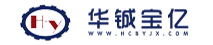
1 老化油的形成和危害
通常把现有技术手段难以处理的原油称之为老化油,包括油田生产过程中,含油污水经污水沉降罐、除油罐、浮选罐等形成的数量可观的污油;污水回收池内的污油;脱水器内的油水过渡层;钻井、作业及原油输送过程中形成的油水乳状液以及落地油。老化油成分复杂,通常含水高于10%,还含有高于普通原油的胶质、沥青质等重组分和固体杂质,其中粒径为50~500nm的固体颗粒,常与沥青质相吸附,共同存在于油水界面上,形成空间势垒,当固体颗粒与沥青质含量达到一定比例和浓度时形成的油水乳状液具有很高稳定性,需要经过特殊处理才能回收利用。
老化油的及时回收与高效处理,对于节约能源,减轻污水处理和集输系统的压力,解决污水水质恶化超标等问题,降低安全和环境隐患,具有重要的环境和社会效益。在国际原油价格急剧上涨的今天,具有很大的经济吸引力。
目前主要通过沉降、过滤等手段对老化油进行预处理,然后回收至油系统,与大量新鲜原油混掺后泵入电脱水器,在电场作用下使水滴聚结,然后借重力从油中分离的办法处理老化油,即老化油的回掺流程。回掺处理过程中易形成乳化程度较高的油水过渡层,对油田生产带来危害:
(1)油水过渡层导电性强,电脱水器易于垮电场,缩短设备使用寿命。
(2)大量油水过渡层占据了采出液处理设备的空间,降低了处理量。
(3)老化油回掺加大了采出液处理难度,导致脱水温度升高和处理剂用量增加,提高了处理成本。
2 老化油回收处理工艺探讨
多数学者认为老化油不应回收油系统,需单独处理。赵守明等取孤东一号联合处理站原油电脱水器的进口原油和污油池的老化油,使用介质击穿仪器进行对比实验,发现老化油的导电性能明显高于新鲜油乳状液。周玉贺等将滨海站的系统净化油、系统净化油与老化油的混合油和老化油用沸程90~120℃的石油醚稀释成5%的溶液,再用注射器在直径1mm的孔上造膜,然后测定油膜电容、电阻及击穿电压。结果表明:脱水净化后的老化油与系统净化油相比,膜电阻值大,膜电容值小,即膜的导电性较差,厚度较大,击穿电压较大,即老化油这样分散体系稳定性高。衡英杰等向新鲜原油中掺入不同比例的老化油,研究静态条件下,对电流和电压的影响程度,发现随着老化油混入比例增大,电场处理消耗能耗越来越多,在混入比例9%~10%之间有一个明显变化,结合现场要求,认为老化油的混入比例不能大于6%。
随着油田开发的延续,老化油产生速率不断增加,应用电场处理老化油,由于其乳化液膜不易破裂,要求外加较高电压;又由于乳状液导电性强,电脱水设备难以保证高电压,易于发生垮电场和放电现象,其直接应用于老化油处理的可行性越来越差。但由于回收油系统处理设备成本低,仍可应用于低回掺量处理或“低污染度”老化油,如经过其他方法处理后杂质含量大幅降低但仍未达到外输油指标的老化油的二次处理过程。
老化油的单独处理工艺研究主要集中在热重力沉降、离心分离、超声波处理和生物处理方面
2.1 热重力沉降
热重力沉降是处理原油乳状液应用较早、范围较广且工艺较简单的方法,其原理是通过将老化油加热到较高温度,从而降低油相粘度,提高油水密度差,再通过加入特定的化学处理剂来降低界面张力或界面膜强度,促使油水界面膜破坏,再进行长时间恒温静止沉降除去老化油中的水和杂质。
胡雪滨等在王场等地应用污油处理剂JH002A、JH002B(投加量为500mg/L)和沉降剂JH001B(投加量为700mg/L)进行热重力沉降处理老化油。处理过程分两次进行,第一次处理时只加入污油处理剂,循环加热至70±2℃后,停止加热,静置沉降8小时;第二次处理时掺入清水并投加污油处理剂和沉降剂,循环加热至70±2℃后,停止加热,再静置沉降8小时或更长时间。经两次处理后可回收约占纯油质80%的原油,处理后含水率小于5%,含砂率小于3%。
刘玉芹等在大庆油田朝一联现场生产运行中应用老化油处理剂ALDT处理老化油,加药浓度为0.4%,罐温保持在65℃以上,沉降时间72h,处理后原油含水降至5%以下。热重力沉降法工艺简单,便于建立较大规模集中处理站,节约设备资源,有效利用热能。缺点是处理时间长,能耗大,药剂投加量高,处理效果对药剂依赖性大,由于目前没有高效处理剂配方,因此处理后的原油仍含有一定量的水和固体杂质,对难处理老化油适应性差。
2.2 离心分离
该工艺是由自动加药装置向老化油中加入破乳剂和絮凝剂,再送入离心机,通过离心作用,使老化油中密度大的固体粒子沉降到转筒壁上,油水两相形成同心圆柱,分离出的固体杂质由螺旋输送器排出,常用的离心装置还包括水力旋流器。离心法分离效率高于热沉降,设备占地面积小。国外多采用这一办法处理老化油,将分离出的固体杂质进行焚烧或生物无害化处理。如美国Unpure公司,先把老化油加热到150℃,1.03MPa以上,再加絮凝剂,然后通过文丘里管减压闪蒸,预处理后的老化油再送入离心机离心分离。该工艺可以打开固体颗粒形成的牢笼,达到固体、水和油分离的目的。
国内也有人进行离心处理老化油的研究。夏福军等发现离心处理老化油的效果随离心处理时间和离心机转速增大而增强。并对中七联合站5#事故罐下部O/W型含硫化亚铁颗粒老化油现场采用离心机处理,处理量2.0~4.0m³/h,转速3500r/min,分离因数2500,功率15~20kW,温度为38℃,处理后老化油平均含水由58.31%降低到17.74%,乳状液类型由O/W型转变为W/O型。
离心法的缺点是一次性投资较大,由于其分离效率随转速升高而增强,因此单独应用离心法处理,要想达到理想的处理效果,对设备要求高,运行费用也高。但离心法占地面积小,特别适合用在海上平台等空间要求严格的领域。
2.3 超声波处理
超声波处理老化油,是通过其机械振动、空化及热作用来降低老化油粘度和油水界面膜刚性,同时作用于性质不同的流体介质产生位移效应实现油水分离。一方面超声波在油中和水中均具有良好的传导性,所以这种方法适用于各种类型乳状液,另一方面,超声波的扩散效应能提高破乳剂作用效率,适用于常规方法不能奏效的情况,因此是国内外研究热点。Paczynska-Lahme B对比了热沉降和超声波处理(频率为35kHz和45kHz)两种方法对老化油的破乳效果,作出超声波破乳效果更优的论断。Davis Robert Michael等用超声波处理老化油乳状液,预处理温度为40~42℃,先经过重力沉降脱除游离水,之后通过超声波作用的管道,工艺温度为80~82℃,声波频率1.25kHz,然后再利用重力沉降使油水分离。所用的破乳剂为AQUANOX272,加量约60ppm,处理后原油含水量为0。
Kotayusov从理论上导出声波对水滴的凝聚作用的较佳频率为10kHz以上。孙宝江等认为超声波频率的大小在一定量级范围内只是影响水滴粒子向波腹或波节运动所走的距离,所以在一定量级内超声波频率对破乳影响不明显,同时指出,较低频率的超声波处理油样需要较长时间。
张玉梅等对超声波处理污油时超声波的声强、辐照时间对处理效果的影响以及超声波对破乳剂用量影响作了研究,结果表明:超声波声强存在较佳值,声强较小时,水滴位移振幅也小,破乳作用不明显;70℃沉降两小时、超声波辐照2min的条件下,污油脱水率在声强为0.66W/c㎡时达到极值91.7%,但当声强进一步增大时,水滴运动变得剧烈,不断与周围的油粒子发生碰撞,凝聚后水滴被重新分散,产生新的乳化,造成脱水效果下降。超声辐照时间的影响与声强相类似,一定范围内随着超声波辐射时间的延长,污油脱水率逐步提高,超过一定值则容易出现二次乳化过程。实验数据还表明,超声波能大大减少破乳剂用量,70℃沉降两小时的条件下,无超声作用,破乳剂用量0.375mg/g时污油脱水率高达79.6%,而在超声声强为0.66W/c㎡时,作用5min,不加破乳剂也可达到同样的脱水率。
超声波处理技术设备简单,运行费用低廉,不但具有热化学沉降技术可以大批量处理的优点,更能够降低处理温度,节约药剂,缩短处理时间,适于常规办法难以奏效的老化油处理,如能大面积推广将取得很好的处理效果和经济效益。但由于各地老化油组成和性质的差异性,以及超声波可能引起的二次乳化,应用时要特别注意参数的选择。
2.4 生物处理技术
生物处理技术,包括生物降解和生物破乳,前者是通过调节环境pH值、温度、湿度以及添加营养盐来促进嗜油细菌生理活动从而降解污染物,如地耕法、堆肥法等。降解过程不产生二次污染,处理费用低廉,但处理周期长,而且沥青质、蜡等重组分更是难以降解甚至无法降解。生物降解多用于含油污泥、落地污油的无害化处理,也适用于对其它方法处理老化油所得到的固体废弃物进行无害化处理,避免直接排放。生物破乳是通过从与原油相关环境中筛选菌种,再通过增殖培养,得到具有破乳优势的菌群或具有表面活性的菌体代谢物,以此代替化学破乳剂使油水分离,其高效性和安全性使其有望成为化学破乳剂的理想替代品。在老化油处理方面,目前的研究主要集中在生物降解方面,国内未见生物破乳剂的应用报道,美国有人采用添加生物酶处理老化油,效果很好,但费用高,目前还难以成为主要处理手段。
3 结语
老化油的处理应单独进行,回收油系统电场处理的办法可用作老化油的二次处理。声化学技术具有处理效果好,处理量大,处理时间短,设备简单,能耗低,节约药剂的特点,适合大面积推广;离心法设备要求高但占地面积小,应用于海上平台等领域。生物法的研究主要集中在生物降解方面,但生物破乳剂的优势决定了这一领域具有研究潜力。热重力沉降法分离效率主要受药剂影响,目前处理效果尚不理想。
随着国家对环保的日益重视,回收老化油实现减量化、无害化和资源化,已成为油田亟待解决的问题之一。中国科学院沈阳应用生态研究所污染生态与环境工程中心提出了氧化破乳的概念,开发研制了老化油高效破乳剂,已在大庆油田开展试验。此外还研究了用磁处理技术、微波处理技术、变频处理技术、震动剪切处理技术,以及高频脉冲处理技术和研磨处理技术等处理老化油,取得了较好效果。今后应针对我国实际,积极寻求老化油的多种利用途径,变废为宝。