤下降50%以上;低循环流速对酵母的剪切作用很小,酵母不易破损,回收酒口感变化小,使回收酒的品质更有保障。